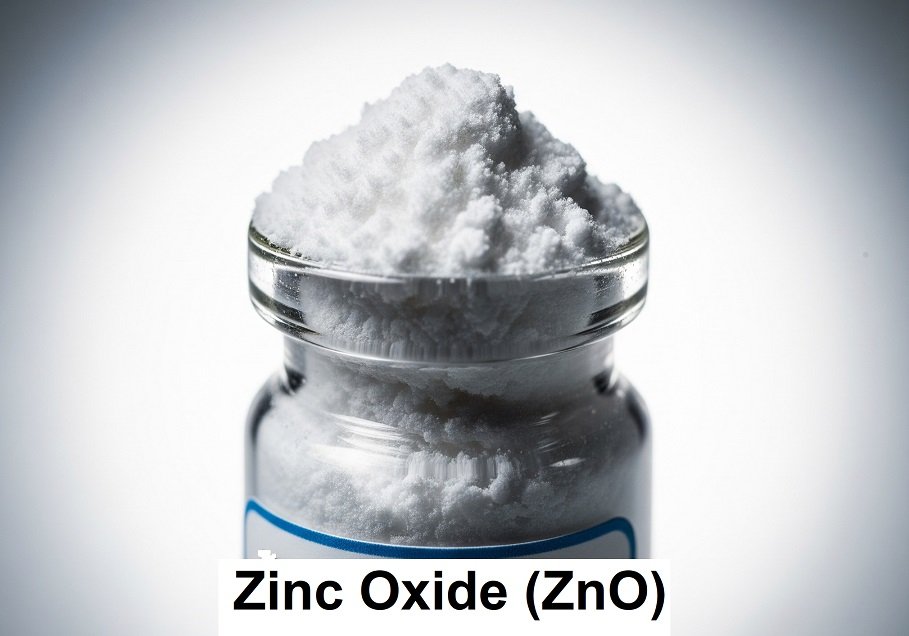
What is Zinc Oxide?
Zinc oxide is an inorganic compound with the chemical formula ZnO. It’s a white powder that is insoluble in water. While it can occur naturally as the mineral zincite, most zinc oxide used commercially is produced synthetically.
In the past, zinc oxide was only used as a white pigment, known by various names, including zinc white (C.I. Pigment White 4), Chinese white, and flowers of zinc.
Zinc oxide emerged as a byproduct of copper smelting. Ancient Romans referred to it as “cadmia,” and they used it in brass production. They also refined it through a reduction-oxidation sequence for medicinal ointments. Medieval alchemists thought that cadmia could be converted into gold.
In the mid-18th century, the German chemist Cramer produced zinc oxide by combusting metallic zinc. Courtois began the production of zinc white in France in 1781; however, the industrial-scale manufacturing only started in 1840 by Leclaire using the indirect, or French, process.
Zinc oxide rapidly replaced white lead due to its superior properties, such as non-toxicity, resistance to discoloration from sulfurous gases, and good opacity.
Around 1850, S. Wetherill of the New Jersey Zinc Company developed a roasting furnace in which a coal-laden grate was charged with coal and then covered with a mixture of zinc ore and coal. Zinc underwent reduction via partial coal combustion and then reoxidized when exiting the furnace.
This method became known as the direct, or American, process. While these furnaces saw later improvements, they are no longer in use.
In the latter half of the 19th century, zinc oxide was incorporated into rubber formulations to reduce the vulcanization time. The discovery of organic accelerators in 1906 significantly enhanced the vulcanization process, thereby increasing the importance of zinc oxide, which was used as an activator in the rubber industry.
Table of Contents
1. Physical Properties of Zinc Oxide
Zinc oxide is a fine white powder that changes to yellow when heated above 300 °C. It absorbs ultraviolet (UV) light at wavelengths below 366 nm.
The introduction of trace monovalent or trivalent elements into its crystal lattice imparts semiconducting properties. Elementary particles of ZnO produced via thermal methods can be granular or nodular (0.1−5 µm) or acicular (needle-shaped).
ZnO is insoluble in water, with a solubility of approximately 0.16 mg/100 mL at 30 °C; however, it dissolves in dilute acids and strong bases due to its amphoteric nature.
Important physical properties of zinc oxide are summarized in the table below:
Property | Value |
---|---|
CAS number | [1314-13-2] |
Chemical Formula | ZnO |
Molecular Weight | 81.38 g/mol |
Melting Point | 1975 °C |
Boiling Point | around 2360 °C |
Density | 5.65–5.68 g/cm3 |
Refractive Index | 1.95–2.1 |
Heat Capacity at 25 °C | 40.26 J mol-1 K-1 |
Heat Capacity at 100 °C | 44.37 J mol-1 K-1 |
Heat Capacity at 1000 °C | 54.95 J mol-1 K-1 |
Thermal Conductivity | 25.2 W m-1 K-1 |
Crystal Structure | hexagonal, wurtzite |
Mohs Hardness | 4–4.5 |
Oil Absorption Value | 20–24 g/100 g |
Apparent Density | 100 cm3/100 g |
Mean Particle Size | 0.11–0.22 mm |
BET Surface Area | 3–10 m2/g |
2. Chemical Properties of Zinc Oxide
Zinc oxide is amphoteric. It reacts with both organic and inorganic acids. It also dissolves in alkaline solutions and ammonia to form zincates. ZnO readily reacts with acidic gases, such as carbon dioxide, sulfur dioxide, and hydrogen sulfide. High-temperature reactions with other oxides yield compounds like zinc ferrites.
It reacts with acids to produce zinc salts and water. This represents a neutralization reaction where ZnO acts as a base.
ZnO + 2 HCl → ZnCl2 + H2O
ZnO + H2SO4 → ZnSO4 + H2O
ZnO + 2 HNO3 → Zn(NO3)2 + H2O
Zinc oxide reacts with strong bases to form soluble zincates. ZnO functions as an acid in these reactions.
ZnO + 2 NaOH → Na2ZnO2 + H2O (sodium zincate)
Zinc oxide can undergo reduction to metallic zinc by using high temperatures and a reducing agent. It is a standard step in zinc ore extraction.
Carbon (coke) reduces zinc oxide to zinc metal, and carbon is oxidized to carbon monoxide. This reaction holds historical and industrial significance.
Hydrogen or reactive metals such as magnesium can also reduce zinc oxide.
Zinc oxide reacts with many organic compounds, especially carboxylic acids and fatty acids (e.g., stearic acid, found in oils and rubber formulations), to form zinc carboxylates (zinc soaps).
Zinc stearate (1), formed by the reaction of stearic acid with zinc oxide, is used as an accelerator activator and can also contributes to the degradation of oil paints containing ZnO pigment.
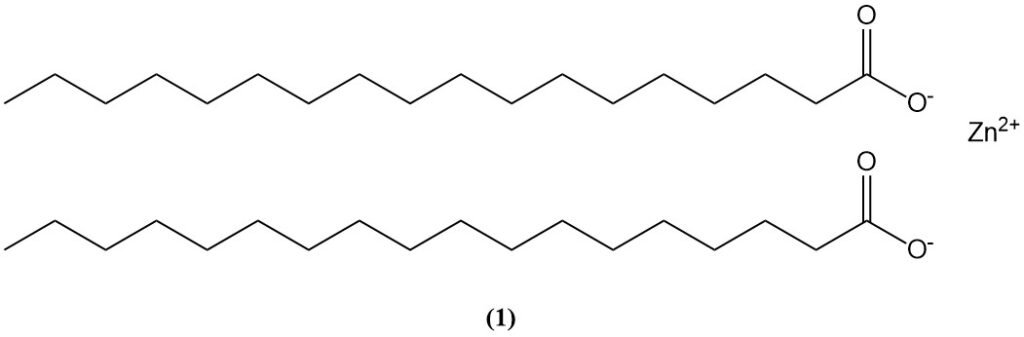
Zinc oxide is thermally stable, but it can dissociate at extremely high temperatures. This thermal decomposition is a key step in certain thermochemical cycles for hydrogen production.
3. Industrial Production of Zinc Oxide
Industrially, zinc oxide is primarily produced by two main processes: the Indirect Process (French Process) and the Direct Process (American Process). A smaller amount is also produced via wet chemical processes.
The wet process accounts for approximately 1−2% of zinc oxide production. The direct process contributes 10−20%, and the indirect process yields the remaining majority.
Historically, raw materials for the direct process primarily comprised zinc ores or concentrates. The indirect process used virgin metallic zinc from producers. Current zinc oxide manufacturing predominantly uses residues and secondary zinc.
This fact, coupled with user demands for high chemical purity, led to process modifications and the use of various purification techniques.
3.1. Production of Zinc Oxide by Direct or American Process
The direct, or American, process for zinc oxide production is characterized by its simplicity, cost-effectiveness, and high thermal efficiency. It involves the initial high-temperature reduction (1000−1200 °C) of zinc-containing materials. Coal is used as the reducing agent. Reduction occurs according to Boudouard’s reactions:
ZnO + C ⇌ Zn + CO
ZnO + CO ⇌ Zn + CO
2 C + O2 ⇌ CO
2 CO2 + C ⇌ 2 CO
Zinc vapor and carbon monoxide gas subsequently undergo oxidation to form zinc oxide and carbon dioxide above the reaction bed or at the furnace exit.
Various zinc-containing feedstocks are utilized. These include zinc concentrates, metallization residues, byproduct zinc hydroxide, and, mainly, zinc dross from casting furnaces or galvanizing operations. Dross should be pretreated by heating at approximately 1000 °C in rotary kilns to remove chloride and lead impurities.
Currently, only rotary kilns are employed for the direct process. Static furnaces are no longer in use. Raw materials typically contain zinc at a range from 60% to 75%. Two primary types of rotary kilns exist: long, narrow kilns and shorter, wider kilns.
1. Long, narrow kilns: These kilns are approximately 30 m in length and 2.5 m in diameter, and they are heated using gas or oil. Raw material, a mixture of zinc-containing substance and coal, is continuously fed countercurrent or cocurrent to the combustion gases.
Residues, containing residual zinc and unburned coal, continuously exit the furnace at the end opposite the feed point. Excess coal is sieved and recycled. Combustion gases, comprising zinc vapor, ZnO, and CO, enter a chamber where oxidation completes and large impurity particles settle.
Gases are then cooled via a heat exchanger or air dilution. Zinc oxide is subsequently collected in bag filters.
2. Shorter, wider kilns: This type of rotary kiln is approximately 5 m in length and 3 m in diameter. Charging of raw materials is continuous; however, dezincified residues are removed batchwise.
Operating conditions for both kiln types are precisely controlled to ensure high yield and the attainment of desired particle shape and size. Chemical purity, assuming no external contamination, is solely determined by the composition of the initial raw materials.
3.2. Production of Zinc Oxide by Indirect or French Process
In the indirect, or French, process, the zinc is boiled, and the zinc vapor formed undergoes oxidation by combustion in air under controlled parameters. Crystallographic and physical properties of the generated zinc oxide can be adjusted by modifying combustion conditions, such as flame turbulence and air excess.
The chemical composition of the ZnO product depends exclusively on the zinc vapor’s composition.
Diverse furnace types facilitate the production of zinc vapor with the required purity from various raw materials, ensuring high zinc yield.
Raw materials used in this process include pure zinc (super high grade, SHG; high grade, HG) and, increasingly, metallic residues (e.g., scrap zinc, die casting dross, galvanizer’s dross). Prior to oxidation, liquid-phase or vapor-phase separation techniques remove impurities such as cadmium, lead, iron, and aluminum from the zinc metal.
Specific methods for zinc vaporization and purification include:
1. Muffle furnaces or retorts (graphite/silicon carbide): Metal feedstock is introduced into the furnace either as solid batches or continuous liquid streams. Vaporization heat is supplied by external heating of the retort with a burner.
Nonvolatile residues, such as iron and lead from smelting dross, accumulate within the retort. Periodic removal of these residues is necessary, often by tilting the retorts.
2. Fractional distillation: Zinc vapor, containing impurities like Cd, Pb, Fe, Al, and Cu, can be purified via fractional distillation. This process occurs in columns, often equipped with silicon carbide plates (e.g., the New Jersey Zinc Co. design). Oxidation of the purified zinc vapor takes place at the column’s exit.
3. Two-chamber furnaces: Metallic raw material, mainly in large pieces, enters a primary melting chamber, which connects to a secondary, electrically heated chamber. Distillation occurs in the second chamber, in an air-free environment.
Nonmetallic residues are extracted from the melting chamber surface. Impurities, including iron, aluminum, and a portion of the lead, accumulate in the distillation chamber and are periodically removed in liquid form. Residual lead traces are subsequently eliminated by fractional distillation. Lundevall developed the first version of this furnace type.
4. Rotary kiln smelting process: Indirect zinc oxide can also be produced by a smelting process within a rotary kiln, using the same raw materials. The melting, the distillation, and a portion of the oxidation occur within a single reaction zone, which enables the use of a large part of the heat of combustion of the zinc.
By controlling the temperature and the partial pressures of carbon dioxide and oxygen, lead impurity content can be limited and ZnO particle shape and size can be adjusted, albeit with less precision than other methods.
3.3. Production of Zinc Oxide by Wet Process
Zinc oxide is produced by the wet process, which precipitates basic zinc carbonate from purified zinc sulfate or chloride solutions. The precipitate is washed and filtered and then is calcinated to form zinc oxide. This method produces ZnO with a high specific surface area.
Similar products are obtained from waste hydroxides, which are chemically purified and then calcined.
3.4. Aftertreatment
Thermal aftertreatment, at temperatures up to 1000 °C, enhances the pigment properties of ZnO and is primarily applied to oxide produced via the direct method. Controlled atmospheric calcination further improves the photoconducting properties of high-purity oxide. This high-purity oxide is used in photocopying applications.
The surface of zinc oxide can be made more organophilic by coating it with oil and propionic acid. Zinc oxide often undergoes deaeration. It is sometimes pelletized or granulated to improve handling properties.
A | B | C | D | |
---|---|---|---|---|
Parameter | Indirect process | Indirect process | Direct process | Wet process |
ZnO (min.), wt% | 99.5 | 99 | 98.5 | 93 |
Pb (max.), wt% | 0.004 | 0.25 | 0.25 | 0.001 |
Cd (max.), wt% | 0.001 | 0.05 | 0.03 | 0.001 |
Cu (max.), wt% | 0.0005 | 0.003 | 0.005 | 0.001 |
Mn (max.), wt% | 0.0005 | 0.001 | 0.005 | 0.001 |
Water-soluble salts (max.), wt% | 0.02 | 0.1 | 0.65 | 1 |
Loss on ignition (max.), wt% | 0.3 | 0.3 | 0.3 | 4 |
Acidity, g H2SO4/100 g | 0.01 | 0.1 | 0.3 | 0.2 |
Specific surface area, m2/g | 3–8 | 3–10 | 1–5 | 25 (min.) |
4. Uses of Zinc oxide
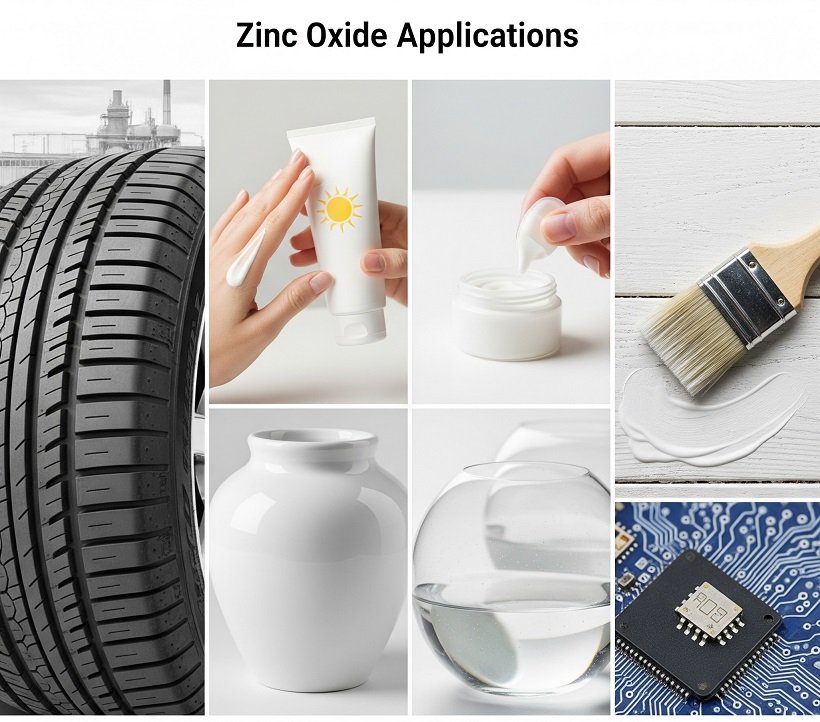
Zinc oxide has many uses. By far the most important is in the rubber industry. Almost half the world’s ZnO is used as an activator for vulcanization accelerators in natural and synthetic rubber.
4.1. Use of zinc oxide in the production of natural and synthetic rubber
The addition of zinc oxide to rubber compounds containing sulfur and accelerators increases cross-link density. For general-purpose rubbers, including natural rubber and styrene-butadiene rubber, ZnO dosages up to approximately 5 phr (parts per hundred rubber) yield high tensile strength and stress values. Higher dosages do not further enhance these properties.
Fatty acids activate the rubber-sulfur-accelerator-zinc oxide system. Stearic acid or zinc stearate is commonly used. The addition of specific zinc salts, in addition to ZnO, can increase cross-link density and improve reversion behavior.
The reactivity of zinc oxide depends on its specific surface area, but the presence of impurities, such as lead and sulfates, also influences it. Zinc oxide ensures good vulcanized rubber durability and also increases its thermal conductivity. Usually, ZnO content ranges from 2% to 5%.
4.2. Use of zinc oxide in paint and coatings
Zinc oxide is no longer the primary white pigment in paints and coatings. However, it is still used by artists for its excellent white color. It is used as an additive in exterior wood preservation paints and in antifouling and anti-corrosion paints.
Zinc oxide is usually combined with other active anticorrosive pigments. Its inhibiting property is based on its ability to react with corrosive substances and to maintain an alkaline pH within the coating. It also reacts with acidic binder components to form soaps and absorbs ultraviolet (UV) light.
Commercial zinc oxide’s lead content varies by manufacturer, ranging from 0.002% to 1.5%. A lead-free zinc oxide coating requires a lead content below 1.5%.
Zinc oxide improves film formation, durability, and mildew resistance. It shows a synergistic effect with other fungicides because it can react with the acidic products of oxidation, and it can absorb UV radiation.
4.3. Use of zinc oxide in the pharmaceutical and cosmetic industries
The pharmaceutical and cosmetic industries use zinc oxide in powders and ointments because it has bactericidal properties. It was also used to form dental cements by reaction with eugenol, but now they are rarely used.
Reactive components, ZnO and eugenol (80−96 wt%), are supplied as two pastes. Oils (e.g., olive oil, mineral oil) and fillers (e.g., talc, kaolin, rosin, vaseline) adjust consistency. Zinc acetate and magnesium chloride are used as accelerators for zinc eugenolate formation.
Zinc oxide is also used as a UV-shielding additive for cosmetics. It is used as sunscreen on and in the horny layer. It acts as ‘‘physical’’ light filters, mainly by reflecting and scattering both UVA and UVB radiation, providing broad-spectrum protection. Micronized and nano-scale ZnO are often used to reduce the visible white residue.
It is used as a white pigment for the production of of colored powders and pearl pigments such as eyeshadow powder.
Zinc oxide is used in various skin products because of its soothing, astringent, and antiseptic properties. Examples include diaper rash creams, calamine lotion, antiseptic ointments, and acne treatments.
4.4. Use of zinc oxide in the ceramic and glass industry
Zinc oxide is used in the industry of glass, ceramics, and enamels to lower melting points and improve gloss, brilliance, and crack resistance (preventing crazing and shivering). It can also be used to modify gloss or to improve opacity.
Higher concentrations of ZnO can produce matte and crystalline surfaces. Its high heat capacity and thermal conductivity are beneficial for ceramic production.
4.5. Use of zinc oxide as a raw material
Zinc oxide is used as a raw material for different products, including stearates, phosphates, chromates, bromates, organic dithiophosphates, and ferrites (ZnO, MnO, Fe2O3). It is also used in electrogalvanization (specifically in cyanide bath formulations).
Zinc oxide is used as a source of zinc in animal feeds and also for desulfurizing gases.
Zinc oxide is used as a catalyst in organic syntheses, such as methanol production, often in conjunction with other oxides. It is also a component in some adhesives.
4.6. Use of zinc oxide in electronics
Highest purity ZnO, calcined with additives like bismuth oxide (Bi2O3), is used in the production of varistors, which are characterized by voltage-dependent resistance, i.e., non-ohmic behavior.
A typical composition includes 96.5 mass% ZnO, 0.5% Bi2O3, 1% CoO, 0.5% MnO, 1% Sb2O3, and 0.5% Cr2O3. The nonohmic behavior results from semiconducting ZnO grains and a thin insulating grain-boundary phase.
A metal oxide varistor based on bismuth-doped ZnO is superior to the classic silicon carbide (SiC) varistors because its voltage-current characteristics have a much lower slope, resulting in a much lower voltage rise per unit current increase.
The photoconducting properties of ZnO are utilized in photoreproduction processes. Doping it with alumina reduces the electrical resistance, and so it can be used in coatings on master papers for offset reproduction.
Zinc oxide is a wide-bandgap semiconductor (3.3 eV). This property makes it suitable for:
- UV lasers and LEDs, particularly for short-wavelength optoelectronic applications.
- Gas sensors, due to its sensitivity to various gases.
- Transparent conductive electrodes in devices like solar cells (e.g., as a buffer layer in CIGS solar cells).
- Transistors and diodes.
- Piezoelectric devices, explored for sensors and energy harvesting.
5. Toxicology of Zinc Oxide
Unlike other heavy metals, zinc is not classified as inherently toxic or dangerous. It is an essential element for human, animal, and plant physiology. The human body contains approximately 2 g of zinc. A daily intake of 10−20 mg is recommended.
The oral LD50 for rats is 630 mg/kg. Workplace air concentrations for zinc oxide dust are permitted at 5 mg/m³ (MAK) and 10 mg/m³ (TLV-TWA). For zinc oxide fumes, values are 5 mg/m³ (TLV-TWA) and 10 mg/m³ (TLV-STEL).
Occupational Exposure Limits (OELs) for zinc oxide are detailed in Table 3.
Country | 8-h TWA, mg/m3 | 15-min STEL, mg/m3 | References |
---|---|---|---|
USA | 5 (fumes), 10 (dust) | 10 (fumes) (ceiling) | ACGIH (1991, guidance values) |
USA | 5 (fumes), 15 (dust; total), 5 (dust; respirable) | OSHA (1989, legal limit values) | |
The Netherlands | 5 (fumes) | SZW (1997) | |
Germany | 5 (fumes), 6 (dust) | DFG (1997) | |
UK | 5 (fumes), 10 (dust) | HSE (1998) | |
Sweden | 5 (fumes) | National Board of Occupational Safety and Health, Sweden (1993) | |
Denmark | 4 (fumes), 10 (dust) | Arbejdstilsynet (1992) |
Accidental ingestion or inhalation of large ZnO quantities can induce fever, nausea, and respiratory tract irritation after several hours. These symptoms are transient and disappear rapidly without long-term consequences.
References
- Pigments, Inorganic, 2. White Pigments. – https://onlinelibrary.wiley.com/doi/10.1002/14356007.n20_n01.pub2
- Rubber, 9. Chemicals and Additives. – https://onlinelibrary.wiley.com/doi/10.1002/14356007.a23_365.pub3
- Pigments, Inorganic, 5. Anticorrosive Pigments. – https://onlinelibrary.wiley.com/doi/10.1002/14356007.n20_n04
- Pigments, Inorganic, 7. Transparent Pigments. – https://onlinelibrary.wiley.com/doi/10.1002/14356007.n20_n06
- Dental Materials. – https://onlinelibrary.wiley.com/doi/10.1002/14356007.a08_251.pub2
- Skin Cosmetics. – https://onlinelibrary.wiley.com/doi/10.1002/14356007.a24_219
- Ceramics, Electronic. – https://onlinelibrary.wiley.com/doi/10.1002/14356007.a06_079.pub2
- The effect of formulation on the penetration of coated and uncoated zinc oxide nanoparticles into the viable epidermis of human skin in vivo
- Zinc Compounds. – https://onlinelibrary.wiley.com/doi/10.1002/14356007.a28_537.pub2