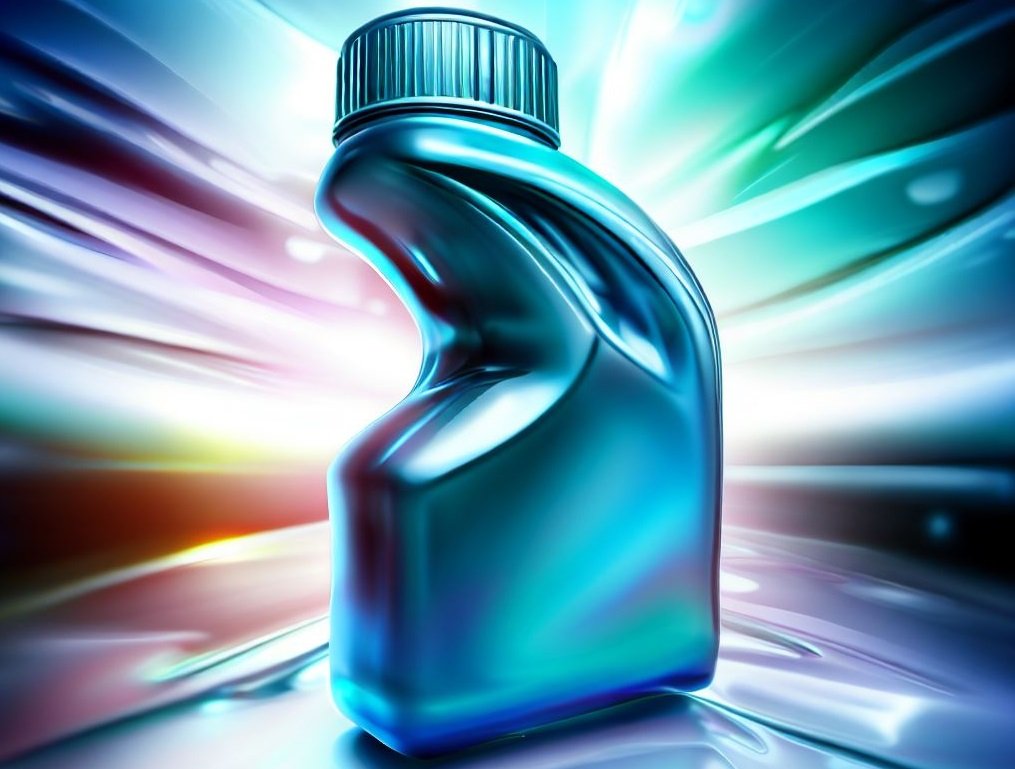
Antifreeze is a substance used to lower the freezing point of water or water-based liquids. It is most commonly used to protect internal combustion engines from freezing, but it also has other applications in refrigeration, heat transfer systems, water heaters, and more.
The most common type of antifreeze is ethylene glycol, which is a colorless, odorless liquid. Ethylene glycol is produced in the United States and Europe, and it is used in antifreeze for cars, trucks, and other vehicles.
Table of Contents
1. Antifreeze Raw Materials
Early internal combustion engines used water as coolant because it was cheap, plentiful, and good at transferring heat. However, water had several drawbacks:
- It can corrode metal parts in the cooling system.
- It has a high freezing point.
- When it freezes, it expands by about 9-10%. This can damage the engine block, water pump, and radiator.
Antifreeze agents and corrosion inhibitors were added to address these problems. Water has a relatively low boiling point (100 °C), so pressure caps are used to raise the coolant’s boiling point.
However, the maximum pressure is limited by the materials used to make the cooling system, especially the radiator and solder joints. Adding ethylene glycol to the coolant raises its boiling point, so lower pressures can be used to achieve higher coolant temperatures.
In the 1920s, as the number of cars in the United States grew from 7.5 million to 26.5 million, the demand for antifreeze also increased. Denatured ethanol became popular because it was cheap, plentiful, and good at lowering the freezing point of water.
Glycerol was also used sometimes as an antifreeze, but it was not always available. Calcium chloride and other salt solutions were tried as engine coolants in some parts of the United States, but they were too corrosive.
Honey, sugar solutions, and even kerosene and other hydrocarbon oils were also tried, but none of them became widely used. Ethanediol emerged as a good antifreeze agent in the 1920s, but it was not widely used at first because it was not always available.
Before World War II (1940), the main antifreeze agents available were ethanol, synthetic methanol, and ethylene glycol. These three agents accounted for 90% of antifreeze consumption in the United States.
The other 10% was made up of wood byproduct methanol, glycerol, and 2-propanol. The choice of antifreeze agent was based on availability rather than cost or performance.
After World War II (1945), the number of cars in the United States and Western Europe increased, and so did the demand for antifreeze. Methanol-based and ethanediol-based coolants dominated the market during this time.
Methanol-based coolants reached their peak consumption in the early 1950s. Carmakers started putting ethanediol in new cars, and by the early 1970s, it was the only antifreeze agent used in new cars. The entire replacement automotive engine coolant market also switched to ethylene glycol.
By 1960, ethanediol had captured over 80% of the market share. Methanol-based coolants were still used in some stationary engines and older vehicles, but they were becoming less popular.
The main reason why methanol-based coolants were replaced by ethanediol in cars was that ethanediol allowed for higher coolant operating temperatures. This was important for efficient space heating in vehicle interiors during cold weather and also resulted in minor improvements in vehicle fuel efficiency.
1,2-propanediol, commonly known as propylene glycol, is used as a heat transfer fluid in systems where the toxicity of the antifreeze is a concern. Examples include some active solar energy collectors, cooling systems for engines that use potable water sources, and freezing and refrigeration systems for food and dairy products.
1,2-propanediol is also used as an automotive antifreeze in some European countries (e.g., Switzerland) because it is less harmful to humans, especially children, if accidentally ingested.
1-methoxy-2-propanol has also been used as an antifreeze agent, primarily in ebullient cooling systems and heavy-duty diesel engines. 1-methoxy-2-propanol and water form an azeotrope, which provides freeze protection in the vapor phase in ebullient cooling applications.
1-methoxy-2-propanol-based antifreeze materials are used in heavy-duty diesel engines and other industrial engines where coolant leakage into the crankcase is a concern.
Because ethanediol has a low volatility, it tends to remain in the crankcase, which can lead to sludge and varnish formation and accelerated bearing wear. In contrast, 1-methoxy-2-propanol is more volatile and is readily expelled, along with water vapor, through the crankcase vent system.
1-methoxy-2-propanol also maintains lower metal temperatures compared to glycol-based coolants, which was advantageous in rotary engines. However, with the decline of rotary engines, this advantage has become less significant in the market.
2. Physical Properties of Antifreeze
Antifreeze-water mixtures freeze and boil differently than pure water or pure antifreeze. When these mixtures freeze, the water crystallizes first, which makes the remaining liquid more concentrated in antifreeze and lowers its freezing point. This results in a slushy mixture that can withstand colder temperatures than pure water or pure antifreeze.
Property | Water | Methanol | 1,2-Ethanediol | 1,2-Propanediol | 1-Methoxy-2-propanol |
---|---|---|---|---|---|
Molar mass (g/mol) | 18.02 | 32.04 | 62.07 | 76.09 | 90.1 |
Density (g/cm3) | 0.998 | 0.792 | 1.113 | 1.036 | 0.923 |
Boiling point (0.1013 MPa), °C | 100.0 | 64.7 | 197.5 | 187.4 | 120.1 |
Freezing point, °C | 0 | -97.6 | -12.6 | -43.5 | -96 |
Specific heat (20 °C), J g-1 K-1 | 4.17 | 2.495 | 2.357 | 2.481 | 2.426 |
Flash point (open cup), °C | - | 12 | 117 | 102 | 38 |
Viscosity (20 °C), mPa·s | 1.0 | 0.57 | 20.1 | 56.2 | 1.81 |
It is easy to calculate the freezing point depression of antifreeze-water mixtures that are not very concentrated, but it is more difficult to calculate the freezing point depression of antifreeze-water mixtures that are.
To estimate the freezing point of a concentrated antifreeze-water mixture, you can use data from mixtures of water and antifreeze that do not have corrosion inhibitors. However, to get the most accurate freezing point, you should do a practical measurement. ASTM Standard Test Method D 1177 provides a convenient method for doing this.
Antifreeze materials also affect the boiling point of water. All antifreeze materials except methanol raise the boiling point of the mixture above the 100°C boiling point of pure water.
Table 2 shows the boiling points of several antifreeze-water mixtures that do not have corrosion inhibitors.
Antifreeze | 10% | 20% | 30% | 40% | 50% | 60% |
---|---|---|---|---|---|---|
Methanol | 91.7 | 86 | 82 | 79 | 76.5 | 74 |
Ethanediol | 101 | 102 | 103 | 104.5 | 107 | 110 |
1,2-Propanediol | 101 | 101.5 | 102 | 102.5 | 104.5 | 107 |
1-Methoxy-2-propanol | 100 | 100.5 | 101 | 102 | 102.5 | 103 |
Methanol is the only antifreeze in the table that lowers the boiling point of the mixture below that of water. Because corrosion inhibitors also raise the boiling point of water, you should use ASTM Standard Test Method D 1120 to determine the precise boiling point of a specific mixture.
3. Corrosion Inhibitors in Antifreezes
Antifreeze is essential for protecting engine components and cooling and heating systems from corrosion. However, antifreeze-water solutions can be more corrosive than water alone. Therefore, corrosion inhibitors are added to antifreeze formulations. These inhibitors prevent corrosion and the oxidation of ethylene glycol into corrosive derivatives.
The corrosivity of antifreeze-water solutions is influenced by the type of antifreeze base, the metals used in the system, the nature of heat-rejection surfaces, the operating temperatures of the cooling system, and the quality of the water used. Anions from strong acids, such as chloride or sulfate, can increase the corrosivity of the solution.
In the United States, coolant inhibitor formulations are typically developed without specific consideration for water quality. This allows for the use of a wide range of inorganic materials, such as orthophosphate, that might not otherwise be used.
Low-corrosivity formulations are achieved by combining ethanediol with inhibitors from various groups, including phosphates, benzoates, sebacates, borates, nitrates, nitrites, silicates, molybdates, and organic compounds like amines, benzothiazoles, benzotriazoles, or imidazoles.
The specific amounts of these inhibitors are determined based on the formulator’s experience to ensure the desired level of corrosion protection.
For example, General Motors’ specification GM 6038-M (in Table 3) contains the typical inhibitors commonly found in most antifreezes produced in the United States.
Composition | GM 6038-M (parts by wt) | GM 6043-M (wt %) |
---|---|---|
Ethylene glycol | 1115.5 | 95.5 |
NaNO3 | 2.5 | 0.1 |
Na2B4O7 · 5 H2O | 11.5 | 0.4 |
Na2SiO3 · 5 H2O | 1.9 | – |
Liquid sodium silicate | – | 0.3 |
Na2MoO4 · 2 H2O | – | 0.2 |
Na3PO4 · 12 H2O | 5.0 | – |
H3PO4 (85 wt % solution) | – | 0.15 |
NaOH | 2.25 | 0.235 |
Sodium 2-mercaptobenzothiazole (50 wt % solution) | 6.5 | 0.5 |
Sodium tolyltriazole (50 wt % solution) | – | 0.2 |
Antifoam | 0.5 | 0.05 |
Dyed | 0.05 | 0.005 |
Water | – | 2.3 |
Silicate antigel | – | 0.06 |
Both in Europe and the United States, some automotive manufacturers restrict the use of materials that might react to form carcinogenic compounds, such as combinations of amines or nitrites.
In Europe, the compatibility of coolant with local hard water is a significant consideration. Some materials, like orthophosphate and, in some areas, silicate, may not meet this criterion.
As an alternative to orthophosphate, benzoate is sometimes used. Amine salts are only used in specific applications where the specifications have not been updated to incorporate improved formulations.
In Japan, inhibited antifreezes are similar to those used in the United States, with triethanolamine (tris(2-hydroxyethyl)amine) frequently utilized as the neutralizing base.
4. Production of Antifreeze
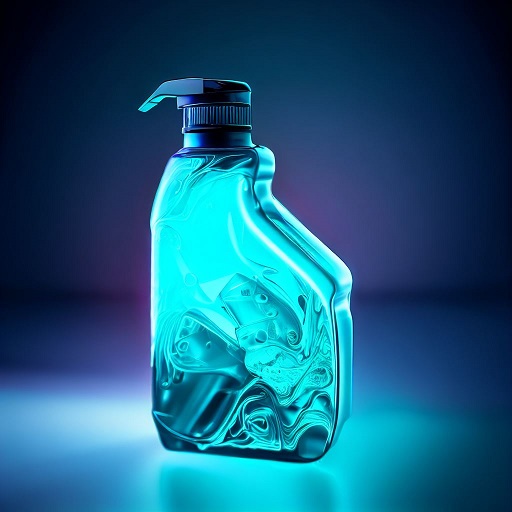
Antifreeze is a mixture of fluids that lowers the freezing point of water. The main ingredient in antifreeze is ethylene glycol, which makes up over 94% of the product by weight. Other ingredients include antioxidants, water, and small amounts of additives to prevent foaming and provide color.
Antifreeze is made in a batch process using a tank with an agitator. Some tanks also have heating coils to help dissolve additives. The tank is usually made of mild steel or glass-fiber-reinforced resin, as rubber-lined tanks are not compatible with ethanediol.
Antifreeze manufacturers may or may not have their own blending facilities. In many cases, regional facilities offer blending and packaging services under contract, which is more cost-effective for distribution.
5. Antifreeze Uses
Antifreeze is primarily used to protect vehicle cooling systems from freezing and corrosion. It is also used in the cooling systems of stationary engines used in petroleum and natural gas pipelines, as well as in other industrial systems that need protection against freezing and corrosion in their cooling and heating systems.
Antifreeze is used because it lowers the freezing point of water and raises its boiling point. This helps to prevent liquid-cooled or heated equipment from being damaged when it operates in cold or hot environments.
When choosing an antifreeze, it is important to consider the following factors:
- Heat-carrying capacity of the fluid
- Viscosity of the fluid
- Materials used in the system’s metallurgy
- Nonmetallic components within the system
- Flammability characteristics of the fluid
- Toxicity profile of the fluid
- Other unique operational considerations
Here are some specific examples of industrial systems that use antifreeze:
- Food processing equipment
- Pharmaceutical manufacturing equipment
- Chemical processing equipment
- Power generation equipment
- Refrigeration and air conditioning systems
- Heating systems
- Solar energy systems
- Wind turbines
- Aircraft
- Ships
6. Toxicity of Antifreeze
Antifreeze toxicity is a concern because it is widely used in many different applications. The toxicity of antifreeze depends on its base composition and any additives that have been added. For example, arsenic compounds were once used as anticorrosives in antifreeze, which made them very toxic.
Ethylene glycol-based antifreeze is the most common type of antifreeze. It is relatively non-toxic when handled externally, but it can be very toxic if ingested. The lethal dose of ethylene glycol for adults is about 100 mL.
Inhalation of ethylene glycol vapors can also be hazardous, but this is not a major concern at normal ambient temperatures.
Propylene glycol-based antifreeze is much less toxic than ethylene glycol-based antifreeze. The lethal dose of propylene glycol for adults is over 1 liter. Propylene glycol is also non-irritating to the skin and eyes, and inhalation of its vapors does not appear to have any toxic effects.
Here are some tips for handling antifreeze safely:
- Wear rubber gloves when handling antifreeze or antifreeze solutions.
- Wear safety glasses, face shields, protective clothing, and general-purpose respiratory equipment when working with antifreeze.
- Avoid ingesting antifreeze. If you do accidentally ingest antifreeze, seek medical attention immediately.
- Avoid inhaling mists or vapors of hot ethylene glycol.
Reference
- Antifreezes; Ullmann’s Encyclopedia of Industrial Chemistry. – https://onlinelibrary.wiley.com/doi/10.1002/14356007.a03_023