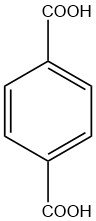
Terephthalic acid is an organic diacid with the chemical formula C6H4(CO2H)2. It is a white crystalline solid classified as commodity chemical, Terephthalic acid exists commercially in a free-flowing powder form that comprises rounded crystals. When recrystallized slowly, it forms needles.
The research work conducted by WHINFIELD and DICKSON in Britain in the 1940s brought terephthalic acid to the forefront of the scientific community.
In the United States, CAROTHERS and his colleagues had already established the potential of producing high molecular weight linear polyesters by reacting diacids with diols. However, they had employed aliphatic diacids and diols which yielded polyesters that were unsuitable for spinning into fibers.
WHINFIELD and DICKSON discovered that symmetrical aromatic diacids produced high-melting, crystalline, and fiber-forming materials. Consequently, poly(ethylene terephthalate) emerged as the most extensively produced synthetic fiber.
In 1992, terephthalic acid and dimethyl terephthalate ranked about 25th in terms of tonnage of all chemicals manufactured globally and about tenth in organic chemicals.
Table of Contents
1. Production of Terephthalic acid
p-Xylene is a critical feedstock for the production of terephthalic acid and dimethyl terephthalate, which are essential in the manufacturing of polyester fibers, films, and resins.
A number of oxidation catalysts and conditions have been developed that lead to nearly quantitative oxidation of the methyl groups present in p-xylene, leaving the benzene ring virtually untouched.
These catalysts are generally based on cobalt, manganese, and bromine or cobalt with a co-oxidant like acetaldehyde. The oxidant used in all of the processes is oxygen, and acetic acid is used as a reaction solvent in all but one process.
1.1. Production of Terephthalic acid by Amoco Oxidation
The Amoco oxidation process, discovered by Scientific Design, accounts for roughly 70% of the terephthalate feedstock produced globally. It is the most widely used catalyst system and is used by almost all new plants.
Mitsui Petrochemical, now Mitsui Sekka, also developed a commercial process and was an early licensee of Mid-Century and Amoco also have licensed the process.
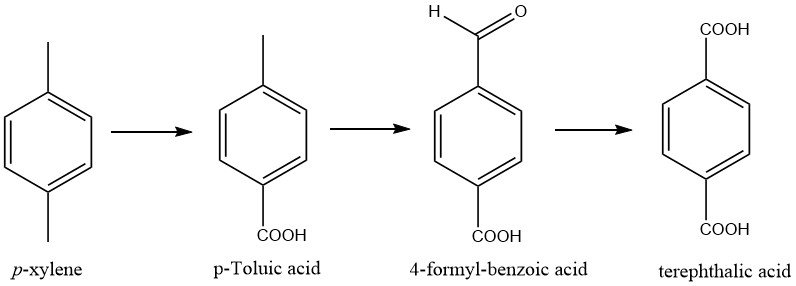
The process for producing terephthalic acid and dimethyl terephthalate involves using p-xylene as a feedstock. This feedstock is oxidized using a soluble cobalt-manganese-bromine catalyst system, resulting in nearly quantitative oxidation of the methyl groups with minimal xylene losses.
The reaction is carried out using acetic acid as the solvent and compressed air as the oxidant. Various cobalt and manganese salts can be used, and the bromine source can be HBr, NaBr, or tetrabromoethane.
Due to the highly corrosive bromine-acetic acid environment, the process requires the use of titanium-lined equipment in some parts.
The feed mixture, consisting of p-xylene, acetic acid, catalyst, and water, is continuously fed to the oxidation reactor. The reactor is operated at temperatures ranging from 175 to 225 °C and at pressures ranging from 1500 to 3000 kPa.
Compressed air is added in excess of stoichiometric requirements to provide measurable oxygen partial pressure and achieve high p-xylene conversion.
The reaction is highly exothermic, releasing water and heat. The reaction of 1 mol p-xylene with 3 mol dioxygen results in the production of 1 mol terephthalic acid and 2 mol water.
Only four hydrogen atoms, representing slightly over 2 wt % of the p-xylene molecule, are not incorporated into terephthalic acid.
Terephthalic acid is not highly soluble in the solvent, causing it to precipitate as it forms. This results in a three-phase system consisting of solid terephthalic acid crystals, solvent with some dissolved terephthalic acid, and vapor made up of nitrogen, acetic acid, water, and a small amount of oxygen.
The heat of the reaction is removed by solvent evaporation, and a residence time up to 2 h is used. The yield of terephthalic acid is over 95 mol %, with over 98 % of the p-xylene reacting.
However, small amounts of p-xylene and acetic acid are lost due to complete oxidation to carbon oxides, and impurities such as oxidation intermediates are present in reactor effluent.
The excellent yield and low solvent loss in a single reactor pass account for the universal selection of this technology for new plants.
The oxidation of the methyl groups in p-xylene occurs in steps, with two intermediates, p-toluic acid and 4-formylbenzoic acid, formed during the process.
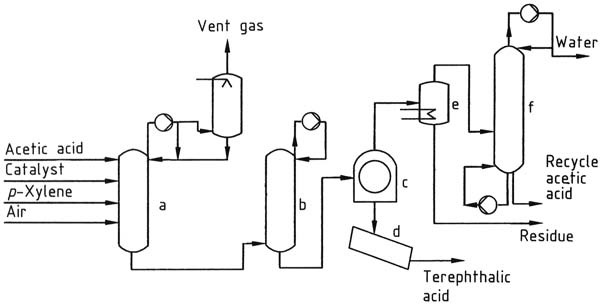
1.2. Production of Terephthalic acid by Multistage Oxidation
Numerous companies in Japan have devised methods to decrease the concentration of 4-formylbenzoic acid to 200 – 300 ppm by implementing more rigorous oxidation procedures.
Such methods have made it possible to omit a separate purification step as the concentration of 4-formylbenzoic acid is adequately low for terephthalic acid to be used as feedstock for some polyester products that do not necessitate high feedstock purity.
This category of terephthalic acid is commonly referred to as medium-purity terephthalic acid, which constitutes approximately 11% of the overall terephthalic acid produced.
The majority of these procedures employ the catalyst system discovered by Scientific Design.
Mitsubishi Kasei and its licensees produce most of the medium-purity terephthalic acid. They have named this product Q-PTA, which generally exhibits a 4-formylbenzoic acid concentration of around 290 ppm.
Mitsubishi has also introduced a more intensive oxidation process that further reduces the level of 4-formylbenzoic acid. This product is named S-QTA.
To oxidize p-xylene in acetic acid with a cobalt-manganese-bromine catalyst, the method followed is similar to that of the Amoco oxidation.
The slurry is heated to 235 – 290 °C and further oxidized in another reactor. More catalyst can be introduced in conjunction with an increase in temperature.
Heating results in enhanced terephthalic acid solubility, leading to the release of 4-formylbenzoic acid and colored impurities as crystals dissolve.
Although terephthalic acid is not entirely soluble at higher temperatures, crystals can undergo digestion. Digestion is a dynamic equilibrium process in which crystals continue to dissolve and reform, thereby increasing the release of 4-formylbenzoic acid into the solution where oxidation can be completed.
While the requirement for a separate purification process has been eliminated, an additional reactor is necessary for the oxidation process.
Moreover, at higher temperatures, acetic acid tends to be oxidized to a greater extent into carbon oxides and water. The Mitsubishi process involves solid-liquid separation and drying to obtain the powdered product.
The acetic acid must be dehydrated and recycled for use in the process.
2. Uses of Terephthalic acid
Saturated polyesters are primarily produced using terephthalic acid and dimethyl terephthalate. Poly(ethylene terephthalate), an alternating copolymer of terephthalic acid and 1,2-ethanediol, is the predominant type, comprising over 90% of demand with a global consumption of more than 12 million tonnes.
The primary use for polyesters is in textile and industrial fibers, which account for 75% of the market. Polyester is currently the largest volume synthetic fiber is used for.
The fastest growing segment of the polyester market is in food and beverage containers, which accounts for 13% of demand. Film for audio, video, and photography accounts for 7% of the market.
Poly(butylene terephthalate) is a high-performance molding resin made by reacting terephthalic acid with 1,4-butanediol. It finds use in special industrial coatings, solvent-free coatings, electrical insulating varnishes, aramid fibers, and adhesives.
A small quantity of bis(2-ethylhexyl) terephthalate is produced as a plasticizer, while some dimethyl terephthalate is ring-hydrogenated to produce the cyclohexane analogue, 1,4-cyclohexanedicarboxylic acid, for specialty polyesters and coatings.
Reference
- Terephthalic Acid, Dimethyl Terephthalate, and Isophthalic Acid; Ullmann’s Encyclopedia of Industrial Chemistry. – https://onlinelibrary.wiley.com/doi/10.1002/14356007.a26_193.pub2