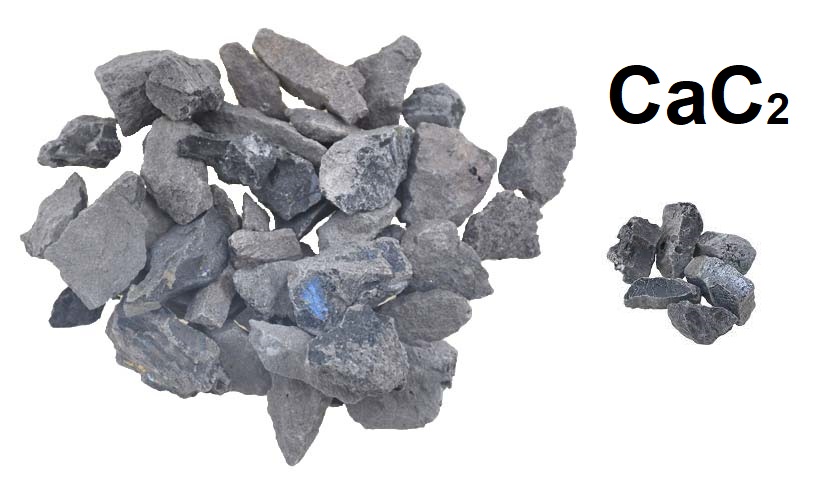
Calcium carbide, also known as calcium acetylide, is a greyish-black, crystalline compound with the chemical formulat CaC2. Upon contact with water it generates acetylene, a highly flammable gas once widely used for lighting and welding.
Among carbides, calcium carbide stands out as the most industrially significant. It remains the backbone of the acetylene welding-gas industry, particularly in regions where raw materials and energy are readily available, and petroleum is scarce.
Table of Contents
Calcium carbide is manufactured in numerous countries as the precursor for various acetylene-based products, notably poly(vinyl chloride) (PVC) and in the production of calcium cyanamide.
It also finds use in desulfurization of molten metals like iron and steel, as well as in foundry practices, where it forms part of metal treatment additives.
The chemical composition of calcium carbide was first identified by Wöhler in 1862, achieved by the reaction of a calcium-zinc alloy and coal. Prior to this, several researchers had prepared the compound in laboratory settings, often using electric arcs on coal or coke products in the presence of calcium compounds.
The late 19th century witnessed the development of industrial-scale production in electrothermic furnaces. Moissan in France and Morehead and Willson in the United States independently laid the groundwork for this technological leap between 1885 and 1895. The first operational industrial carbide furnace, built by the Willson Aluminum Company in Spray, USA, emerged in 1895.
Bertolus proposed the use of multiphase electric currents for industrial furnaces in 1897. Helfenstein followed suit in 1904 with a three-phase current furnace equipped with three electrodes. These early furnaces, boasting capacities ranging from 3000 to 7500 kW, even incorporated waste-gas recovery systems (Helfenstein barrier). Within a centry, 40 MW furnaces became usual.
Modern large electric furnaces, capable of handling up to 60 MW, employ Soderberg electrodes and are fully enclosed, allowing for carbon monoxide byproduct recovery. Recent advancements have focused on developing reliable, medium-sized closed furnaces better suited to market demands and available raw materials.
The carbothermic process, employed by BASF in Germany between 1940 and 1960, provided an alternative route to calcium carbide production, but it has since been abandoned.
1. Physical Properties of Calcium Carbide
Calcium carbide, CaC2, is a binary ionic compound with a molar mass of 64.10 g/mol. In its pure form, it is colorless and odorless. However, technical-grade material often exhibits various shades of grey to brownish black, occasionally with violet or red-brown hues, due to impurities.
The characteristic phosphine odor of technical-grade calcium carbide stems from traces of calcium phosphide reacting with moisture.
Pure calcium carbide possesses a high melting point of 2160 °C, decomposing completely above 2500 °C. Four distinct crystallographic modifications exist:
- Phase I: tetragonal, stable between 25 and 440 °C (dominant in commercial carbide)
- Phases II and III: lower symmetry, stable below 440 °C
- Phase IV: face-centered cubic, stable above 440 °C
The heat of transformation at 440°C is 8.68 J/g. Notably, the CaC2-CaO phase diagram exhibits a simple eutectic behavior, with no compound formation or solid solutions in the solid state. The components become fully miscible only above the liquidus line. Impurities in technical-grade carbide lower its liquidus temperature.
Calcium carbide has an average specific heat capacity of 1047 J kg⁻¹ K⁻¹ between 20 and 440 °C and a heat of fusion of 1470 J/g for pure material. Its standard enthalpy of formation from elements at 298 K is -59.4 kJ/mol and standard entropy is 70.3 J mol⁻¹ K⁻¹.
The electrical conductivity of calcium carbide ranges from 100 to 1000 S.m⁻¹ and is highly dependent on purity and temperature.
2. Chemical Properties of Calcium Carbide
Calcium carbide, CaC2, undergoes a range of important chemical reactions:
Synthesis of calcium cyanamide: This exothermic reaction (ΔH298 = -289 kJ/mol) converts calcium carbide and nitrogen gas into calcium cyanamide and carbon: CaC2 + N2 → CaCN2 + C.
Hydrolysis to acetylene: Reaction with water readily produces acetylene, calcium hydroxide, and heat (ΔH298 = -128.4 kJ/mol): CaC2 + 2 H2O → C2H2 + Ca(OH)2.
Efficient acetylene production occurs below 300 °C, with pure calcium carbide yielding 346.89 L/kg (dry) at 0 °C and 101.3 kPa (slightly higher at 15 °C with water vapor present). High temperatures yield calcium oxide, hydrogen, and carbon dioxide instead.
Reaction with sulfur: Calcium carbide reacts with sulfur in molten iron to form calcium sulfide and release carbon: CaC2 + [S]Fe → CaS + 2 [C]Fe.
Hydrogenation: Under pressure, hydrogenation of calcium carbide produces not only calcium hydride and methane but also other hydrocarbons.
Calcium carbide dissolves in various molten salts, enabling diverse reduction reactions.
Electrolysis: Electrolysis of dissolved calcium carbide in molten salts yields calcium at the cathode and carbon at the anode.
3. Production of Calcium Carbide
While the preparation of pure calcium carbide holds academic interest, its industrial production prioritizes technical-grade material for practical applications. This largely relies on the high-temperature reaction of quicklime (CaO) with carbonaceous sources like coke and anthracite:
CaO + 3 C → CaC2 + CO (ΔH298 = +465 kJ/mol)
The reaction rate becomes significant only above 1600 °C. However, exceeding 2000 °C introduces undesirable side reactions, particularly:
CaC2 → Ca + 2 C
CaC2 + 2 CaO → 3 Ca + 2 CO
Therefore, industrial processes operate within the 1800-2100 °C range, yielding technical-grade calcium carbide with approximately 80% CaC2 content. The remainder comprises mainly CaO, with additional impurities like SiO2 and Al2O3 from raw materials.
High temperatures are crucial for calcium carbide production, requiring two potential approaches:
- Electrothermic Shaft Furnace: Melts the carbonaceous material with CaO in a short furnace, directly introducing electrical energy.
- Oxygen-Combustion Shaft Furnace: Combusts carbonaceous material with pure or enriched oxygen in the presence of CaO.
While the latter method offered synthesis gas as a byproduct, it was ultimately abandoned after 50 years due to the cheaper production of the same gas from petroleum. Today, all commercial calcium carbide production uses the first electrothermic approach.
3.1. Raw Materials
The raw materials for calcium carbide production, known as the “burden” in the electrothermic furnace, play a crucial role in efficiency and product quality. These materials consist of two main components: a carbonaceous source and a lime-bearing component.
Particle size, strength, and conductivity significantly impact furnace performance and operational stability. Smaller open furnaces offer flexibility in adjusting these properties manually or mechanically, while high-capacity closed furnaces require stricter specifications for unattended operation.
Volatiles and ash content influence reaction efficiency and waste generation. Modern closed furnaces allow fine-grained materials by injecting them directly through hollow electrodes. Impurities like metal oxides can cause undesirable side reactions and require careful management.
Carbon Source
- Coke: Derived from bituminous coal or lignite, coke is the primary carbonaceous material used globally due to its availability and suitable properties. Grain size typically ranges from 3-25 mm, with finer fractions injected through electrodes. Moisture content must be below 2% and ash content below 15% for optimal production.
- Other Options: Uncalcined anthracite and petroleum coke can be used partially in closed furnaces, but require calcination to reduce volatiles below 2% for sole use. Charcoal finds application only in small open furnaces.
Lime-Bearing Component
- Quicklime: The predominant choice, with large closed furnaces requiring a 6-50 mm grain size and injection of finer fractions. Magnesium content should be below 2% for efficient operation. Lime must be soft yet durable, achievable through modern kilns, and have a CO2 content below 2%.
- Recycled Calcium Hydroxide: This byproduct from acetylene generation can be used as a cheap raw material after granulation or briquetting, but impurity build-up limits its recycling potential.
Waste plastics are increasingly explored as a secondary carbon source, with strict specifications on chlorine content (max. 12%) due to its undesirable vaporization and reaction with calcium.
Tables 1 and 2 provide examples of typical raw material compositions for calcium carbide production.
Material | Fixed Carbon | Volatile Carbon | Moisture | Sulfur | Ash |
---|---|---|---|---|---|
Metallurgical Coke | 89.0 | 0.8 | 0.8 | 0.8 | 9.4 |
Anthracite | 80.0 | 6.0 | 8.0 | 0.8 | 6.0 |
Petroleum Coke | 81.6 | 9.0 | 8.0 | 1.9 | 0.3 |
Component | New Lime | Recycled Lime |
---|---|---|
Total CaO | 93.8 | 89.0 |
Free CaO | 93.6 | - |
CaSO4 | 0.4 | - |
SiO2 | 1.3 | 2.9 |
Fe2O3 | 0.4 | 0.4 |
Al2O3 | 0.5 | 2.4 |
MgO | 0.8 | 0.8 |
CO2 | 2.7 | 3.0 |
P2O5 | 0.015 | 0.01 |
Loss on ignition (CO2) | 0.5 | 0.5 |
3.2. Electrothermic Reduction
The raw material mixture for calcium carbide production undergoes high-temperature processing in a short-shaft electric furnace. Investigations suggest a two-step reaction mechanism:
- Calcination: CaO + C → Ca + CO
- Carbide Formation: Ca + 2 C → CaC2
The primary reaction zone within the furnace lies in a molten CaC2-CaO phase. However, the complex interplay of electric current, heat supply, temperature, and chemical reactions remains imperfectly understood.
The rate-limiting step likely involves transporting dissolved CaO in the melt to the coke grain surface, where CaC2 formation occurs. This newly formed CaC2 readily dissolves back into the melt.
Finally, the molten calcium carbide is tapped from the furnace bottom.
3.3. Furnaces
Calcium carbide furnaces can be categorized based on three key aspects:
- Electrical supply: Single-phase or three-phase.
- Electrode arrangement: Serial, symmetrical, or other configurations.
- Air exclusion: Open, half-covered, or closed.
1. Single-Phase Furnaces
Developed in 1928, these furnaces operate at high current and low voltage, achieving power factors up to 0.95. However, they are less efficient and have fallen out of favor compared to three-phase designs.
2. Three-Phase Furnaces
The dominant type today, categorized by electrode arrangement:
- Serial: Offers advantages in feeding and distribution but limitations in gas recovery and power consumption.
- Symmetrical: High-performance design with balanced power factors and overlapping molten zones at higher power.
3. Half-Covered Furnaces
Early furnaces vented CO directly, causing pollution. Modern designs employ gas collection hoods, though closed furnaces offer the best environmental control.
4. Closed Furnaces
These modern furnaces provide 100% gas recovery and minimal environmental impact. Key components include:
- Hearth: Constructed with steel and refractory materials to withstand high temperatures.
- Electrodes: Soderberg electrodes are preferred for their cost-effectiveness and continuous operation. Hollow electrodes allow direct injection of raw materials.
- Power Supply: Transformers with oil cooling and controllable output to manage fluctuations.
- Power Diagram: Represents the complex interplay of resistances and reactances within the furnace.
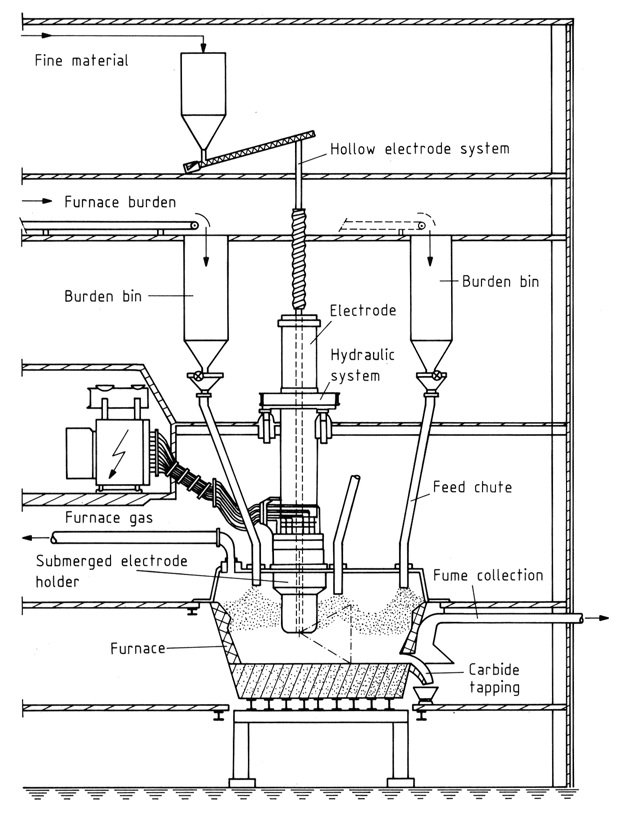
Control and Operation
Three-phase furnaces require impedance control by adjusting electrode immersion depth to manage power and furnace resistance. Closed hoods may allow manipulation of feeding chutes to further regulate resistance.
3.4. Industrial Process
Calcium carbide production begins with a foundation of coarse coke layered within the furnace. Electrodes are meticulously lowered towards the coke until electric arcs signal contact. As the coke attains red heat, the furnace bottom is gradually fed with burden, and power is incrementally elevated to match the rising temperature.
Consistent burden feeding is essential for optimal furnace operation. Minor compositional variations can be mitigated through lime additions, necessitating deeper electrode immersion due to lime’s lower conductivity.
Excessive electrode height risks carbide formation in the upper burden layers, potentially leading to hazardous melt “spurting.” Maintaining gas permeability within the solid material is essential for consistent production.
Furnace hood pressure must be meticulously balanced with atmospheric pressure to prevent oxygen intrusion or the leakage of carbon monoxide. Large-scale furnace setups often employ centralized control rooms for efficient operation and comprehensive monitoring of environmental parameters.
Tapping involves either mechanically opening the furnace or using an electric arc to create a tapping hole. A dedicated baked electrode facilitates the melting of carbide, which flows at temperatures ranging from 1700-2100 °C depending on purity, into specifically designed cooled cast-iron ladles.
Due to its high melting point and rapid heat loss, technical-grade carbide (80% CaC2) solidifies quickly, necessitating continuous maintenance of the tapping hole with steel rods.
Chain curtains, wire netting, and steel shields safeguard operators from hot gases, dust, and potentially hazardous spurting carbide during the tapping process. Specialized protective gear, including aluminum-covered fireproof coats, dark glasses, and protective visors, is mandatory for all personnel involved in tapping operations.
Fume extraction systems effectively remove harmful aerosol particles, reducing environmental impact.
Modern hydraulic manipulators equipped with interchangeable tools have revolutionized tapping procedures, minimizing the need for direct human involvement and enhancing safety.
The reduction of impurities like Fe2O3 and SiO2 by carbon yields ferrosilicon, which, due to its higher density, settles below the carbide melt and typically flows out during tapping. However, its lower melting point relative to carbide necessitates constant vigilance and preventive measures to avert leakage through cracks in the furnace lining.
4. Uses of Calcium carbide
Calcium carbide is used in the production of acetylene, the reaction with nitrogen to form calcium cyanamide, and the desulfurization of hot metals.
While its use as a precursor for heavy chemicals has declined due to the dominance of petrochemicals since the 1960s, acetylene derived from calcium carbide remains important in gas welding. Its adaptability and portability make it indispensable for tasks like pipeline construction, even amidst advancements in material joining techniques.
Acetylene continues to find niche applications in the synthesis of specific chemicals, such as butynediol for plastics and fibers, and acetylene black for dry batteries.
Calcium carbide’s reactivity with sulfur makes it a valuable tool in metallurgy. Stringent steel quality standards demand minimal sulfur content, and desulfurization using calcium carbide before the steelmaking converter proves the most economical method.
Injection of finely ground (< 100 mm) calcium carbide into the molten metal effectively reduces sulfur content, typically from 0.2% to as low as 0.001%. Combinations of calcium carbide with magnesium are increasingly explored to enhance reactivity within the hot metal.
In foundry practices, coarse-grained calcium carbide, often combined with additives like fluorspar, finds use in desulfurization. The mixture is stirred into the ladle after tapping and before casting, contributing to improved metal quality.
5. Toxicology of Calcium carbide
Calcium carbide is classified as a severe eye irritant and a skin irritant, with low potential for sensitization.
Commercial-grade calcium carbide may pose acute inhalation harm due to its corrosive/irritating properties.
Limited data are available for calcium carbide itself, but concerns are raised by certain trace components:
- Phosphine: Genotoxic evidence exists, but its low concentration in calcium carbide (< 0.1%) minimizes the risk.
- Arsenic: Although present at < 0.1%, this potential carcinogen may generate arsine upon contact with water. However, current CLP criteria do not necessitate classification as a carcinogen.
Based on the low levels of arsenic and its limited conversion to arsine, classification as a carcinogen is not warranted.
Due to its quick breakdown in water, the pure compound’s ecotoxicity is negligible.
Studies on fish, Daphnia, and algae provide insights into the toxicity of breakdown products and minor constituents.
The high LC50 for fish (>50 mg/L) and EC50 for Daphnia (4.42 mg/L) likely reflect the toxicity of hydrogen sulfide, produced from the impurity calcium sulfide.
Overall, biodegradation studies suggest readily biodegradable properties for calcium carbide and its breakdown products.
Reference
- Calcium Carbide; Ullmann’s Encyclopedia of Industrial Chemistry. – https://onlinelibrary.wiley.com/doi/10.1002/14356007.a04_533.pub2