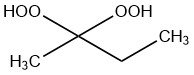
Methyl ethyl ketone peroxide (MEKP) is a liquid chemical compound from the family of ketone peroxides that it is used to initiate the polymerization of unsaturated polyester and vinylester resins at different curing temperatures.
It is the condensation product from the reaction of hydrogen peroxide and 2-butanone and is available as open-chain and cyclic structure.
Table of Contents
1. Physical Properties Methyl ethyl ketone peroxide (MEKP)
Pure methyl ethyl ketone peroxide is a liquid product with a dissociation energy of ca. 100 kJ/mol. It is a water-soluble peroxide.
Commercial formulaion is ≈ 30% solution in 1-isopropyl-2,2-dimethyltrimethylene-diisobutyrate.
Density = 1.01
Refractive index (20 °C) = 1.437
Active oxygen content = 9.3%
2. Chemical Reactions of Methyl ethyl ketone peroxide (MEKP)
Thermolysis of methyl ethyl ketone peroxide gives a complex mixture of products, among them ketone, water, carbon dioxide, acids, alcohol, and alkane.
The decomposition of methyl ethyl ketone peroxide to carboxylic acid is accelerated by acid catalysis. Moreover, this peroxide are sensitive towards metals. Decomposition is induced by transition-metal promoters such as cobalt ions.
In the presence of iron or copper salts, cyclic methyl ethyl ketone peroxide undergo ring-opening reaction to carboxylic acids.
Reaction of hydrogen peroxide with methyl ethyl ketone results in the formation of α-hydroxyalkyl hydroperoxides, which easily react to further condensation products. Thus, ketone peroxides are always obtained as a mixture of different peroxidic species.
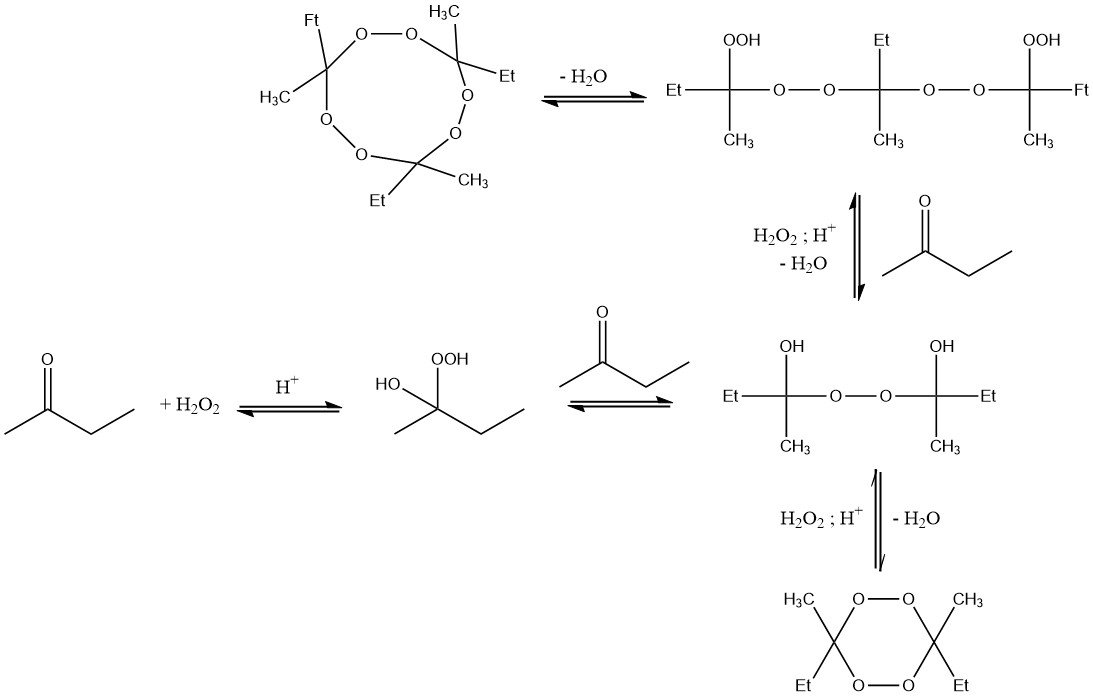
The degree of condensation depends on the reaction conditions, in particular, on the concentration of hydrogen peroxide and 2-butanone, reaction temperature, time, and amount of acid.
The most stable and prevalent compounds are monomeric and dimeric species. Highly condensed derivatives typically constitute a small fraction.
Moreover, trimeric cyclic condensation products can be formed during the reaction. These compounds are temperature-sensitive and potentially explosive when in a solid state.
To ensure stability, commercial formulations of methyl ethyl ketone peroxide may include amine bases for pH adjustment, effectively preventing condensation into potentially hazardous substances.
3. Production of methyl ethyl ketone peroxide (MEKP)
Methyl ethyl ketone peroxide can be prepared either by reaction of hydrogen peroxide with methyl ethyl ketone or by autoxidation.

According to data from 2016, the utilization of ketone peroxides in the plastics sector reached approximately 60,000 metric tons worldwide. This implies that ketone peroxides accounted for 25% of the total peroxide consumption within the plastics industry on a global scale.
It is noteworthy that these particular peroxides find almost exclusive application in the curing process of unsaturated polyester (UP) materials.
Due to it potentially detonable characteristics, MEKP is only available as highly phlegmatized solutions with about 30% peroxide content.
The industrial process entails the addition of 70% hydrogen peroxide to a solution containing dibutyl phthalate, methyl ethyl ketone, and 65% HNO3 at a temperature of 30°C for a duration of 1 hour. The reaction solution is further stirred for an additional 30 minutes at the same temperature.
Following the phase separation step, the resulting raw material is combined with diacetone alcohol, collidine, and 70% hydrogen peroxide.
Traditional synthetic process for producing the trimeric cyclic ketone peroxide of butanone involve the pyrolysis of tricycloalkylidene peroxides. In this method, 2-butanone, hydrogen peroxide, and acid react to form 1-hydroxyperoxy-1´-hydroxy-dicycloalkylidene peroxide, which then undergoes condensation in the presence of a strong acid, yielding a cyclic compound with an approximate yield of 60%.
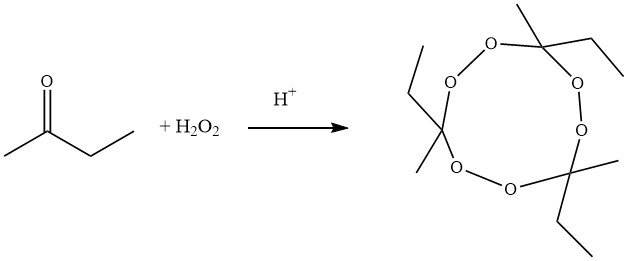
Modern methods, on the other hand, employ the conversion of 2-butanone with hydrogen peroxide in the presence of nitric acid, isoalkanes, and acetic acid as a solubilizing agent. After synthesis, any remaining hydrogen peroxide and hydroperoxides are reduced using sodium sulfite. The trimeric ketone peroxide is obtained with a yield of 90%, and the ratio of trimer to dimer is approximately 94:6.
4. Uses of methyl ethyl ketone peroxide (MEKP)
In the year 2016, an estimated quantity of approximately 250-260 million metric tons of plastics was produced, out of which around 75% of the volume came in contact organic peroxides during the manufacturing process. The applications of methyl ethyl ketone peroxide can be categorized into three segments: polymer manufacture, polymer modification, and nonpolymer applications.
Polymer manufacture involves the utilization of organic peroxides in various industrial polymerization processes such as bulk, suspension, and solution. Key polymers in this category include PVC, LDPE, PS, PP, and PMMA. The total consumption of peroxides for polymer manufacture was estimated to be around 100,000 metric tons.
4.1. Polymer Manufacture
PVC, which is widely used in construction, is a significant thermoplastic polymer. Different polymerization techniques are employed for PVC production, including suspension (S-PVC), microsuspension (MS-PVC), mass (M-PVC), and emulsion (E-PVC). Methyl ethyl ketone peroxide serves as initiator in all these processes except for E-PVC, with an input factor ranging from approximately 0.05% to 0.1%.
LDPE, another important thermoplastic, requires organic peroxide for the radical polymerization of ethylene gas. The process occurs continuously at pressures up to 3000 bar, resulting in conversion rates between 10% and 30%.
Polypropylene, the second largest thermoplastic globally, undergoes degradation of the polymer chain during the final extrusion/granulation process when MEKP is added. This process, known as controlled-rheology PP (cr-PP), leads to higher melt flow indices (MFI) due to a reduction in the molecular mass.
Polystyrene (PS) exhibits versatility and can easily be copolymerized with other monomers. Organic peroxides are commonly used as initiators in most grades of PS, while thermal or oxygen-initiated processes are less frequent.
Poly(meth)acrylates (PMMA) and other (meth)acrylic acid esters find applications in industries such as opto-electronics, automotive, and construction. Ketone peroxides are utilized in bulk and solution polymerization processes, typically ranging from 0.03% to 0.3% of the total composition.
4.2. Polymer Processing
Polymer processing accounts for over 50% of global organic peroxide consumption and involves activities such as curing unsaturated polyester resins (UP) and cross-linking polymers (XL).
4.2.1. UP Curing
Unsaturated polyesters utilize unsaturated dicarboxylic acids, such as fumaric and maleic acid, during the polycondensation step. Methyl ethyl ketone peroxide generates radicals that copolymerize these unsaturated polyesters with reactive monomers like styrene or methyl methacrylate.
Cold curing, where accelerators (redox systems) are added to the resin, enables peroxide decomposition at ambient temperatures. Two common combinations of organic peroxide/accelerator are MEKP/Co2+ salts and dibenzoyl peroxide/aromatic amines (dimethylaniline), with input factors ranging from 2% to 4%.
4.2.2. Cross-Linking of Polymers (XL)
Cross-linking of polymers is the second most significant application after UP curing and accounts for approximately 40% of organic peroxides used in polymer processing. This process finds applications in the manufacturing of elastomers (rubbers) and cross-linking of polyethylene (PE). Organic peroxides, with their highly energetic radicals, are suitable for both saturated polymers and unsaturated elastomers.
4.3. Nonpolymer Applications
In addition to polymer-related uses, approximately 5-6% of methyl ethyl ketone peroxide is employed in various nonpolymer applications, including cosmetics, chemical synthesis (production of catechol), epoxidation reactions, flavorings, and fragrances.
5. Safety Hazards for methyl ethyl ketone peroxide
Methyl ethyl ketone peroxide (MEKP) possesses the potential for spontaneous and explosive decomposition when exposed to thermal or mechanical stress. Factors such as shock, impact, friction, and the presence of impurities like heavy metals or accelerators can catalyze this decomposition process. Consequently, MEKP falls under the regulatory framework for explosive substances.
It is important to note that MEKP is sensitive to temperature and can undergo exothermic decomposition. In the absence of effective cooling mechanisms, the temperature can rise, thereby accelerating the decomposition reaction.
At elevated temperatures, the decomposition of MEKP can occur spontaneously and give rise to fire hazards. Moreover, if the decomposition process takes place within a confined space, the resulting gas can lead to an increase in pressure, potentially resulting in explosions within reactors, vessels, or other containers.
Additionally, the volatile decomposition products of MEKP can contribute to the formation of vapor-phase explosions. To ensure safe storage, it is essential to limit the maximum storage temperature to below 30 °C.
References
- Peroxy Compounds, Organic, Ullmann’s Encyclopedia of Industrial Chemistry. – https://onlinelibrary.wiley.com/doi/10.1002/14356007.a19_199.pub2
- Production of salt-free and low-water-content methyl ethyl ketone peroxide. – https://patents.google.com/patent/EP0788477B1/en