Acetylen wird auf verschiedene Weise hergestellt: Calciumcarbid-Reaktion, Teilverbrennung von Kohlenwasserstoffen, Lichtbogenprozesse, thermisches Cracken mit Wärmeträgern und als Nebenprodukt des Dampfcrackens.
1. Calciumcarbid-Reaktion:
- Diese traditionelle Methode beinhaltet die Reaktion von Calciumcarbid mit Wasser, wodurch sowohl Acetylen als auch Calciumhydroxid entstehen.
- Es ist ein einfacher und gut etablierter Prozess, aber die Herstellung von Calciumcarbid erfordert einen hohen Energiebedarf und ist umweltbedenklich.
2. Teilweise Verbrennung von Kohlenwasserstoffen:
- Diese Methode nutzt die partielle Oxidation von Erdgas, Methan oder schwereren Kohlenwasserstoffen wie Naphtha und Vakuumgasöl in einem Brenner, um vor Ort Acetylen zu erzeugen.
- Es bietet Flexibilität bei der Auswahl des Ausgangsmaterials und möglicherweise eine höhere Effizienz im Vergleich zu Calciumcarbid, aber eine präzise Kontrolle der Reaktionsbedingungen ist entscheidend.
3. Lichtbogenprozesse:
- Diese Prozesse spalten Kohlenwasserstoffe mithilfe von Hochtemperatur-Lichtbögen und treiben so direkt die endotherme Acetylensynthesereaktion an.
- Sie bieten Unabhängigkeit von der Art des Kohlenwasserstoff-Ausgangsmaterials und möglicherweise einen geringeren Kohlenwasserstoffverbrauch im Vergleich zur Teilverbrennung, erfordern jedoch hochwertige Elektrizität und ein komplexes Lichtbogenreaktordesign.
4. Thermisches Cracken mit Wärmeträgern:
- Diese Methode nutzt die indirekte Wärmeübertragung durch verschiedene Wärmeträger wie feuerfeste Materialien oder heiße Verbrennungsgase, um Ausgangsmaterialien zu cracken.
- Während ältere Verfahren wie Wulff und Hoechst HTP mit Einschränkungen konfrontiert waren, erweisen sich neuere Weiterentwicklungen wie die ACR- und Dow PCC-Verfahren als vielversprechend bei der Handhabung schwererer Beschickungen und beim Erreichen eines effizienten Crackens für die Acetylenproduktion.
5. Nebenprodukt des Dampfcrackens:
- Dampfcracken zur Olefinproduktion wie Ethylen erzeugt auf natürliche Weise Acetylen als Nebenprodukt.
- Diese Quelle kann durch die Implementierung von Acetylenentfernungstechniken wie katalytischer Hydrierung oder Lösungsmittelextraktion zur Rückgewinnung von hochreinem Acetylen erschlossen werden.
1. Thermodynamische und kinetische Aspekte
Hohe Temperaturen und schnelle Reaktionszeiten sind für die Acetylenproduktion aus Kohlenwasserstoffen unerlässlich. Dies liegt an den folgenden Aspekten:
- Thermodynamische Einschränkungen: Bei Standardtemperaturen ist Acetylen im Vergleich zu anderen Kohlenwasserstoffen instabil (hohes ΔHf und ΔGf). Oberhalb von ~1230 °C wird Acetylen jedoch thermodynamisch bevorzugt, wobei sich der Schnittpunkt in ΔGf-Diagrammen mit abnehmender Kohlenwasserstoffkettenlänge nach links verschiebt (Methan erfordert die höchste Temperatur).
- Kinetische Überlegungen: Selbst bei diesen hohen Temperaturen bleibt Acetylen weniger stabil als seine elementaren Bestandteile (C und H). Diese thermodynamische Bevorzugung der Zersetzung erfordert ein schnelles Abschrecken des entstehenden Acetylens (Verweilzeiten ~0,1–10 ms), um seinen Zerfall zu verhindern.
- Konkurrierende Reaktionen: Neben der Bildung von Acetylen finden auch das Cracken und die Rekombination der Ausgangskohlenwasserstoffe sowie die weitere Umwandlung von Acetylen in Nebenprodukte statt. Kurze Verweilzeiten sind entscheidend, um diese konkurrierenden Reaktionen zu minimieren und die Acetylenausbeute zu maximieren.
Partielle Oxidation bietet einen alternativen Weg, bei dem durch die Verbrennung eines Teils des Kohlenwasserstoffs aus dem verbleibenden Teil die für die Acetylenproduktion benötigte Wärme erzeugt wird. Eine genaue Steuerung des Methan-Sauerstoff-Verhältnisses ist wichtig, um die gewünschte Reaktionstemperatur zu erreichen und die Acetylenausbeute zu optimieren.
Zusammenfassend lässt sich sagen, dass eine erfolgreiche Acetylenproduktion aus Kohlenwasserstoffen die Überwindung thermodynamischer Einschränkungen durch hohe Temperaturen in Kombination mit schnellem Abschrecken und präziser Reaktionssteuerung erfordert, um konkurrierende und unerwünschte Reaktionen zu minimieren.
2. Acetylenproduktion durch Teilverbrennungsprozesse
Teilverbrennungsprozesse nutzen die Wärmeerzeugung vor Ort durch teilweise Oxidation eines Teils des Ausgangsmaterials, um die Acetylensynthese aus dem verbleibenden Teil voranzutreiben.
Diese Methode ermöglicht die Verwendung verschiedener Rohstoffe, von Methan und Ethan bis hin zu schwereren Fraktionen wie Naphtha und Vakuumgasöl. Erdgas eignet sich aufgrund seiner weiten Verfügbarkeit als besonders geeigneter Rohstoff.
Prozessbeschreibung
Bei diesem Verfahren werden sowohl das Ausgangsmaterial als auch der Sauerstoff getrennt vorgewärmt, um eine optimale Leistung zu erzielen. Die vorgewärmten Ströme gelangen in einen Brenner, wo sie sich innerhalb einer Reaktionszone vermischen und entzünden. Das Produktgemisch verlässt die Reaktionszone und wird schnell abgekühlt, typischerweise mit Wasser oder Öl, um unerwünschte Zersetzung zu verhindern.
Eine effiziente Acetylenbildung erfordert eine kurze und gleichmäßige Verweilzeit des Gases in der Reaktionszone, typischerweise einige Millisekunden. Die präzise Steuerung der Strömungsgeschwindigkeit gleicht eine hohe Ausbeute mit der Vermeidung von Vorentflammung, Flammeninstabilität und Koksablagerung aus.
Beispiele für Industrieanlagen sind:
- Das BASF-Verfahren ist das am weitesten verbreitete Teilverbrennungsverfahren für Erdgas mit Tauchbrennern und effizienter Wärmerückgewinnung.
- Submerged Flame Process (SFP) ist ein für Schwerölfraktionen konzipiertes Verfahren, das sich durch einfaches Cracken, gleichzeitige Acetylen-Ethylen-Produktion und einen hohen thermischen Wirkungsgrad auszeichnet.
- Partial Combustion Carbide Process ist ein Verfahren im Pilotanlagenmaßstab unter Verwendung von Koks, Sauerstoff und Kalk und bietet potenzielle zukünftige Vorteile wie eine hohe Kohlenstoffumwandlung und thermische Effizienz für die kohlebasierte Acetylenproduktion.
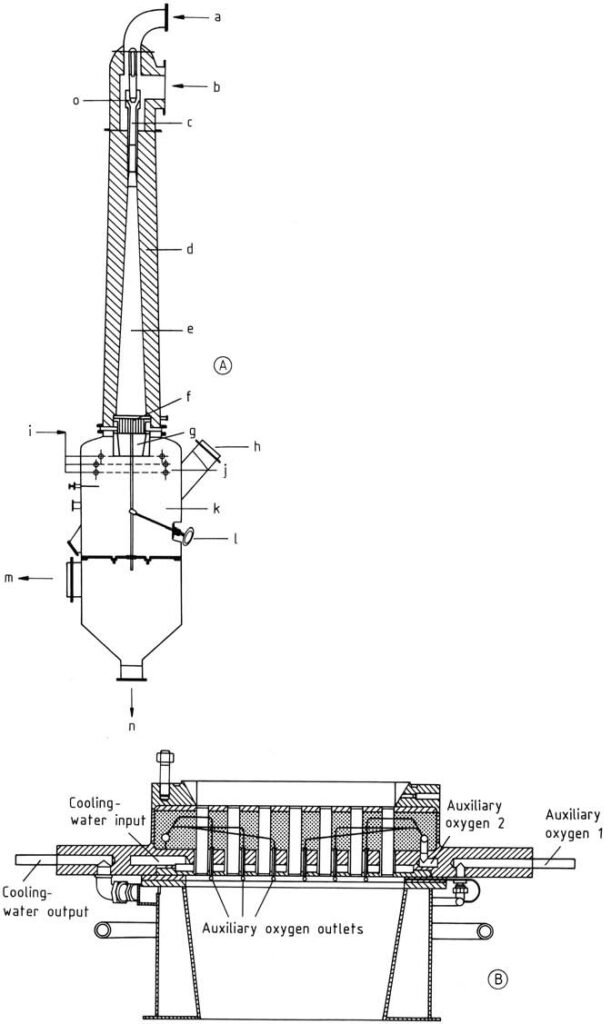
A) Der Brenner: a) Sauerstoff: b) Kohlenwasserstoff; c) Mischer; d) Betonauskleidung; e) Diffusor; f) Brennerblock; g) Reaktionskammer; h) Berstscheibe; i) Quenchmedium-Einlass; j) Quenchringe; k) Abschreckkammer; l) Manueller Schaber; m) Spaltgasauslass; n) Quenchmedium-Auslass. B) Der Brennerblock
Teilverbrennungsprozesse zielen zwar hauptsächlich auf Acetylen ab, erzeugen aber auch Nebenprodukte wie Wasserstoff und Kohlenmonoxid. In einer komplexen Chemieanlage können diese Nebenprodukte in wertvolle Produkte wie Synthesegas, reinen Wasserstoff und Kohlenmonoxid umgewandelt werden, was letztendlich die Gesamtwirtschaftlichkeit des Prozesses erhöht.
- Für eine detailliertere Beschreibung dieser industriellen Prozesse wenden Sie sich bitte an Sie kann auf die Referenz am Ende dieses Artikels verweisen.
3. Acetylenproduktion durch elektrothermische Prozesse
Elektrothermische Prozesse nutzen im Gegensatz zur partiellen Oxidation die Lichtbogentechnologie, um die Acetylensynthese zu erreichen. Diese Methode bietet mehrere Vorteile:
- Rohstoffunabhängigkeit: Die für die Acetylenbildung erforderliche Energie ist vom spezifischen Kohlenwasserstoff-Rohstoff entkoppelt.
- Reduzierter Kohlenwasserstoffverbrauch: Im Vergleich zur partiellen Oxidation können elektrothermische Prozesse den Kohlenwasserstoffverbrauch um bis zu 50 % senken.
- Günstige wirtschaftliche Aspekte: Unter günstigen Bedingungen wie Zugang zu billigem Strom (Kernkraft, Wasserkraft, Kohle) oder begrenzter Verfügbarkeit von Kohlenwasserstoffen können elektrothermische Prozesse möglich sein wirtschaftlicher.
Unter den elektrothermischen Optionen zeichnet sich das Lichtbogenverfahren durch seine Eignung aus, die stark endotherme Hochtemperatur-Acetylensynthesereaktion voranzutreiben. Es wurde 1925 in Deutschland für die Butadien-Produktion entwickelt, das Lichtbogenverfahren zur Acetylensynthese wurde erstmals kommerzialisiert 1940 bei den Chemischen Werken Hüls.
Als Ausgangsstoffe für Lichtbogenprozesse können sowohl gasförmige als auch flüssige Kohlenwasserstoffe sowie Feststoffe wie Kohle dienen. Das Design des Lichtbogenofens und die Produktreinigungsschritte werden auf das spezifische Ausgangsmaterial zugeschnitten.
Gasförmige/vergaste Beschickungen verwenden typischerweise einen einstufigen Prozess, bei dem der Lichtbogen das Crackgas direkt erhitzt. Flüssige und feste Beschickungen können einen zweistufigen Prozess nutzen, bei dem der im Lichtbogenofen vorgewärmte Wasserstoff als Plasmamedium für die Beschickungsinjektion fungiert.
Der beim Cracken entstehende Wasserstoff erzeugt bei beiden Prozessarten eine Wasserstoffatmosphäre für den Lichtbogen. Aufgrund der hohen Leitfähigkeit und Ionen-Elektronen-Rekombinationsrate von Wasserstoff erfordern Lichtbogenlängen, die einen bestimmten Schwellenwert überschreiten, einen Gleichstrombetrieb (DC) bei Standardfrequenzen und hohen Spannungen. Folglich sind alle kommerziellen Lichtbogen-Acetylenanlagen auf Gleichstrom angewiesen.
Beispiele für industrielle elektrothermische Prozesse sind:
- Herstellung aus gasförmigen und/oder vergasten Kohlenwasserstoffen (Hüls-Lichtbogenverfahren)
- Herstellung aus flüssigen Kohlenwasserstoffen (Plasma-Lichtbogen-Verfahren)
- Produktion aus Kohle (Arc Coal Process)
- Herstellung aus Calciumcarbid
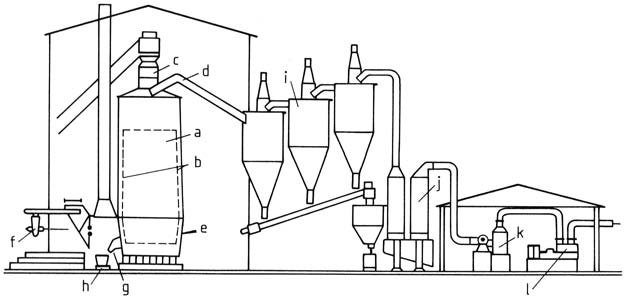
a) Karbidofen; b) Feuerfeste Ziegelauskleidung; c) Einfülltrichter; d) Gasauslass; e) Sauerstoffstrahl; f) Anstichbrenner; g) Zapfrutsche; h) Bogey; i) Zyklon; j) Waschkolonne; k) Desintegrator; l) Kompressor
- Für eine detailliertere Beschreibung dieser industriellen Prozesse wenden Sie sich bitte an Sie kann auf die Referenz am Ende dieses Artikels verweisen.
4. Herstellung von Acetylen durch andere Crackverfahren
4.1. Thermisches Cracken durch Wärmeträger
Thermisches Cracken mit Wärmeträgern bietet einen alternativen Weg zur Acetylenproduktion, der sich von der partiellen Oxidation und den Lichtbogenmethoden unterscheidet. Ältere Verfahren wie das HTP von Wulff und Hoechst wurden jedoch durch Einschränkungen wie Rohstoffbeschränkungen (raffiniertes Naphtha und LPG) und Rußbildung behindert, was letztendlich zu ihrer Einstellung führte.
Beispiele für neue Technologien, die das alte Wulff- und Hoechst-HTP-Verfahren ersetzen, sind:
- Kureha, Chiyoda, Union Carbide ACR-Prozess: Bei diesem Pilotprozess wird überhitzter Dampf als Wärmeträger bei 2000 °C erzeugt durch Verbrennung von H2-CH4-Gemischen mit Sauerstoff. Rohöl-Ausgangsmaterial wird in einem Mehrkanalreaktor schnell gecrackt, wodurch hohe Wasserstoff-, Olefin- und Acetylenausbeuten erzielt werden (4,2 Gew.-%, deutlich höher als bei herkömmlichen Olefinverfahren).
- Dow Partial Combustion Cracking (PCC)-Prozess: Dieser Prozess behebt Verkokungs- und Rußprobleme durch teilweise Oxidation von recyceltem Abschrecköl (vom Cracken). Der Brenner erzeugt Synthesegas und hält einen hohen Wasserstoffpartialdruck in der Reaktionszone aufrecht. Während schwerere Einsatzstoffe wie Rohöl und Rückstände akzeptiert werden, ist die Acetylenausbeute (2,5 Gew.-%) aufgrund der längeren Verweilzeiten (3-10x länger) geringer als beim ACR-Verfahren.
Die folgende Tabelle bietet einen Vergleich der Merkmale dieser Prozesse:
Funktion | Wulff & Hoechst HTP | ACR | Dow PCC |
---|---|---|---|
Rohstoff | Raffiniertes Naphtha, LPG | Rohöl | Rohöl, schwere Rückstände |
Wärmeträger | Feuerfestes Material, heiße Verbrennungsgase | Überhitzter Dampf (2000°C) | Synthesegas aus der partiellen Oxidation von Quenchöl |
Acetylen-Ausbeute | Begrenzt | Hoch (4,2 Gew.%) | Mäßig (2,5 Gew.%) |
Vorteile | Indirekte Wärmeübertragung, hoher thermischer Wirkungsgrad | Rohölkompatibilität, hohe Olefinausbeute | Schwere Beschickungskapazität, hohe Wasserstoffrückgewinnung |
Nachteile | Rußbildung, Naphtha/LPG-Einschränkung | Pilotmaßstab, komplexer Brenner | Geringere Acetylenausbeute, längere Verweilzeit |
4.2. Acetylen als Nebenprodukt beim Dampfcracken
Dampfcracken erzeugt die gewünschten Olefine wie Ethylen und Propen, erzeugt aber auch verschiedene Nebenprodukte, einschließlich Acetylen. Seine Konzentration hängt ab von:
- Rohstoff: Verschiedene Kohlenwasserstoffe ergeben unterschiedliche Acetylenwerte.
- Verweilzeit: Längere Crackdauern erhöhen die Acetylenbildung.
- Rissschwere: Höhere Rissschwere (Umwandlung oder KGV) führt zu mehr Acetylen.
Typische Acetylenkonzentrationen im Abgas liegen zwischen 0,25 und 1,35 Gew.-%, wobei in bestimmten Fällen bis zu 2,1 Gew.-% erreicht werden. Die C2-Fraktion enthält typischerweise 0,4–2,5 Gew.-% Acetylen. Eine 400.000 t/a-Ethylenanlage erzeugt 4.500–11.000 t/a Acetylen.
Um Acetylen zu entfernen, nutzen die meisten Ethylenanlagen entweder katalytische selektive Hydrierung, die vorherrschende Methode zur Umwandlung von Acetylen in Ethylen an Pd-dotierten Katalysatoren, oder Lösungsmittelextraktion unter Verwendung von DMF für die Rückgewinnung von hochreinem Acetylen.
Über 112.000 t/a petrochemisches Acetylen wurden 2006 weltweit als Nebenprodukt zurückgewonnen. Der gesamte Acetylenmarkt ging jedoch aufgrund verschiedener Faktoren zurück, was zu einer begrenzten Anzahl neuer Acetylenrückgewinnungsanlagen führte Installationen in den letzten Jahren.
Petrochemisches Acetylen bleibt auch bei verdoppelten Ethylenpreisen wirtschaftlich attraktiv. Die Nachrüstung bestehender Olefinanlagen mit Acetylenabsorption und -extraktion aus unvermeidbarem Nebenprodukt Acetylen bleibt der praktikabelste Weg zur Deckung des Acetylenbedarfs.
Referenz
- Acetylen; Ullmanns Enzyklopädie der industriellen Chemie. – https://onlinelibrary.wiley.com/doi/10.1002/14356007.a01_097.pub4