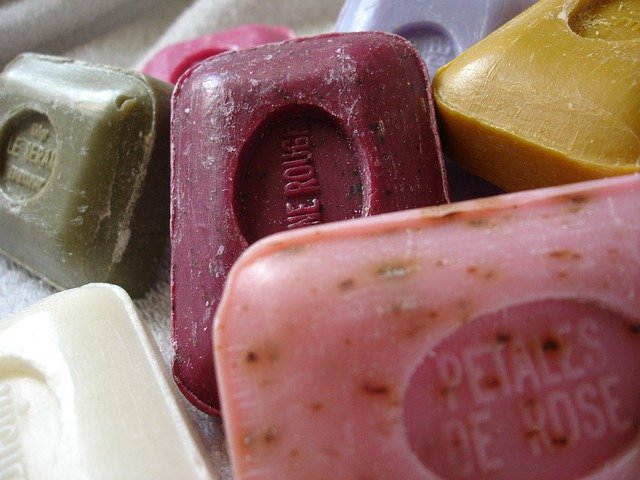
Originally the term metallic soaps was only used for metal salts of fatty acids of naturally occurring animal fats (mainly tallow and lard) and vegetable fats.
Today, metallic soaps are understood to refer to the sparingly soluble or insoluble salts of saturated and unsaturated, straight-chain and branched, aliphatic carboxylic acids with 8–22 carbon atoms.
Because of the great number of possible combinations of metal and acid groups, only general production processes can be described here.
Three types of reaction are possible:
- Double decomposition (precipitation)
- Direct reaction with metal oxides, metal hydroxides, or metal salts of volatile acids
- Direct reaction with metals
Table of Contents
1. Sodium Soaps
1.1. Production
The sodium soaps of stearic and oleic acid have the most industrial importance. They are produced by direct reaction.
A solution of sodium hydroxide is added to the fatty acid, and after completion of the reaction, the product is dried and grounded.
1.2. Uses
Sodium stearate is used in various fields, but mainly in the pharmaceutical and cosmetics industries as emulsifying and gelling agent. Sodium oleate is largely used in the building industry as an initial dispersing agent that becomes a waterproofing agent after application.
2. Potassium Soaps
2.1. Production
The potassium soaps are produced by direct reaction. A solution of potassium hydroxide is added into the fatty acid, and after the reaction is completed the product is dried and ground.
2.2. Uses
Potassium soaps, mainly stearate and oleate, are employed for their swelling properties. They are used to thicken natural and synthetic oils and to raise the melting point and flexibility of waxes and paraffins.
3. Lithium Soaps
3.1. Production
Lithium soaps of stearic and 12-hydroxystearic acid have the greatest industrial importance. They are produced by direct reaction in aqueous medium. A very dilute solution of lithium hydroxide hydrate, LiOH·H2O (concentration ca. 1:40, i.e., 2.5 wt%), is slowly added with intense stirring to the fatty acid dispersed in water in the ratio 1:20 at 90 °C.
Lithium soaps are difficult to filter; flocculation is improved by using an excess of lithium hydroxide or by adding neutral salts. The resulting lithium soap dispersion is, however, often not filtered but spray-dried, even though this involves evaporation of a large quantity of water.
Under modified reaction conditions, lithium hydroxide hydrate can be replaced by lithium carbonate and ammonia.
3.2. Uses
Lithium soaps have particularly good swelling properties. Lithium stearate has the following uses:
- To thicken natural and synthetic oils
- To raise the melting point and flexibility of microcrystalline waxes and paraffins
- As additive for coating waxes to increase water repellence
- As lubricant in the production of injection-molded articles from light metal
Multipurpose lubricating greases have particularly good penetration properties, high oxidation stability, and dropping points up to ca. 200 °C. Lithium 12-hydroxystearate is used primarily for the production of lubricating greases based on synthetic oils (e.g., from silicon and ester oils).
These lubricants cannot be produced by the usual saponification in mineral oil because the synthetic oils are attacked under the saponification conditions employed.
4. Magnesium Soaps
4.1. Production
Magnesium soaps are produced as neutral salts by the double decomposition process, using water-soluble magnesium salts (primarily magnesium chloride) and alkali salts of organic acids in an aqueous medium, or by direct reaction with magnesium oxide or magnesium hydroxide. Particularly important are powdered magnesium soaps based on stearic acid.
The degree of purity required, especially with regard to heavy-metal impurities, determines the choice of raw materials in pharmaceutical products. Pharmaceutical quality must fulfill the requirements of the European, Japanese, and U.S. pharmacopoeias.
4.2. Uses
Magnesium soaps have the following uses:
- In the plastics industry as lubricants and mold-release agents for thermosetting plastics and thermoplastics
- In the pharmaceutical industry as processing aids in the production of sugar-coated pills and as lubricants for tablet pressing
- Inthecosmeticsindustryaspowdercomponents and for consistency in water-free ointments
- In the wax industry to increase the retention of creams based on semisolid wax products and in the production of lubricating waxes
- In the building industry as a waterproofing agent
5. Calcium Soaps
5.1. Production
Calcium soaps are generally neutral salts. They are obtained by double decomposition or direct reaction.
The raw materials consist of saturated straight-chain aliphatic acids (C8–C22), montan wax acids, unsaturated straight-chain carboxylic acids (e.g., oleic and linoleic acids), branched-chain aliphatic carboxylic acids (e.g., ethylhexanoic acids), naphthenic acids, and resin acids.
Calcium chloride, calcium hydroxide, and lime are used as the metal compounds.
Very finely divided calcium soaps of aliphatic straight-chain carboxylic acids are produced by double decomposition in aqueous medium. Stearates, myristates, and laurates are commercial products, but the most important calcium soaps are stearates.
Direct reaction is the most common production method for solid calcium soaps.
In both cases the products are free of water-soluble salts; their purity depends on the quality of calcium hydroxide or lime used.
Calcium soaps are also produced as neutral soaps by the double decomposition process from water-soluble calcium salts and sodium soaps in an aqueous medium. This process can be used to obtain a very high specific surface area, but is mainly used to produce highly crystalline calcium soaps.
Aqueous calcium stearate pastes with a solid content of 40–50% are also produced by the direct process and are used as additives for paper coating (slips).
Calcium soaps which are not in powder form and are therefore used mostly as solutions in organic media (e.g., 2-ethylhexanoates and naphthenates) are produced by direct reaction in an appropriate medium.
5.2. Uses
Calcium stearate is the most important calcium soap and is widely used in polyolefins (PE, PP) and in PVC as lubricant (internal or external), release agent, and acid scavenger.
Calcium soaps are used as physiologically inert lubricants and secondary stabilizers in the plastics industry to improve the flow properties and prevent the caking of hygroscopic substances; as lubricants and mold-release agents along with magnesium soaps in pharmaceutical tablet pressing; as waterproofing additives in agents used for building protection and for surface treatment of fillers; and in the paper industry in recording paper, diagram paper, and coating slips.
6. Barium Soaps
6.1. Production
The most important organic acids in barium soaps are 12-hydroxystearic, lauric, 2-ethylhexanoic, and naphthenic acids. The metal compounds used are barium chloride and barium hydroxide (mono- or octahydrate).
6.2. Uses
Barium soaps are used in the paint industry for wetting pigments and as dispersion agents, in metal forming as a component of wire-drawing and other auxiliaries, and in the plastics industry as lubricants and costabilizers.
7. Aluminum Soaps
7.1. Production
Commercial aluminum soaps are generally produced by treating alkali soaps with water-soluble aluminum salts. During precipitation in aqueous systems, agglomerates of aluminum hydroxide and carboxylic acids are produced which subsequently react with each other to form salts during the following drying process.
Because aluminum is trivalent, three types of soap are possible:
- Aluminum monosoaps Al(OH)2(OOC–R)
- Aluminum disoaps Al(OH)(OOCR)2
- Aluminum trisoaps Al(OOCR)3
All types of organic acids are used for aluminum soaps, particularly stearic, oleic, naphthenic, and 2-ethylhexanoic acids. Aluminum sulfate, potassium aluminum sulfate, and aluminum chloride are the preferred water-soluble aluminum salts. In industrial production of the three types of aluminum soap, the organic acids are saponified with 1, 2, or 3 mol of alkali, respectively.
As the three types differ greatly in their thickening properties, commercial products are available with intermediate metal contents.
Metal, ash, and free fatty acid contents are given to characterize the soaps. To achieve special thickening properties, in particular for the production of mineral oil based lubricating greases, fatty acids are combined
with aromatic carboxylic acids (e.g., benzoic acid or phthalic acid) or with dimeric fatty acids.
Lubricating grease with high fastness to fulling resistance and a high dropping point is obtained in this way.
Aluminum soaps in powder form are obtained by double decomposition in aqueous medium.
Catalyzed reactions between fatty acids and freshly precipitated aluminum oxide hydrate are known but not used industrially. Aluminum oxide hydrate ages too quickly and is not suitable for melting or direct reaction processes in non-aqueous media because of its low reactivity.
An exception is the in situ production of lubricating greases in which aluminum alkoxides and freshly precipitated aluminum hydroxide hydrate are used.
7.2. Uses
The gel-forming property of aluminum soaps is exploited in the mineral oil, cosmetics, and pharmaceutical industries. They are also employed in the paint industry as antisettling and matting agents and for wetting pigments.
Aluminum soaps in powder form are used as lubricants in thermosetting plastics and thermoplastics, as waterproofing agents in building protection, and as flow promoters for caking powders.
8. Lead Soaps
8.1. Production
Neutral lead soaps are produced by double decomposition, by direct reaction in the melt, or by direct reaction in aqueous media in the presence of catalysts, such as triethanolamine and sparingly soluble alcohols.
Basic Lead Soaps are produced by direct reaction in the presence of catalysts in aqueous media. The addition salts contain a maximum of two molecules of lead(II) oxide to one molecule of neutral lead soap:
3 PbO + 2 HOOCR → 2 PbO·Pb(OOCR)2 + H2O
Direct reaction in the melt does not go beyond the addition of one molecule of lead(II) oxide because of an increase in the melting point. In the presence of a fusible organic medium (e.g., C16–C18 fatty alcohols or a combination of fatty alcohols and paraffin or long-chain fatty acid esters), however, a further molecule of lead(II) oxide can be added to give dispersions of dibasic lead soaps.
The basicity of basic lead soaps in the direct reaction depends on their solvent solubility. In general, only one molecule of lead (II) oxide can be added.
Technical-grade stearic, oleic, 2-ethylhexanoic, and naphthenic acids are used for the production of the most important lead soaps. The principal metal source is lead oxide. Lead acetate is used as the water-soluble lead salt in the double decomposition process. Direct reaction in aqueous medium is performed with reactive lead(II) oxide (litharge, commercial specification ‘‘canary yellow’’).
The red lead oxide content should be very low because this modification cannot form basic addition salts. The red modification is, however, suitable for the production of neutral salts in the melt or in an aqueous medium. In the melt process, the lead metal content of the lead oxide should be very low to avoid blockage of valves by agglomeration.
Regulations for personal and environmental protection must be observed, particularly with lead soaps in powder form. Even the absorption of small quantities of lead can lead to chronic illness.
8.2. Uses
Neutral and basic lead stearates are used as heat stabilizers and lubricants in PVC processing, as lubricants in the pencil industry, and as additives for specialty papers.
Lead 2-ethylhexanoate, naphthenates, and resinates are used in the paint industry for wetting pigments and as dryers and in the mineral oil industry as components of high-pressure lubricants. However, for safety reason these are nowadays being replaced by mixtures of calcium-zinc stearate plus other stabilizers.
9. Copper Soaps
9.1. Production
Copper forms neutral soaps which are produced either by double decomposition or by the direct process in the melt or in organic media. Production from metallic copper is also known: copper powder is dispersed in solvent naphtha, and copper soaps that are soluble in solvent naphtha are formed by passage of air in the presence of an organic acid.
Commercial copper soaps are produced from stearic, naphthenic, oleic, and 2-ethylhexanoic acids. Water-soluble copper salts, mainly copper sulfate, are used as copper source for the double decomposition; copper hydroxide or basic copper carbonate is used for direct reaction.
Production of copper soaps in powder form by double decomposition requires a separate plant, because cleaning the drying and filtration units is almost impossible.
9.2. Uses
Copper soaps are used mainly as fungicides in wood and ship paints, textiles (e.g., tents, awnings, sandbags, camouflage netting, ropes), paper, and cardboard. Compared with inorganic copper compounds, they have the advantage of being difficult to wash out. Naphthenates, oleates, and 2-ethylhexanoate are used as solutions in organic media.
10. Zinc Soaps
10.1. Production
The most important zinc soaps are zinc stearates. Neutral Zinc Soaps are produced by double decomposition, direct reaction in the melt, direct reaction in aqueous or organic media, and reaction of zinc oxide with fatty acids below the melting point of the soaps.
Basic Zinc Soaps produced by double decomposition are obtained in powder form; the basic moiety can be in the form of a basic soap, zinc oxide, or zinc carbonate. In organic media, soluble zinc soaps (particularly naphthenates, 2-ethylhexanoate, and oleates) can be rendered basic during the direct reaction by addition of excess zinc hydroxide.
Soaps with 1.7 equivalents of zinc hydroxide to 1 equivalent of acid can be obtained.
Commercial Zinc Soaps are produced from stearic, lauric, oleic, 2-ethylhexanoic, and naphthenic acids. Those derived from stearic acid are produced on the largest scale.
Water-soluble salts, preferably zinc sulfate and chloride, are used as zinc source for double decomposition; zinc oxide, hydroxide, and carbonate are employed for direct reaction.
When several types of product are prepared in a single plant, attention must be paid to the production order because zinc stearate acts as a gel breaker with gels from aluminum soaps. Normally calcium, magnesium, zinc, and aluminum soaps are produced in a single plant.
10.2. Uses
Zinc soaps are used for the following purposes:
- In the plastics industry as lubricants, release agents, and components of PVC stabilizers
- In the rubber industry, as release agents for unvulcanized products (wettable zinc stearate soaps and zinc stearate dispersions in water are also used)
- In paints, as matting agents and abrasives
- In building protection, as waterproofing agents
- For textiles, also as waterproofing agents
- In the cosmetics and pharmaceutical industries, as additives to body and face powders
- As components of wire-drawing greases (special zinc arachidate is used in tube drawing because of its low ash content)
- In paints, as components of dryers and as anticaking agents for powdered products
11. Cadmium Soaps
11.1. Production
Neutral and basic cadmium soaps are produced by double decomposition, direct reaction in the melt, or direct reaction in organic media. Stearic, lauric, 12-hydroxystearic, oleic, and 2-ethylhexanoic acids are commonly used.
Cadmium sulfate, chloride, and nitrate are used in double decomposition, cadmium oxide and hydroxide in the direct reaction. Cadmium soaps are highly toxic. Cadmium accumulates in organs such as the liver and adrenal gland and is released very slowly. Absorption of very small quantities of cadmium over a long period leads to chronic illness.
11.2. Uses
The use of cadmium soaps as components of PVC stabilizers is decreasing because of their toxic properties. Solid PVC stabilizers contain cadmium soaps of saturated fatty acids, whereas liquid stabilizers contain soaps of unsaturated or branched, short-chain fatty acids.
The soaps act as heat and light stabilizers, and soaps of saturated fatty acids are used as lubricants in the processing of PVC. Unlike other metallic soaps used in the PVC sector, cadmium soaps do not affect transparency and are suitable for hard, transparent PVC products.
However, for safety reason their use is nowadays being replaced by mixtures of calcium-zinc stearate plus other stabilizers.
12. Manganese Soaps
12.1. Production
NeutralManganese(II) Soaps are produced by double decomposition from alkali soaps and water-soluble manganese salts in an aqueous medium or in the presence of organic solvents, and by direct reaction in the melt or in organic media with manganese oxides, hydroxides, or salts of volatile acids.
The oxides and hydroxides are very unreactive and must be freshly prepared; conversion is generally incomplete. In the reaction with metallic manganese in powder form or as divided gauze, lower carboxylic acids (e.g., acetic acid) are added to the solvent as catalysts.
Basic Manganese(II) Soaps are produced by double decomposition in an aqueous medium; oversaponified alkali soaps (i.e., more than 1 mol of alkali is used per mole of acid) react with water-soluble manganese salts.
The excess alkali forms manganese hydroxide or manganese oxide hydrate, which adds to the neutral manganese soap. It is, however, unclear whether a true addition salt or a simple mixture is formed.
The basic manganese soaps are insoluble or sparingly soluble in organic solvents. Stearic, oleic, naphthenic, and 2-ethylhexanoic acids are commonly used. Sources of manganese for the double decomposition are water-soluble manganese salts such as manganese chloride and sulfate; for the direct reaction, manganese oxide, hydroxide, and acetate are used.
Manganese soaps are hazardous to health. A particular danger arises from dust formation by powered products. Because of their brown color, separate production plants are necessary for powdered products.
12.2. Uses
Manganese soaps are used mainly as dryers in paints, printing inks, and varnishes based on drying oils or alkyd resins. Basic powdered products are also added to printing inks.
Manganese soaps can be used as catalysts (e.g., in paraffin oxidation or the reduction of fatty acids to alcohols).
13. Iron Soaps
13.1. Production
Neutral iron(III) soaps and mixed iron(II)–iron (III) soaps are produced industrially. Formation of basic soaps by addition of iron oxide or hydroxide is known but is not exploited commercially.
Iron soaps are obtained by double decomposition from alkali soaps and water-soluble iron salts in an aqueous medium with or without organic solvents. Direct reaction in the melt with iron oxides does not go to completion and is very slow thus a catalyst is necessary; the unreacted free fatty acid is extracted with alcohol.
Raw materials used arestearic, oleic, naphthenic, and 2-ethylhexanoic acids. In double decomposition, iron(II) or iron(III) chloride is generally used as the iron source; in the direct reaction, iron oxide, hydroxide, or carbonate are employed.
Because of the intense color of iron soaps, separate precipitation units are necessary. Although iron soaps do not pose a danger to health, local regulations regarding personal and environmental protection for dust-producing products must be observed during handling.
13.2. Uses
Iron soaps are components of dryer mixtures. Because of their intense color, they are used only with dark colors. The function of the iron as a dryer is based on polymerization at elevated temperature rather than catalyzing the oxidation.
Today the main application is in agriculture as a catalyst of the photodegradation of polyolefin films. This application dramatically increases the biodegradation of the polymers, avoiding its accumulation in the soil and thus these salts can be considered environmentally friendly.
Further uses are as hydrogenation catalysts, as dry-film lubricants in the form of monomolecular adhesive layers, in the production of fast-copy paper, in waterproofing, and in pharmaceuticals as oil-soluble iron compounds for the treatment of different diseases.
14. Cobalt Soaps
14.1. Production
Neutral and weakly basic cobalt(II) soaps are known. They are produced by double decompo- sition using alkali soaps with water-soluble cobalt salts in an aqueous medium with or without organic solvents or by direct reaction via the meltprocess or in solvents.Reaction of metallic cobalt in powder or gauze form in organic media is also possible; air acts as an oxidizing agent.
Stearic, oleic, naphthenic, and 2-ethylhexanoic acids are used. For double decomposition, cobalt(II) sulfate is used as the water-soluble salt; for the direct reaction, cobalt acetate, cobalt(II) hydroxide, and cobalt(II) oxide are employed.
Cobalt soaps have an intense blue-violet color. Soaps in powdered form must be produced in separate plants. Dust from cobalt soaps is hazardous to health. Local regulations concerning personal and environmental protection and the compulsory labeling of packaging must be observed.
14.2. Uses
Cobalt soaps are very effective dryers for printing and writing inks because they catalyze oxidation. Cobalt stearate is used as an adhesive for rubber–metal bonding. Due to health concerns their substitution with other materials is being evaluated.
15. Nickel Soaps
15.1. Production
Divalent nickel forms neutral to weakly basic soaps. They are produced by double decomposition from alkali soaps and water-soluble nickel salts in an aqueous medium in the presence of organic solvents or by direct reaction in the melt or in solvents with nickel oxide, hydroxide, or salts of volatile acids.
In the melt process, decomposition occurs above 200 °C with formation of a black powder. The usual acids are stearic, oleic, 2-ethylhexanoic, and naphthenic acids. Nickel sulfate and chloride are used as water-soluble salts for double decomposition, and nickel(II) hydroxide, oxide, acetate, or carbonate for the melt process.
Nickel soaps in powder form must be produced in separate plants because of their intense green color. Dust from nickel soaps is hazardous to health. Local regulations concerning personal and environmental protection and compulsory labeling must be observed. During nickel oxide and carbonate processing, protective measures must be taken because of their carcinogenic properties.
15.2. Uses
Nickel soaps are used as oxidation catalysts in dryers; as oil-soluble hydrogenation catalysts, which liberate finely divided nickel on heating or decomposition; as detergents in petroleum ether; and as additives in lubricating oils for preventing cyclization and resinification. Due to health concerns their substitution with other materials is being evaluated.
Reference
- Metallic Soaps; Ullmann’s Encyclopedia of Industrial Chemistry. – https://onlinelibrary.wiley.com/doi/10.1002/14356007.a16_361.pub2