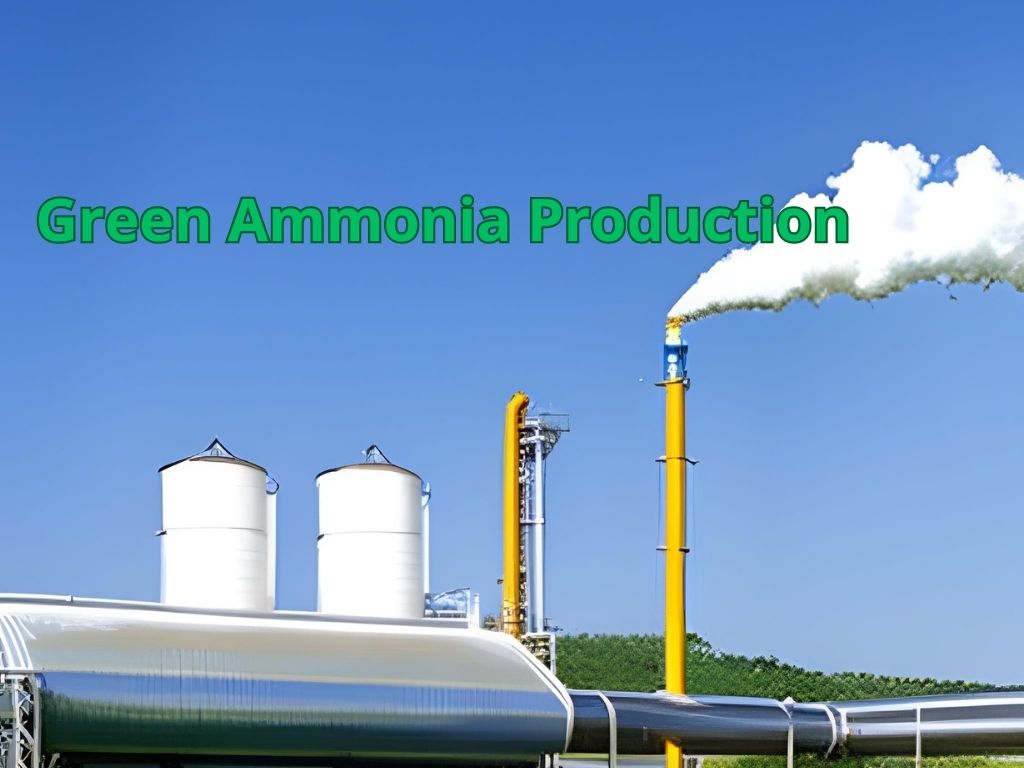
L’ammoniac vert est défini comme l’ammoniac synthétisé avec une empreinte carbone pratiquement nulle. L’ammoniac vert peut être produit en utilisant une technologie conventionnelle pour la boucle de synthèse d’ammoniac en combinaison avec une électrolyse à base d’hydrogène ou en utilisant des technologies non conventionnelles pour la synthèse d’ammoniac.
Table des matières
Avant la disponibilité du gaz naturel bon marché dans les années 1950 et au-delà, la synthèse d’ammoniac par électrolyse était l’une des technologies les plus largement utilisées, juste derrière la gazéification du charbon. Enfin, la production d’hydrogène à partir de biomasse avec CSC peut être considérée comme une alternative à la synthèse décentralisée d’ammoniac vert.
Le premier procédé Haber-Bosch basé sur l’électrolyse a démarré dans les années 1920, avec une consommation d’énergie d’environ 46 à 48 GJ/tNH3.
Quatre moteurs peuvent être identifiés pour la production d’ammoniac vert, à savoir la durabilité des réactifs, la faible consommation d’énergie, l’évolutivité modulaire et la viabilité économique.
L’énergie minimale théorique requise pour la synthèse d’ammoniac à partir de l’air et de l’eau est de 22,5 GJ/tNH3.
1. Production d’hydrogène par électrolyse
L’hydrogène vert est synthétisé par électrolyse. Diverses technologies d’électrolyse sont disponibles dans le commerce pour le couplage avec la synthèse d’ammoniac, telles que l’électrolyse alcaline et l’électrolyse à membrane échangeuse de protons (PEM). D’autres technologies sont au stade de la démonstration, comme l’électrolyse des oxydes solides (SOE). D’autres technologies font actuellement l’objet de recherches dans le milieu universitaire, telles que l’électrolyse à membrane échangeuse d’anions (AEM).
L’efficacité et le coût en capital dépendent de l’échelle d’application. Tous les systèmes commerciaux ont des réponses de charge de l’ordre de quelques secondes en mode veille à chaud, ce qui est nécessaire pour un couplage adéquat avec l’électricité renouvelable intermittente. Cependant, en veille froide, l’électrolyse PEM est la seule technologie capable d’accélérer les temps de l’ordre de quelques secondes.
Des combinaisons d’hydrogène à base d’électrolyse et d’hydrogène dérivé du méthane sont également possibles. Par exemple, une usine hybride avec un électrolyseur à oxyde solide et un reformeur autothermique (ATR) peut être bénéfique, car l’oxygène purifié est nécessaire pour l’ATR.
Un ATR fonctionne par combustion partielle de méthane avec de l’oxygène purifié, et est particulièrement intéressant pour la synthèse d’ammoniac à grande échelle en raison de la coûteuse usine de purification d’oxygène, qui n’est économique qu’à grande échelle.
Dans un électrolyseur à oxyde solide, de l’oxygène purifié est produit dans tous les cas, ce qui rend possible le reformage autothermique à plus petite échelle. On estime qu’une telle configuration permet d’économiser jusqu’à 22 % en termes de consommation de gaz naturel.
2. Production d’hydrogène à partir de la biomasse
La production d’hydrogène à partir de la biomasse est une alternative à la production d’hydrogène par électrolyse pour la synthèse d’ammoniac. Les installations typiques à base de biomasse sont limitées par la logistique (c’est-à-dire l’approvisionnement en biomasse), de sorte que les capacités des centrales sont généralement inférieures à 50 MW.
La mesure clé du coût de l’hydrogène est le coût de la biomasse, qui varie fortement selon le type de biomasse et l’emplacement. L’hydrogène à base de biomasse peut être produit par des procédés thermochimiques ou biochimiques.
Un avantage de la production d’hydrogène à base de biomasse est la compatibilité avec le procédé de production d’hydrogène brun conventionnel.
Les produits du traitement thermochimique ou biochimique de la biomasse sont la charge du réacteur SMR utilisé dans la synthèse de l’ammoniac brun. Un inconvénient de l’hydrogène à base de biomasse est le traitement complexe de la biomasse.
De plus, le potentiel technique de la biomasse pour satisfaire la demande en hydrogène est de plusieurs ordres de grandeur inférieur à celui des ressources électriques renouvelables telles que le solaire, l’énergie marémotrice et éolienne, en raison de la disponibilité limitée de la biomasse.
Les sources typiques de biomasse sont la bagasse, les cultures, la paille, le panic raide, le bois et les copeaux de bois. Les produits typiques sont le biogaz, la bio-huile et le biochar. Une alternative aux matières premières de la biomasse naturelle est l’utilisation des déchets municipaux.
Un exemple de processus de transformation des déchets en ammoniac est l’utilisation de plastique recyclé, comme c’est le cas au Japon à des fins de réduction catalytique sélective.
Le biogaz issu de la biomasse peut être combiné avec de l’électricité renouvelable. Un exemple d’un tel système est la digestion anaérobie pour la production de biogaz couplée à des réacteurs tubulaires électrifiés de reformage à la vapeur. Une autre alternative est la combinaison d’un réacteur à biogaz avec un électrolyseur à oxyde solide et un ATR.
3. Production d’azote
L’azote gazeux purifié est produit à partir de l’air par diverses technologies, à savoir une unité de séparation de l’air (ASU, distillation cryogénique), une adsorption modulée en pression (PSA), une perméation membranaire et une combustion d’hydrogène.
Dans le SMR, la séparation de l’air est généralement intégrée à la production d’hydrogène, et l’oxygène est brûlé avec une partie de l’hydrogène. De même, la combustion d’hydrogène peut être utilisée dans un électrolyseur à oxyde solide pour générer la chaleur nécessaire à la production d’hydrogène à partir d’eau.
Les trois autres technologies peuvent être utilisées en combinaison avec des électrolyseurs alcalins ou PEM, dans lesquels l’azote et l’hydrogène sont produits dans des unités séparées.
L’alternative préférée dépend de la pureté de l’azote et de l’échelle d’application. Pour le PSA et la perméation membranaire, un système deoxo est nécessaire pour éliminer l’oxygène résiduel.
L’oxygène est éliminé par combustion catalytique avec de l’hydrogène, après quoi l’eau est éliminée dans un sécheur régénératif. L’oxygène doit être éliminé avant la boucle de synthèse, car les composés oxygénés sont néfastes pour le catalyseur de synthèse d’ammoniac.
4. Boucle de synthèse d’ammoniac
En principe, la boucle de synthèse de l’ammoniac n’est pas modifiée par la source d’hydrogène et d’azote, bien que les niveaux d’impuretés puissent changer. En principe, le choix du catalyseur a peu d’influence sur le rendement de fonctionnement de la boucle de synthèse. Cependant, les températures et pressions de fonctionnement varient en fonction du choix du catalyseur. Ceci est particulièrement pertinent en cas de fonctionnement à échelle réduite et intermittent avec des énergies renouvelables, car des conditions de fonctionnement plus douces entraînent moins de pertes de chaleur avec un degré décroissant d’intégration de la chaleur.
De plus, la production d’hydrogène vert implique différents flux de chaleur et de masse dans le processus, qui nécessitent différents schémas d’intégration de la chaleur. Divers catalyseurs sont souvent combinés dans un même réacteur avec des lits différents.
5. Aspects économiques de la production d’ammoniac vert
A titre de comparaison, une usine à base de biogaz d’une capacité de 22,5 tNH3/j a un coût d’investissement d’environ 14,4 M€. Une usine à base de SMR d’une capacité de 1800 tNH3/j a un coût d’investissement d’environ 199 M€.
Les coûts d’exploitation d’un procédé Haber-Bosch basé sur l’électrolyse peuvent être divisés en coûts d’électricité et coûts du propriétaire. Environ 75 à 95% de l’électricité est nécessaire pour l’électrolyseur dans un procédé Haber-Bosch basé sur l’électrolyse à grande échelle. La consommation et le coût de l’électricité dépendent de l’échelle et de l’emplacement de l’usine. Les coûts du propriétaire sont d’environ 120 k€ a–1 tpj–1 pour une usine de 3 tNH3/j.
La production d’hydrogène est le principal facteur de coût pour la synthèse d’ammoniac. Selon le lieu, différentes alternatives peuvent être envisagées. L’hydrogène brun produit par SMR coûte 845–1585 €/t (hors CCS, les coûts augmentent à 1305–2145 €/t avec CCS).
D’autre part, le coût de l’hydrogène renouvelable basé sur l’électrolyse varie de moins de 1440 €/t à plus de 3605 €/t, en fonction des heures de charge solaire et éolienne cumulées à un endroit donné. Le SMR électrifié peut être intéressant lorsque le coût de l’électricité est inférieur à 15-25 €/MWh, en fonction du coût du gaz naturel à un endroit donné. Par rapport à l’électrolyse, un avantage de l’eSMR est la compatibilité avec les usines SMR existantes pour la production d’hydrogène et l’investissement en capital inférieur.
L’ammoniac à base de biomasse avec traitement thermochimique coûte de 380 à 1875 €/t, selon l’échelle d’application, la source de la biomasse et l’emplacement. Le coût de l’ammoniac produit à partir des déchets municipaux s’élève à 2135 €/t.
Référence
- Ammonia, 4. Green Ammonia Production, Ullmann’s Encyclopedia of Industrial Chemistry. – https://onlinelibrary.wiley.com/doi/10.1002/14356007.w02_w02