Acetylene is produced by several methods: calcium carbide reaction, partial combustion of hydrocarbons, electric arc processes, thermal cracking with heat carriers and as byproduct of steam cracking.
1. Calcium Carbide Reaction:
- This traditional method involves reacting calcium carbide with water, generating both acetylene and calcium hydroxide.
- It’s a simple and well-established process, but the production of calcium carbide has high energy requirements and environmental concerns.
2. Partial Combustion of Hydrocarbons:
- This method utilizes the partial oxidation of natural gas, methane, or heavier hydrocarbons like naphtha and vacuum gas oil in a burner to generate acetylene in situ.
- It offers flexibility in feedstock choice and potentially higher efficiency compared to calcium carbide, but precise control of reaction conditions is crucial.
3. Electric Arc Processes:
- These processes crack hydrocarbons using high-temperature electric arcs, directly driving the endothermic acetylene synthesis reaction.
- They offer independence from hydrocarbon feedstock type and potentially reduced hydrocarbon consumption compared to partial combustion, but require high-grade electricity and complex arc reactor design.
4. Thermal Cracking with Heat Carriers:
- This method employs indirect heat transfer through various heat carriers like refractory materials or hot combustion gases to crack feedstocks.
- While older processes like Wulff and Hoechst HTP faced limitations, newer advancements like the ACR and Dow PCC processes show promise in handling heavier feeds and achieving efficient cracking for acetylene production.
5. Byproduct of Steam Cracking:
- Steam cracking for olefin production like ethylene naturally creates acetylene as a byproduct.
- This source can be tapped by implementing acetylene removal techniques like catalytic hydrogenation or solvent extraction for high-purity acetylene recovery.
1. Thermodynamic and Kinetic Aspects
High temperature and rapid reaction times are essential for acetylene production from hydrocarbons. This is because of the following aspects:
- Thermodynamic constraints: At standard temperatures, acetylene is unstable compared to other hydrocarbons (high ΔHf and ΔGf). However, above ~1230 °C, acetylene becomes thermodynamically favored, with the intersection point in ΔGf diagrams shifting leftward with decreasing hydrocarbon chain length (methane requiring the highest temperature).
- Kinetic considerations: Even at these high temperatures, acetylene remains less stable than its elemental constituents (C and H). This thermodynamic preference for decomposition necessitates rapid quenching of nascent acetylene (residence times ~0.1-10 ms) to prevent its breakdown.
- Competing reactions: Cracking and recombination of feedstock hydrocarbons, along with further acetylene conversion to byproducts, occur alongside acetylene formation. Short residence times are crucial to minimize these competing reactions and maximize acetylene yield.
Partial oxidation offers an alternative route, where combustion of part of the hydrocarbon generates the heat needed for acetylene production from the remaining portion. Precise control of the methane:oxygen ratio is important to achieve the desired reaction temperature and optimize acetylene yield.
In summary, successful acetylene production from hydrocarbons necessitates overcoming thermodynamic limitations by high temperatures, combined with rapid quenching and precise reaction control to minimize competing and undesirable reactions.
2. Acetylene Production by Partial Combustion Processes
Partial combustion processes capitalize on in situ heat generation by partial oxidation of a portion of the feedstock to drive acetylene synthesis from the remaining portion. This method enables the use of diverse raw materials, from methane and ethane to heavier fractions like naphtha and vacuum gas oil. Natural gas, due to its widespread availability, serves as a particularly suitable feedstock.
Process description
In this process, both feedstock and oxygen undergo separate preheating for optimal performance. The preheated streams enter a burner, where they mix and ignite within a reaction zone. The product mixture exits the reaction zone and is rapidly cooled, typically with water or oil, to prevent undesirable decomposition.
Efficient acetylene formation demands a short and uniform residence time for the gas within the reaction zone, typically a few milliseconds. Precise control of flow velocity balances high yield with avoidance of preignition, flame instability, and coke deposition.
Examples of industrial plants are:
- BASF process is the most widely used partial combustion process for natural gas, featuring submerged burners and efficient heat recovery.
- Submerged Flame Process (SFP) is a process designed for heavy oil fractions, featuring simple cracking, simultaneous acetylene-ethylene production, and high thermal efficiency.
- Partial Combustion Carbide Process is a pilot-plant scale process using coke, oxygen, and lime, offering potential future advantages like high carbon conversion and thermal efficiency for coal-based acetylene production.
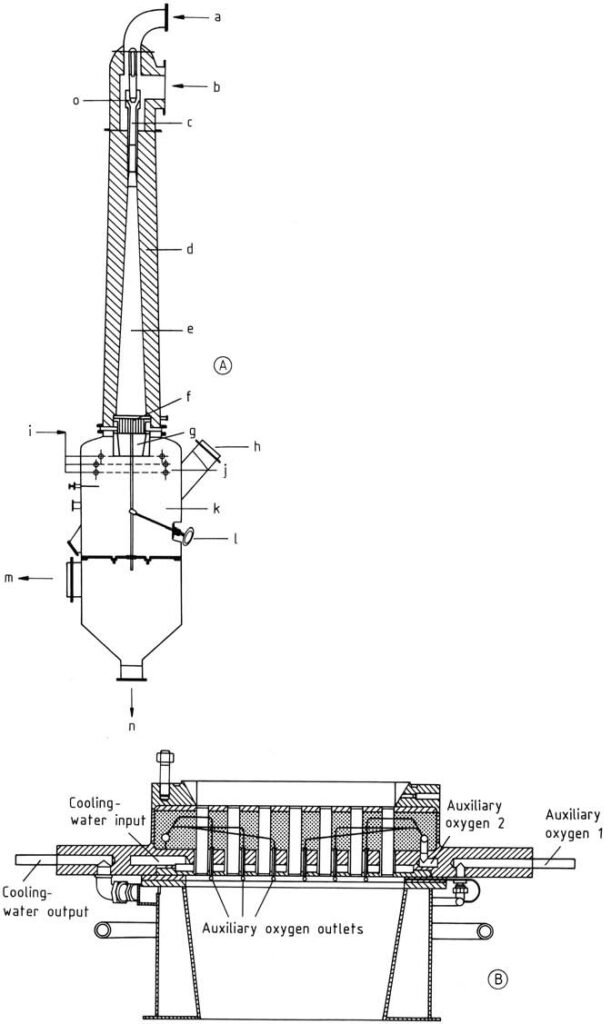
A) The burner: a) Oxygen: b) Hydrocarbon; c) Mixer; d) Concrete lining; e) Diffuser; f) Burner block; g) Reaction chamber; h) Rupture disk; i) Quench-medium inlet; j) Quench rings; k) Quench chamber; l) Manual scraper; m) Cracked-gas outlet; n) Quench-medium outlet. B) The burner block
While partial combustion processes primarily target acetylene, they also generate byproducts like hydrogen and carbon monoxide. Within a complex chemical plant, these byproducts can be converted to valuable products like synthesis gas, pure hydrogen, and carbon monoxide, ultimately enhancing the overall economic viability of the process.
- For a more detailed description of these industrial processes, you can refer to the reference at the end of this article.
3. Acetylene Production by Electrothermic Processes
Electrothermic processes, distinct from partial oxidation, use electric arc technology to achieve acetylene synthesis. This method offers several advantages:
- Feedstock independence: The energy required for acetylene formation is decoupled from the specific hydrocarbon feedstock.
- Reduced hydrocarbon consumption: Compared to partial oxidation, electrothermic processes can cut hydrocarbon consumption by up to 50%.
- Favorable economics: Under favorable conditions like access to cheap electricity (nuclear, hydro, coal) or limited hydrocarbon availability, electrothermic processes can be more economical.
Among electrothermic options, the electric arc process stands out for its suitability in driving the highly endothermic high-temperature acetylene synthesis reaction. It was pioneered in Germany in 1925 for butadiene production, the electric arc process for acetylene synthesis was first commercialized in 1940 at Chemische Werke Hüls.
Both gaseous and liquid hydrocarbons, as well as solids like coal, can serve as feedstock for electric arc processes. Arc furnace design and product purification steps are tailored to the specific feedstock.
Gaseous/gasified feeds typically employ a one-step process where the arc directly heats the cracking gas. Liquid and solid feeds may utilize a two-step process where hydrogen, preheated in the arc furnace, acts as a plasma medium for feedstock injection.
Hydrogen formed during cracking creates a hydrogen atmosphere for the arc in both process types. Due to hydrogen’s high conductivity and ion-electron recombination rate, arc lengths exceeding a certain threshold necessitate direct current (DC) operation at standard frequencies and high voltages. Consequently, all commercial electric arc acetylene plants rely on DC power.
Examples of industrial electrothermic processes are:
- Production from Gaseous and/or Gasified Hydrocarbons (Hüls Arc Process)
- Production from Liquid Hydrocarbons (Plasma Arc Process)
- Production from Coal (Arc Coal Process)
- Production from Calcium Carbide
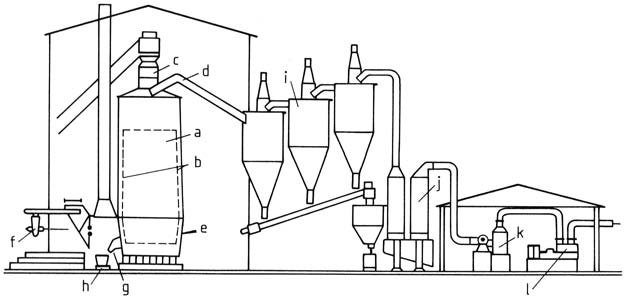
a) Carbide furnace; b) Refractory brick lining; c) Charging hopper; d) Gas outlet; e) Oxygen jet; f) Tapping burner; g) Tapping chute; h) Bogey; i) Cyclone; j) Washing column; k) Desintegrator; l) Compressor
- For a more detailed description of these industrial processes, you can refer to the reference at the end of this article.
4. Production of Acetylene by Other Cracking Processes
4.1. Thermal Cracking By Heat Carriers
Thermal cracking using heat carriers offers an alternative route to acetylene production, distinct from partial oxidation and electric arc methods. However, older processes like the Wulff and Hoechst HTP were hindered by limitations like feedstock restrictions (refined naphtha and LPG) and soot formation, ultimately leading to their discontinuation.
Example of emerging technologies replacing the old Wulff and Hoechst HTP process are:
- Kureha, Chiyoda, Union Carbide ACR Process: This pilot-scale process utilizes superheated steam as a heat carrier at 2000 °C, generated via combustion of H2-CH4 mixtures with oxygen. Crude oil feedstock undergoes rapid cracking in a multi-port reactor, achieving high hydrogen, olefins, and acetylene yields (4.2 wt%, significantly higher than traditional olefin processes).
- Dow Partial Combustion Cracking (PCC) Process: This process addresses coking and soot issues by partially oxidizing recycled quench oil (from cracking) in the burner to generate synthesis gas and maintain a high hydrogen partial pressure in the reaction zone. While accepting heavier feeds like crude oil and residues, the acetylene yield (2.5 wt%) is lower than the ACR process due to longer residence times (3-10x longer).
The following table provides a comparison of the features of these processes:
Feature | Wulff & Hoechst HTP | ACR | Dow PCC |
---|---|---|---|
Feedstock | Refined naphtha, LPG | Crude oil | Crude oil, heavy residues |
Heat Carrier | Refractory material, hot combustion gases | Superheated steam (2000°C) | Synthesis gas from quench oil partial oxidation |
Acetylene Yield | Limited | High (4.2 wt%) | Moderate (2.5 wt%) |
Advantages | Indirect heat transfer, high thermal efficiency | Crude oil compatibility, high olefin yield | Heavy feed capability, high hydrogen recovery |
Disadvantages | Soot formation, naphtha/LPG restriction | Pilot-scale stage, complex burner | Lower acetylene yield, longer residence time |
4.2. Acetylene as a Byproduct of Steam Cracking
Steam cracking produces desired olefins like ethylene and propene, but also generates various byproducts, including acetylene. Its concentration depends on:
- Feedstock: Different hydrocarbons yield varying acetylene levels.
- Residence Time: Longer cracking durations increase acetylene formation.
- Cracking Severity: Higher crack severity (conversion or P/E ratio) leads to more acetylene.
Typical off-gas acetylene concentrations range from 0.25 to 1.35 wt%, with specific cases reaching up to 2.1 wt%. The C2 fraction typically contains 0.4-2.5 wt% acetylene. A 400,000 t/a ethylene plant generates 4,500-11,000 t/a acetylene.
To remove acetylene, most ethylene plants employ either: catalytic selective hydrogenation which is the dominant method for converting acetylene to ethylene on Pd-doped catalysts or solvent extraction that uses DMF for high-purity acetylene recovery.
Over 112,000 t/a of petrochemical acetylene were recovered as byproduct globally in 2006. However the total acetylene market declined due to various factors, leading to limited new acetylene recovery facility installations in recent years.
Petrochemical acetylene remains economically attractive, even with doubled ethylene prices. Retrofitting existing olefin plants with acetylene absorption and extraction from unavoidable byproduct acetylene remains the most viable route for meeting acetylene demand.
Reference
- Acetylene; Ullmann’s Encyclopedia of Industrial Chemistry. – https://onlinelibrary.wiley.com/doi/10.1002/14356007.a01_097.pub4