Inhaltsverzeichnis
1. Färben von Wolle
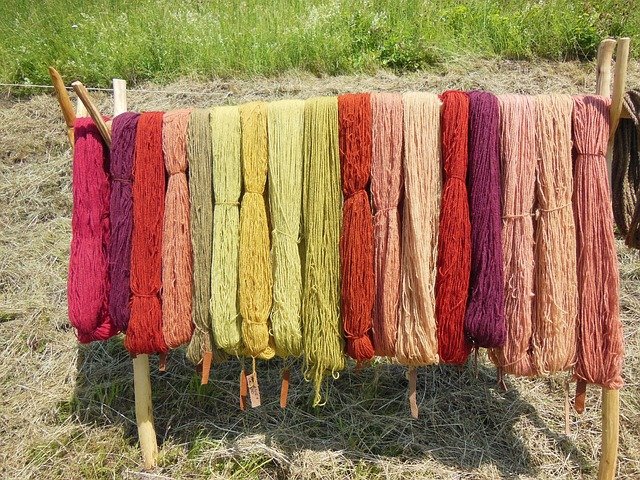
Die Farbabsorptionseigenschaften von Wolle können je nach Herkunft, Rasse, Alter, Ernährung, Jahreszeit und Lebensraum der Schafe variieren. Bemerkenswerterweise gibt es sogar innerhalb eines einzelnen Schafes erhebliche Unterschiede in der Qualität des Vlieses.
Tatsächlich können einzelne Wollfasern aufgrund biologischer und umweltbedingter Einflüsse auch Abweichungen in ihren Eigenschaften aufweisen (sogenannte Tippy-Färbung). Durch die spezielle Sortierung von Wollherkunft und Vliesbestandteilen entstehen Chargen, die hinsichtlich Feinheit, Verarbeitung und Anwendungsmerkmalen genau aufeinander abgestimmt sind.
Neben Schurwolle bietet der Markt in bestimmten Mengen auch Wolle an, die aus Häuten und Fellen geschlachteter Tiere gewonnen wird. Fellwolle ist mit geschorener Wolle vergleichbar, während rutschige Wolle durch Alkali verursachte Schäden aufweisen kann.
1.1. Prinzipien des Wollfärbens
Wollfasern bestehen hauptsächlich aus einer komplexen Struktur von Keratin, einem Proteinfilament. Der Färbeprozess beruht maßgeblich auf den im Keratin vorhandenen Aminogruppen. Wollfasern enthalten etwa 850 μmol titrierbare Grundgruppen pro Gramm. Carboxylgruppen kommen im sauren und neutralen pH-Bereich überwiegend in undissoziiertem Zustand in der Faser vor.
Das Vorhandensein ionischer Gruppen in der Faser ist pH-abhängig. Keratin weist seinen stabilsten Zustand auf, wenn die Anzahl negativer und positiver Ionen im Gleichgewicht ist. Diese als isoionische Region bekannte Region unterscheidet sich geringfügig von der isoelektrischen Region, die mit der Ladungsneutralität verbunden ist.
Adsorbierte Ionenladungen tragen zu den Gesamtionenladungen der Faser bei. Laut ELöD liegt der isoelektrische Punkt von Wolle bei Raumtemperatur bei pH 4,9.
Die morphologische Struktur der Faser spielt eine entscheidende Rolle im Färbeprozess und beeinflusst den Weg und die Effizienz der Farbstoffaufnahme. Frühere Annahmen deuteten darauf hin, dass Farbstoffe die Schuppenschicht auf der Faseroberfläche durchdringen mussten, wobei Epikutikula und Exokutikula aufgrund ihrer hydrophoben Natur als Barrieren betrachtet wurden.
Dies wurde durch die Tatsache gestützt, dass der oxidative oder chlorierende Abbau der Epikutikula und Exokutikula die Farbstoffabsorption deutlich steigerte. Diese Methoden werden immer noch bei der Herstellung bedruckter Wollmaterialien verwendet.
Studien haben jedoch gezeigt, dass Farbstoffe vor allem in die interzellulären Bereiche der Faser eindringen. Der Zellmembrankomplex fungiert als „Lösungsmittel“ für hydrophobe Textilchemikalien und die Quellfähigkeit des interzellulären Kittes ist wichtig für den Färbeprozess. Anschließend dringen die Farbstoffmoleküle in die schwefelreichen Keratine ein und bestimmen so die Lage des Färbegleichgewichts.
Zwischen dem Farbstoff und der Faser wirken verschiedene Bindungskräfte. Ionische Bindungen können entstehen, wenn Farbstoffanionen mit in den Fasern vorhandenen kationischen Gruppen interagieren. Allerdings reicht die Bildung ionischer Bindungen allein nicht aus, um die Farbstoffbindung zu erklären, da dissoziierbare Verbindungen in Gegenwart von Wasser gespalten werden.
Zwischen dem Farbstoff und der Faser bilden sich auch sekundäre Bindungen, darunter Dispersionskräfte, polare Bindungen und Wasserstoffbrücken. Für die Bindungsbildung ist eine enge Nähe zwischen den beiden erforderlich. Dies wird jedoch durch die den Farbstoff und das Wollkeratin umgebenden Hydratationssphären behindert.
Der Ansatz zerstört diese Sphären, insbesondere bei höheren Temperaturen, was zur Bildung gemeinsamer Hydratationssphären führt, die als „Eisbergstrukturen“ bekannt sind. Dieser Prozess erhöht die Entropie der beteiligten Wassermoleküle, ein Phänomen, das als hydrophobe Bindung bezeichnet wird.
Die Farbstoffbindung kann als Ionenaustauschprozess verstanden werden, bei dem die Ionenbindung durch Sekundärbindungen zwischen dem Farbstoff und dem Polymer unterstützt wird. ZOLLINGER bezeichnete dies als „Einweisungsfunktion“, die auf dem umfangreichen Potenzial ionischer Gruppen als „Pilotionen“ beruhte.
Neben sekundären und ionischen Bindungen können auch koordinative und kovalente Bindungen beitragen, insbesondere im Fall von Chrom-, Metallkomplex- und Reaktivfarbstoffen.
1.2. Farbstoffklassen und Färbeverfahren
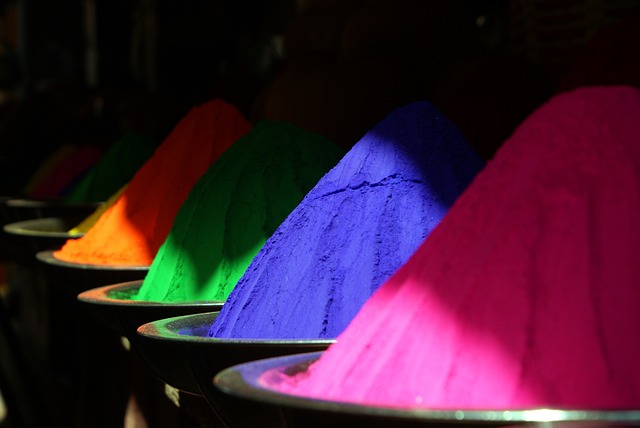
1.2.1. Säurefarbstoffe
Säurefarbstoffe bestehen aus einfachen chromophoren Systemen, die durch den Einbau von Sulfonsäuregruppen wasserlöslich gemacht werden. Bei der Dissoziation erzeugen diese Farbstoffe negativ geladene Farbstoffanionen, die mit den in der Faser vorhandenen Ammoniumgruppen interagieren. Diese Ammoniumgruppen werden in Gegenwart von Säure aus Aminogruppen gebildet, weshalb diese Farbstoffklasse auch so genannt wird.
Aus koloristischer Sicht werden Säurefarbstoffe nach ihrer Affinität kategorisiert. Dieses Affinitätsspektrum reicht von egalisierenden Farbstoffen über schwach sauer absorbierende (mäßig egalisierende) Mahlfarbstoffe bis hin zu neutral absorbierenden (schlecht egalisierenden) Supermahlfarbstoffen.
Im Allgemeinen nimmt die Größe des Farbstoffmoleküls entlang dieser Sequenz zu. Das Vorhandensein aliphatischer Gruppen im Farbstoffmolekül verbessert dessen Bindung an Wolle erheblich und wandelt egalisierende Farbstoffe in Typen um, die Walkfestigkeit aufweisen. Die Sulfonsäuregruppen bestimmen nicht nur die Anzahl der möglichen Ionenbindungen mit der Faser, sondern beeinflussen auch die Hydratation, die dem Bindungsprozess entgegenwirkt.
Bei kombinierten Anwendungen empfiehlt sich die Auswahl von Säurefarbstoffen mit ähnlichem Absorptionsverhalten. Ursprünglich für Polyamidfarben festgelegte Kombinationswerte wurden später für die Verwendung mit Wollfarben angepasst.
Während des Färbeprozesses kann die Zugabe von Salz als Zusatz eine verzögernde und egalisierende Wirkung haben. Es wird angenommen, dass höhere Konzentrationen an Sulfationen mit Farbstoffanionen um Ammoniumgruppen auf der Faser konkurrieren.
Dieser Wettbewerb schwächt die elektrostatische Anziehung zwischen Farbstoff und Faser, hauptsächlich aufgrund von Coulomb-Kräften. Mit zunehmendem pH-Wert nimmt die schwächende Wirkung ab. Andererseits fördern Salzzusätze die Aggregation von Farbstoffmolekülen, was zu einer verstärkten Anlagerung führt.
Die Färbeprozesse unterscheiden sich je nach Art der Säurefarbstoffe für Wolle, insbesondere im Hinblick auf den verwendeten pH-Bereich. Je größer die Affinität des Farbstoffs zur Faser ist, desto höher muss der anfängliche pH-Wert sein, um die ionische Bindungskomponente zu unterdrücken.
Der Färbeprozess beginnt typischerweise bei 60 °C für egalisierende Farbstoffe, 50 °C für Mahlfarbstoffe und 30 °C für Supermahlfarbstoffe. Man lässt die Säure 10 Minuten lang mit der Faser reagieren, gefolgt von der Zugabe von Salz nach weiteren 10 Minuten.
Der gelöste Farbstoff wird dann nach weiteren 10 Minuten zugegeben. Das System wird 30–45 Minuten lang erhitzt, bis eine Endtemperatur von 95 °C erreicht ist, und anschließend 45–90 Minuten lang bei 95 °C weiter gefärbt. Die Zugabe von Säure gegen Ende des Färbeprozesses sorgt für eine Erschöpfung des Färbebades.
Anschließend erfolgt eine Warm- und Kaltspülung. In manchen Fällen kann das Färben bei 80°C durchgeführt werden. Mahlfarben erfordern die Zugabe eines Egalisiermittels. Trichromes Färben kann mit egalisierenden Farbstoffen erreicht werden, während Mahlfarbstoffe möglicherweise die Auswahl eines Farbstoffs mit einem ähnlichen Farbton und einer ähnlichen Schattierung erfordern, um die gewünschte Farbe zu erzielen.
Zur Verbesserung der Echtheit kann die Nassechtheit von mit Kunstharz (z. B. Polyamid-Epichlorhydrin oder Polyurethan) behandelter chlorierter Wolle durch den Einsatz von Methylolamidverbindungen erhöht werden.
Sowohl die Echtheit als auch die Antifilzeigenschaften können durch den Einsatz einer polyquaternären Verbindung (einer Verbindung mit mehreren quartären Gruppen) wie Basolan F (BASF) oder Sandofix L (Sandoz) verbessert werden. Anionische Kondensationsprodukte können eine Barriere auf der Faseroberfläche bilden und so das Ausbluten anionischer Farbstoffe, beispielsweise Mesitol HWS (Bayer), reduzieren.
1.2.2. Chromfarbstoffe
Chromfarbstoffe sind eine spezielle Art von Säurefarbstoffen, die mit Chromionen Komplexe bilden. Während der Komplexbildung kommt es aufgrund der Überlagerung mehrerer angeregter Zustände zu einer deutlichen Farbtonverschiebung, was zu einer Abstumpfung des Farbtons führt.
Der Prozess der Komplexbildung findet in einer stark sauren Umgebung statt, wobei Elektronendonoren (Liganden) aus dem Chromophor und der Faser beteiligt sind. Chrom, das als Zentralatom des Komplexes fungiert, dient als Brücke zwischen dem Farbstoff und der Faser und bildet eine starke Bindung, die zu hervorragenden Echtheitseigenschaften beiträgt.
Chrom bindet an die Faser durch Substitution von Wasserstoff in -COOH- oder -OH-Gruppen sowie durch die Nutzung freier Elektronenpaare von >CO-, -NH2- oder -N=N-Gruppen und bildet dative Bindungen.
Um die Komplexbildung zu erleichtern, müssen in den Farbstoffen geeignete funktionelle Gruppen vorhanden sein:
1. Monofunktionelle Gruppen: wie Salicylsäure oder Alizarin-Typen.
2. Bifunktionelle Gruppen: dargestellt durch o,o‘-Dihydroxyazogruppen.
Als Zentralatom des Komplexes fungiert Chrom(III) mit der Koordinationszahl 6. Es entsteht aus Dichromat, das durch die Faser reduziert wird. Starke Säuren wirken auf diesen Prozess aktivierend und die reduzierende Wirkung von Wolle kann durch organische Säuren wie Wein-, Milch- oder Ameisensäure verstärkt werden.
Thiosulfat wirkt auch als Reduktionsmittel, wodurch die Umwandlungsrate und das Ausmaß der Verchromung erhöht und Faserschäden reduziert werden. Das Absenken der Temperatur von Siedetemperatur auf 90 °C trägt zum Schutz der Faser bei.
In der Vergangenheit betrug die erforderliche Dichromatmenge typischerweise 50 % bezogen auf den verwendeten Farbstoff, jedoch nicht weniger als 0,25 % und nicht mehr als 2,5 % bezogen auf die Faser. Allerdings konnte der Gehalt an Kaliumdichromat deutlich gesenkt werden.
Mithilfe von Hilfsmitteln werden Chromfarbstoffe dispergiert und mit ihnen Addukte gebildet. Diese Addukte zerfallen erst bei Siedetemperatur, wodurch die Anzahl der für die Komplexbildung verfügbaren freien Aminogruppen verringert wird und weniger Säure benötigt wird. Dies führt zu einer gleichmäßigeren Färbung und reduzierter Kippfärbung. Geeignete Hilfsstoffe sind unter anderem ethoxylierte Fettalkohole, Alkylphenole und Fettamine.
Für die Anwendung von Chromfarbstoffen werden hauptsächlich zwei Methoden angewendet:
1. Nachverchromungsmethode (Chrom entwickelnde Farbstoffe): Der Prozess beginnt mit einer Färbeflotte, die aus Ameisensäure, kalziniertem Natriumsulfat und Wollschutzmittel hergestellt wird. Das Färben beginnt bei 40°C und der gelöste Farbstoff wird nach 10 Minuten zugegeben. Anschließend wird das System erhitzt und das Färben bei 90 °C für 30–45 Minuten durchgeführt.
Reicht die Baderschöpfung nicht aus, wird Ameisensäure zugesetzt und die Färbung fortgesetzt. Anschließend erfolgt die Verchromung durch Abkühlen des Bades, Zugabe von Kaliumdichromat und Erhitzen auf 90–100 °C für 30–45 Minuten. Um das gebundene Chromat aus der Wolle zu lösen, wird Natriumsulfat zugesetzt und mit Ammoniak neutralisiert.
2. Einbad-Chromierungsverfahren (Metachrom-Verfahren): Bei diesem Verfahren erfolgt die Diffusion des Farbstoffs vor der Komplexbildung. Die Färbeflotte wird mit Metachrombeize (einer Mischung aus Natriumchromat und Ammoniumsulfat) und kristallinem Natriumsulfat hergestellt.
Das System wird langsam erhitzt und 45–90 Minuten bei Siedetemperatur gefärbt. Durch Zugabe von Essigsäure wird das Bad kurz vor Beendigung des Färbens erschöpft.
Es können verschiedene Hilfsstoffe verwendet werden, wie unter anderem Albegal W, Avolan AV, Lyogen MS, WD, Lyocol CR, Syntegal V7 (Ciba–Geigy), Uniperol O (BASF). Diese Hilfsmittel unterstützen den Färbeprozess und verstärken die Eigenschaften von Chromfarbstoffen.
1.2.3. 1:1 Metallkomplexfarbstoffe
Metallkomplexfarbstoffe weisen chemische Ähnlichkeiten mit Chromfarbstoffen auf. Das Risiko einer Faserschädigung wird jedoch minimiert, da der Komplex während der Farbstoffproduktionsphase gebildet wird.
Der Färbeprozess wird in einem schwefelsauren Medium mit hohem Säuregehalt (pH 1,9–2,2) durchgeführt. Aminogruppen in der Faser werden in die Ammoniumform umgewandelt und bilden so ionische Bindungen mit dem Farbstoffanion. In dieser Umgebung stehen die Aminogruppen nicht als Liganden zur Verfügung.
Erst beim Spülen, wenn der pH-Wert steigt, können sie durch Austausch von Aquo-Liganden in den Komplex eingebaut werden. Der Zusatz von Hilfsstoffen wie Alkanolethoxylaten ermöglicht eine Reduzierung der benötigten Säuremenge (pH 2,5-3), da diese mit dem Farbstoff Verbindungen eingehen und so die Komplexbildung unterdrücken.
Dies führt zu einem langsameren und gleichmäßigeren Färbeprozess. Mit synergistisch wirkenden amphoteren Hilfsstoffmischungen kann das Färben sogar bei höheren pH-Werten (3,5-4) durchgeführt werden.
Der Färbeprozess hängt vom Flottenverhältnis ab und das Bad wird mit Schwefelsäure (96 %) in einer Konzentration von 2–6 g/L eingestellt, um den gewünschten pH-Bereich (1,9–2,2 oder 2,5 bei Anwesenheit von 1–2 g/L Hilfsstoffen) zu erreichen.
Nach der Zugabe von kalziniertem Natriumsulfat (5–10 g/L) wird das Material 10 Minuten lang bei einer Temperatur von 40–50 °C in die Färbeflotte eingetaucht. Anschließend wird der gelöste Farbstoff zugegeben und nach weiteren 10 Minuten das System über einen Zeitraum von 30-45 Minuten schrittweise erhitzt.
Anschließend wird 90 Minuten bei Kochtemperatur gefärbt. Dem letzten Spülbad kann Ammoniak (25 %) in einer Konzentration von 1–2 ml/L oder Natriumacetat (2–3 g/L) zugesetzt werden. Eine Senkung der Temperatur auf 80 °C ist möglich, wenn ein ethoxyliertes Fettamin in einer sauren Umgebung (pH 1,9–2,2) verwendet wird.
Beispiele für Farbstoffreihen sind Chromolan (Ostacolor), Inochrom (Zeneca), Neolan (Ciba–Geigy) und Palatinecht (BASF).
Es können verschiedene Hilfsstoffe eingesetzt werden, wie Albegal NF, Albegal Plus (Ciba–Geigy), Avolan S, SCN (Bayer), Lyogen WD (Sandoz), Syntegal V7 (Ostacolor), Uniperol O und Uniperol SE (BASF).
1.2.4. 1:2 Metallkomplexfarbstoffe
Im schwach sauren pH-Bereich werden Metallkomplexe im Molverhältnis 1:2 gebildet. Typischerweise koordinieren zwei Chromophore ein zentrales Atom, beispielsweise Chrom (Cr) oder Kobalt (Co). Das Zentralatom befindet sich zwischen den beiden Chromophoren, oft senkrecht zueinander angeordnet.
Die hohe Affinität zur Faser wird auf die große Größe der Farbstoffmoleküle, ihre kompakte und kugelförmige Form sowie ihre negative Ladung zurückgeführt.
Zunächst wurde auf den Einbau von Sulfonsäuregruppen in die Farbstoffmoleküle verzichtet, um zusätzliche ionische Wechselwirkungen zwischen Faser und Farbstoff auszuschließen und eine bessere Egalität beim Färben zu erreichen. Stattdessen wurde die Wasserlöslichkeit durch den Einbau von Methylsulfon- (–SO2–CH3) oder Sulfonamidgruppen (–SO2–NH2) erreicht.
Erst nach 1960 fanden Farbstoffe mit Sulfonsäuregruppen Anwendung. Vorteile dieser Farbstoffe sind eine kostengünstige Herstellung, höhere Ausbeute und Kältelöslichkeit.
Im Allgemeinen ist ihre Nassechtheit etwas höher als bei Farbstoffen mit Methylsulfon- und Sulfonamidgruppen. Allerdings sind Farbstoffe mit zwei Sulfonsäuregruppen besonders anfällig für eine nicht egale Färbung.
Um dies zu mildern, werden Hilfsstoffe, insbesondere ethoxylierte Fettamine, zugesetzt, die mit dem Farbstoff Addukte bilden. Diese Addukte zerfallen bei höheren Temperaturen. Der nivellierende Effekt wird durch die Zugabe von Glaubersalz verstärkt.
Da die Bildung von 1:2-Farbstoffkomplexen in einem schwach sauren Medium erfolgt, können sie unter den gleichen Bedingungen auf Wolle aufgetragen werden. Dies ermöglicht einen schonenden Färbeprozess, der oxidative Angriffe durch Cr(VI) oder hydrolytische Angriffe durch Schwefelsäure vermeidet.
Beim Färbevorgang wird der Flotte Ammoniumsulfat (1–2 g/L) oder Ammoniumacetat (2–4 g/L) (pH 5,5) zugesetzt. Nach einem Vorlauf von 10 Minuten bei 30-50°C wird der gelöste Farbstoff zugegeben. Das System wird über 30–60 Minuten schrittweise erhitzt und 30–60 Minuten bei Siedetemperatur gefärbt.
Bei Verwendung von Hilfsmitteln (1-2 g/L) erfolgt die Färbung unter Zusatz von Essigsäure (30 %) (1-3 g/L) (pH 4,5-5) und kalziniertem Natriumsulfat (1-2 g/L). Auch die Dosierung von Säuren über Steuerungs- und Überwachungssysteme ist eine sinnvolle Option. Nach dem Spülen wird Ameisensäure (1-2 g/L) zur Ansäuerung eingesetzt, um den Griff und die Nassechtheit zu verbessern.
Es werden verschiedene Hilfsstoffe verwendet, darunter Albegal A, SET, SW (Ciba-Geigy); Avolan IL, IS, IWN, UL75 (Bayer); Eganal SZ (Hoechst); Lyogen FN, MS (Sandoz); Remol U (Hoechst); Uniperol SE, W (BASF); Unisol WL (Zeneca); Wofalansalz EM (Wolfen).
1.2.5. Reaktive Farbstoffe
Reaktivfarbstoffe für Wolle sind dafür bekannt, leuchtende Farben mit guter Farbechtheit zu erzeugen. Sie unterscheiden sich jedoch von Reaktivfarbstoffen für Zellulosefasern durch die deutlich höhere Reaktivität der Aminogruppen in Wolle im Vergleich zu Hydroxylgruppen in Zellulose. Um eine gleichmäßige und egale Färbung auf Wolle zu erreichen, ist es notwendig, die Reaktivität des Farbstoffs zu reduzieren und einen Hilfsstoff zuzusetzen.
Wolle enthält verschiedene reaktive Gruppen, darunter Amino-, Imino- und Hydroxylgruppen, wobei Aminogruppen die bedeutendste sind. Färbereaktionen finden in einem schwach sauren Medium mit einem pH-Wert im Bereich von 3–5 statt.
Bei diesen Reaktionen handelt es sich um nukleophile Substitutionen von Abgangsgruppen (typischerweise Cl, F und gelegentlich Sulfonat- oder Ammoniumgruppen) oder um Additionsreaktionen an polarisierte aliphatische Doppelbindungen.
Die beiden erstgenannten Ankergruppen, N-Methyltaurinethylsulfon und β-Sulfatoethylsulfon, bieten den Vorteil, dass sie zu Beginn des Prozesses über maskierte funktionelle Gruppen verfügen. Dadurch wird verhindert, dass es unterhalb der Siedetemperatur zu vorzeitigen Reaktionen kommt. Darüber hinaus ermöglicht die erhöhte Löslichkeit eine gleichmäßige Färbung. Bifunktionelle Farbstoffe wie Drimalan und Lanasol können eine vernetzende Wirkung auf Wolle haben.
Der pH-Wert spielt beim Färbeprozess eine entscheidende Rolle. Im sauren Bereich bilden sich ionische Bindungen zwischen Farbstoff und Faser, die eine Migration des Farbstoffs ermöglichen. Bei pH 5 überwiegt die kovalente Bindung an die Faser.
Beim Färbevorgang wird der Flotte ein Hilfsstoff (1-2 g/L) zugesetzt und der pH-Wert mit Ameisensäure oder 1-3 g/L Essigsäure auf 3-4 eingestellt. Der Prozess beginnt bei 40°C und der gelöste Farbstoff wird nach 10 Minuten zugegeben. Nach 20–30 Minuten wird der pH-Wert mit Natriumdihydrogenphosphat auf 5–6 eingestellt. Die Färbung erfolgt 1 Stunde bei Siedetemperatur.
Um hydrolysierten Farbstoff zu entfernen, wird eine Nachbehandlung für 15 Minuten bei 80 °C unter Zugabe von 1,5 g/L Ammoniak (pH 8,5–9,0) durchgeführt. Das letzte Spülbad ist leicht angesäuert.
Es stehen verschiedene Hilfsstoffe zur Verfügung, darunter Albegal B (Ciba-Geigy), Avolan REN (Bayer), Eganal GES (Hoechst) und Lyogen FN (Sandoz).
1.2.6. Küpenfarbstoffe, Leukoester von Küpenfarbstoffen
Historisch gesehen hatten Küpenfärber beim Färben von Wolle eine große Bedeutung. Insbesondere Indigo wurde aufgrund seiner unübertroffenen Farbechtheit auf Wolle als „König der Farbstoffe“ verehrt. Bis Mitte der 1950er Jahre wurde Marinestoff überwiegend mit Indigo gefärbt.
Allerdings war die Anwendung von Indigo aufgrund der schädlichen Wirkung von Reduktionsmitteln und Alkali auf Wolle mit Herausforderungen verbunden. Infolgedessen haben sich moderne Färbepraktiken von Indigo, Thioindigo und deren Derivaten abgewendet und sie durch alternative Farbstoffklassen ersetzt, mit denen man bequemer arbeiten kann.
1.3. Technologie des Färbens
Wolle wird üblicherweise in zwei Formen gefärbt: Flock (lose Fasern) und Lummen (dicke Faserstränge). Allerdings gibt es einen zunehmenden Trend zu Stück- und Garnfärbemethoden.
Stückfärben und Garnfärben können mit Überlauffärbemaschinen durchgeführt werden, wodurch Winden- und Baumfärbemaschinen oder Jigger überflüssig werden, insbesondere wenn das Material zum Schrumpffestmachen vorbehandelt wurde.
Für hochwertige Wollartikel aus feinen Garnen ist ein schonender Behandlungsprozess notwendig.
Das Färben von Wolle erfolgt typischerweise bei oder nahe der Siedetemperatur, was zu einer Verschlechterung der Faser führen kann. In manchen Fällen kann die Temperatur auf 80-90°C gesenkt werden. Bei schlecht egalisierenden Farbstoffen können jedoch höhere Färbetemperaturen erforderlich sein.
Die allgemein akzeptierte Temperaturobergrenze liegt bei 108 °C, außer beim Färben von Polyester-Wolle-Mischungen im Hochtemperaturverfahren, wo die Grenze auf 120 °C angehoben werden kann. Um den Faserabbau zu mildern, wird der Färbeflotte Formaldehyd zugesetzt, das Methylenbrücken in der Faser bildet und das Keratin gegen hydrolytischen Abbau stabilisiert.
Die Auswahl von Wollfarben für verschiedene Anwendungen hängt von ihrem Absorptions- und Verlaufsvermögen ab.
Kontinuierliche Färbeverfahren werden üblicherweise zum Färben von Lunten eingesetzt. Bei diesem Verfahren wird der Klotzflotte ein Verdickungsmittel auf Basis von verethertem Guar- oder Johannisbrotkernmehl sowie ein spezieller Hilfsstoff und eine Säure oder ein Säurespender zugesetzt. Als Chromierungsmittel wird häufig Chromtrifluorid verwendet. Nach dem Foulardieren wird das Material einer Dampfbehandlung für 15-60 Minuten unterzogen.
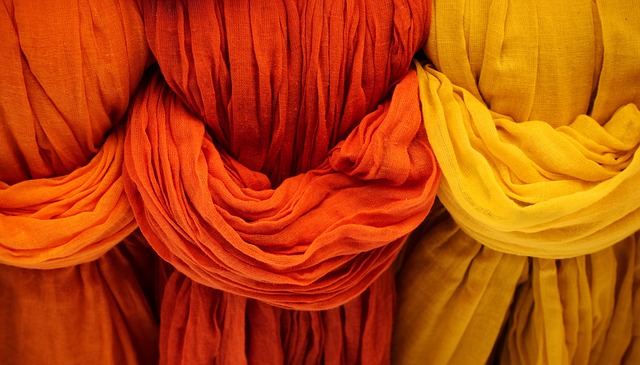
1.4. Eigenschaften von Farbstoffen
Unter den genannten Farbstoffklassen sind Reaktiv- und 1:2-Metallkomplexfarbstoffe volumenmäßig am häufigsten verwendet, gefolgt von 1:1-Metallkomplex-, Chrom- und Säurefarbstoffen.
Die Verteilung der Farbstoffklassen hängt nicht nur von der gewünschten Farbechtheit ab, sondern auch von der gewünschten Brillanz. Säure- und Reaktivfarbstoffe sind dafür bekannt, lebendige Farbtöne zu erzeugen, während Chromfarbstoffe bei schwarzen Farbtönen dominieren.
1:2-Metallkomplexfarbstoffe sind neben Chrom- und Metallkomplexfarbstoffen besonders anwenderfreundlich und ermöglichen bei Bedarf Farbkorrekturen (Shading). Superwash-Artikel, die eine hohe Farbechtheit erfordern, können mit Reaktivfarbstoffen erreicht werden. Chrom- und Metallkomplexfarbstoffe bieten eine hervorragende Echtheit gegenüber Mahl- und Vergussprozessen.
Während des Färbeprozesses kann Wolle durch Säuren, Oxidationsmittel (Chromat), Wasser, Hitze und mechanische Beanspruchung beschädigt werden. Längerer Kontakt mit kochendem Wasser kann zur Spaltung von Cystin-Vernetzungen in der Wollfaser führen.
Es können sich neue Brücken wie Lysinoalanin bilden, die zur Faltenfixierung beitragen. Daher empfiehlt es sich, Wollstoffe vor dem Färben vorzufixieren. Der hydrolytische Abbau nimmt mit zunehmender Entfernung vom isoelektrischen Punkt der Wolle zu.
Das häufig vorhandene Natriumsulfat kann die Hydrolyse fördern und zu einer Verschlechterung der mechanischen Eigenschaften führen. Unter den Farbstoffklassen gelten 1:2-Metallkomplexfarbstoffe als die günstigsten Auswirkungen auf den Erhalt des Griffs, der Elastizität und der Festigkeit der Wolle.
Chlorierte Wolle weist im Vergleich zu unbehandelter Wolle ein anderes Farbverhalten auf. Die Entfernung der Schuppenschicht erleichtert sowohl die Aufnahme als auch die Freisetzung des Farbstoffs.
Die Nassechtheit chlorierter Wolle ist deutlich geringer, daher werden zum Färben solcher Fasern Reaktivfarbstoffe empfohlen. Andererseits führen Antifilzbehandlungen mit Kunstharz in der Regel nicht zu nennenswerten Veränderungen im koloristischen Verhalten.
2. Färben von Seide
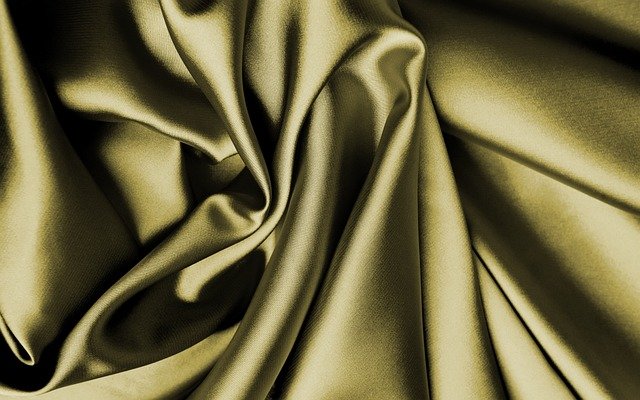
Trotz ihres relativ geringen Beitrags zur gesamten Faserproduktion ist Seide aufgrund ihrer einzigartigen Eigenschaften von großer Bedeutung. Insbesondere im Bereich der Mode für Damenmode sowie Herrenhemden, -jacken, -krawatten und -schals ist dies nicht zu unterschätzen.
2.1. Faserstruktur von Seide und Färbeverhalten
Seidenfibroin besteht aus 18 verschiedenen Aminosäuren. Ähnlich wie bei Wolle ist das Vorhandensein von Aminogruppen in Seide entscheidend für die Aufnahme ionischer Farbstoffe. Allerdings ist die Anzahl der Aminogruppen in Seide mit 230 μmol pro Gramm Faser im Vergleich zu Wolle deutlich geringer.
Der isoionische Punkt von Seide liegt bei pH 5,0. Seide weist im Vergleich zu Wolle aufgrund des Fehlens von Cystin-Vernetzungen eine geringere Stabilität auf. Selbst unter milden Bedingungen, beispielsweise bei pH 4,0 und 85 °C, kann es zu hydrolytischem Abbau kommen.
Um Schäden an der Seidenfaser zu mildern, muss die Säure während des Färbevorgangs kontinuierlich und nicht auf einmal hinzugefügt werden. Daher wird das Färben häufig bei Temperaturen um 70–80 °C durchgeführt, diese sollten jedoch 90 °C nicht überschreiten, um Schäden an der Oberflächenstruktur zu minimieren und Faltenbildung zu verhindern.
Aufgrund ihrer feinen Textur reflektiert Seide das Licht von ihrer Oberfläche stark. Daher ist im Vergleich zu anderen Materialien eine größere Farbstoffmenge erforderlich, um den gewünschten Farbton zu erzielen.
2.2. Klassen von Seidenfarben
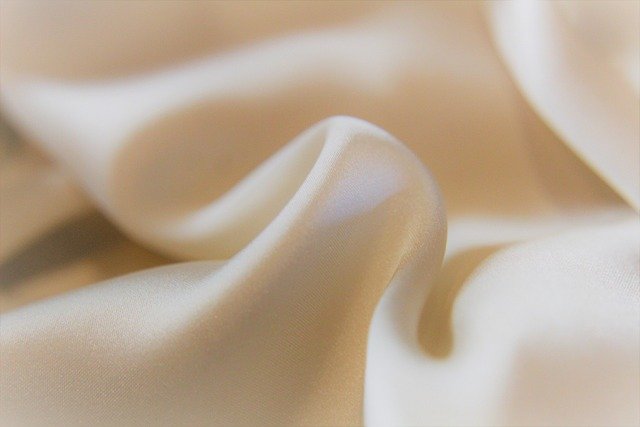
Direktfarbstoffe: Direktfarbstoffe werden aufgrund ihrer guten Echtheitseigenschaften häufig auf Seide verwendet.
Färbeverfahren: Das Färben erfolgt im neutralen pH-Bereich oder unter Zusatz von 1–3 g/L Essigsäure (30 %) und 2–5 g/L Natriumsulfat. Der Prozess beginnt bei 30–40 °C und die Temperatur wird innerhalb von 30–45 Minuten schrittweise erhöht. Das Färben wird bei 90°C für 30–45 Minuten fortgesetzt. Ein Egalisierungsmittel, typischerweise 1/3–1/5 der mit Essigsäure schwach angesäuerten Entschleimungsflotte, kann zugesetzt werden.
Säurefarben: Säurefarben sind die am häufigsten verwendeten Farbstoffe für Seide.
Färbeverfahren: Das Färben erfolgt unter Zugabe von 1–4 g/L Essigsäure (30 %) oder 1–2 g/L Ammoniumsulfat bei pH 4–5,5. Der Prozess beginnt bei 30–40 °C und die Temperatur wird innerhalb von 30–45 Minuten schrittweise erhöht. Das Färben wird bei 70–85°C für 45–60 Minuten fortgesetzt. Einen besseren Faserschutz bietet das Färben im zum Entschleimen verwendeten Seifenbad (pH 8-8,5) unter Zusatz von Natriumsulfat.
Metallkomplexfarbstoffe: Obwohl sie im Vergleich zu Wolle von geringerer Bedeutung sind, können Nachchromierungsfarbstoffe auf Seide aufgetragen werden. 1:1-Metallkomplexfarbstoffe lassen sich in schwach saurem Medium bei 90°C färben und liefern hervorragende Echtheitswerte. Für Seide sind jedoch 1:2-Metallkomplexfarbstoffe besser geeignet, da sie in einem schwach sauren Medium aufgetragen werden können und eine gute Echtheit bieten.
Färbeverfahren: Das Färben erfolgt unter Zusatz von 2–5 g/L Ammoniumacetat oder 2–3 g/L Ammoniumsulfat und 0,5–1 % eines Egalisiermittels. Nach einem Vorlauf von 15 Minuten bei 40°C wird gelöster Farbstoff zugegeben. Die Temperatur wird innerhalb von 30–40 Minuten schrittweise erhöht und das Färben bei 80–95°C für 45–60 Minuten fortgesetzt.
Verbesserung der Echtheit: Mit Säure-, Direkt- und Metallkomplexfarbstoffen hergestellte Farben können mit 8 % Gerbsäure und 4 % Essigsäure (30 %) bei 35–40 °C für 60 Minuten nachbehandelt werden. Anschließend wird ohne Zwischenspülung ein Frischbad mit 4 % Kaliumantimon(III)oxidtartrat bei 20-25°C verwendet.
Reaktivfarbstoffe: Reaktivfarbstoffe werden auf Seide aufgetragen, wenn brillante Farbtöne gewünscht sind und die mit Säurefarbstoffen erzielte Farbechtheit nicht den erforderlichen Anforderungen genügt.
Färbeverfahren: Das Färben erfolgt unter Zugabe von 10–40 g/l kalziniertem Natriumsulfat, wobei die Hälfte nach 15 Minuten und die andere Hälfte nach 30 Minuten bei 30 °C zugegeben wird. Die Temperatur wird innerhalb von 30 Minuten schrittweise auf 50–70 °C erhöht und nach weiteren 15 Minuten werden 2 g/L Soda hinzugefügt. Die Färbung wird 40 Minuten lang fortgesetzt. Eine Nachwäsche bei 80°C erhöht die Nassechtheit.
Andere Farbstoffklassen: Entwicklungsfarbstoffe, Küpenfarbstoffe und deren Leukoester sowie kationische Farbstoffe können ebenfalls zum Färben von Seide verwendet werden, sind jedoch von geringerer Bedeutung.
2.3. Technologie des Färbens
Garnstränge werden häufig mit Sprüh- oder Paketfärbemaschinen gefärbt. Andererseits werden zum Färben von Stoffen üblicherweise Winden-, Baum- und Überlaufverfahren bevorzugt.
Um das charakteristische krausige Gefühl von Seide zu erreichen, werden Beschwerungs- und Auffrischungsprozesse eingesetzt, typischerweise unter Verwendung von 1–2 g/l Ameisen-, Essig-, Milch- oder Zitronensäure.
Referenz
- Textile Dyeing, 3. Dyeing of Wool and Silk; Ullmann’s Encyclopedia of Industrial Chemistry. – https://onlinelibrary.wiley.com/doi/10.1002/14356007.u26_u02
FAQ: Färben von Wolle und Seide
Beim Färben von Wolle werden die Wollfasern in ein Färbebad getaucht, das geeignete Farbstoffe und Hilfschemikalien enthält. Die Wolle wird normalerweise unter Rühren auf nahezu Siedetemperatur erhitzt, um eine gleichmäßige Farbstoffdurchdringung zu gewährleisten. Die spezifische Färbemethode kann je nach Ausrüstung und verwendetem Farbstofftyp variieren.
Der beste Farbstoff für Wolle hängt von der gewünschten Farbe, den Anforderungen an die Echtheit und der spezifischen Färbetechnik ab. Säurefarbstoffe werden aufgrund ihrer hervorragenden Farbpalette, Echtheitseigenschaften und Kompatibilität mit Wollfasern häufig für Wolle verwendet. Auch Reaktivfarbstoffe und Metallkomplexfarbstoffe eignen sich zum Färben von Wolle.
Um Wollmaterial zu färben, bereiten Sie zunächst ein Färbebad vor, indem Sie den gewählten Farbstoff in heißem Wasser auflösen und bei Bedarf Hilfschemikalien hinzufügen. Tauchen Sie das Wollmaterial in das Färbebad und erhitzen Sie das Bad unter Rühren, um eine gleichmäßige Farbverteilung zu gewährleisten. Färben Sie weiter, bis die gewünschte Farbe erreicht ist, spülen Sie das Material aus und führen Sie ggf. Nachbehandlungen durch.
Für Wolle werden üblicherweise verschiedene Arten von Farbstoffen verwendet, darunter Säurefarbstoffe, Reaktivfarbstoffe, Metallkomplexfarbstoffe und Direktfarbstoffe. Säurefarben erfreuen sich aufgrund ihrer leuchtenden Farben und hervorragenden Waschechtheit besonderer Beliebtheit. Reaktivfarbstoffe sind für ihre brillanten Farbtöne und ihre gute Farbechtheit bekannt. Metallkomplexfarbstoffe bieten hervorragende Echtheitseigenschaften und Direktfarbstoffe werden aufgrund ihrer guten Echtheit auf Wolle häufig verwendet.
Ja, 100 % Seide kann gefärbt werden. Seidenfasern haben eine Affinität zu Farbstoffen und können mit geeigneten Färbetechniken erfolgreich gefärbt werden. Welche Art von Farbstoff für Seide verwendet wird, hängt von Faktoren wie der gewünschten Farbe, den Anforderungen an die Echtheit und der verwendeten Färbemethode ab.
Welcher Seidenstoff am besten gefärbt wird, hängt von verschiedenen Faktoren wie der gewünschten Farbe, der Färbemethode und den gewünschten Echtheitseigenschaften ab. Säurefarben werden aufgrund ihrer leuchtenden Farben und guten Farbechtheit häufig für Seide verwendet. Zur Erzielung brillanter Farbtöne können bei Seide auch Reaktivfarbstoffe eingesetzt werden, während Direktfarbstoffe aufgrund ihrer guten Echtheitseigenschaften geeignet sind.
Seidenfarbe kann hergestellt werden, indem man die gewünschte Farbe in heißem Wasser auflöst und dabei die Anweisungen des Farbstoffherstellers befolgt. Der Farbstoff erfordert möglicherweise zusätzliche Chemikalien oder Beizen, um seine Affinität zu Seidenfasern zu erhöhen. Es ist wichtig, die Anweisungen des Farbstoffherstellers sorgfältig zu befolgen, um eine ordnungsgemäße Vorbereitung und Anwendung des Farbstoffs sicherzustellen.
Ja, Naturseide kann gefärbt werden. Seidenfasern haben eine natürliche Affinität zu Farbstoffen und eignen sich daher zum Färben mit einer Vielzahl von Farbstofftypen. Es ist jedoch wichtig, den spezifischen Farbstofftyp und das Färbeverfahren zu berücksichtigen, um die gewünschte Farbe zu erzielen und eine gute Farbechtheit auf Naturseide zu gewährleisten.