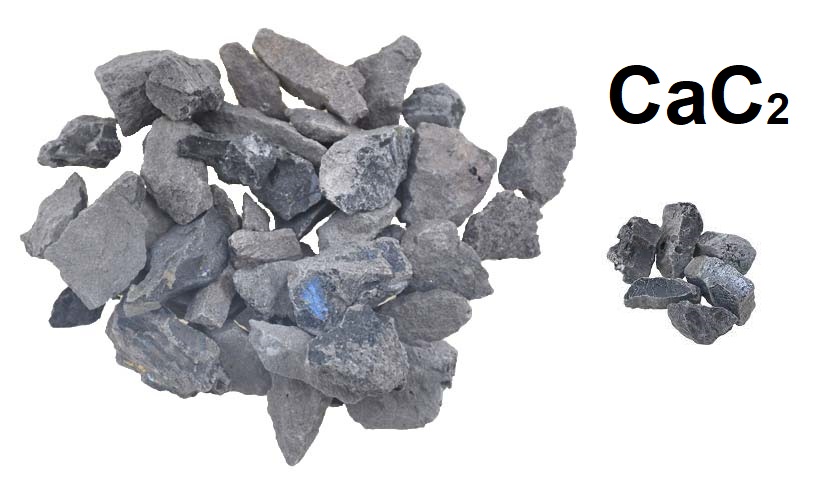
Calciumcarbid, auch Calciumacetylid genannt, ist eine grauschwarze, kristalline Verbindung mit der chemischen Formel CaC2. Bei Kontakt mit Wasser entsteht Acetylen, ein leicht entzündliches Gas, das einst häufig zum Beleuchten und Schweißen verwendet wurde.
Unter den Carbiden ist Calciumcarbid das industriell bedeutendste (CAS-Nummer: 75-20-7). Es bleibt ein wesentlicher Werkstoff der Acetylen-Schweißgasindustrie, insbesondere in Regionen, in denen Rohstoffe und Energie leicht verfügbar und Erdöl knapp sind.
Inhaltsverzeichnis
Calciumcarbid wird in zahlreichen Ländern als Vorläufer für verschiedene Produkte auf Acetylenbasis, insbesondere Poly(vinylchlorid) (PVC) und bei der Herstellung von Calciumcyanamid hergestellt.
Es findet auch Verwendung bei der Entschwefelung geschmolzener Metalle wie Eisen und Stahl sowie in Gießereien, wo es Teil von Metallbehandlungsadditiven ist.
Die chemische Zusammensetzung von Calciumcarbid wurde erstmals 1862 von Wöhler identifiziert und durch die Reaktion einer Calcium-Zink-Legierung mit Kohle erreicht. Zuvor hatten mehrere Forscher die Verbindung im Labor hergestellt, wobei sie häufig Lichtbögen auf Kohle- oder Koksprodukten in Gegenwart von Kalziumverbindungen verwendeten.
Im späten 19. Jahrhundert entwickelte sich die Produktion im industriellen Maßstab in elektrothermischen Öfen. Moissan in Frankreich und Morehead und Willson in den Vereinigten Staaten legten zwischen 1885 und 1895 unabhängig voneinander den Grundstein für diesen Technologiesprung. Der erste betriebsfähige industrielle Hartmetallofen wurde 1895 von der Willson Aluminium Company in Spray, USA, gebaut.
Bertolus schlug 1897 die Verwendung mehrphasiger elektrischer Ströme für Industrieöfen vor. Helfenstein folgte 1904 mit einem Drehstromofen mit drei Elektroden. Diese frühen Öfen mit Leistungen von 3000 bis 7500 kW verfügten sogar über Abgasrückgewinnungssysteme (Helfenstein-Barriere). Innerhalb eines Jahrhunderts wurden 40-MW-Öfen üblich.
Moderne große Elektroöfen mit einer Leistung von bis zu 60 MW verwenden Soderberg-Elektroden und sind vollständig geschlossen, was die Rückgewinnung von Kohlenmonoxid als Nebenprodukt ermöglicht.
Die jüngsten Fortschritte konzentrierten sich auf die Entwicklung zuverlässiger, mittelgroßer geschlossener Öfen, die besser an die Marktanforderungen und verfügbaren Rohstoffe angepasst sind.
Das carbothermische Verfahren, das von BASF in Deutschland zwischen 1940 und 1960 eingesetzt wurde, stellte einen alternativen Weg zur Calciumcarbidproduktion dar, wurde jedoch inzwischen aufgegeben.
1. Physikalische Eigenschaften von Calciumcarbid
Calciumcarbid, CaC2, ist eine binäre ionische Verbindung mit einer Molmasse von 64,10 g/mol. In reiner Form ist es farb- und geruchlos. Allerdings weist technisches Material aufgrund von Verunreinigungen häufig verschiedene Grautöne bis hin zu bräunlichem Schwarz auf, gelegentlich mit violetten oder rotbraunen Farbtönen.
Der charakteristische Phosphingeruch von technischem Calciumcarbid entsteht durch Spuren von Calciumphosphid, die mit Feuchtigkeit reagieren.
Reines Calciumcarbid besitzt einen hohen Schmelzpunkt von 2160 °C und zersetzt sich oberhalb von 2500 °C vollständig. Es gibt vier verschiedene kristallographische Modifikationen:
- Phase I: tetragonal, stabil zwischen 25 und 440 °C (dominant in kommerziellem Hartmetall)
- Phasen II und III: geringere Symmetrie, stabil unter 440°C
- Phase IV: kubisch flächenzentriert, stabil über 440°C
Die Umwandlungswärme bei 440°C beträgt 8,68 J/g. Bemerkenswerterweise zeigt das CaC2-CaO-Phasendiagramm ein einfaches eutektisches Verhalten ohne Verbindungsbildung oder feste Lösungen im festen Zustand. Erst oberhalb der Liquiduslinie werden die Komponenten vollständig mischbar. Verunreinigungen in technischem Hartmetall senken dessen Liquidustemperatur.
Calciumcarbid hat eine durchschnittliche spezifische Wärmekapazität von 1047 J kg⁻¹ K⁻¹ zwischen 20 und 440 °C und eine Schmelzwärme von 1470 J/g reines Material. Seine Standardbildungsenthalpie aus Elementen bei 298 K beträgt -59,4 kJ/mol und die Standardentropie beträgt 70,3 J mol⁻¹ K⁻¹.
Die elektrische Leitfähigkeit von Calciumcarbid liegt zwischen 100 und 1000 S m⁻¹ und hängt stark von der Reinheit und der Temperatur ab.
2. Chemische Eigenschaften von Calciumcarbid
Calciumcarbid, CaC2, durchläuft eine Reihe wichtiger chemischer Reaktionen:
Synthese von Calciumcyanamid: Diese exotherme Reaktion (ΔH₂₉₈ = -289 kJ/mol) wandelt Calciumcarbid und Stickstoffgas in Calciumcyanamid um Kohlenstoff: CaC₂ + N₂ → CaCN₂ + C.
Hydrolyse zu Acetylen: Durch die Reaktion mit Wasser entstehen leicht Acetylen, Calciumhydroxid und Wärme (ΔH₂₉₈ = -128,4 kJ/mol): CaC₂ + 2 H₂O → C₂H₂ + Ca(OH)₂.
Eine effiziente Acetylenproduktion erfolgt unterhalb von 300 °C, wobei reines Calciumcarbid 346,89 l/kg (trocken) bei 0 °C und 101,3 kPa (etwas höher bei 15 °C) ergibt C mit vorhandenem Wasserdampf). Bei hohen Temperaturen entstehen stattdessen Kalziumoxid, Wasserstoff und Kohlendioxid.
Reaktion mit Schwefel: Calciumcarbid reagiert mit Schwefel in geschmolzenem Eisen unter Bildung von Calciumsulfid und setzt Kohlenstoff frei: CaC2 + [S]Fe → CaS + 2 [C]Fe
Hydrierung: Bei der Hydrierung von Calciumcarbid entstehen unter Druck nicht nur Calciumhydrid und Methan, sondern auch andere Kohlenwasserstoffe.
Calciumcarbid löst sich in verschiedenen geschmolzenen Salzen und ermöglicht so vielfältige Reduktionsreaktionen.
Elektrolyse: Die Elektrolyse von gelöstem Calciumcarbid in geschmolzenen Salzen ergibt Calcium an der Kathode und Kohlenstoff an der Anode.
3. Herstellung von Calciumcarbid
Während die Herstellung von reinem Calciumcarbid akademisches Interesse genießt, stehen bei der industriellen Produktion technisch hochwertige Materialien für praktische Anwendungen im Vordergrund. Dies beruht größtenteils auf der Hochtemperaturreaktion von Branntkalk (CaO) mit kohlenstoffhaltigen Quellen wie Koks und Anthrazit:
CaO + 3 C → CaC2 + CO (ΔH₂₉₈ = +465 kJ/mol)
Die Reaktionsgeschwindigkeit wird erst oberhalb von 1600°C signifikant. Bei Temperaturen über 2000 °C kommt es jedoch zu unerwünschten Nebenreaktionen, insbesondere:
CaC2 → Ca + 2 C
CaC2 + 2 CaO → 3 Ca + 2 CO
Daher laufen industrielle Prozesse im Temperaturbereich von 1800–2100 °C ab und liefern Calciumcarbid in technischer Qualität mit einem CaC2-Gehalt von etwa 80 % . Der Rest besteht hauptsächlich aus CaO, mit zusätzlichen Verunreinigungen wie SiO₂ und Al₂O₃ aus Rohstoffen.
Hohe Temperaturen sind für die Calciumcarbidproduktion von entscheidender Bedeutung und erfordern zwei mögliche Ansätze:
- Elektrothermischer Schachtofen: Schmilzt das kohlenstoffhaltige Material mit CaO in einem kurzen Ofen und führt dabei direkt elektrische Energie ein.
- Sauerstoffverbrennungsschachtofen: Verbrennt kohlenstoffhaltiges Material mit reinem oder angereichertem Sauerstoff in Gegenwart von CaO.
Während die letztere Methode Synthesegas als Nebenprodukt lieferte, wurde sie nach 50 Jahren aufgrund der günstigeren Produktion desselben Gases aus Erdöl endgültig aufgegeben. Heutzutage nutzt die gesamte kommerzielle Calciumcarbidproduktion den ersten elektrothermischen Ansatz.
3.1. Rohstoffe
Die Rohstoffe für die Calciumcarbid-Produktion, die sogenannte „Bürde“ im elektrothermischen Ofen, spielen eine entscheidende Rolle für Effizienz und Produktqualität. Diese Materialien bestehen aus zwei Hauptkomponenten: einer kohlenstoffhaltigen Quelle und einer kalkhaltigen Komponente.
Partikelgröße, Festigkeit und Leitfähigkeit haben einen erheblichen Einfluss auf die Ofenleistung und Betriebsstabilität. Kleinere offene Öfen bieten Flexibilität bei der manuellen oder mechanischen Anpassung dieser Eigenschaften, während geschlossene Öfen mit hoher Kapazität strengere Spezifikationen für den unbeaufsichtigten Betrieb erfordern.
Flüchtige Stoffe und der Aschegehalt beeinflussen die Reaktionseffizienz und die Abfallerzeugung. Moderne geschlossene Öfen ermöglichen die Herstellung feinkörniger Materialien durch direktes Einspritzen durch Hohlelektroden. Verunreinigungen wie Metalloxide können unerwünschte Nebenreaktionen verursachen und erfordern eine sorgfältige Handhabung.
Kohlenstoffquelle
- Koks: Koks wird aus Steinkohle oder Braunkohle gewonnen und ist aufgrund seiner Verfügbarkeit und geeigneten Eigenschaften das weltweit am häufigsten verwendete kohlenstoffhaltige Material. Die Korngröße liegt typischerweise zwischen 3 und 25 mm, wobei feinere Fraktionen über Elektroden injiziert werden. Für eine optimale Produktion muss der Feuchtigkeitsgehalt unter 2 % und der Aschegehalt unter 15 % liegen.
- Andere Optionen: Unkalzinierter Anthrazit und Petrolkoks können teilweise in geschlossenen Öfen verwendet werden, erfordern jedoch eine Kalzinierung, um die flüchtigen Bestandteile für Sole auf unter 2 % zu reduzieren verwenden. Holzkohle findet nur in kleinen offenen Öfen Anwendung.
Kalkhaltige Komponente
- Branntkalk: Die vorherrschende Wahl bei großen geschlossenen Öfen, die eine Korngröße von 6–50 mm und die Einspritzung feinerer Fraktionen erfordern. Für einen effizienten Betrieb sollte der Magnesiumgehalt unter 2 % liegen. Kalk muss weich und dennoch haltbar sein, in modernen Brennöfen hergestellt werden können und einen CO2-Gehalt unter 2 % haben.
- Recyceltes Calciumhydroxid: Dieses Nebenprodukt der Acetylenerzeugung kann nach der Granulierung oder Brikettierung als billiger Rohstoff verwendet werden, es bilden sich jedoch Verunreinigungen schränkt sein Recyclingpotenzial ein.
Kunststoffabfälle werden zunehmend als sekundäre Kohlenstoffquelle untersucht, wobei aufgrund der unerwünschten Verdampfung und Reaktion mit Kalzium strenge Vorgaben für den Chlorgehalt (max. 12 %) gelten.
Tabellen 1 und 2 liefern Beispiele typischer Rohstoffzusammensetzungen für die Calciumcarbidproduktion.
Material | Fester Kohlenstoff | Flüchtiger Kohlenstoff | Feuchtigkeit | Schwefel | Asche |
---|---|---|---|---|---|
Metallurgischer Koks | 89,0 | 0,8 | 0,8 | 0,8 | 9.4 |
Anthrazit | 80,0 | 6.0 | 8.0 | 0,8 | 6.0 |
Petrolkoks | 81,6 | 9.0 | 8.0 | 1,9 | 0,3 |
Komponente | Neue Limette | Recycelter Kalk |
---|---|---|
Gesamt-CaO | 93,8 | 89,0 |
Freies CaO | 93,6 | - |
CaSO4 | 0,4 | - |
SiO2 | 1.3 | 2.9 |
Fe2O3 | 0,4 | 0,4 |
Al2O3 | 0,5 | 2.4 |
MgO | 0,8 | 0,8 |
CO2 | 2.7 | 3.0 |
P2O5 | 0,015 | 0,01 |
Glühverlust (CO2) | 0,5 | 0,5 |
3.2. Elektrothermische Reduzierung
Das Rohstoffgemisch für die Calciumcarbid-Herstellung wird in einem Kurzschacht-Elektroofen einer Hochtemperaturverarbeitung unterzogen. Untersuchungen deuten auf einen zweistufigen Reaktionsmechanismus hin:
- Kalzination: CaO + C → Ca + CO
- Karbidbildung: Ca + 2 C → CaC2
Die primäre Reaktionszone im Ofen liegt in einer geschmolzenen CaC2-CaO-Phase. Das komplexe Zusammenspiel von elektrischem Strom, Wärmeversorgung, Temperatur und chemischen Reaktionen ist jedoch noch immer nicht vollständig verstanden.
Der geschwindigkeitsbestimmende Schritt beinhaltet wahrscheinlich den Transport von gelöstem CaO in der Schmelze zur Kokskornoberfläche, wo die Bildung von CaC2 stattfindet. Dieses neu gebildete CaC2 löst sich leicht wieder in der Schmelze auf.
Zuletzt wird das geschmolzene Calciumcarbid vom Ofenboden abgestochen.
3.3. Öfen
Calciumcarbidöfen können anhand von drei Hauptaspekten kategorisiert werden:
- Elektrische Versorgung: Einphasig oder dreiphasig.
- Elektrodenanordnung: Seriell, symmetrisch oder andere Konfigurationen.
- Luftausschluss: Offen, halb abgedeckt oder geschlossen.
1. Einphasenöfen
Diese 1928 entwickelten Öfen arbeiten mit hohem Strom und niedriger Spannung und erreichen Leistungsfaktoren von bis zu 0,95. Allerdings sind sie weniger effizient und im Vergleich zu dreiphasigen Designs in Ungnade gefallen.
2. Dreiphasenöfen
Der heute vorherrschende Typ, kategorisiert nach Elektrodenanordnung:
- Seriennummer: Bietet Vorteile bei der Einspeisung und Verteilung, aber Einschränkungen bei der Gasrückgewinnung und dem Stromverbrauch.
- Symmetrisch: Hochleistungsdesign mit ausgewogenen Leistungsfaktoren und überlappenden Schmelzzonen bei höherer Leistung.
3. Halbgedeckte Öfen
Frühe Öfen gaben CO direkt ab, was zu Umweltverschmutzung führte. Moderne Designs verwenden Gassammelhauben, geschlossene Öfen bieten jedoch die beste Umgebungskontrolle.
4. Geschlossene Öfen
Diese modernen Öfen bieten eine 100-prozentige Gasrückgewinnung und minimale Umweltbelastung. Zu den wichtigsten Komponenten gehören:
- Herd: Konstruiert aus Stahl und feuerfesten Materialien, um hohen Temperaturen standzuhalten.
- Elektroden: Soderberg-Elektroden werden aufgrund ihrer Kosteneffizienz und ihres kontinuierlichen Betriebs bevorzugt. Hohlelektroden ermöglichen die direkte Einspritzung von Rohstoffen.
- Stromversorgung: Transformatoren mit Ölkühlung und steuerbarer Leistung zur Bewältigung von Schwankungen.
- Leistungsdiagramm: Stellt das komplexe Zusammenspiel von Widerständen und Reaktanzen innerhalb des Ofens dar.
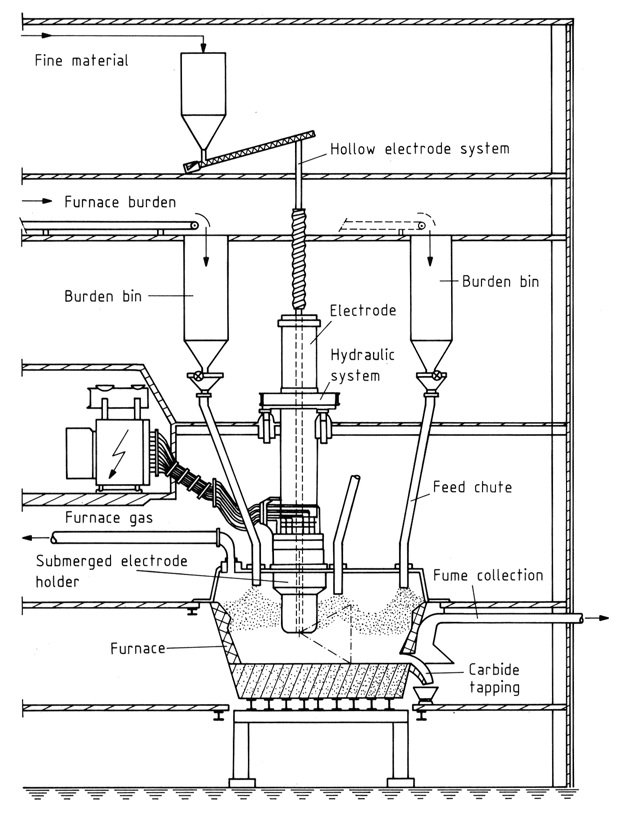
Steuerung und Betrieb
Dreiphasenöfen erfordern eine Impedanzkontrolle durch Anpassung der Eintauchtiefe der Elektrode, um Leistung und Ofenwiderstand zu steuern. Geschlossene Hauben ermöglichen möglicherweise die Manipulation der Futterrutschen, um den Widerstand weiter zu regulieren.
3.4. Industrieller Prozess
Die Produktion von Calciumcarbid beginnt mit der Schichtung groben Kokses im Ofen. Die Elektroden werden vorsichtig in Richtung des Kokses abgesenkt, bis Lichtbögen den Kontakt signalisieren. Wenn der Koks Rotglut erreicht, wird der Ofenboden nach und nach mit Möller beschickt und die Leistung wird schrittweise erhöht, um sich an die steigende Temperatur anzupassen.
Für einen optimalen Ofenbetrieb ist eine gleichmäßige Möllerzufuhr unerlässlich. Geringfügige Schwankungen in der Zusammensetzung können durch Kalkzusätze abgemildert werden, was aufgrund der geringeren Leitfähigkeit von Kalk ein tieferes Eintauchen der Elektrode erforderlich macht.
Eine zu hohe Elektrodenhöhe birgt die Gefahr der Karbidbildung in den oberen Möllerschichten, was möglicherweise zu einem gefährlichen „Ausspritzen“ der Schmelze führt. Die Aufrechterhaltung der Gasdurchlässigkeit innerhalb des Feststoffmaterials ist für eine gleichmäßige Produktion von entscheidender Bedeutung.
Der Druck der Ofenhaube muss sorgfältig mit dem atmosphärischen Druck abgeglichen werden, um das Eindringen von Sauerstoff oder das Austreten von Kohlenmonoxid zu verhindern. Bei großen Ofenanlagen werden häufig zentrale Kontrollräume für einen effizienten Betrieb und eine umfassende Überwachung der Umgebungsparameter eingesetzt.
Beim Abstich wird entweder der Ofen mechanisch geöffnet oder mithilfe eines Lichtbogens ein Abstichloch erzeugt. Eine spezielle gebrannte Elektrode erleichtert das Schmelzen von Karbid, das je nach Reinheit bei Temperaturen zwischen 1700 und 2100 °C fließt, in speziell entwickelte gekühlte Gusseisenpfannen.
Aufgrund seines hohen Schmelzpunkts und des schnellen Wärmeverlusts erstarrt technisches Hartmetall (80 % CaC2) schnell, was eine kontinuierliche Wartung des Abstichlochs mit Stahlstangen erforderlich macht.
Kettenvorhänge, Drahtgeflechte und Stahlabschirmungen schützen die Bediener während des Gewindeschneidvorgangs vor heißen Gasen, Staub und potenziell gefährlichem herausspritzendem Karbid. Eine spezielle Schutzausrüstung, einschließlich aluminiumbeschichteter feuerfester Mäntel, dunkler Brillen und Schutzvisiere, ist für das gesamte Personal, das an Absticharbeiten beteiligt ist, obligatorisch.
Rauchabsaugsysteme entfernen effektiv schädliche Aerosolpartikel und reduzieren so die Umweltbelastung.
Moderne hydraulische Manipulatoren, die mit austauschbaren Werkzeugen ausgestattet sind, haben die Gewindeschneidverfahren revolutioniert, indem sie die Notwendigkeit einer direkten menschlichen Beteiligung minimiert und die Sicherheit erhöht haben.
Durch die Reduktion von Verunreinigungen wie Fe2O3 und SiO2 durch Kohlenstoff entsteht Ferrosilizium, das sich aufgrund seiner höheren Dichte unterhalb der Karbidschmelze absetzt und typischerweise beim Abstich ausfließt. Sein im Vergleich zu Karbid niedrigerer Schmelzpunkt erfordert jedoch ständige Wachsamkeit und vorbeugende Maßnahmen, um Leckagen durch Risse in der Ofenauskleidung zu verhindern.
4. Verwendung von Calciumcarbid
Calciumcarbid wird bei der Herstellung von Acetylen, der Reaktion mit Stickstoff zu Calciumcyanamid und der Entschwefelung heißer Metalle verwendet.
Während seine Verwendung als Vorläufer für Schwerchemikalien aufgrund der Dominanz der Petrochemie seit den 1960er Jahren zurückgegangen ist, bleibt aus Calciumcarbid gewonnenes Acetylen beim Gasschweißen wichtig. Seine Anpassungsfähigkeit und Tragbarkeit machen es für Aufgaben wie den Rohrleitungsbau unverzichtbar, selbst angesichts der Fortschritte bei den Materialverbindungstechniken.
Acetylen findet weiterhin Nischenanwendungen in der Synthese spezifischer Chemikalien, wie zum Beispiel Butindiol für Kunststoffe und Fasern und Acetylenruß für Trockenbatterien.
Die Reaktivität von Calciumcarbid mit Schwefel macht es zu einem wertvollen Werkzeug in der Metallurgie. Strenge Stahlqualitätsstandards verlangen einen minimalen Schwefelgehalt und die Entschwefelung mit Kalziumkarbid vor dem Stahlkonverter erweist sich als die wirtschaftlichste Methode.
Das Einspritzen von fein gemahlenem (< 100 mm) Calciumcarbid in die Metallschmelze reduziert den Schwefelgehalt effektiv, typischerweise von 0,2 % auf bis zu 0,001 %. Kombinationen von Calciumcarbid mit Magnesium werden zunehmend erforscht, um die Reaktivität im heißen Metall zu verbessern.
In Gießereien wird grobkörniges Calciumcarbid, oft kombiniert mit Zusatzstoffen wie Flussspat, zur Entschwefelung verwendet. Die Mischung wird nach dem Abstich und vor dem Gießen in die Pfanne eingerührt und trägt so zu einer verbesserten Metallqualität bei.
5. Toxikologie von Calciumcarbid
Calciumcarbid wird als stark augenreizend und hautreizend mit geringem Sensibilisierungspotenzial eingestuft.
Handelsübliches Calciumcarbid kann aufgrund seiner ätzenden/reizenden Eigenschaften beim Einatmen akute Schäden verursachen.
Für Calciumcarbid selbst liegen nur begrenzte Daten vor, bestimmte Spurenbestandteile geben jedoch Anlass zur Sorge:
- Phosphin: Es liegen Hinweise auf eine genotoxische Wirkung vor, aber seine geringe Konzentration in Calciumcarbid (< 0,1 %) minimiert das Risiko.
- Arsen: Obwohl bei Bei einer Konzentration von ca. < 0,1 % kann dieses potenzielle Karzinogen bei Kontakt mit Wasser zur Bildung von Arsenwasserstoff führen. Die aktuellen CLP-Kriterien erfordern jedoch keine Einstufung als Karzinogen.
Aufgrund des geringen Arsengehalts und seiner begrenzten Umwandlung in Arsin ist eine Einstufung als krebserregend nicht gerechtfertigt.
Aufgrund der schnellen Zersetzung im Wasser ist die Ökotoxizität der reinen Verbindung vernachlässigbar.
Untersuchungen an Fischen, Daphnien und Algen geben Aufschluss über die Toxizität von Abbauprodukten und Nebenbestandteilen.
Der hohe LC50-Wert für Fische (> 50 mg/L) und der EC50-Wert für Daphnien (4,42 mg/L) spiegeln wahrscheinlich die Toxizität von Schwefelwasserstoff wider, der aus der Verunreinigung Calciumsulfid entsteht.
Insgesamt deuten Studien zum biologischen Abbau darauf hin, dass Calciumcarbid und seine Abbauprodukte leicht biologisch abbaubar sind.
Referenz
- Calciumcarbid; Ullmanns Enzyklopädie der industriellen Chemie. – https://onlinelibrary.wiley.com/doi/10.1002/14356007.a04_533.pub2