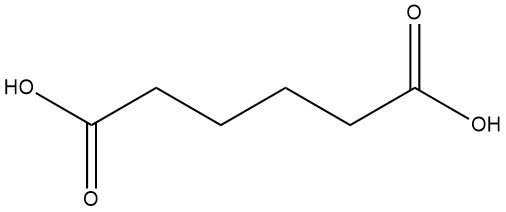
Adipic acid, also known as hexanedioic acid or 1,4-butanedicarboxylic acid, is an organic compound with the formula C6H10O4. It is a widely used aliphatic dicarboxylic acid that appears as a white crystalline solid.
While its occurrence in nature is limited, it is globally synthesized on a large scale. The main application of this compound is in the production of nylon 66 polyamide that was discovered by W. H. Carothers of DuPont in the early 1930s.
Since then, the manufacturing of nylon 66 polyamide fiber has emerged as a dominant process in the synthetic fiber industry on a global scale.
Table of Contents
1. Physical Properties of Adipic Acid
Adipic acid is obtained in the form of colorless and odorless crystals with a characteristic acidic taste. It demonstrates high solubility in methanol and ethanol, and it is also soluble in water and acetone.
However, its solubility in cyclohexane and benzene is quite limited. When crystallized, adipic acid forms monoclinic prisms when using water, ethyl acetate, or acetone/petroleum ether as solvents.
Here are a few of its physical properties:
Property | Value |
---|---|
melting point, °C | 152.1 |
boiling point, °C at 101.3 kPa | 337.5 |
boiling point, °C at 13.3 kPa | 265 |
boiling point, °C at 2.67 kPa | 222 |
boiling point, °C at 0.67 kPa | 191 |
boiling point, °C at 0.133 kPa | 159.5 |
Relative density (170 °C) | 1.085 |
Bulk density, kg/m³ | 600 - 700 |
Solubility, g/100 g water at 15 °C | 1.42 |
Solubility, g/100 g water at 40 °C | 4.5 |
Solubility, g/100 g water at 60 °C | 18.2 |
Solubility, g/100 g water at 80 °C | 73 |
Solubility, g/100 g water at 100 °C | 290 |
Dissociation constants k1 | 4.6 × 10-5 |
Dissociation constants k2 | 3.6 × 10-6 |
Specific heat of liquid (200 °C), kJ kg⁻¹ K⁻¹ | 2.719 |
Specific heat of vapor (300 °C), kJ kg⁻¹ K⁻¹ | 1.680 |
Heat of fusion, kJ/kg | 115 |
Heat of vaporization, kJ/kg | 549 |
Heat of solution in water, kJ/kg at 10 - 20 °C | -214 |
Heat of solution in water, kJ/kg at 90 - 100 °C | -241 |
Melt viscosity, mPa · s at 160 °C | 4.54 |
Melt viscosity, mPa · s at 193 °C | 2.64 |
2. Chemical Reactions of Adipic Acid
Adipic acid exhibits stability in atmospheric conditions, yet upon heating the molten acid beyond 230 – 250 °C, a certain degree of decarboxylation occurs, leading to the formation of cyclopentanone, with a boiling point of 131 °C.
This reaction is notably catalyzed by metal salts, including iron, calcium, and barium.
In comparison to glutaric or succinic acids, adipic acid demonstrates a much lesser tendency to form cyclic anhydrides by water loss.
Adipic acid displays reactivity at one or both carboxylic acid groups, engaging in the formation of salts, esters, amides, nitriles, and other compounds.
It generally withstands the action of most oxidizing agents, as evidenced by its production in nitric acid, but when exposed to nitric acid above 180 °C, adipic acid experiences autocatalytic attack, yielding carbon dioxide, water, and nitrogen oxides.
3. Production of Adipic Acid
In the initial stages of commercial adipic acid production, a two-step process involved the air oxidation of cyclohexane. The first step was the oxidation of cyclohexane to cyclohexanol and cyclohexanone at low conversion, followed by a high-conversion process that air-oxidized the mixture to yield adipic acid.
However, as of the year 2000, all large-scale manufacturing of adipic acid uses the nitric acid oxidation of cyclohexanol, cyclohexanone, or a blend of both substances known as ketone-alcohol (KA) oil.
The primary differences between these commercial processes lie in the method of producing the KA oil. Typically, the six carbon atoms forming the adipic acid backbone are sourced from benzene, which is hydrogenated to cyclohexane, or phenol, which is hydrogenated to cyclohexanol.
Subsequently, cyclohexane is oxidized with air to produce the KA oil. Over the past two decades, there has been a noticeable shift towards the more cost-effective cyclohexane-based process.
3.1. Nitric Acid Oxidation of Cyclohexanol
3.1.1. Reaction Mechanism
The second step of the conventional adipic acid production process, developed by DuPont in the late 1940s, involves the oxidation of cyclohexanol, cyclohexanone, or a mixture of both using nitric acid. Adipic acid is obtained with a yield greater than 90%.
During this process, carbon dioxide, nitrogen oxides, and some lower molecular mass dicarboxylic acids are formed as major byproducts. Additionally, certain byproducts arising from impurities present in the starting KA oil are also detected.
The chemical mechanism for this reaction was initially discussed in 1956 including considerations of kinetics and reactor design. Figure 1 provides a summary of the findings from these investigations.
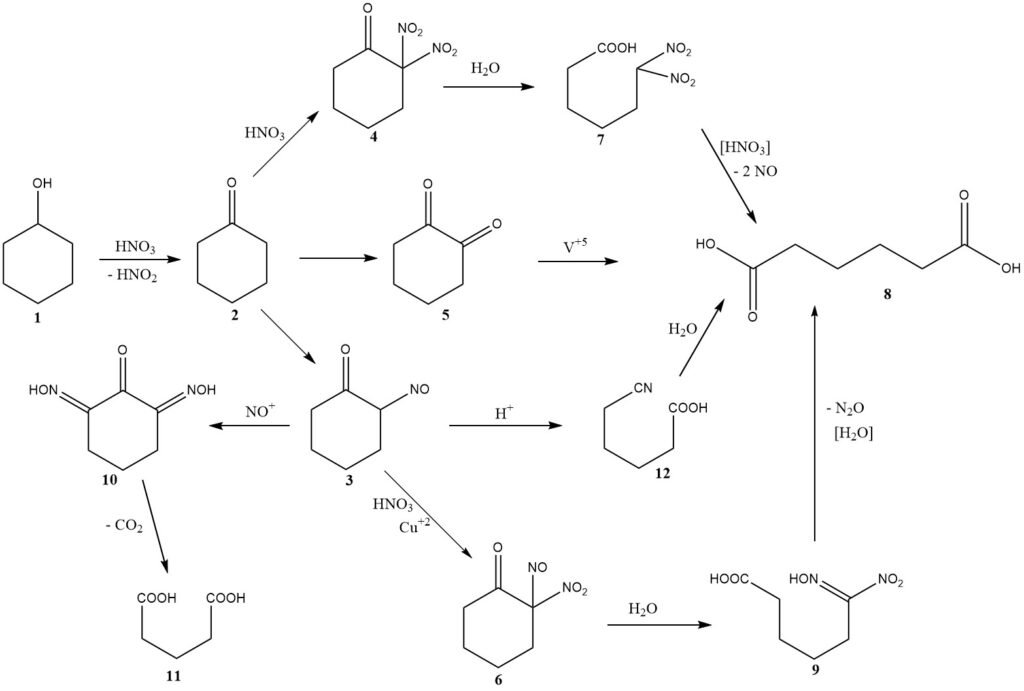
The oxidation of cyclohexanol (1) produces cyclohexanone (2) while generating nitrous acid. Then, cyclohexanone undergoes one of three possible pathways leading to the formation of adipic acid (8).
The major pathway involves nitrosation to produce 2-nitrosocyclohexanone (3), which then reacts further with nitric acid to form 2-nitro-2-nitrosoketone (6).
Hydrolytic cleavage of this intermediate yields 6-nitro-6-hydroximinohexanoic acid, also known as nitrolic acid (9), which further breaks down to give adipic acid and nitrous oxide, the main unrecovered nitric acid reduction products.
Typically, 2.0 moles of nitric acid are converted to nitrous oxide for each mole of adipic acid produced.
At higher temperatures, a second pathway becomes significant, involving nitration, leading to the formation of dinitroketone (4).
Early investigators proposed a third pathway, involving the intermediate formation of 1,2-diketone (5) or its dimer, where the use of a vanadium catalyst is required to achieve a good yield of adipic acid. The presence of vanadium suggests its significant contribution to the overall yield.
The intermediate nitrosoketone (3) can undergo two important side reactions. Multiple nitrosation leads to an intermediate (10), which loses carbon dioxide to produce glutaric acid (11) or succinic acid through subsequent reaction with nitric acid.
Copper metal is added to the nitric acid to inhibit these reactions. Under specific conditions with a relatively high steady-state concentration of the nitrosoketone (3) or the tautomeric oximinoketone, a Beckmann-type rearrangement occurs, leading to the minor formation of 5-cyanopentanoic acid (12), which is slowly hydrolyzed to adipic acid.
3.1.2. Commercial Nitric Acid Oxidation Processes
The nitric acid oxidation process for converting cyclohexanol-cyclohexanone (KA) into adipic acid remains similar to the early patent literature, but advancements have been made in byproduct removal, catalyst and nitric acid recovery, and reducing emissions of nitrous oxide, a greenhouse gas that was traditionally released into the atmosphere.
Due to the corrosive nature of nitric acid, manufacturing plants are constructed using materials like stainless steel (type 304L or better) or titanium in areas of high exposure.
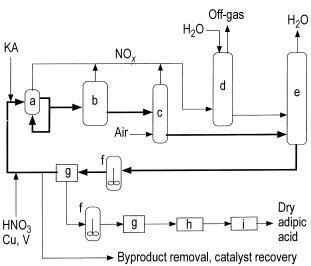
The process typically involves a reactor (a), functioning as a large heat exchanger, operating at 60 – 80 °C and 0.1 – 0.4 MPa pressure. The reactor receives the recycled nitric acid mother liquor (NML), KA feed material, makeup acid with 50 – 60% nitric acid, and a copper-vanadium catalyst.
The residence time in the reactor is less than 5 minutes. Some facilities use a second reactor (b) at elevated temperature (110 – 120 °C) to complete the reaction and reduce impurities before proceeding to crystallization.
The reaction is highly exothermic (6280 kJ/kg), and innovative reactor designs have been patented to control the heat of reaction and minimize energy usage. A surplus of recycled NML to KA feed stream is maintained (at least 3:1 up to 1000:1) to control the reaction and enhance the yield.
The product stream undergoes several steps, including passing through a bleacher (c) to remove excess dissolved nitrogen oxides, which are then recovered as nitric acid in the absorber (d).
The off-gas from the absorber can be utilized to initiate the oxidation at lower temperatures by passing it through the KA feed stream before feeding it to the oxidizer. The water produced in the process is removed in a concentrating still (e) operated under vacuum.
The concentrated product stream is either recycled back to the reactor with a portion diverted for product recovery or passed directly to product recovery before recycling the NML filtrate. Crude adipic acid is extracted from the NML loop by crystallization (f) and subsequently filtered or centrifuged (g).
This effluent stream, containing higher concentrations of glutaric acid, succinic acid, and byproducts, is further processed to recover the vanadium and copper catalysts and remove the byproduct acids. Metal recovery is typically accomplished through ion exchange.
The crude adipic acid from the first crystallizer (g) undergoes one or more recrystallization steps before proceeding to a dryer (h) and cooler (i). Alternatively, if dry adipic acid is not required, the crystals from the centrifuge/filter (g) can be dissolved in water and added to a solution of aqueous 1,6-hexanediamine to produce nylon salt.
Additional improvements to the conventional process have been described, especially concerning the separation and recovery of the dibasic acid byproducts.
Depending on the end use, the crude adipic acid can be refined to different degrees, but recrystallization from water is a common approach. Refluxing the crude adipic acid in 60% nitric acid with dissolved vanadium has been claimed to produce high-quality product.
3.2. Butadiene-Based Routes
In the early 1970s, BASF initiated an extensive research program to produce dimethyl adipate, a diester that could be later hydrolyzed to adipic acid. The process involved the carbomethoxylation of butadiene using carbon monoxide and methanol, catalyzed by cobalt and pyridine under high pressure.
This reaction yielded methyl 3-pentenoate, which was separated from byproducts through distillation. Subsequently, a second carbomethoxylation step at lower pressure, with a reduced pyridine to cobalt ratio, resulted in dimethyl adipate formation.
The hydrolysis of the diester to adipic acid and methanol was achieved through a high-yield catalytic process. Overall, the process exhibited an approximate yield of about 70% from butadiene. Although demonstrated at a pilot-plant scale, it has not been commercialized yet.
In the mid-1980s, DuPont also embarked on a significant program involving a butadiene-based route to adipic acid. In contrast to BASF’s diester approach, DuPont’s method involved the direct dihydrocarboxylation of butadiene to adipic acid (as shown in Figure 3).
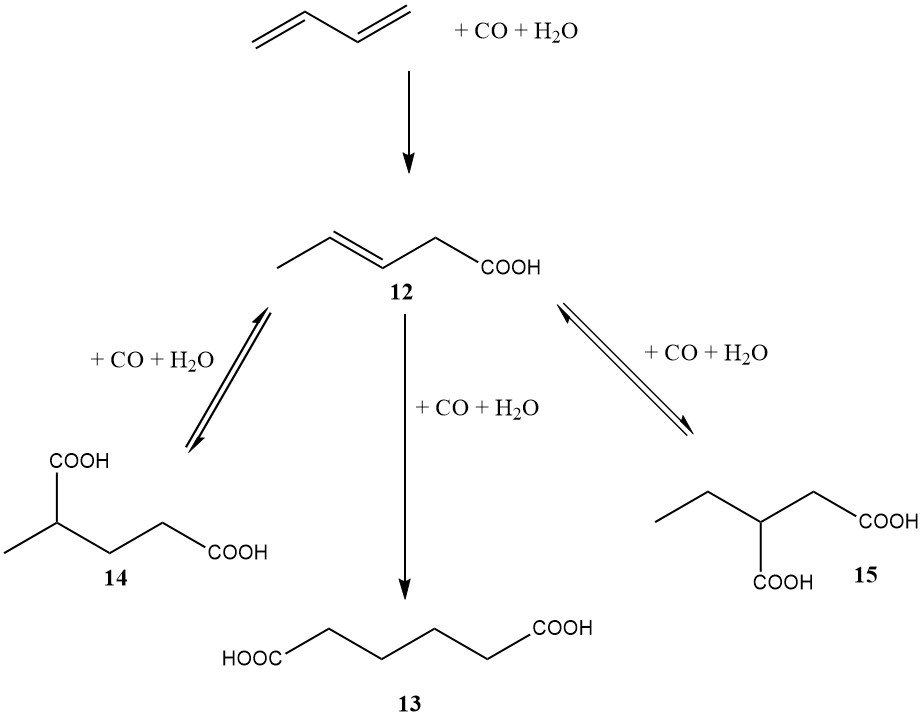
The first step, catalyzed by palladium, rhodium, or iridium, led primarily to 3-pentenoic acid. The second step, catalyzed by rhodium or iridium, resulted in the formation of adipic acid (13), 2-methylglutaric acid (14), and 2-ethylsuccinic acid (15).
The advantage of this process was the ability to isomerize 2-methylglutaric and 2-ethylsuccinic acids to adipic acid using the same catalyst system. The catalyst required a halide promoter, such as hydroiodic acid.
Pentanoic acid, a saturated carboxylic acid and a byproduct of the process, typically served as the solvent. Since the late 1980s, many major chemical companies have obtained numerous patents for variations of these butadiene-based routes.
3.3. Other Routes
Apart from the conventional two-step air/nitric acid oxidation of cyclohexane and the carboxylation/carbomethoxylation of butadiene, various other processes have been explored for the production of adipic acid.
Monsanto conducted research on the palladium halide catalyzed dicarbonylation of 1,4-disubstituted 2-butenes. This process involves the production of adipic acid from 1,4-dimethoxy-2-butene, carbon monoxide, and palladium chloride at 100 °C, followed by hydrogenation and hydrolysis of the resulting unsaturated dimethyl ester.
The one-step oxidation of cyclohexane using nitric acid, nitrogen dioxide, or air has also been investigated. The one-step all-air oxidation of cyclohexane is particularly economically attractive and has received extensive research attention.
Early studies were carried out by Gulf Research and Development, Asahi Chemical Industries, and other groups. For instance, cyclohexane can be oxidized in one step to adipic acid with a yield of 70 – 75% in the presence of a cobalt acetate catalyst in acetic acid as the solvent.
Recently, there has been renewed interest in this approach, resulting in several patents issued to companies like Redox Corporation and Bayer.
Adipic acid can also be produced by the ozonolysis of cyclohexene or by adding a carboxylic acid to cyclohexene and subsequently oxidizing the resulting ester with nitric acid.
Additionally, the formation of adipic acid derivatives via the electrolytic coupling of acrylates has been described.
These alternative processes represent ongoing research efforts to develop new methods for adipic acid synthesis.
4. Uses of Adipic Acid
Approximately 80% of the global adipic acid consumption is directed towards the production of nylon 66 fibers and resins.
A smaller amount of adipic acid is still utilized captively to produce adiponitrile.
Significant quantities of adipic acid are transformed into esters for various applications such as plasticizers, lubricants, and a range of polyurethane resins.
Monomeric esters are essential plasticizers for poly(vinyl chloride) and other resins, while polymeric esters are used when exceptionally high plasticizer levels are required.
Polyurethane resins that incorporate adipic acid are created from polyisocyanates and polyester polyols (adipates) and find use in various applications.
Adipic acid also serves as an acidulant in gelatins and jams and acts as a buffering or neutralizing agent in other food products.
Additionally, it is employed to modify the properties of unsaturated polyesters for use in reinforced plastics and alkyd coatings.
Adipic acid is utilized in polyamide-epichlorohydrin resins to enhance the wet strength of paper products.
Other miscellaneous applications include its use in adhesives, insecticides, tanning, dyeing, and the textile industries. Moreover, adipic acid and mixed dibasic acids (DBAs) are employed as buffers in flue gas desulfurization treatment in power plants.
5. Toxicology and Occupational Health
Adipic acid exhibits minor irritation and has low oral toxicity. The published lethal doses (LDLo) are 3600 mg/kg (rat, oral), LD50 275 mg/kg (rat or mouse, i.p.), and LD50 1900 mg/kg (mouse, oral).
Some chronic feeding tests showed delayed body weight increases, alterations in certain enzymes, and changes in urea and chloride levels in the blood. However, no teratogenic activity was observed in studies involving pregnant mice.
Metabolism studies using rats fed 14C-labeled adipic acid revealed the presence of both unchanged adipic acid and normal metabolic products in the urine.
Exposure to adipic acid may cause irritation to mucous membranes such as the eyes and respiratory tract, while prolonged skin exposure can lead to drying or irritation.
In cases of spills or leaks, personnel should be protected from inhalation or excessive skin contact. Dusting should be controlled, and measures should be taken to avoid static sparks. If spills occur, the area can be flushed with water.
While there is no established TLV (Threshold Limit Value) or MAK (Maximal Concentration Value), airborne exposure to adipic acid should be maintained below that of an organic nuisance dust: ACGIH (1979) recommends an 8-hour TWA (Time-Weighted Average) of 10 mg/m3 for total dust and 5 mg/m3 for respirable dust. The OSHA TLV for total dust is 15 mg/m3.
6. Adipic Acid Derivatives
6.1. Adiponitrile
The principal derivative of adipic acid is adiponitrile, also known as 1,6-hexanedinitrile or 1,4-dicyanobutane, Mr 108.14, boiling point 298 – 300 ◦C (at 101.3 kPa), 154 ◦C (at 1.3 kPa), and freezing point 2.4 ◦C.
Adiponitrile serves as an intermediate in the production of the major component of nylon 66, 1,6-hexanediamine. The earlier production methods involved the conversion of adipic acid to the dinitrile by liquid- or vapor-phase dehydration of the ammonium salt, using phosphoric acid or a boron – phosphorus catalyst. However, these methods are no longer employed by major nylon 66 producers.
Various routes have been used for adiponitrile production, including processes by Celanese, which produced 1,6-hexanediamine from ammonolysis of 1,6-hexanediol, obtained by hydrogenation of adipic acid.
6.2. Adipic acid Salts
Adipic acid forms water-soluble alkali metal and ammonium salts, as well as alkaline earth salts that are moderately soluble.
Their solubilities in 100 g of water are as follows: diammonium salt 40 g (14 ◦C), disodium salt 59 g of hemihydrate (14 ◦C), dipotassium salt 65 g (15 ◦C), calcium salt 4 g of monohydrate (13 ◦C), and 1 g of anhydrous salt (100 ◦C).
The most common salt is poly(1,6-hexanediammonium hexanedioate), produced by reacting adipic acid with 1,6-hexanediamine. This water-soluble salt, a precursor to nylon 66, can be conveniently shipped or stored before the final polyamidation, during which water is removed.
6.3. Adipic acid Esters and Polyesters
Esters and polyesters of adipic acid make up the largest non-polyamide market for adipic acid. Esters derived from long-chain alcohols are used as plasticizers and lubricants, while those from short-chain alcohols primarily serve as solvents.
Refluxing adipic acid with methanol in the presence of an acid catalyst yields monomethyl adipate, along with the diester. Electrolysis of the salt of the monoester (Kolbe synthesis) generates dimethyl sebacate, another polyamide precursor.
The esters dissolve readily in most organic solvents, with dimethyl adipate being the most commonly used solvent and di-2-ethylhexyl adipate being the most widely used plasticizer. Other simple adipate plasticizers include n-octyl, n-decyl, isodecyl, and isooctyl esters.
More complex polymeric plasticizers, prepared from glycols, account for a little less than half of the adipic acid-based plasticizers. Low molecular mass polyester polyols having hydroxyl end groups are used with polyisocyanates to produce polyurethane resins.
6.4. Adipic acid Anhydrides
The anhydride of adipic acid is usually obtained by dehydrating adipic acid, resulting in the formation of the linear, polymeric form. Distillation of the polymeric anhydride can produce the monomeric cyclic form, which is highly unstable and easily reverts to the linear, polymeric anhydride.
6.5. Adipic acid Amide
The diamide of adipic acid has a melting point of 228 ◦C and is virtually insoluble in cold water. Traditionally, it has been prepared by treating the dimethyl ester with concentrated ammonium hydroxide or by heating the diammonium salt of adipic acid in a stream of ammonia. Various substituted amides can be synthesized from amines using standard synthetic methods.
Reference
- Adipic Acid; Ullmann’s Encyclopedia of Industrial Chemistry. – https://onlinelibrary.wiley.com/doi/10.1002/14356007.a01_269
FAQ
Adipic acid is a white, crystalline organic compound with the chemical formula C6H10O4. It belongs to the class of aliphatic dicarboxylic acids and is often referred to as hexanedioic acid. Adipic acid is commercially significant and widely used in various industries due to its versatile properties.
Adipic acid has diverse applications across industries. Its primary and most prominent use is in the production of nylon 66 polyamide, a crucial material for manufacturing fibers and resins. Besides, adipic acid is utilized in the production of esters, polyurethane resins, plasticizers, lubricants, and as an acidulant or buffering agent in the food industry. It is also employed in the synthesis of various chemical derivatives.
Adipic acid can be produced through several methods. The most common commercial processes involve the two-step air/nitric acid oxidation of cyclohexane or direct hydrocyanation of butadiene. The former method starts with cyclohexane oxidation to produce cyclohexanol and cyclohexanone, followed by their oxidation with nitric acid to obtain adipic acid. The latter method involves the hydrocyanation of butadiene to produce adiponitrile, which is subsequently hydrogenated and hydrolyzed to yield adipic acid.
Adipic acid exhibits solubility in various solvents. It is soluble in methanol, ethanol, water, and acetone. However, its solubility is relatively lower in cyclohexane and benzene.
Adipic acid is generally considered safe when used in accordance with the recommended guidelines and concentrations. It is a minor irritant and has low oral toxicity. The lethal dose for rats (LDLo) is relatively high (3600 mg/kg), but caution should be exercised to avoid excessive inhalation or skin contact. Adipic acid is not known to be teratogenic, and its metabolic products are excreted in urine.
The chemical formula of adipic acid is C6H10O4.
Adipic acid is also known by the name “hexanedioic acid”.