Production de solution d'hydroxyde de sodium
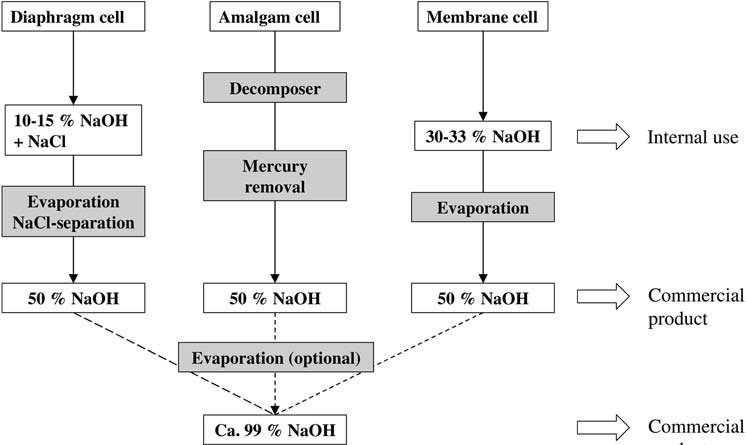
1. Électrolyse du chlorure de sodium
La soude caustique est produite industriellement principalement par électrolyse du chlorure de sodium. Cela donne une solution d’hydroxyde de sodium, du chlore et de l’hydrogène dans le rapport massique 1 : 0,88 : 0,025 conformément à l’équation globale suivante :
2 NaCl + 2 H2O → 2 NaOH + Cl2 + H2
Au début des années 1980, le procédé à membrane a été introduit, les autres procédés en fonctionnement à cette époque étant les procédés à amalgame et à diaphragme. La production de chlore-alcali en 2004 a été répartie entre les différents procédés.
La technologie membranaire a continué à gagner des parts de marché en 2004. Sur la base des changements de capacité annoncés, les procédés membranaires ont représenté plus de 44 % de la capacité totale installée de chlore-alcali.
La technologie à membrane permet d’économiser environ 30 % d’énergie électrique et est la meilleure technique disponible, elle sera donc de plus en plus utilisée dans les nouvelles unités.
Au Japon, en 1988, toutes les usines basées sur le procédé d’amalgame avaient été soit fermées, soit converties au procédé à membrane. Certaines usines à membranes japonaises ont également été remplacées par des usines à membranes pour des raisons à la fois de coût et de qualité.
Dans le procédé d’amalgame, une solution d’hydroxyde de sodium est produite à partir d’amalgame de sodium et d’eau sur un catalyseur en graphite à 80 – 120 °C. La solution à 50 % en poids produite est très pure. Il est refroidi, le mercure est éliminé par centrifugation ou filtration à travers des filtres à cartouche ou à plaque de pression, et il est ensuite vendu sans autre traitement.
Dans la cellule à diaphragme, la solution de chlorure de sodium appauvrie du compartiment anodique est transférée quantitativement au compartiment cathodique, de sorte que la liqueur de cellule qui y est produite contient env. 18 % en poids de chlorure de sodium et 10 à 15 % en poids d’hydroxyde de sodium.
Au cours de l’évaporation pour donner une solution de NaOH à 50 % en poids, toutes les impuretés entraînées avec la solution de chlorure de sodium appauvrie sont éliminées jusqu’à leur solubilité limite par cristallisation fractionnée ; ainsi, la teneur en chlorure de sodium ne peut être réduite qu’à env. 1 à 1,5 % en poids
Dans le procédé DH de la société PPG, une purification supplémentaire est effectuée par extraction avec de l’ammoniac liquide anhydre. On obtient ainsi un produit comparable à celui issu du procédé amalgame (qualité rayonne), mais le procédé est peu utilisé à cause du coût.
Ceci est également vrai d’un procédé japonais dans lequel une solution d’hydroxyde de sodium relativement pure est obtenue en refroidissant la liqueur de diaphragme à 50 % en poids et en récupérant les cristaux de NaOH pur. 3,5 H2O formé.
Dans le procédé à membrane, une membrane hydrauliquement imperméable empêche le mélange des électrolytes. Ce procédé produit une solution d’hydroxyde de sodium de haute pureté, pratiquement sans chlorure, comparable à celle du procédé d’amalgame. Cependant, la teneur en chlorure augmente d’un facteur d’env. 10 si le fonctionnement de la cellule est interrompu, du fait de la diffusion des ions Cl‾ à travers la membrane.
Le sulfate et le chlorate présents dans l’anolyte affectent également la concentration de ces impuretés dans la liqueur caustique de la cellule membranaire, puisque la membrane sélective des cations a une perméabilité résiduelle appréciable pour les anions. La plupart des cellules à membrane offrent des performances économiques optimales à une concentration de NaOH de 30 à 35 % en poids.
Une membrane échangeuse d’ions a maintenant été développée qui permet de produire une solution d’hydroxyde de sodium à 50% en poids dans la cellule, bien qu’une augmentation considérable de la tension soit nécessaire. De telles membranes ne sont viables que si les coûts de vapeur sont élevés et les coûts d’électricité faibles.
La solution d’hydroxyde de sodium à 30 – 33 % en poids est généralement concentrée dans un évaporateur à film tombant à deux ou trois étages (selon les coûts de vapeur et la taille de l’usine) pour donner une solution commerciale à 50 % en poids.
Pour un évaporateur à trois étages, la consommation de vapeur est de 0,55 t par tonne de NaOH (100 %), et pour un évaporateur à deux étages, de 0,71 t par tonne de NaOH (100 %), avec une solution d’hydroxyde de sodium et de la vapeur en contre-courant.
flux de courant.
L’évaporation de la liqueur de la cellule à membrane (contrairement à celle de la liqueur de la cellule à diaphragme) ne produit aucun matériau solide susceptible d’encrasser l’échangeur de chaleur ou d’éroder la tuyauterie. L’absorption de métaux pendant l’évaporation est d’environ 1 ppm en poids si des matériaux de construction appropriés sont utilisés (nickel, acier inoxydable).
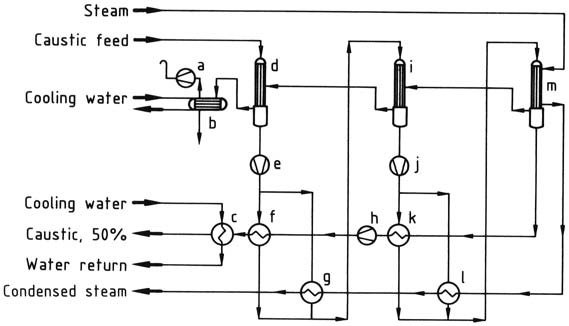
Les trois processus électrolytiques ont des besoins énergétiques différents. Le procédé à membrane consomme le moins d’énergie électrique (2200 à 2500 kWh par tonne de NaOH) mais nécessite 200 à 300 kWh supplémentaires par tonne de NaOH sous forme de vapeur pour produire une solution à 50 % en poids.
Le procédé à membrane consomme moins d’énergie électrique que le procédé à l’amalgame, mais nécessite 700 à 900 kWh par tonne de NaOH sous forme de vapeur pour l’étape d’évaporation et a donc le besoin énergétique total le plus élevé.
En raison de la forte consommation d’énergie électrique, de nombreuses recherches se sont attachées à réduire la tension des cellules. Un env. Une réduction de 1 V peut être obtenue en utilisant une cathode à diffusion d’oxygène (comme dans une pile à combustible) dans le processus de cellule à membrane, bien que dans ce cas, aucun sous-produit d’hydrogène ne soit produit.
Cette technologie suscite un intérêt croissant. La conception de la cellule, la cathode de diffusion d’oxygène et l’intégration de la cathode dans la conception de la cellule sont des points de développement prioritaires. L’étude des paramètres de fonctionnement et de la périphérie des cellules est également au centre des préoccupations.
L’électrolyse de NaCl fondu à 350 °C avec un diaphragme β-Al2O3 est également intéressante. Dans les cellules à l’échelle du laboratoire, une consommation électrique de 2350 kWh par tonne de NaOH peut être atteinte. Cette technique, elle aussi, n’a pas encore été utilisée à l’échelle commerciale.
2. Autres processus
La caustification de la solution de carbonate de sodium est la méthode la plus ancienne de production d’hydroxyde de sodium et était la seule méthode disponible jusqu’à l’introduction de l’électrolyse. Bien qu’il ait quasiment disparu de l’usage, il présente aujourd’hui un intérêt particulier pour les entreprises ayant accès au carbonate de sodium synthétique issu du procédé Solvay ou au carbonate de sodium naturel (ex. trona, Na3H(CO3)2·2 H2O).
Dans ce processus, un chaud, ca. Une solution à 12 % de carbonate de sodium est mélangée à de la chaux vive. Le carbonate de calcium qui précipite selon l’équation est éliminé, et le ca. Une solution d’hydroxyde de sodium à 12 % est évaporée en plusieurs étapes.
Na2CO3 + CaO·H2O → 2 NaOH + CaCO3
Les impuretés qui précipitent, principalement NaCl et Na2SO4, sont filtrées.
Dans une combinaison de cellules d’électrolyse et de dialyse, les sels de sodium peuvent être divisés en acides et alcalis correspondants, par exemple,
Na2SO4 + 2 H2O → 2 NaOH + H2SO4
Cette réaction peut être réalisée dans une cellule à deux chambres avec une membrane échangeuse de cations ou d’anions ; dans une cellule à trois chambres avec une membrane échangeuse de cations et une membrane échangeuse d’anions ; ou dans une cellule multichambre avec une combinaison de membranes cationiques, anioniques et bipolaires.
Cependant, dans toutes les cellules exploitées industriellement, le produit est une solution diluée d’hydroxyde de sodium (15 à 30 % en poids), qui contient également une partie du sel utilisé comme matière première.
Pour cette raison, ce type de procédé est le plus approprié pour traiter les eaux usées contenant des sels de sodium provenant de procédés dans lesquels la solution diluée d’hydroxyde de sodium obtenue peut être recyclée à des fins de neutralisation.
Une méthode alternative de production de solution d’hydroxyde de sodium pour les petites usines de pâte à papier, le procédé de récupération de la ferrite.
Ici, la liqueur résiduaire contenant des sels de sodium et des substances organiques est évaporée, et le résidu est mélangé avec du Fe2O3 et calciné. La ferrite de sodium formée est décomposée par l’eau pour donner NaOH et Fe2O3.
Les références
- Sodium Hydroxide; Ullmann’s Encyclopedia of Industrial Chemistry. Weinheim: Wiley-VCH.- https://onlinelibrary.wiley.com/doi/10.1002/14356007.a24_345.pub2