Le benzène était traditionnellement produit à partir du charbon, mais le pétrole est devenu la principale source au milieu du XXe siècle en raison de nouveaux procédés et d’une demande accrue. Le craquage catalytique et le reformage des fractions pétrolières produisent du benzène et d’autres composés aromatiques.
Table des matières
1. Production de benzène à partir du charbon
La carbonisation du charbon produit des huiles légères contenant du benzène, du toluène et des xylènes (BTX). Le rendement et la composition de ces huiles dépendent du type de charbon et de la température de carbonisation. La cokéfaction à basse température produit un coke à combustion propre avec une teneur en benzène plus faible. La cokéfaction à haute température produit un coke dur pour les hauts fourneaux et les huiles légères à plus forte teneur en benzène.
Les huiles légères sont séparées des goudrons de houille et la fraction BTX est extraite à l’aide d’une fraction pétrolière à haut point d’ébullition. Le BTX est ensuite récupéré de l’huile absorbante et purifié par distillation, traitement à l’acide sulfurique et hydrotraitement. L’extraction par solvant et le fractionnement étroit sont utilisés pour isoler les composants aromatiques individuels.
Divers procédés ont été développés pour affiner la coupe BTX en benzène de haute pureté ou en composants BTX de qualité supérieure. Le procédé Houdry-Litol est un exemple de procédé utilisant une série de réactions et un réacteur catalytique pour affiner la coupe BTX. Le procédé Litol modifié est particulièrement adaptable aux matériaux aromatiques complexes issus des fours à coke.
Une petite quantité de benzène peut également être obtenue par distillation des goudrons de cokerie, mais cette source n’a pas une importance majeure dans la production de benzène. Les goudrons de houille sont plus importants en tant que sources de brais, de naphtalène, d’anthracène et d’autres matières aromatiques condensées.
2. Production de benzène à partir du pétrole
Le craquage catalytique et le reformage du pétrole, développés à la fin des années 1930 et dans les années 1940, sont devenus une nouvelle source de benzène, de toluène, de xylènes et d’aromatiques supérieurs. Le pétrole a remplacé le charbon comme source de matériaux BTX, notamment aux États-Unis. La transition du charbon au pétrole s’est produite au Royaume-Uni et en Europe vers 1960.
Le toluène était très demandé pendant la Seconde Guerre mondiale pour la production de TNT. Cependant, il était coûteux de le produire à partir de naphtas vierges, puis à partir de naphtas de craquage catalytique et de reformage. L’un des premiers procédés de craquage catalytique a été développé par Houdry Corp.
Ce procédé utilisait un catalyseur silice-alumine déposé dans plusieurs lits fixes et régénéré fréquemment avec de l’air pour brûler le coke déposé. Un autre procédé développé par Mobil Oil utilisait un catalyseur silice-alumine à lit mobile. Le troisième type de procédé, développé par Exxon et d’autres, est connu sous le nom de procédé de craquage catalytique fluide (FCC) et est désormais utilisé exclusivement.
Bien que les procédés de craquage catalytique aient été développés principalement pour augmenter le rendement et l’indice d’octane des carburants automobiles, l’essence produite avait une teneur élevée en aromatiques, constituant une source de benzène pétrochimique.
2.1. Benzène du reformat
Le reformage catalytique est devenu une autre source d’aromatiques BTX issus du pétrole. Il a été installé dans les années 1940 et au début des années 1950 pour répondre à la demande croissante de benzène, utilisé dans la fabrication de résines, de détergents, de fibres synthétiques et d’autres produits chimiques.
Le reformage implique la déshydrogénation des naphtènes en aromatiques, ou l’isomérisation des alkylnaphtènes suivie d’une déshydrogénation. Les paraffines peuvent également être déshydrocyclisées en aromatiques. La réaction est lente, les conditions du procédé doivent donc être ajustées pour la rendre économique. Une petite quantité de désalkylation des aromatiques alkylés peut également se produire.
Les premières unités de reformage catalytique utilisaient des catalyseurs à base de métaux communs, tels que le molybdène, sur de l’alumine activée. Ces procédés avaient un cycle court et nécessitaient une régénération fréquente du catalyseur.
Le processus d’hydroformage fonctionnait à des températures et des pressions élevées avec recyclage d’hydrogène. Il convertissait les fractions de naphta en essences à indice d’octane élevé. Le catalyseur nécessitait une régénération toutes les 8 à 16 heures.
Les procédés de reformage catalytique ultérieurs utilisaient soit des lits de catalyseur mobiles, soit des lits fluidisés avec un catalyseur finement divisé. Différents procédés catalytiques utilisant du platine sur alumine et du platine avec modificateurs sur alumine ont également été développés.
Ces processus peuvent avoir des durées de cycle allant jusqu’à six mois ou beaucoup plus courtes, en fonction de la matière première, des conditions du processus et de la gravité de l’opération. La charge naphta doit être prétraitée par hydrotraitement catalytique pour éliminer les composés soufrés.
Les procédés commerciaux de reformage catalytique comprennent : le reformage catalytique (Institut Français du Pétrole), le magnaformage (Engelhard Industries), le plate-forme (UOP), le powerforming (Exxon Research & Engineering), le rhéniformage (Chevron Research Co.) et l’ultraformage (Standard Oil of Indiana). .
Les conditions de fonctionnement varient considérablement. Les températures varient de 425 à 525 °C et les pressions manométriques de 0,7 à 3,5 MPa.
Les conversions en naphtène approchent les 100 %. La cyclisation des paraffines est bien moindre. Par exemple, pour produire du benzène à partir de stocks C6 et supérieurs, le méthylcyclopentane est isomérisé en cyclohexane et déshydrogéné en benzène. La conversion du n-hexane en benzène est limitée.
Les unités de reformage catalytique peuvent fonctionner à des pressions relativement élevées avec une série de réacteurs à lit fixe. Le catalyseur est régénéré à intervalles définis. Les unités conçues pour une conversion plus élevée fonctionnent à une pression plus basse avec une régénération du catalyseur plus fréquente. Des cycles plus courts, des réacteurs oscillants ou une régénération continue sont utilisés.
Le processus de plate-forme illustré à la figure 1 utilise une régénération continue du catalyseur.
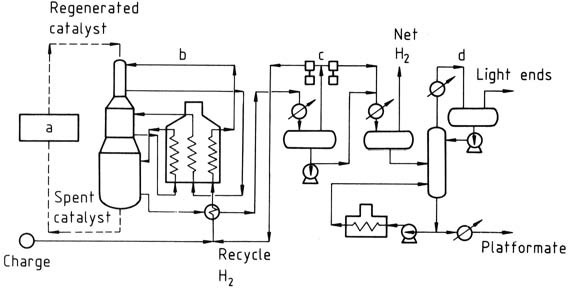
a) Régénération du catalyseur ; b) Réacteurs ; c) Séparation des produits ; d) Stabilisateur
Une autre conception développée par Standard Oil of Indiana utilise un réacteur oscillant dans lequel le catalyseur à lit fixe d’un réacteur est régénéré et remis en service, les catalyseurs de chacun des réacteurs restants étant régénérés en rotation. Des pressions manométriques de 0,7 à 2,4 MPa sont utilisées dans les différents processus.
Pour la production d’essence, on utilise des naphtas avec des plages d’ébullition d’environ 80 à 210 °C. Si le reformage est réalisé pour la production de charges aromatiques, la composition et l’intervalle d’ébullition du naphta peuvent être modifiés.
Le reformat peut avoir un indice d’octane clair RON allant jusqu’à 100 et peut contenir jusqu’à 70 % en volume d’aromatiques.
Au fil des années, le processus est devenu plus efficace. Les catalyseurs de reformage ont été modifiés. Il a été constaté que de petites quantités d’eau améliorent les rendements en benzène avec certains catalyseurs lors de la production de BTX. Des rendements plus élevés en xylène ont résulté d’un fonctionnement à des vitesses spatiales accrues.
2.2. Benzène issu de la pyrolyse de l’essence
L’essence de pyrolyse, un sous-produit de la production d’éthylène, est une autre bonne source de BTX. La quantité d’essence de pyrolyse produite dépend de la matière première et des conditions de fonctionnement. Elle est plus élevée avec les charges plus lourdes et peut aller jusqu’à 20 % pour le naphta de moyenne portée.
La composition de l’essence de pyrolyse varie en fonction du point d’ébullition de la charge, les charges plus lourdes produisant plus de toluène et de xylène que de benzène.
L’essence de pyrolyse contient > 60 % de BTX, mais elle contient également des insaturés et des dioléfines en raison de la température élevée nécessaire à la production d’éthylène. La teneur en dioléfines est généralement de 3 à 5 %, et la teneur totale en oléfines cycliques et en dioléfines cycliques est également de 3 à 5 %.
L’essence de pyrolyse est instable en raison de la matière dioléfinique. Les dioléfines à point d’ébullition inférieur peuvent être éliminées par distillation, mais cela peut être difficile en raison de leur tendance à polymériser et à dépolymériser. C’est pourquoi un procédé d’hydrotraitement en deux étapes est généralement utilisé.
La première étape convertit les dioléfines en oléfines. Si l’essence doit être utilisée comme carburant, un traitement supplémentaire peut ne pas être nécessaire. Toutefois, si l’essence est source d’aromatiques, une deuxième étape est utilisée pour saturer les oléfines et éliminer le soufre résiduel.
3. Autres méthodes de production de benzène
Pour répondre à la demande, la production de benzène peut être augmentée à partir d’autres composés aromatiques, tels que les fractions BTX obtenues à partir du reformat catalytique, de l’essence de pyrolyse ou des huiles légères issues de la carbonisation du charbon. Cela peut être réalisé en utilisant des procédés d’hydrodésalkylation, de dismutation ou de combinaison.
3.1. Production de benzène par hydrodésalkylation
L’hydrodésalkylation est un processus d’élimination des groupes alkyles des composés aromatiques à l’aide d’hydrogène. C’est une source de benzène et le toluène est le stock de charge habituel. Des composés aromatiques alkylés supérieurs peuvent également être utilisés, mais la réaction se déroule par étapes. D’autres alkylbenzènes, tels que l’éthylbenzène et le propylbenzène, se désalkylent en une seule étape et forment les alcanes correspondants.
Procédés catalytiques et thermiques
Des procédés catalytiques et thermiques sont utilisés pour l’hydrodésalkylation. Les procédés catalytiques, tels que Detol et Hydeal, fonctionnent entre 575 et 650 °C et entre 2,5 et 6 MPa. Les procédés thermiques, tels que HDA et THD, fonctionnent à des températures plus élevées que les procédés catalytiques, mais les rendements et les systèmes réactionnels sont similaires dans les deux types.
Processus de détol
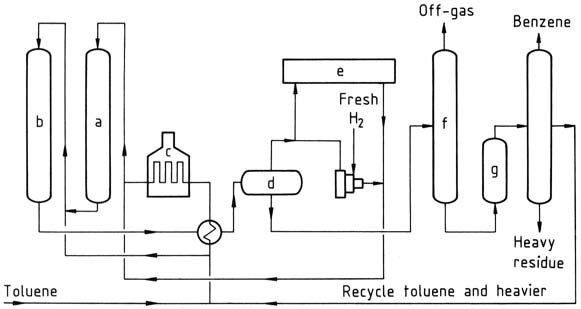
a) Réacteur I ; b) Réacteur II ; c) Fournaise ; d) Séparateur ; e) Purification de l'hydrogène ; f) Stabilisateur ; g) Traitement de l'argile
Le procédé Detol est un procédé de désalkylation catalytique qui utilise un catalyseur de désalkylation en lit fixe. La charge est constituée de toluène ou de mélanges de toluène et d’autres benzènes alkylés. Les aromatiques alkylés et l’hydrogène passent à température et pression élevées sur le catalyseur en série.
Les échangeurs de chaleur refroidissent les produits du réacteur et condensent le benzène, le toluène n’ayant pas réagi et les benzènes alkylés les plus lourds n’ayant pas réagi. Un ballon de flash haute pression sépare l’hydrogène recyclé et le gaz produit. Le gaz produit est divisé en flux pour le gaz combustible, pour la purification de l’hydrogène si nécessaire et pour le recyclage de l’hydrogène.
Le liquide du ballon flash est pompé vers un stabilisateur, où le gaz restant et les hydrocarbures à faible point d’ébullition sont évacués et utilisés comme gaz combustible. Les queues du stabilisant sont traitées avec de l’argile et envoyées vers une colonne où le benzène est distillé en tête.
Le toluène n’ayant pas réagi et les composés aromatiques plus lourds sont recyclés. Le benzène produit avec des rendements d’environ 99 % en moles est très pur, généralement 99,95 %, avec un point de congélation de 5,45 °C.
Processus hydéal
Le procédé Hydeal est un autre procédé de désalkylation catalytique. Il est similaire au procédé Detol, mais utilise à la place un catalyseur chrome-alumine. Le benzène de qualité nitration est obtenu avec des rendements d’env. 98 % en moles. La matière de charge aromatique n’ayant pas réagi provenant de l’opération à passage unique est recyclée pour obtenir une conversion pratiquement complète. Le procédé est également utilisé pour hydrodésalkyler les alkylnaphtalènes.
Processus HDA et THD
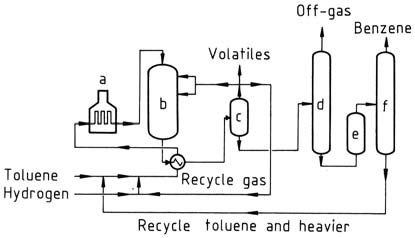
a) Chauffage ; b) Réacteur ; c) Séparateur ; d) Stabilisateur ; e) Traitement de l'argile ; f) Distillation
Les procédés HDA et THD sont des procédés de désalkylation thermique. Ils fonctionnent à des températures et des pressions plus élevées que les procédés catalytiques. Des rendements en benzène de 99 % en moles sont obtenus.
Processus CMH
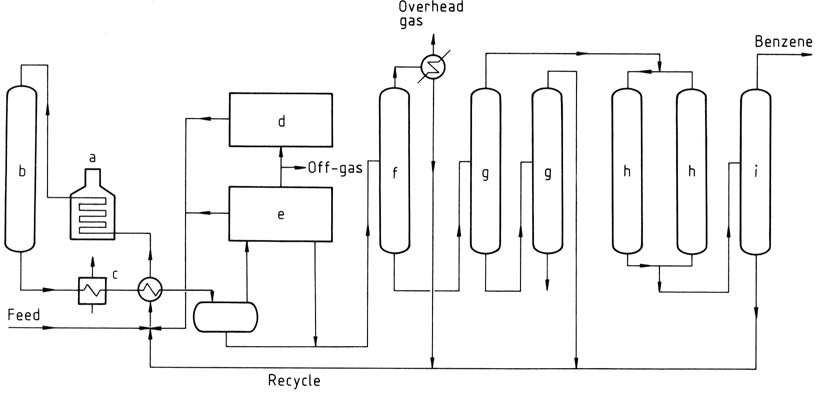
a) Chauffage ; b) Réacteur ; c) Chaudière à récupération de chaleur ; d) Régénération de l'hydrogène ; e) Récupération aromatique ; f) Fractionnement ; g) Colonnes à vide ; h) Traitement de l'argile ; i) Colonne Benzène
Le procédé MHC est un procédé de désalkylation thermique développé par Mitsubishi Petrochemical Co. Il peut traiter des matières premières contenant jusqu’à 30 % de matières non aromatiques sans recourir à des étapes d’extraction aromatique et de distillation fractionnée.
Le procédé fonctionnera avec de l’hydrogène de faible pureté, réduisant ainsi la quantité d’hydrogène d’appoint requise. Un benzène d’une pureté de 99,95 % est facilement obtenu.
3.2. Production de benzène par disproportion
Le procédé Tatoray est un moyen de fabriquer du benzène et des xylènes à partir de toluène et d’aromatiques en C9. Il utilise un catalyseur de métal noble ou de terre rare et recycle l’hydrogène pour faire fonctionner la réaction. Le processus fonctionne à 350-525 °C et 1-5 MPa.
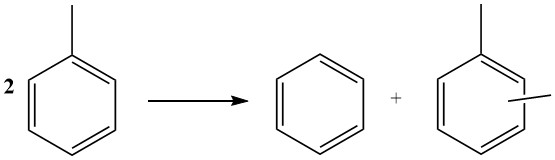
Le benzène produit est très pur et les xylènes contiennent très peu d’hydrocarbures saturés. Lorsque la matière première est limitée aux aromatiques en C9 et C10, le procédé produit un mélange de benzène, de toluène et de xylènes.
Le procédé Tatoray est utilisé dans un certain nombre d’usines commerciales à travers le monde. Le rendement en benzène et xylènes est d’environ 97 % lorsque le toluène est utilisé comme matière première.
3.3. Production de benzène par des procédés de désalkylation combinés
Plusieurs procédés ont été développés pour produire du benzène à partir de matières premières impures de BTX en combinant l’hydrogénation et la désalkylation.
Un exemple est le procédé Pyrotol, qui consiste à fractionner la charge pour éliminer les composés légers et lourds, à vaporiser la fraction C6-C8 et à la faire passer dans un réacteur catalytique pour hydrogéner sélectivement les dioléfines, les dioléfines cycliques et le styrène.
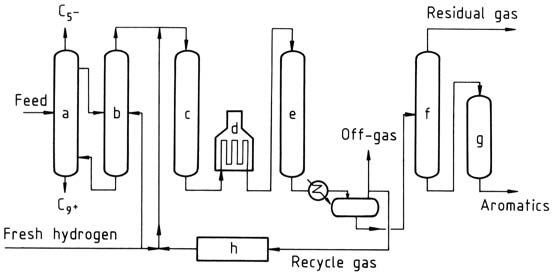
a) Distillation ; b) Vaporisateur ; c) Préréacteur ; d) Chauffage ; e) Réacteur pyrotol ; f) Stabilisateur ; g) Traitement de l'argile ; h) Purification de l'hydrogène
L’effluent du réacteur de prétraitement est ensuite chargé dans les réacteurs Pyrotol, où les aromatiques sont désalkylés en benzène. D’autres réactions incluent la désulfuration et l’hydrocraquage des produits non aromatiques. Le toluène n’ayant pas réagi et les composés aromatiques plus lourds sont recyclés. Le produit benzénique contient moins de 0,5 ppm de thiophène et a un point de congélation d’au moins 5,47 °C.
Un autre exemple est le procédé Litol, développé par la division Houdry d’Air Products et par Bethlehem Steel. Ce processus produit du benzène pur à partir d’huile légère aromatique obtenue par carbonisation du charbon. Il utilise deux étapes de réaction catalytique.
Après préfractionnement du pétrole léger brut pour éliminer les fractions C5 et plus légères en tête et C9 et plus lourdes en queue, la fraction C6-C8 est vaporisée. Dans un premier temps, les dioléfines et le styrène sont hydrogénés.
L’effluent entre ensuite en contact avec le catalyseur chrome-alumine Litol à 500-600 °C, où se produisent la désulfuration, l’hydrocraquage et la désalkylation. Une pureté de benzène de 99,97 % avec un point de congélation de 5,5 °C et une teneur en thiophène inférieure à 0,5 ppm sont typiques.
Un procédé a été développé par Mitsubishi Petrochemical Co. pour produire du benzène à partir d’essence de pyrolyse. Ce processus implique une hydrogénation en deux étapes suivie d’une extraction par solvant pour extraire les aromatiques, ou bien d’une réaction de la matière hydrogénée dans le procédé MHC de Mitsubishi.
Mobil Chemical Co. a développé un procédé de dismutation en phase liquide pour convertir le toluène en benzène et xylènes. Ce procédé de dismutation à basse température (LTD) utilise un catalyseur à base de zéolite hautement actif qui permet à la réaction de se dérouler à des températures aussi basses que 260 °C. Le recyclage de l’hydrogène n’est pas nécessaire dans ce procédé en phase liquide.
Référence
- Benzene; Ullmann’s Encyclopedia of Industrial Chemistry. – https://onlinelibrary.wiley.com/doi/10.1002/14356007.a03_475