
Il 1,4-butandiolo è un composto chimico con formula molecolare C4H10O2. È un liquido incolore e inodore che appartiene alla famiglia dei dioli, composti che contengono due gruppi idrossilici (OH).
Sommario
1. Proprietà fisiche del 1,4-butandiolo
Il 1,4-butandiolo (massa molare: 90,12 g/mol) è un liquido trasparente con odore minimo, che mostra proprietà igroscopiche. Si dissolve facilmente in acqua, alcoli, chetoni, glicoleteri e acetati di glicoleteri. Tuttavia, la sua solubilità in etere dietilico ed esteri è inferiore e non è solubile con idrocarburi alifatici e aromatici, così come con idrocarburi clorurati.
Proprietà | Valore |
---|---|
Punto di fusione | 20,2 °C |
Punto di ebollizione | 230,5 °C (a 101,3 kPa) |
Densità (𝜚) | 1,017 g/cm³ (a 20 °C) 1,0154 g/cm³ (a 25 °C) |
Temperatura critica | 446 °C |
Pressione critica | 41,2 bar |
Viscosità (𝜂) | 91,56 mPa s (a 20 °C) 71,5 mPa s (a 25 °C) |
Indice di rifrazione | 1,4460 (a 20 °C) 1,4446 (a 25 °C) |
Costante dielettrica (𝜀) | 31,4 |
Flash Punto | 134 °C |
2. Reazione chimica del 1,4-butandiolo
Il 1,4-butandiolo subisce facilmente ciclizzazione quando esposto a un mezzo acido, producendo tetraidrofurano.
Quando sottoposto a deidrogenazione in fase gassosa e utilizzando catalizzatori a base di rame, forma 𝛾-butirrolattone.
Inoltre, il 1,4-butandiolo reagisce con acidi monocarbossilici, producendo diesteri. L’esterificazione con acidi dicarbossilici e i loro derivati determina la formazione di esteri polimerici termoplastici lineari, parzialmente cristallini.
A circa 200 °C, il 1,4-butandiolo reagisce con ammoniaca o un’ammina utilizzando catalizzatori di nichel o cobalto e in presenza di idrogeno, producendo pirrolidina o derivati della pirrolidina.
Il fosgene reagisce con il 1,4-butandiolo a -5 °C, producendo il bis(cloroformiato) del butandiolo.
Inoltre, l’acrilonitrile reagisce con il 1,4-butandiolo a temperature comprese tra 20 e 100 °C in presenza di quantità catalitiche di alcali, per formare 1,4-bis(2-cianoetossi)butano.
Similmente ad altri alcoli, anche il 1,4-butandiolo può subire vinilazione, con conseguente formazione di mono o diviniletere.
3. Produzione di 1,4-butandiolo
Dagli anni ’90, sono state sviluppate varie tecnologie alternative per la produzione di 1,4-butandiolo. La tecnologia Reppe, che si basa su acetilene e formaldeide, rimane il metodo più diffuso.
Inoltre, altri processi utilizzano benzene o butano tramite anidride maleica, propilene, butadiene e zuccheri come percorsi alternativi per la sua produzione.
3.1. Produzione di 1,4-butandiolo da 2-butyne-1,4-diolo
L’1,4-butandiolo viene prodotto su larga scala industriale mediante idrogenazione continua del 2-butyne-1,4-diolo. Questo processo impiega prevalentemente catalizzatori di nichel modificati. Il processo di flusso a due stadi viene eseguito nell’intervallo di temperatura di 80-170 °C e a una pressione di 250-300 bar.

Il processo inizia con una soluzione acquosa di 2-butyne-1,4-diolo (30-50%), insieme a idrogeno privo di monossido di carbonio e miscela di reazione riciclata, che agisce come mezzo di dissipazione del calore.
Questa miscela passa attraverso un catalizzatore a letto fisso di tipo nichel ridotto nel reattore principale, dove avviene oltre il 99% della reazione.
La temperatura iniziale è di circa 80 °C e non deve superare i 170 °C per evitare reazioni di decomposizione indesiderate. La circolazione dell’idrogeno assicura una migliore distribuzione del liquido. Il secondo reattore o reattore di finitura completa la conversione dei composti insaturi.
I diversi processi impiegati commercialmente differiscono principalmente nel catalizzatore utilizzato. BASF e Invista Technologies descrivono Ni supportato su ossidi di zirconio o alluminio, mentre il nichel Raney, impiegato come catalizzatore a letto fisso, è utilizzato e concesso in licenza da Invista.
Un’altra variante prevede l’idrogenazione a bassa pressione a circa 20 bar utilizzando un catalizzatore di nichel Raney sospeso, seguita da idrogenazione a 120-140 °C e 140-210 bar catalizzata da un contatto a letto fisso (da Ineos).
Il prodotto grezzo ottenuto contiene metanolo, propanolo e butanolo come sottoprodotti, insieme a tracce di 2-metil-1,4-butandiolo, 4-idrossibutirraldeide, 𝛾-butirrolattone, acetali e trioli.
Per ottenere 1,4-butandiolo puro, l’effluente del reattore viene sottoposto a distillazione frazionata. Inizialmente, vengono rimossi acqua e monoalcoli come metanolo, propanolo e butanolo. Successivamente, il 1,4-butandiolo viene separato da sostanze ad alto punto di ebollizione come trioli e sali, insieme a impurità come 𝛾-butirrolattone, acetali, 2-metil-1,4-butandiolo e 4-idrossibutirraldeide.
Il 1,4-butandiolo puro può essere ulteriormente isolato in una colonna aggiuntiva, che separa 4-idrossibutirraldeide, acetali e 𝛾-butirrolattone come sostanze a basso punto di ebollizione.
3.2. 1,4-butandiolo a base di benzene o butano tramite anidride maleica
L’ossidazione in fase gassosa di benzene o n-butano con ossigeno porta alla produzione di anidride maleica. Questa anidride maleica può essere adsorbita dall’acqua dai gas di scarico dell’ossidazione, producendo acido maleico, o da composti organici altobollenti come il dibutilftalato.
La soluzione di acido maleico in acqua può essere idrogenata in un processo ad alta pressione per produrre 1,4-butandiolo, con la presenza di catalizzatori di carbone attivo a base di Re drogato. I droganti utilizzati in questi catalizzatori sono principalmente Pd e Pt.
Tuttavia, il processo genera sottoprodotti come n-butanolo, n-propanolo, metanolo e tetraidrofurano. Nonostante la sua semplicità, il catalizzatore di idrogenazione è costoso a causa dell’elevato contenuto di metalli preziosi.
Di conseguenza, finora è stata realizzata solo una produzione commerciale di questo processo, condotta da Lima negli Stati Uniti.
Un approccio commerciale più comune prevede l’idrogenazione in fase gassosa dei diesteri maleici, derivati dall’anidride maleica.
Questo processo è stato sviluppato da Kvaerner Process Technology (KPT, Londra, ora Johnson Matthey Davy Technologies (JM Davy)) negli anni ’80. Il primo passaggio prevede la produzione di dimetil maleato da anidride maleica e metanolo, utilizzando una resina a scambio ionico fortemente acida come catalizzatore.
Il dimetil maleato risultante viene quindi idrogenato in fase gassosa utilizzando un sistema di catalizzatore contenente Cu a una pressione di 2-8 MPa e temperature di 150-250 °C.
Questo processo produce una miscela di 1,4-butandiolo, tetraidrofurano, butirrolattone, una piccola quantità di dimetil succinato intermedio e, come principale sottoprodotto, n-butanolo.
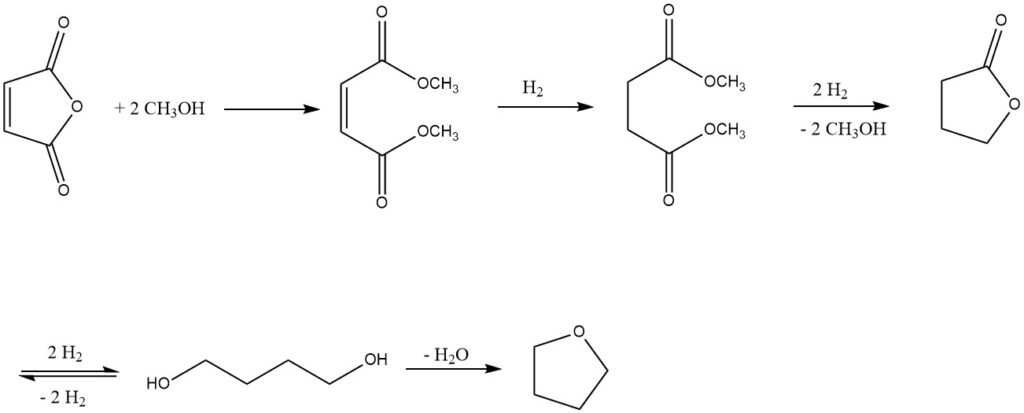
Il butirrolattone e il dimetil succinato possono essere recuperati come azeotropi e riciclati nella fase di idrogenazione per ottenere la conversione completa in 1,4-butandiolo e tetraidrofurano.
JM Davy ha concesso in licenza questo processo più volte per stabilire impianti di butandiolo/butirrolattone/tetraidrofurano in varie località dell’Asia, tra cui Arabia Saudita, Malesia, Corea e Cina.
3.3. Produzione di 1,4-butandiolo dal propilene
Una materia prima alternativa per il 1,4-butandiolo è il propilene, che può essere ottenuto tramite alcol allilico. Dairen a Taiwan e in Cina, così come Lyondell negli Stati Uniti e nei Paesi Bassi, utilizzano questo processo.
Per ottenere l’alcol allilico, il propilene viene prima ossidato a ossido di propilene, che viene poi isomerizzato (Lyondell) o idrolizzato ad alcol allilico. L’idrolisi comporta l’acetossilazione del propilene in fase gassosa con ossigeno, che porta alla formazione di acetato di allile, che viene successivamente idrolizzato per produrre alcol allilico (Dairen).
Il passaggio successivo comporta l’idroformulazione dell’alcol allilico in un solvente con un catalizzatore omogeneo a base di rodio, producendo 4-idrossibutirraldeide. Un sottoprodotto principale in questo passaggio è la 3-idrossi-2-metil-propionaldeide.
Dopo l’estrazione delle aldeidi, vengono sottoposte a idrogenazione utilizzando nichel Raney come catalizzatore, con conseguente 1,4-butandiolo, che viene quindi purificato tramite distillazione.

Tuttavia, uno dei principali sottoprodotti di questa reazione è il 2-metil-1,3-propandiolo. Inoltre, altri sottoprodotti formati durante questo processo includono n-propanolo e isobutyraldeide.
3.4. Produzione di 1,4-butandiolo dal butadiene
Mitsubishi impiega un processo in tre fasi per produrre 1,4-butandiolo:
- Il butadiene e l’acido acetico subiscono una reazione catalitica per produrre 1,4-diacetossi-2-butene.
- La successiva idrogenazione di 1,4-diacetossi-2-butene produce 1,4-diacetossibutano.
- Infine, l’idrolisi di 1,4-diacetossibutano porta alla formazione di 1,4-butandiolo.
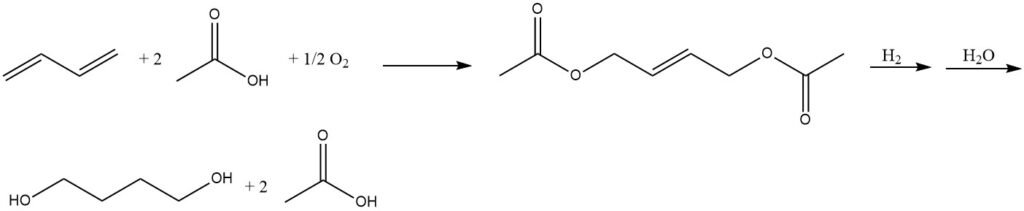
L’idrolisi del diacetato può anche produrre tetraidrofurano a causa delle condizioni di reazione altamente acide.
BASF ha brevettato un processo simile, in cui l’acido acetico si aggiunge prima al butadiene e il prodotto risultante si isomerizza in 1,4-diacetossi-2-butene.
Il processo di Toyo Soda prevede l’aggiunta di cloro al butadiene per formare una miscela di 1,4-dicloro-2-butene e 3,4-dicloro-1-butene. Questa miscela reagisce con l’acetato di sodio per produrre 1,4-diacetossi-2-butene, che viene poi direttamente idrogenato a 1,4-butandiolo.
In un brevetto descritto da Shell, il butadiene reagisce con terz-butil idroperossido usando un catalizzatore al cobalto per formare 1,4-di(terz-butilperossi)butene-2, che viene poi convertito in 1,4-butandiolo mediante idrogenazione. Come sottoprodotto, si forma l’1,2-butandiolo.
Eastman ha un processo diverso che inizia con il butadiene come materia prima. Innanzitutto, il butadiene viene ossidato dall’ossigeno in presenza di un catalizzatore d’argento per formare 1,2-epossi-3-butene. L’epossido subisce quindi un riarrangiamento per produrre 2,5-diidrofurano, che viene successivamente isomerizzato a 2,3-diidrofurano.
Dopo l’aggiunta di acqua catalizzata da acido a un equilibrio di 2-idrossitetraidrofurano e 4-idrossibutirraldeide, seguita da idrogenazione, si genera 1,4-butandiolo. In alternativa, la conversione di 2,5-diidrofurano in 1,4-butandiolo può essere eseguita come una sintesi one-pot.
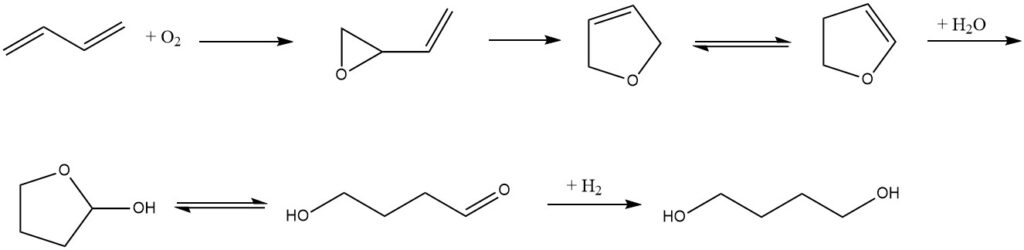
3.5. Produzione di 1,4-butandiolo da biomassa
Negli ultimi due decenni sono stati compiuti notevoli sforzi per produrre 1,4-butandiolo e suoi derivati da fonti di biomassa.
Uno dei primi approcci prevedeva l’uso di furfurale, che può essere decarbonilato a furano.
BASF ha sviluppato un metodo promettente in cui il furano viene idrogenato in presenza di acqua e un catalizzatore a base di renio a pressione elevata, con conseguente formazione di 1,4-butandiolo. 𝛾-butirolattone e n-butanolo vengono prodotti come sottoprodotti.
Shell ha anche lavorato all’ottimizzazione del processo utilizzando catalizzatori a base di renio. Con un catalizzatore Re/Pd su carbonio, Shell ha ottenuto un’elevata resa di tetraidrofurano e 1,4-butandiolo come prodotti principali.
Alcune aziende utilizzano metodi di fermentazione basati sullo zucchero per ottenere direttamente 1,4-butandiolo o i suoi precursori. Genomatica ha sviluppato un processo per produrre 1,4-butandiolo fermentando il glucosio utilizzando batteri Escherichia coli geneticamente modificati. Dopo la fermentazione, il brodo contiene 1,4-butandiolo diluito in acqua, insieme a biomassa e sali.
Un processo di distillazione separa l’acqua e, dopo un’accurata filtrazione e rimozione dei sali, il 1,4-butandiolo grezzo subisce un’idrogenazione per eliminare le impurità che possono influire sulla stabilità del colore.
Un’ulteriore purificazione viene eseguita tramite ulteriori fasi di distillazione. Il processo Genomatica è stato implementato commercialmente in un impianto (capacità 30 ×103 t, Novamont) in Italia dal 2016.
Un altro approccio prevede la fermentazione degli zuccheri in acido succinico, che funge da precursore per la produzione di 1,4-butandiolo. Aziende come BioAmber, Myriant, Reverdia e Succinity sono state coinvolte nella commercializzazione di questo processo di fermentazione.
La fermentazione diretta degli zuccheri in acido succinico richiede il controllo del pH a causa del basso pH risultante del brodo di fermentazione. Materiali di base come ammoniaca o idrossidi alcalini/alcalini terrosi vengono utilizzati per il controllo del pH.
Il succinato di diammonio risultante può essere trattato con acido solforico per liberare l’acido succinico. L’acido succinico può quindi essere convertito in 1,4-butandiolo mediante idrogenazione in fase gassosa come anidride o diestere utilizzando catalizzatori a base di Cu o mediante idrogenazione in fase liquida utilizzando catalizzatori a base di metalli preziosi.
La fermentazione degli zuccheri può anche portare a 𝛾-butirrolattone. Metabolix ha sviluppato un metodo per convertire gli zuccheri in un processo di fermentazione in poli(4-idrossibutirrato) (poli(butirrolattone)), che può essere depolimerizzato in butirrolattone in presenza di un catalizzatore a temperature superiori a 200 °C.
I risultati migliori si ottengono con l’idrossido di calcio come catalizzatore e la biomassa residua viene convertita in combustibile solido. Tuttavia, non è stato ancora stabilito alcun impianto commerciale per questo processo.
4. Utilizzi del 1,4-butandiolo
Il 1,4-butandiolo svolge un ruolo cruciale come intermedio versatile nell’industria chimica e funge da precursore per 𝛾-butirrolattone e tetraidrofurano.
La sua applicazione più significativa risiede nella produzione di poliuretani e poliesteri, come il poli(butilene tereftalato), comunemente noto come PBT. Questi materiali hanno diversi usi in vari settori.
I poliuretani derivati dal 1,4-butandiolo sono impiegati nella produzione di elastomeri cellulari e compatti, che trovano applicazioni di vasta portata grazie alla loro elasticità e resilienza.
Il poli(butilene tereftalato) è ampiamente lavorato per creare materiali plastici e adesivi hot-melt. Inoltre, è utilizzato nella produzione di pellicole e fibre di plastica, il che lo rende un materiale versatile utilizzato in diversi prodotti e settori.
Riferimenti
- Butandiols, Butenediol, and Butynediol, Ullmann’s Encyclopedia of Industrial Chemistry. – https://onlinelibrary.wiley.com/doi/10.1002/14356007.a04_455.pub2
- Acidi organici: acido succinico e malico. – https://www.sciencedirect.com/science/article/abs/pii/B9780444640468001592
- https://www.industrialchemicals.gov.au/sites/default/files/1-4-Butanediol.pdf