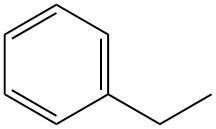
Was ist Ethylbenzol?
Ethylbenzol, auch bekannt als Phenylethan, ist ein einringiger alkylaromatischer Kohlenwasserstoff mit der Formel C8H10. Es ist eine leicht entzündliche, farblose Flüssigkeit mit einem charakteristischen aromatischen Geruch.
Es wird hauptsächlich (> 99 %) als Zwischenprodukt bei der Herstellung von Styrolmonomer verwendet, einer der weltweit bedeutendsten Massenchemikalien.
Die großtechnische Produktion von Ethylbenzol begann in den 1930er Jahren durch Dow Chemical (USA) und BASF (Deutschland). Die Ethylbenzol-/Styrolindustrie blieb bis zum Zweiten Weltkrieg relativ unbedeutend.
Der Anstieg der Nachfrage nach synthetischem Styrol-Butadien-Kautschuk (SBR) während der Kriegsjahre beschleunigte den schnellen technologischen Fortschritt und die erhebliche Kapazitätserweiterung. Diese Kriegsanstrengungen führten zum Bau zahlreicher Großfabriken, und die Styrolproduktion entwickelte sich rasch zu einer bedeutenden Industrie.
Bis 1999 lag die weltweite jährliche Produktionskapazität für Ethylbenzol bei fast 25 Millionen Tonnen. Besonders hervorzuheben ist, dass die 1990er Jahre den größten Kapazitätszuwachs in den fernöstlichen Ländern (ohne Japan) verzeichneten, wo die grundlegenden petrochemischen Industrien eine erhebliche Entwicklung und Expansion erlebten.
Inhaltsverzeichnis
1. Physikalische Eigenschaften von Ethylbenzol
Unter normalen Bedingungen ist Ethylbenzol eine farblose Flüssigkeit mit aromatischem Geruch. Es ist wasserunlöslich, jedoch in jedem Verhältnis löslich in Ethanol und Ethylether. Ethylbenzol reizt Haut und Augen und ist bei Einnahme, Einatmen und Hautabsorption mäßig giftig.
Einige physikalische Eigenschaften von Ethylbenzol sind in der folgenden Tabelle aufgeführt.
Eigenschaft | Wert |
---|---|
CAS-Nummer | [100-41-4] |
Chemische Formel | C6H5CH2CH3 |
Molekularmasse | 106,168 g/mol |
Dichte |
|
Schmelzpunkt | -94,949 °C |
Siedepunkt (101,3 kPa) | 136,2 °C |
Brechungsindex |
|
Dampfdichte | 3,66 |
Kritischer Druck | 3609 kPa (36,09 bar) |
Kritische Temperatur | 344,02 °C |
Flammpunkt (geschlossener Tiegel) | 15 °C |
Selbstentzündungstemperatur | 460 °C |
Entzündbarkeitsgrenze |
|
Latentwärme |
|
Heizwert |
|
Kinematisch Viskosität |
|
Oberflächenspannung | 28,48 mN/m |
Spezifische Wärmekapazität |
|
Azentrischer Faktor | 0,3026 |
Kritische Kompressibilität | 0,263 |
2. Chemische Reaktionen von Ethylbenzol
Die bedeutendste kommerzielle Reaktion von Ethylbenzol ist seine Dehydrierung zu Styrol. Diese Reaktion findet bei hohen Temperaturen (600–660 °C) statt und verwendet typischerweise einen kaliumhaltigen Eisenoxidkatalysator mit Dampf als Verdünnungsmittel.
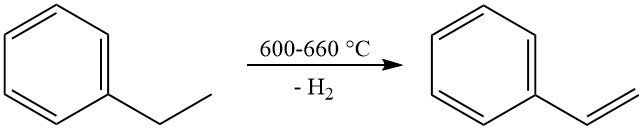
Bei der industriellen Produktion werden Styrol-Selektivitäten von 90 bis 97 Mol-% bei Umsätzen pro Durchgang von 60–70 % erreicht. Die wichtigste Nebenreaktion ist die Dealkylierung von Ethylbenzol zu Benzol und Toluol.
Eine weitere Reaktion, die zunehmend an kommerzieller Bedeutung gewinnt, ist die Luftoxidation von Ethylbenzol zu Ethylbenzolhydroperoxid. Dies ist ein unkatalysierter Prozess, der in der flüssigen Phase stattfindet. Aufgrund der inhärenten Instabilität von Hydroperoxiden muss die Einwirkung hoher Temperaturen jedoch minimiert werden, um die Zersetzungsrate zu verringern.
Das Hydroperoxid wird anschließend mit Propylen behandelt, um gleichzeitig Styrol und Propylenoxid herzustellen. 1999 wurden etwa 15 % der weltweiten Ethylbenzolproduktion auf diesem Weg zur gleichzeitigen Herstellung von Styrolmonomer und Propylenoxid eingesetzt.

Ähnlich wie Toluol kann Ethylbenzol durch katalytische oder thermische Prozesse zu Benzol dealkyliert werden. Außerdem durchläuft Ethylbenzol verschiedene andere Reaktionen, die für alkylaromatische Verbindungen charakteristisch sind, wie Alkylierung, Acylierung, Nitrierung und Sulfonierung.
3. Industrielle Produktion von Ethylbenzol
Historisch gesehen war über mehrere Jahrzehnte die Friedel-Crafts-Alkylierung von Benzol mit Ethylen unter Verwendung gelöster Lewis-Säuren, hauptsächlich Aluminiumchlorid, als Katalysatoren in der Flüssigphase die vorherrschende Methode zur Ethylbenzolproduktion. Diese Methode wird noch immer für etwa 40 % der weltweiten Ethylbenzolproduktion verwendet.
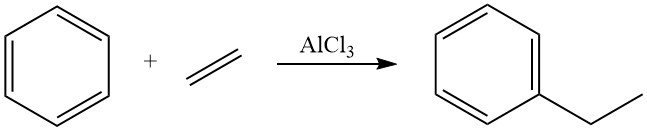
Obwohl die Aluminiumchlorid-Methode wirtschaftlich konkurrenzfähig sein kann, erzeugt dieser Prozess Abfallströme, deren Entsorgung aufgrund von Umweltvorschriften immer teurer wird. Außerdem ist Aluminiumchlorid hochgradig korrosiv, was zu einem erheblichen Wartungsbedarf für Geräte und Rohrleitungen führt.
Seit Anfang der 1980er Jahre sind heterogene Zeolithkatalysatoren die bevorzugte Technologie für neue Ethylbenzol-Produktionsanlagen. Die ursprüngliche Zeolithtechnologie arbeitete in der Dampfphase, was im Vergleich zu flüssigphasigem Aluminiumchlorid eine verbesserte Prozesseffizienz bot.
In jüngerer Zeit wurden flüssigphasige Zeolithprozesse entwickelt, die zusätzliche Flexibilität bieten. Diese Technologie erzeugt im Vergleich zum Aluminiumchlorid-Verfahren weniger gefährliche Abfälle.
Steigende Umweltbedenken und Fortschritte in der Zeolithtechnologie haben viele Hersteller, die Aluminiumchloridanlagen verwenden, dazu veranlasst, ihre Anlagen mit Zeolithtechnologie nachzurüsten. Zwischen 1997 und 1999 wurden etwa 106 Tonnen Kapazität von Aluminiumchlorid- auf Zeolithprozesse umgestellt.
Ab dem Jahr 2000 befanden sich weitere Umbauten in der Planungsphase, und der Bau neuer Anlagen mit Aluminiumchlorid-Technologie wurde im letzten Jahrzehnt praktisch eingestellt.
Einige Anlagen produzieren eine geringe Menge Ethylbenzol durch Superfraktionierung gemischter C8-Aromatenströme.
3.1. Ethylbenzolproduktion mit Aluminiumchlorid und anderen Lewis-Säure-Katalyseverfahren
Mehrere Jahrzehnte lang dominierten Flüssigphasen-Aluminiumchlorid-Prozesse die Ethylbenzolproduktion. Mehrere Unternehmen, darunter Dow, BASF, Shell und Monsanto, entwickelten Varianten dieser Technologie. Heute werden noch etwa 40 % der weltweiten Ethylbenzolproduktion mit AlCl3 durchgeführt.
Die Alkylierung von Benzol mit Ethylen ist stark exotherm und setzt eine erhebliche Wärmemenge frei (ΔH = -114 kJ/mol). Die Verwendung von Aluminiumchlorid als Katalysator in dieser Reaktion fördert eine schnelle Reaktion mit nahezu stöchiometrischen Ausbeuten an Ethylbenzol.
Andere Lewis-Säuren wie AlBr3, FeCl3, ZrCl4 und BF3 können ebenfalls eingesetzt werden. Verfahren mit AlCl3 enthalten häufig Promotoren wie Ethylchlorid oder Chlorwasserstoff. Diese Promotoren reduzieren die für die Reaktion benötigte Menge an AlCl3.
Das herkömmliche AlCl3-Verfahren (Abbildung 1) verwendet drei Phasen im Reaktor: aromatische Flüssigkeit (Benzol), Ethylengas und eine rote Ölkatalysatorkomplexphase. Die Reaktion findet nahe dem thermodynamischen Gleichgewicht statt und erfordert einen einzigen Reaktor sowohl für die Alkylierung als auch für die Transalkylierung.
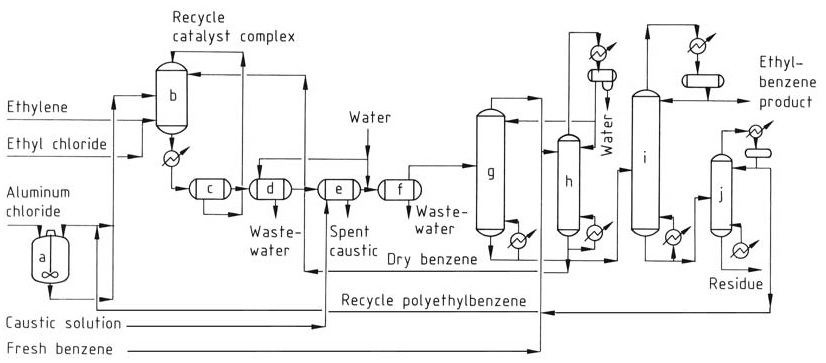
a) Katalysatormischtank; b) Alkylierungsreaktor; c) Absetzbehälter; d) Säureabscheider; e) Laugenabscheider; f) Wasserabscheider; g) Benzolrückgewinnungssäule; h) Benzol-Dehydratationssäule; i) Ethylbenzolrückgewinnungssäule; j) Polyethylbenzolsäule
Die Katalysatorkomplexmischung, trockenes Benzol und recycelte Polyalkylbenzole werden kontinuierlich in den Reaktor eingespeist. Ethylen und ein Katalysatorpromotor (z. B. Ethylchlorid) werden in die Reaktionsmischung eingespritzt.
Die Betriebstemperaturen sind auf 130 °C begrenzt, um eine Katalysatordeaktivierung und Nebenproduktbildung zu verhindern, und es wird ausreichend Druck aufrechterhalten, um die Reaktanten in der flüssigen Phase zu halten.
Das verbesserte Monsanto-Verfahren (Abbildung 2) bietet Vorteile gegenüber herkömmlichen AlCl3-Verfahren und wurde in vielen älteren Anlagen implementiert.
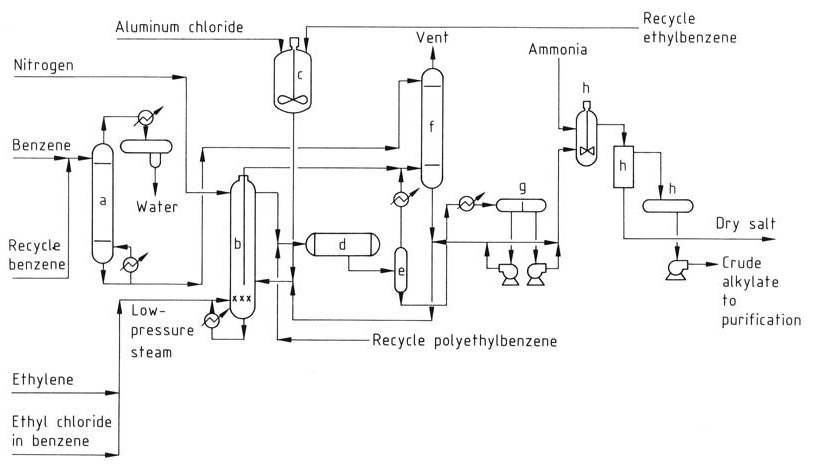
a) Benzoltrocknungskolonne; b) Alkylierungsreaktor; c) Katalysatorherstellungstank; d) Transalkylator; e) Entspannungstrommel; f) Abgaswaschsystem; g) Dekantierbehälter; h) Neutralisationssystem
Dieser Prozess läuft bei höheren Temperaturen (160–180 °C) ab und verwendet eine homogene Flüssigphase. Die höhere Temperatur ermöglicht die Rückgewinnung von Abwärme als Dampf. Aufgrund der geringeren Katalysatorkonzentration ist jedoch ein separater Transalkylierungsreaktor erforderlich.
Durch Optimierung der Temperatur und der Ethylenzugabe reduziert der Prozess die erforderliche Menge an AlCl3-Katalysator erheblich und minimiert so die Probleme bei der Abfallentsorgung. Da er in einer einzigen homogenen Flüssigphase abläuft, entfällt die komplexe Katalysatorphase, die bei herkömmlichen Verfahren vorhanden ist.
Sowohl konventionelle als auch Monsanto-Prozesse verwenden ähnliche Reinigungsschritte mit mehreren Destillationskolonnen, um nicht umgewandelte Benzol-, Ethylbenzol- und Polyalkylbenzolfraktionen zu trennen. Organische Rückstände (Fluxöl) werden typischerweise als Brennstoff verwendet.
Der von UOP entwickelte Alkar-Prozess verwendet Bortrifluorid als Lewis-Säure-Katalysator. Obwohl er Vorteile wie ein hochreines Ethylbenzolprodukt und die Möglichkeit bietet, verdünntes Ethylen als Ausgangsmaterial zu verwenden, ist der Prozess aufgrund der hohen Wartungskosten und der Empfindlichkeit des Katalysators gegenüber selbst kleinen Wassermengen nicht vorteilhaft.
3.2. Herstellung von Ethylbenzol durch Dampfphasenalkylierung über Zeolithe
Die Dampfphasentechnologie von Mobil-Badger, die Mobils synthetischen Zeolithkatalysator ZSM-5 nutzt, entstand in den 1970er Jahren. Diese Technologie wurde in verschiedenen Konfigurationen angeboten.
Das Design der ersten Generation, das 1980 kommerzialisiert wurde, führte Alkylierung und Transalkylierung in einem einzigen Reaktor durch, ähnlich wie Aluminiumchloridverfahren. Die neueste Technologie der dritten Generation trennt diese Prozesse und bietet Vorteile in Bezug auf Ertrag, Reinheit und Kapitalkosten.
Das Dampfphasenzeolithverfahren eignet sich besonders für verdünnte Ethylenströme, wie sie beispielsweise aus Fluid Catalytic Cracking-Einheiten in Raffinerien stammen.
Bis zur Einführung der Flüssigphasenzeolithtechnologien in den 1990er Jahren dominierte dieses Verfahren die Installation neuer Anlagen aufgrund seiner Fähigkeit, die durch die Aluminiumchloridtechnologie erzeugten wässrigen Abfallströme zu vermeiden.
Mobil-Badger hat seit 1980 31 Anlagen lizenziert und die Technologie ist für verdünnte Ethylenrohstoffe nach wie vor relevant.
Der Festbettkatalysator ZSM-5 fördert die gleiche Alkylierungsreaktion wie andere Verfahren. Allerdings aktiviert die Ethylenadsorption an den Brønsted-Säurestellen des Zeoliths das Ethylenmolekül und erleichtert seine Bindung an Benzol. Dieser Mechanismus führt zu einem anderen Nebenprodukt als bei Friedel-Crafts-Verfahren.
Kohlenstoffstahl ist aufgrund des Fehlens hochkorrosiver Komponenten das primäre Baumaterial. Das Design der dritten Generation ist in Abbildung 3 dargestellt.
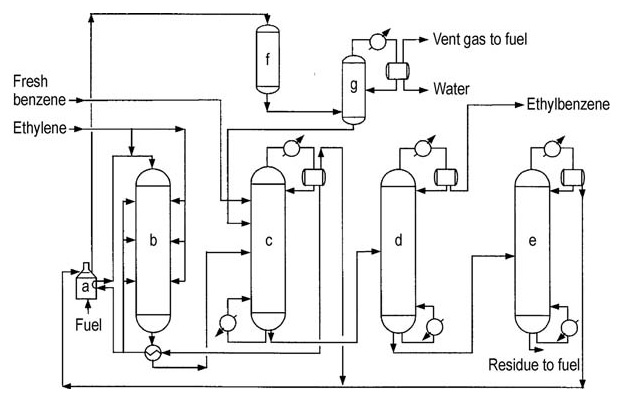
a) Reaktorzufuhrheizung; b) Alkylierungsreaktor; c) Benzolrückgewinnungssäule; d) Ethylbenzolrückgewinnungssäule; e) Polyethylenbenzolrückgewinnungssäule; f) Sekundärreaktor; g) Stabilisator
Der Alkylierungsreaktor arbeitet bei 350–450 °C und 1–3 MPa, wodurch die Rückgewinnung des Großteils der Prozesswärme als Dampf möglich ist. Der Reaktor verwendet eine Mehrbettkonfiguration mit einem befeuerten Heizgerät und Wärmerückgewinnungsgeräten.
Im Vergleich zu Ethylen bleibt ein Überschuss an Benzol erhalten. Der Katalysator wird aufgrund der Koksbildung allmählich deaktiviert, was eine regelmäßige Regeneration vor Ort (ungefähr alle 18–24 Monate) erfordert, die etwa 36 Stunden dauert.
Im Vergleich zu Flüssigphasenzeolithen und Lewis-Säure-Katalysatoren zeigt diese Technologie eine höhere Toleranz gegenüber Wasser, Schwefel und anderen potenziellen Giften.
Der verdampfte Reaktorausfluss wird gereinigt. Benzol wird durch Destillation in der ersten Kolonne zurückgewonnen und recycelt. Die zweite Kolonne trennt Ethylbenzol vom Bodenstrom, der dann zu einer letzten Kolonne geleitet wird, um wiederverwertbare Alkylbenzol- und Polyalkylbenzolfraktionen vom schweren, nicht wiederverwertbaren Rückstand zu trennen.
Dieser niedrigviskose Rückstand, der hauptsächlich aus Diphenylmethan und Diphenylethan besteht, wird als Brennstoff verwendet. Die abgetrennten wiederverwertbaren höheren Alkylbenzole und Polyalkylbenzole werden dem Dampfphasen-Transalkylator zugeführt, wo sie mit überschüssigem Benzol über einem Zeolithkatalysator reagieren.
Der Transalkylator arbeitet im Vergleich zum Alkylator bei niedrigerem Druck, aber höherer Temperatur und fördert die Dealkylierung höherer Alkylbenzole, während Diethylbenzol zu Ethylbenzol transalkyliert wird. Diese Fähigkeit zur Dealkylierung minimiert die Gesamtproduktion von Rückständen.
Die früheren Verfahren der ersten und zweiten Generation unterschieden sich hauptsächlich in der Position des recycelten Polyethylbenzolstroms, was zu einer geringeren Leistung im Vergleich zum Design der dritten Generation führte.
3.3. Ethylbenzolproduktion durch Flüssigphasenalkylierung über Zeolithe
Die Flüssigphasen-Zeolithtechnologie zur Ethylbenzolproduktion entstand Anfang der 1990er Jahre. Die erste kommerzielle Anlage in Oita, Japan, verwendete ultrastabile Zeolith-Y- oder Zeolith-Beta-Katalysatoren, lizenziert von ABB Lummus Global und Unocal (später von ABB übernommen).
Ein anderes Verfahren, EBMax von Mobil-Badger, verwendete Mobil MCM-22-Katalysatoren. Bis 1999 waren weltweit zwölf Anlagen in Betrieb.
Im Vergleich zu früheren Technologien mit Ethylen in Polymerqualität erfordern Flüssigphasen-Zeolithverfahren weniger Investitionen und liefern ein Ethylbenzolprodukt höherer Qualität.
Die Dampfphasentechnologie ist jetzt hauptsächlich von Mobil-Badger für Anwendungen lizenziert, bei denen verdünnte Ethylen-Ausgangsstoffe zum Einsatz kommen.
Flüssigphasenverfahren erfordern Zeolithe mit breiteren Poren im Vergleich zu ZSM-5, das in Dampfphasenverfahren verwendet wird, um Diffusionsbeschränkungen zu überwinden. Eine Katalysatorregeneration außerhalb des Standorts wird im Allgemeinen empfohlen, da die Katalysatorzykluszeiten verlängert werden und der Bedarf an Ausrüstung vor Ort sowie die Investitionskosten reduziert werden.
Beide großen Lizenzgeber (ABB Lummus und Mobil-Badger) bieten ähnliche Prozessfließbilder an (Abbildungen 4 und 5).
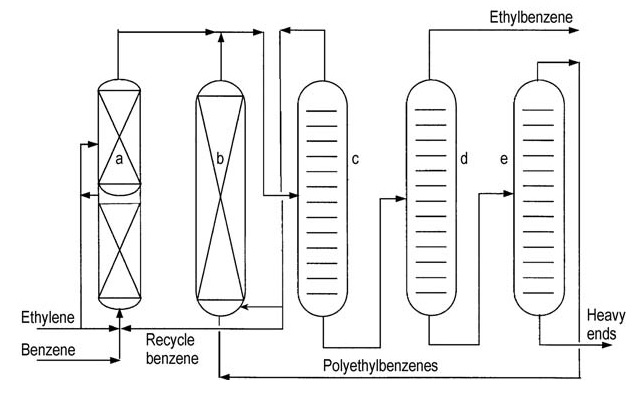
a) Alkylierungsreaktor; b) Transalkylierungsreaktor; c) Benzolkolonne; d) Ethylbenzolkolonne; e) Polyethylbenzolkolonne
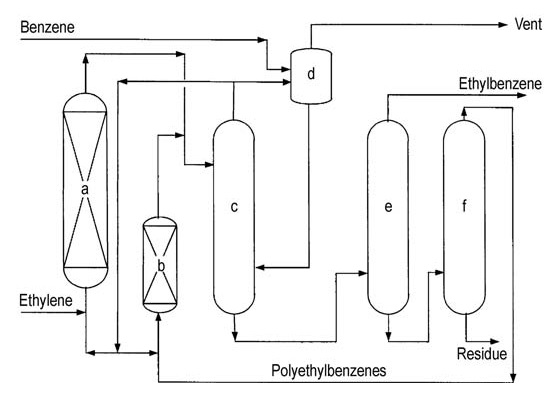
a) Alkylierungsreaktor; b) Transalkylierungsreaktor; c) Benzolkolonne; d) Abgaskolonne; e) Ethylbenzolkolonne; f) Polyethylbenzolkolonne
Ethylen wird in einen mehrstufigen Festbettreaktor eingeführt, der überschüssiges Benzol enthält. Die Reaktortemperaturen werden unter der kritischen Temperatur von Benzol (289 °C) gehalten. Hohe Drücke von etwa 4 MPa sind erforderlich, um leichte Gase in Lösung zu halten.
Überschüssiges Benzol wird vom Reaktorausfluss abgetrennt und in die Alkylierungsstufe zurückgeführt.
Eine Reihe von Destillationskolonnen reinigt das Rohethylbenzol. Durch Benzoldestillation wird überschüssiges Benzol zur Wiederverwertung entfernt. Durch Ethylbenzoldestillation wird das gewünschte Produkt abgetrennt, und durch Polyethylbenzoldestillation werden höhere Alkylbenzole und Polyethylbenzole aus dem Rückstand gewonnen.
Die gewonnenen höheren Alkylbenzole und Polyethylbenzole werden zur weiteren Umwandlung in einen Transalkylierungsreaktor eingespeist. Die Hauptverunreinigungen im endgültigen Ethylbenzol können Nichtaromaten, Toluol und höhere Alkylbenzole umfassen, die entweder aus dem Zufuhr- oder Produktionsprozess stammen.
3.4. Herstellung von Ethylbenzol durch ein zeolithbasiertes Mischphasenverfahren
CDTech, eine Zusammenarbeit zwischen ABB Lummus Global und Chemical Research and Licensing, bot ein zeolithbasiertes Mischphasenverfahren zur Herstellung von Ethylbenzol an. Die erste kommerzielle Anlage wurde 1994 in Betrieb genommen, und bis 1999 waren drei solcher Anlagen in Betrieb.
Das innovative Merkmal dieses Verfahrens ist der Alkylierungsreaktor, der einen Zeolithkatalysator in einer reaktiven Destillationskolonne enthält.
Sowohl Ethylen (Gas) als auch Benzol (Flüssigkeit) werden der reaktiven Destillationskolonne zugeführt. Diese Fähigkeit ermöglicht es dem Verfahren, verdünnte Ethylenströme zu verwenden, die während der Steamcracker-Destillation entstehen. Dieses Verfahren kann auch für Ethylen-Rohstoffe in Polymerqualität angepasst werden.
Der Prozessablauf ist in Abbildung 6 dargestellt.
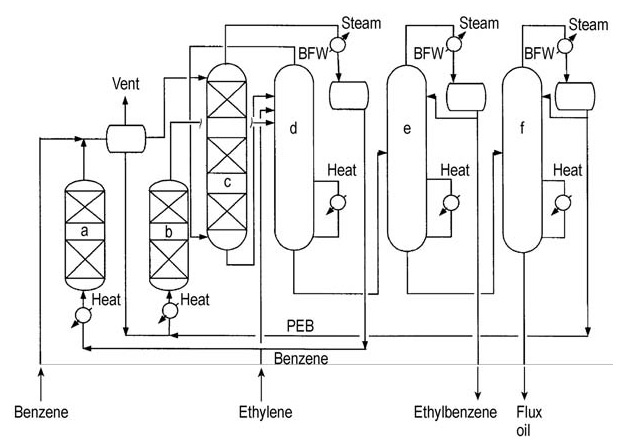
a) Finishing-Reaktor; b) Transalkylator; c) Alkylator; d) Benzolstripper; e) Ethylbenzolkolonne; f) Polyethylbenzolkolonne. BFW = Kesselspeisewasser, PEB = Polyethylbenzol
Die Alkylierung und die Benzolabtrennung erfolgen gleichzeitig in derselben reaktiven Destillationskolonne. Nicht umgewandeltes Ethylen und überschüssiges Benzol werden als Kopfprodukte abgezogen und zur weiteren Verarbeitung in einen Endreaktor geleitet.
Das Ethylbenzolprodukt wird in der Kopfproduktkolonne vom Bodenstrom getrennt. Der verbleibende Rückstand wird weiter verarbeitet, um transalkylierbare Polyethylbenzole zurückzugewinnen.
Die isolierten Polyethylbenzole werden dann zusammen mit überschüssigem Benzol in einen separaten Flüssigphasen-Transalkylierungsreaktor geleitet. Das Produkt aus dieser Transalkylierungsstufe wird zur weiteren Reinigung in die Fraktionierungsanlage zurückgeführt.
3.5. Trennung von Ethylbenzol aus gemischten C8-Strömen
Weniger als 1 % der weltweiten Ethylbenzolproduktion stammt aus der Trennung gemischter C8-Aromatenströme, die typischerweise parallel zur Xylolproduktion aus Reformat erfolgt. Obwohl es Adsorptionsverfahren wie EBEX von UOP gibt, bleibt die Destillation die primäre Methode zur Ethylbenzolrückgewinnung aus dieser Quelle.
Da es schwierig ist, Ethylbenzol aus diesen Strömen abzutrennen, ist ein Verfahren namens Superfraktionierung erforderlich. Dieses Verfahren wurde 1957 von der Cosden Oil & Chemical Company entwickelt und umfasst eine Reihe von drei Destillationskolonnen mit jeweils über 100 Stufen.
In den 1960er Jahren wurden in den USA, Europa und Japan mehrere Superfraktionierungsanlagen errichtet. Steigende Energiekosten und hohe Baukosten machten diese Methode jedoch wirtschaftlich unwettbewerbsfähig. Daher wurde die Superfraktionierung zugunsten effizienterer Methoden weitgehend aufgegeben.
4. Verwendung von Ethylbenzol
Fast das gesamte kommerziell hergestellte Ethylbenzol wird intern in Raffinerien oder Chemiewerken zur Herstellung von Styrolmonomer verwendet, einem wichtigen Baustein für die Herstellung von Polystyrol. In einigen Fällen wird Ethylbenzol zusammen mit Propylenoxid hergestellt.
Weniger als 1 % Ethylbenzol wird als Farblösungsmittel oder als Zwischenprodukt für die Synthese von Diethylbenzol, Acetophenon und Ethylanthrachinon verwendet.
5. Toxikologie von Ethylbenzol
Ethylbenzol wird nach Einatmen, oraler und dermaler Exposition leicht absorbiert. Es unterliegt einem primären Metabolismus durch Seitenkettenoxidation, wobei kleinere Metaboliten durch Hydroxylierung aromatischer Ringe entstehen. Weniger als 5 % werden unverändert als 2- und 4-Ethylphenol im Urin ausgeschieden.
Die wichtigsten identifizierten Metaboliten sind:
- 1-Phenylethanol (wichtigster Metabolit im Urin bei Ratten)
- Mandelsäure (wichtigster Metabolit im Urin beim Menschen)
- Phenylglyoxylsäure (wichtigster Metabolit im Urin beim Menschen)
- Benzoesäure
- Phenylessigsäure (weniger wichtiger Metabolit)
Experimentelle Studien weisen auf eine geringe akute Toxizität bei Tieren hin. Die oralen LD50-Werte bei Ratten liegen zwischen 3,5 und 4,7 g/kg Körpergewicht. Es wurde ein dermaler LD50-Wert von etwa 15 g/kg Körpergewicht berichtet.
Inhalationsexposition bei Ratten führte ab 1000 ppm zu Reizungen der Atemwege. Höhere Konzentrationen bei 5000 ppm führten zu Unsicherheit, schwankendem Gang und schließlich zu Bewusstlosigkeit und Tod. Freiwillige Versuchspersonen, die 7,5 Stunden lang 25 ppm ausgesetzt waren, berichteten von leichter Schleimhautreizung, die sich bei 100 ppm noch verstärkte.
Wiederholter Hautkontakt mit unverdünntem Ethylbenzol kann zu Erythem, Ödem und oberflächlicher Nekrose führen. Ähnliche Effekte werden bei Menschen aufgrund der Entfettung der Haut bei wiederholter Exposition erwartet.
Studien zur wiederholten Exposition zeigten, dass signifikante Nebenwirkungen bei Tieren nur bei relativ hohen Ethylbenzol-Dosen auftraten.
Bei Ratten wurden bei 100 ppm und Mäusen bei 500 ppm im Verlauf einer dreimonatigen Inhalationsstudie keine Effekte beobachtet; jedoch wurden erhöhte Lungen-, Nieren- und Lebergewichte ab 250 ppm bei Ratten und 750 ppm bei Mäusen beobachtet. Es wurden keine histopathologischen Veränderungen festgestellt.
Zweijährige Inhalationsstudien zeigten bei 75 ppm keine Auswirkungen bei Ratten und Mäusen. Bei 250 ppm wurden leichte Veränderungen beobachtet, mit vermehrten Leber- und Lungentumoren bei Mäusen und Nierentumoren bei männlichen Ratten bei 750 ppm (gilt als rattenspezifisch und für den Menschen nicht relevant).
Bezüglich der Reproduktionstoxizität von Ethylbenzol wurden in verschiedenen Studien widersprüchliche Ergebnisse berichtet. Einige Studien deuten auf eine potenzielle Fetotoxizität bei hohen Expositionswerten bei trächtigen Mäusen und Ratten hin, aber bei Kaninchen wurden bei 1000 ppm und einer 7-stündigen täglichen Exposition keine eindeutigen Auswirkungen beobachtet.
Das Gesamtergebnis verschiedener Studien deutet darauf hin, dass Ethylbenzol keine mutagene Gefahr darstellt. Begrenzte In-vitro-Daten für die meisten Metaboliten deuten ebenfalls auf kein eindeutiges genotoxisches Potenzial hin.
Eine zweijährige Inhalationsstudie zeigte eine erhöhte Tumorinzidenz bei männlichen Ratten (Niere), männlichen Mäusen (Lunge) und weiblichen Mäusen (Leber) bei der höchsten Expositionsstufe (750 ppm). In einer oralen Studie mit Ratten und Mäusen, die Xylolmischungen mit 17 % Ethylbenzol ausgesetzt waren, wurden keine expositionsbedingten Tumore beobachtet.
Ethylbenzol ist in vivo nicht genotoxisch, was auf eine nicht genotoxische Wirkungsweise der beobachteten Tumore in der Hochdosis-Inhalationsstudie hindeutet. Eine verstärkte Tumorbildung kann mit einer durch Ethylbenzol induzierten Zellproliferation in der Niere (Ratten) und Lunge/Leber (Mäuse) zusammenhängen.
Weitere Untersuchungen sind erforderlich, um die Relevanz für den Menschen zu bestimmen und einen sicheren Arbeitsplatzgrenzwert festzulegen.
Die IARC stuft Ethylbenzol aufgrund ausreichender Beweise bei Tieren und unzureichender Beweise beim Menschen als „möglicherweise krebserregend für den Menschen“ (Gruppe 2B) ein.
Die deutsche MAK-Kommission stuft Ethylbenzol aufgrund von Daten zur Karzinogenität als Karzinogen der Kategorie 3A ein. Sie wartet auf weitere mechanistische Daten, bevor sie einen Arbeitsplatzgrenzwert festlegen kann.
ACGIH stuft Ethylbenzol als A3-Karzinogen ein („bestätigtes Tierkarzinogen mit unbekannter Relevanz für den Menschen“) und empfiehlt einen TLV-TWA von 100 ppm und einen TLV-STEL von 125 ppm. Sie definieren auch einen biologischen Expositionsindex (BEI) für Mandelsäure im Urin von 1,5 g/g Kreatinin.
In der EU wird Ethylbenzol als „leicht entzündlich“ (F) und „gesundheitsschädlich beim Einatmen“ (Xn) eingestuft.
Referenz
- Ethylbenzol; Ullmanns Enzyklopädie der industriellen Chemie. – https://onlinelibrary.wiley.com/doi/10.1002/14356007.a10_035.pub2