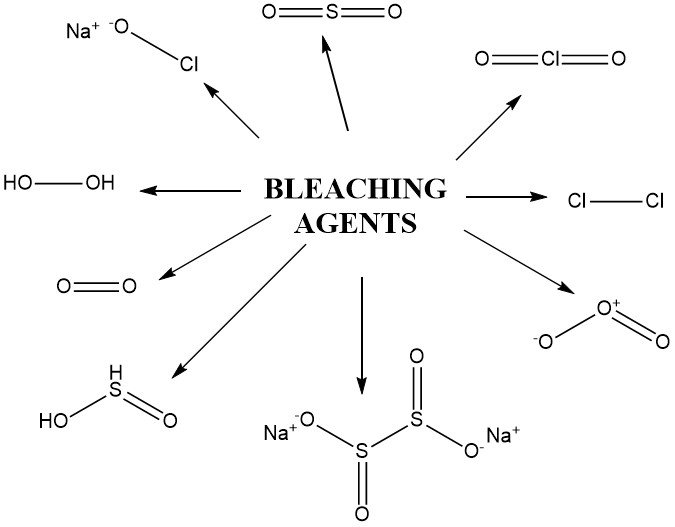
Introduzione
Il processo per ottenere un effetto sbiancante comporta la rimozione dei cromofori. Ciò può essere ottenuto adsorbendo i composti colorati su superfici attive come carbone attivo o argille sbiancanti.
Questo metodo è comunemente impiegato su scala industriale per sbiancare e purificare liquidi come l’olio vegetale. Un altro approccio comunemente utilizzato in contesti industriali è la distruzione chimica dei cromofori nei composti organici o inorganici, che è spesso combinata con processi di purificazione o pulizia.
Ciò è particolarmente importante per i prodotti naturali, che spesso contengono impurità. Ad esempio, il cotone è contaminato da residui di capsule di semi, cera, costituenti grassi e composti inorganici. Sbiancando il cotone, la sua luminosità viene aumentata mentre le impurità vengono contemporaneamente rimosse. Lo sbiancamento può anche servire come continuazione o integrazione di precedenti fasi di lavorazione.
Per illustrare, nel contesto della polpa chimica, lo sbiancamento rimuove la lignina dalle fibre di legno, con conseguente aumento della luminosità e ulteriore purificazione della cellulosa. Ottenere uno sbiancamento quasi incolore senza causare danni è impegnativo e richiede competenza. L’obiettivo dello sbiancamento dall’inizio potrebbe anche essere quello di creare una tonalità più uniforme, come lo sbiancamento dell’impiallacciatura di legno.
In termini di volume e valore del prodotto, lo sbiancamento di materiali fibrosi per la produzione di carta e tessuti ha un’importanza significativa.
Sommario
1. Meccanismo di sbiancamento
Lo sbiancamento può essere categorizzato in sbiancamento ossidativo e riduttivo. Lo sbiancamento ossidativo distrugge irreversibilmente i cromofori, mentre lo sbiancamento riduttivo può essere reversibile, ad esempio tramite riossidazione da parte dell’ossigeno atmosferico.
Nel caso di prodotti naturali, la composizione chimica completa dei composti colorati spesso non è nota. In genere, questi composti contengono doppi legami carbonio-carbonio coniugati, come catene polimetiniche, sistemi aromatici o sistemi chinoidi. Lo sbiancamento ossidativo interrompe i doppi legami, elimina la coniugazione e genera composti chimici con peso molecolare inferiore.
Uno sbiancamento efficace spesso comporta un processo in più fasi. La ripetizione dell’ossidazione acida e dell’estrazione alcalina consente di mantenere condizioni moderate e basse concentrazioni chimiche.
L’effetto sbiancante è misurato dall’aumento della luminosità. I fotometri a remissione sono utilizzati per determinare la luminosità rispetto a uno standard a più lunghezze d’onda, con BaSO4 come standard più comunemente utilizzato. Tuttavia, sono disponibili metodi alternativi per valutare la luminosità. La stabilità della luminosità funge anche da indicatore della qualità e dell’efficienza del processo di sbiancamento.
Un’ossidazione eccessiva può portare alla formazione di nuovi cromofori o a un potenziale ingiallimento in futuro. L’ingiallimento si verifica se i gruppi auxocromici in un cromoforo possono essere riossidati. La luce e il calore possono causare cambiamenti di colore nei materiali sbiancati.
La radiazione UV rompe facilmente i legami carbonio-carbonio, producendo radicali. La ricombinazione di questi radicali con l’ossigeno o altre parti della molecola può generare nuovi cromofori.
Durante i processi di sbiancamento, è importante assicurarsi che il grado di polimerizzazione dei polimeri trattati non venga influenzato negativamente. Una diminuzione del peso molecolare può influire sulla resistenza delle fibre e ridurre il valore economico.
Pertanto, lo sbiancamento dovrebbe mirare ai cromofori preservandone la struttura molecolare. La complessità delle materie prime ha portato allo sviluppo di vari metodi di sbiancamento.
Ad esempio, lo sbiancamento del cotone è diverso dallo sbiancamento della lana. Mentre è possibile applicare condizioni fortemente alcaline per sbiancare la cellulosa polimerica dei carboidrati (cotone), la fibra di lana di cheratina (proteina) è altamente sensibile agli alcali. Non è possibile utilizzare lo sbiancamento alcalino in quanto ciò comporterebbe la distruzione del polimero tramite l’estrazione di amminoacidi.
2. Agenti sbiancanti
2.1. Pretrattamento
La preparazione per un processo di sbiancamento comporta la rimozione di contaminanti. Un metodo di pretrattamento comune è il lavaggio. La lana tosata, ad esempio, può contenere una quantità significativa di sabbia e materiale grasso (lanolina), fino al 50% in peso.
Allo stesso modo, i composti che consumano o decompongono l’agente sbiancante devono essere eliminati prima del processo di sbiancamento effettivo. Il lavaggio con tensioattivi o composti chelanti è una procedura standard per ottenere questo risultato.
Riduce la richiesta di agenti sbiancanti e riduce al minimo il potenziale di reazioni collaterali negative durante lo sbiancamento. Nel caso dello sbiancamento chimico della polpa, questo è spesso un requisito cruciale.
Il lavaggio acido a un pH inferiore a 3 dissolve gli ioni metallici. La presenza di agenti riducenti come l’anidride solforosa, che abbassano lo stato di ossidazione dei metalli, può aumentare questo effetto. Agenti chelanti come i sali di sodio dell’acido dietilentriamminopentaacetico (DTPA) o dell’acido etilendiamminotetraacetico (EDTA) vengono utilizzati in condizioni leggermente acide (pH 5-6) per accelerare la rimozione dei metalli.
Questo intervallo di pH consente l’eliminazione dei metalli di transizione preservando gli ioni di magnesio e calcio, che fungono da stabilizzatori nel processo di sbiancamento. Per la polpa chimica prodotta tramite polpaggio alcalino, questa fase di rimozione dei metalli è necessaria se si desidera implementare un processo di sbiancamento totalmente privo di cloro (TCF).
Nello sbiancamento convenzionale o privo di cloro elementare (ECF), i metalli vengono rimossi durante le fasi di biossido di cloro acido. Nella polpaggio acido al solfito, vengono solubilizzati durante il processo di polpaggio ed eliminati nel lavaggio del brown stock.
Durante la polpaggio alcalino del legno duro, vengono generati doppi legami polimerici di xilano. Questi composti di emicellulosa consumano sostanze chimiche sbiancanti elettrofile. Un pretrattamento acido a circa 90 °C e pH inferiore a 3 viene condotto per idrolizzare questi composti, producendo acido furancarbossilico. Ciò aiuta a ridurre la domanda di sostanze chimiche sbiancanti.
Enzimi come la xilanasi possono essere utilizzati come pretrattamento. Durante la polpazione alcalina, lo xilanasi si dissolve ma può precipitare di nuovo nelle fasi finali della procedura di cottura, ponendo sfide per lo sbiancamento. L’enzima xilanasi rimuove il precipitato e facilita il processo di sbiancamento. Per questo scopo sono preferiti enzimi estratti da batteri termofili con elevata tolleranza a temperatura e pH.
Nello sbiancamento tessile, possono essere necessari trattamenti con amilasi o perossosolfato per rimuovere l’amido.
2.2. Agenti ossidanti
Nell’antichità, lo sbiancamento ossidativo dei tessuti era praticato dagli Egizi e dai Fenici utilizzando la luce solare combinata con un trattamento alcalino delicato che prevedeva carbonato di potassio lisciviato dalle ceneri di legno.
Nel 1700, emerse un metodo di sbiancamento noto come “sbiancamento olandese”, che prevedeva trattamenti alternati con carbonato di potassio, esposizione alla luce solare su prati erbosi e latte acido. Questa tecnica raggiunse il suo apice nei pressi di Haarlem, nei Paesi Bassi.
I progressi nella conoscenza chimica alla fine del 1700 portarono alla scoperta di un nuovo agente sbiancante, l’ipoclorito. L’ipoclorito di potassio (Eau de Javelle), l’ipoclorito di sodio (Eau de Labarraque) e l’ipoclorito di calcio divennero gli agenti sbiancanti industriali più significativi per quasi 150 anni.
Il cloro fu introdotto nello sbiancamento chimico della cellulosa negli anni ’30, seguito dal biossido di cloro e dal perossido di idrogeno un decennio dopo.
L’uso industriale dell’ossigeno come agente sbiancante per la cellulosa chimica iniziò alla fine degli anni ’60 e l’ozono fu successivamente incorporato nelle sequenze di sbiancamento chimico della cellulosa.
Altri composti ossidanti impiegati per lo sbiancamento includono derivati del perossido di idrogeno come acido peracetico, perborato di sodio, perossodisolfati (persolfati) e perossomonosolfati (acido di Caro). Questi composti sono usati in condizioni specifiche, tra cui il permanganato di potassio.
2.2.1. Ossigeno
L’utilizzo dell’ossigeno come agente sbiancante ha registrato un aumento significativo dall’inizio degli anni ’70. Viene impiegato nello sbiancamento della polpa chimica per sostenere e intensificare la degradazione della lignina, che in genere inizia durante la polpazione alcalina.
La delignificazione con ossigeno richiede condizioni alcaline, solitamente con idrossido di sodio (NaOH), per il processo di ossidazione. Richiede inoltre temperature relativamente elevate (75-100 °C) e una pressione dell’ossigeno di 0,3-0,5 MPa. L’aumento della temperatura, della pressione o della concentrazione di soda caustica aumenta la velocità di ossidazione.
Il processo di delignificazione con ossigeno comporta due reazioni simultanee: delignificazione desiderata e degradazione indesiderata dei carboidrati. Di conseguenza, esistono limiti pratici per l’aumento della temperatura e della quantità di alcali. La riduzione del grado di polimerizzazione è parzialmente ostacolata dai sali di magnesio.
Sebbene l’impatto dell’ossigeno sulla polpa chimica sia limitato, il suo trattamento riduce la domanda di altri prodotti chimici sbiancanti del 40-50%. La delignificazione con ossigeno consente il recupero combinato degli effluenti dalla polpatura e dalle successive fasi di delignificazione, riducendo efficacemente lo scarico totale di materiale organico dall’impianto di sbiancamento.
Nei processi di polpatura a base di magnesio, come la polpatura con solfito di magnesio, la fase di ossigeno può essere condotta utilizzando idrossido o ossido di magnesio come fonte di alcali. In genere, il perossido di idrogeno viene aggiunto simultaneamente (a circa 90 °C) per accelerare la velocità di delignificazione.
2.2.2. Biossido di cloro e clorito di sodio
Il biossido di cloro è un agente sbiancante eccezionalmente selettivo che è stato utilizzato per la prima volta nello sbiancamento della polpa chimica nel 1946.
Il biossido di cloro possiede un elettrone spaiato, il che lo rende un radicale libero con stabilità limitata. Esiste come gas in condizioni standard e può esplodere spontaneamente a pressioni parziali superiori a 40 kPa, scomponendosi in cloro e ossigeno.
Quando esposto al calore o alla luce, anche concentrazioni inferiori di biossido di cloro possono esplodere, sebbene con violenza ridotta. Di conseguenza, il biossido di cloro puro non può essere trasportato o immagazzinato. Invece, viene generato in loco e in genere gestito come una soluzione acquosa diluita.
Il principale metodo industriale per la generazione di biossido di cloro comporta la riduzione del clorato. Storicamente, il processo Mathieson, che impiega biossido di zolfo per la riduzione, ha svolto un ruolo significativo. Acido solforico diluito e solfato di sodio o idrogenosolfato di sodio sono prodotti come sottoprodotti.
Processi alternativi con meno sottoprodotti impiegano acido cloridrico, metanolo o perossido di idrogeno come agente riducente. L’acido cloridrico offre il vantaggio di un basso costo, ma comporta una quantità relativamente elevata di cloro presente come sottoprodotto nel biossido di cloro, portando a una maggiore formazione di prodotti alogenati indesiderati durante lo sbiancamento.
Oggi, i processi con metanolo e perossido di idrogeno sono i metodi più importanti. Questi processi generano gas di biossido di cloro altamente puro, che viene diluito con aria o vapore acqueo per prevenire esplosioni.
Il gas viene quindi assorbito in acqua fredda per raggiungere una concentrazione di 6-12 g/L. Per le reazioni del biossido di cloro con la polpa, viene in genere mantenuto un valore di pH compreso tra 2 e 5. In questo intervallo di pH, il biossido di cloro non influisce sul grado di polimerizzazione della cellulosa.
La temperatura di reazione consigliata per il biossido di cloro è compresa tra 50 e 75 °C. Nello sbiancamento della polpa di legno duro, l’avvio dello sbiancamento ad alte temperature (> 90 °C) è favorevole in quanto consente l’ossidazione simultanea della lignina e l’idrolisi degli acidi esenuronici.
Nello sbiancamento tessile, il clorito di sodio viene impiegato come fonte di biossido di cloro. L’acido cloridrico, l’acido formico o l’acido acetico vengono utilizzati per liberare il biossido di cloro attraverso la seguente reazione:
5 NaClO2 + 4 HCl → 4 ClO2 + 2 H2O + 5 NaCl
2.2.3. Perossido di idrogeno e altri composti perossidi
Il perossido di idrogeno è stato utilizzato come sbiancante industriale sin dai primi anni del 1900, principalmente nello sbiancamento delle fibre tessili.
Il perborato di sodio, NaBO3·4 H2O, derivato dal perossido di sodio e dal borace, è stato utilizzato come sbiancante nei detersivi per bucato come Persil già nel 1907. Ancora oggi, perborati e percarbonati sono ampiamente utilizzati nei detersivi per bucato per il loro effetto sbiancante delicato a temperature elevate, che è più delicato sulle fibre rispetto agli ipocloriti più aggressivi utilizzati come sbiancanti a freddo. Vengono applicati prodotti rivestiti speciali per migliorare la stabilità di conservazione del percarbonato puro.
Soluzioni acquose di perossido di idrogeno sono disponibili in commercio in concentrazioni fino al 90% in peso. Le soluzioni con il 35-70% in peso sono comunemente utilizzate nello sbiancamento.
L’applicazione più significativa del perossido di idrogeno è nello sbiancamento della polpa per la produzione di carta. La pasta meccanica e la pasta chimica vengono sbiancate utilizzando soluzioni di perossido alcalino. Il perossido di idrogeno viene impiegato anche per sbiancare fibre tessili come cotone, lino, lana e sintetici.
I processi commerciali di sbiancamento con perossido di idrogeno generalmente operano in condizioni da leggermente a fortemente alcaline. L’idrossido di sodio viene comunemente utilizzato come fonte alcalina. La reazione iniziale comporta l’addizione nucleofila di anioni idroperossido a gruppi carbonilici. Di conseguenza, l’aggiunta di alcali aumenta la velocità di sbiancamento:
HOOH + OH– ↔ HOO– + H2O
Tuttavia, le condizioni alcaline favoriscono anche reazioni collaterali come la sproporzione del perossido di idrogeno in ossigeno e acqua:
HOO– + H2O2 → H2O + OH– + O2
Il risultato dello sbiancamento dipende dall’attivazione e dalla stabilizzazione. La velocità di reazione aumenta con la temperatura e la concentrazione alcalina.
Tuttavia, ad alte temperature, reazioni collaterali come la decomposizione termica del perossido di idrogeno in radicali diventano più probabili, portando potenzialmente a perdite di resa e solubilizzazione del materiale sbiancato. Pertanto, l’intervallo di temperatura tipico per lo sbiancamento con perossido è compreso tra 60 e 90 °C.
La stabilizzazione della soluzione sbiancante alcalina può essere necessaria per ridurre al minimo la decomposizione del perossido. I radicali idrossilici, generati tramite la decomposizione del perossido, sono agenti ossidanti altamente non selettivi che causano reazioni collaterali indesiderate.
Nello sbiancamento chimico della polpa, la chelazione dei metalli di transizione è necessaria solo nello sbiancamento TCF (totalmente privo di cloro). Nello sbiancamento ECF (elemental chlorine-free), il perossido di idrogeno viene in genere applicato dopo una fase acida, che rimuove i metalli di transizione durante la fase di lavaggio.
Per lo sbiancamento meccanico della polpa, i metalli dannosi vengono rimossi al meglio tramite pretrattamento con un agente chelante. Gli agenti chelanti comunemente utilizzati sono i sali di sodio dell’acido dietilentriamminopentaacetico (DTPA), l’acido etilendiamminotetraacetico (EDTA) o fosfonati simili con capacità chelanti comparabili o superiori.
Vengono impiegati anche stabilizzanti come il silicato di sodio e i sali di magnesio (principalmente solfato di magnesio). Questi stabilizzanti aiutano a precipitare o assorbire i composti dannosi sulla silice colloidale o sull’idrossido di magnesio.
Durante il processo di sbiancamento, il perossido di idrogeno scinde le catene laterali e distrugge irreversibilmente le strutture chinoidi. L’ossidazione e la distruzione dei chinoni sono fondamentali per ottenere una buona stabilità della brillantezza. I prodotti sbiancati con perossido presentano una minore inversione rispetto ad altri ossidanti.
L’acido peracetico viene utilizzato in piccole quantità come fase di attivazione prima del trattamento alcalino con perossido di idrogeno. La sua applicazione consente un maggiore aumento della brillantezza o un minore consumo complessivo di sostanze chimiche sbiancanti.
La reazione con la polpa viene effettuata in condizioni leggermente acide, che coinvolgono prevalentemente la reazione di idrossilazione della lignina residua. L’acido peracetico viene prodotto mescolando acido acetico e perossido di idrogeno.
In presenza di un acido forte (ad esempio, acido solforico), si stabilisce un rapido equilibrio tra acido acetico, acido peracetico, perossido di idrogeno e acqua. Poiché gli altri composti nella miscela non contribuiscono alla reazione di sbiancamento dell’acido peracetico, l’uso di acido peracetico in equilibrio è costoso.
L’acido peracetico distillato è un’alternativa, ottenuta tramite distillazione sotto vuoto dell’acido peracetico in equilibrio, che si traduce in una soluzione di acido peracetico relativamente pura in acqua. L’acido peracetico distillato con un contenuto di circa il 35% in acqua deve essere conservato a una temperatura inferiore a 4 °C per impedire il lento ripristino dell’equilibrio con perossido di idrogeno e acido acetico a temperature più elevate.
Un’altra opzione è la miscelazione in loco, che produce una miscela di acido peracetico/perossido che può essere utilizzata per una reazione iniziale con acido peracetico seguita da una successiva fase di sbiancamento con perossido. Ciò si ottiene aggiungendo alcali sufficienti dopo la fase acida.
L’acido peracetico può anche essere generato in situ da perossido di idrogeno e tetraacetiletilendiammina (TAED) in condizioni debolmente alcaline. Questa procedura è applicata negli agenti di lavaggio che utilizzano percarbonato o perborato come fonte di perossido ed è applicabile anche nello sbiancamento speciale.
Il perossosolfato di potassio (KHSO5) è utilizzato per lo sbiancamento di fibre di poliammide e cellulosa, sebbene sia impiegato principalmente per pulire la lana e ridurne il restringimento.
Il perossodisolfato di sodio (Na2S2O8) e il perossodisolfato di ammonio ((NH4)2S2O8) sono utilizzati nella sbozzimatura del cotone e occasionalmente come additivi nello sbiancamento con perossido di idrogeno.
2.2.4. Ozono
L’ozono viene generato tramite una scarica elettrica silenziosa dall’ossigeno. Nello sbiancamento della polpa, l’ozono viene in genere prodotto utilizzando ossigeno puro. Questo metodo consente un’elevata concentrazione di ozono nel gas (fino al 12% in peso) e facilita il processo di miscelazione.
Per mantenere uno sbiancamento efficace, l’ozono viene utilizzato a un pH inferiore a 4. È importante mantenere la temperatura al di sotto di circa 50 °C per evitare reazioni collaterali con la cellulosa causate dal suo elevato potenziale di ossidazione. Temperature più elevate possono causare una luminosità meno stabile e un facile ingiallimento.
2.2.5. Cloro e ipocloriti
Storicamente, il cloro è stato ampiamente utilizzato per l’ossidazione della lignina (delignificazione) nello sbiancamento chimico della polpa. La clorazione comporta la sostituzione e l’ossidazione degli anelli aromatici nella lignina, con conseguente produzione di acido dicarbossilico e frammenti di lignina clorurati.
Circa il 10% del cloro applicato si trova come composti alogenati nell’effluente, tra cui fenoli clorurati e dibenzodiossine e dibenzofurani polialogenati.
Questi composti vengono analizzati quantitativamente utilizzando un metodo estrattivo con carbone attivo e la misurazione è espressa come composti organici alogenati adsorbibili (AOX).
Alcuni di questi composti sono mutageni, portando a un’eliminazione graduale dell’applicazione di cloro nella maggior parte delle regioni dopo l’identificazione di queste sostanze nell’effluente.
Attualmente, l’ipoclorito è utilizzato principalmente come smacchiatore, noto come “candeggina a freddo” nel lavaggio. Nello sbiancamento chimico della polpa, la sua applicazione è limitata a piccole quantità per la riduzione controllata del grado di polimerizzazione della polpa dissolta.
L’acido ipoclorico (HOCl) ha un potenziale di ossidazione più elevato (+1,50 V) rispetto al cloro (+1,35 V) o all’ipoclorito (OCl–) (+0,94 V). Per prevenire reazioni collaterali, in particolare la depolimerizzazione causata dall’acido ipoclorico aggressivo, lo sbiancamento viene condotto in soluzioni alcaline per ridurre al minimo la concentrazione di acido ipoclorico non dissociato.
Le condizioni alcaline determinano meno reazioni collaterali sfavorevoli poiché l’anione ipoclorito è un nucleofilo debole incapace di attaccare sistemi aromatici ricchi di elettroni. Tuttavia, lo sbiancamento con ipoclorito genera composti alogenati come sottoprodotti, con formazione di AOX significativamente inferiore rispetto al cloro. Il principale sottoprodotto è il cloroformio.
Sono disponibili in commercio soluzioni di ipoclorito di sodio con concentrazioni di cloro attivo di 150-160 g/L. Il termine “cloro attivo” si riferisce alla quantità di cloro liberata dall’acidificazione della soluzione di ipoclorito.
2.3. Agenti riducenti
Il principale agente sbiancante riducente è il ditionito di sodio, utilizzato per lo sbiancamento della lana fin dall’antichità. Tuttavia, la sua importanza è diminuita. I derivati dell’acido solfinico sono impiegati principalmente per rimuovere i coloranti dai tessuti tessili.
2.3.1. Ditionito di sodio
Il ditionito di sodio (Na2S2O4), noto anche come idrosolfito in Nord America (nonostante la descrizione iniziale errata), è attualmente prodotto da formiato di sodio e anidride solforosa. In precedenza, il ditionito di zinco ottenuto da anidride solforosa e polvere di zinco era più diffuso del sale di sodio.
Tuttavia, le preoccupazioni ambientali associate allo zinco hanno portato all’interruzione della produzione in loco di ditionito di zinco utilizzando polvere di zinco o amalgama di sodio. Il ditionito di sodio può essere generato in loco in alcune cartiere utilizzando una soluzione alcalina di boroidruro di sodio, bisolfito di sodio e anidride solforosa.
Il ditionito di sodio è disponibile in polvere cristallina (90% Na2S2O4) o come soluzione refrigerata da 150 g/L stabilizzata con alcali. Le soluzioni devono essere conservate ben al di sotto dei 10 °C per evitare che il ditionito si sproporzioni in tiosolfato e bisolfito.
Il ditionito agisce riducendo i gruppi carbonilici ad alcoli e i chinoni a fenoli, distruggendo così i cromofori. Viene utilizzato per sbiancare polpa meccanica, lana, seta, setole, capelli, paglia, sapone, colla, caolino e vari prodotti alimentari come zucchero, melassa, gelatina e grassi commestibili.
Il ditionito è suscettibile all’ossidazione da parte dell’ossigeno, convertendolo in solfito e solfato. A temperature elevate, la soluzione si decompone in tiosolfato, solfito, idrogeno solforato o zolfo, con prodotti specifici dipendenti dal pH. Il pH scelto per lo sbiancamento con ditionito è un compromesso tra sbiancamento efficace e perdita minima di ditionito, in genere intorno al pH 5-6 a temperature di 50-80 °C.
Nello sbiancamento meccanico della polpa, il perossido di idrogeno e lo sbiancamento con ditionito sono spesso combinati in due fasi sequenziali.
2.3.2. Anidride solforosa
L’anidride solforosa è utilizzata prevalentemente sotto forma di idrogenosolfito di sodio (NaHSO3). Tuttavia, a causa del suo effetto sbiancante relativamente scarso, SO2 non è più ampiamente utilizzata. Può essere utilizzata come pretrattamento nella produzione meccanica della polpa prima dello sbiancamento con ditionito e trova applicazione anche nel trattamento della lana.
2.3.3. Derivati dell’acido solfinico
I derivati importanti dell’acido solfinico includono l’idrossimetansolfinato di sodio e l’acido formamidinesolfinico.
Gli idrossimetansolfinati vengono prodotti trattando i ditioniti con formaldeide e sono più stabili dei ditioniti. Richiedono temperature più elevate per raggiungere il loro pieno potere riducente.
Questi derivati vengono impiegati in processi che operano sopra i 75 °C, dove il ditionito si decomporrebbe rapidamente. Trovano applicazione nel sapone sbiancante, nella colla, nella gelatina, negli acidi grassi e principalmente nei processi di tintura.
L’acido formamidinesolfinico, noto anche come biossido di tiourea, si ottiene dalla tiourea e dal perossido di idrogeno. È un prodotto cristallino scarsamente solubile in acqua che diventa più solubile in condizioni alcaline e mostra il suo massimo potere riducente sopra gli 80 °C.
Questo acido viene utilizzato per migliorare la brillantezza dei tessuti e rimuovere i coloranti dai tessuti, in modo simile all’acido idrossimetansolfinico. Il suo forte potere riducente ad alte temperature lo rende adatto allo sbiancamento delle fibre secondarie durante la fase di dispersione ed è particolarmente efficace nel distruggere i coloranti utilizzati per la carta colorata.
3. Enzimi
L’uso tecnico degli enzimi nello sbiancamento non è ancora ampiamente adottato e rimane l’eccezione nei processi industriali. Mentre la scoperta di enzimi che degradano la lignina nei funghi del marciume bianco ha offerto un potenziale per la delignificazione e lo sbiancamento su scala industriale, vi erano delle sfide che ne limitavano l’applicazione pratica.
La reazione catalizzata da questi enzimi era lenta e non abbastanza selettiva, e gli enzimi richiedevano coenzimi che degradassero la cellulosa, il che era indesiderabile.
Uno dei problemi generali con l’applicazione degli enzimi è la necessità di ceppi di enzimi altamente puri per evitare reazioni collaterali negative causate da altri enzimi. Inoltre, molti processi industriali operano a temperature elevate o a livelli di pH estremi, che richiedono l’uso di enzimi adattati a queste condizioni.
Gli organismi termofili, che prosperano in ambienti ad alta temperatura, sono spesso preferiti come fonte per la selezione di enzimi con proprietà adatte.
Sono stati studiati enzimi specifici per il loro potenziale nei processi di sbiancamento. Le xilanasi, ad esempio, vengono utilizzate per rimuovere una parte dello xilano precipitato dalle polpe kraft non sbiancate. Questo trattamento riduce la domanda di biossido di cloro nello sbiancamento senza cloro elementare (ECF) di circa il 10%.
Si ritiene che la lignina sulle fibre sia parzialmente coperta dallo xilano precipitato e la rimozione dello xilano rende più facile il lavaggio della lignina. Tuttavia, l’effetto complessivo dell’applicazione della xilanasi è moderato e rimane un’opzione di nicchia per le cartiere con accesso limitato al biossido di cloro.
La laccasi è un enzima coinvolto nella polimerizzazione delle unità di fenilpropano nelle piante, che contribuisce alla formazione del polimero di lignina. La laccasi può essere utilizzata per la delignificazione della polpa con l’aiuto di un mediatore.
I mediatori possono essere facilmente convertiti in cationi radicali dalla laccasi e dall’ossigeno, e questi prodotti intermedi ossidano la lignina. Teoricamente, il mediatore può essere riossidato più volte dall’enzima, ma in pratica, le reazioni ripetute sono rare. Di conseguenza, la domanda di mediatori, come l’N-idrossibenzotriazolo, è elevata, rendendo l’applicazione industriale economicamente non praticabile.
Le cellulasi, un gruppo di enzimi che scompongono la cellulosa, sono state utilizzate per ammorbidire il tessuto di cotone. Sono applicate nel lavaggio con pietra dei jeans come sostituto dell’effetto meccanico delle pietre pomici. L’azione delle cellulasi sulla superficie del tessuto provoca lo sbiadimento del colore poiché il colorante si trova principalmente sullo strato esterno delle fibre.
Le cellulasi sono state anche suggerite per migliorare la resistenza delle fibre della polpa di carta straccia. Dissolvendo particelle fini e fibrille, le cellulasi possono aumentare la lunghezza media delle fibre e potenziare il potenziale di resistenza. Tuttavia, questo processo di solubilizzazione riduce la resa e aumenta il carico sull’effluente, rendendo improbabile un’applicazione su larga scala da una prospettiva economica e ambientale.
Riferimento
- Bleaching; Ullmann’s Encyclopedia of Industrial Chemistry. – https://onlinelibrary.wiley.com/doi/10.1002/14356007.a04_191.pub2