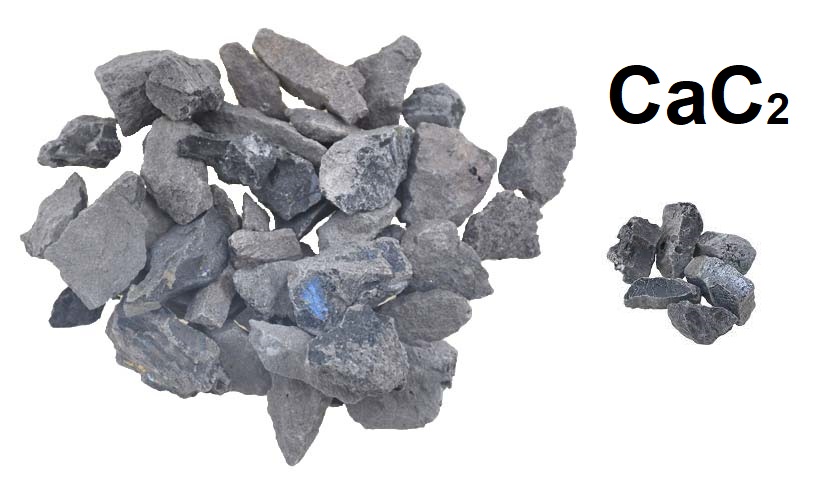
El carburo de calcio, también conocido como acetiluro de calcio, es un compuesto cristalino de color negro grisáceo con la fórmula química CaC2. Al entrar en contacto con el agua, genera acetileno, un gas altamente inflamable que alguna vez se usó ampliamente para iluminación y soldadura.
Entre los carburos, el carburo de calcio destaca como el de mayor importancia industrial (número CAS: 75-20-7). Sigue siendo un material esencial de la industria del gas de soldadura de acetileno, particularmente en regiones donde las materias primas y la energía están fácilmente disponibles y el petróleo es escaso.
Tabla de contenido
El carburo de calcio se fabrica en numerosos países como precursor de diversos productos a base de acetileno, en particular poli(cloruro de vinilo) (PVC) y en la producción de cianamida cálcica.
También se utiliza en la desulfuración de metales fundidos como el hierro y el acero, así como en prácticas de fundición, donde forma parte de los aditivos para el tratamiento de metales.
La composición química del carburo de calcio fue identificada por primera vez por Wöhler en 1862, lograda mediante la reacción de una aleación de calcio-zinc y carbón. Antes de esto, varios investigadores habían preparado el compuesto en entornos de laboratorio, a menudo utilizando arcos eléctricos sobre carbón o productos de coque en presencia de compuestos de calcio.
A finales del siglo XIX se desarrolló la producción a escala industrial de hornos electrotérmicos. Moissan en Francia y Morehead y Willson en Estados Unidos sentaron de forma independiente las bases para este salto tecnológico entre 1885 y 1895. El primer horno industrial de carburo operativo, construido por Willson Aluminium Company en Spray, EE. UU., surgió en 1895.
Bertolus propuso el uso de corrientes eléctricas multifásicas para hornos industriales en 1897. Helfenstein hizo lo mismo en 1904 con un horno de corriente trifásica equipado con tres electrodos. Estos primeros hornos, con capacidades que oscilaban entre 3.000 y 7.500 kW, incorporaban incluso sistemas de recuperación de gases residuales (barrera de Helfenstein). En un siglo, los hornos de 40 MW se volvieron habituales.
Los grandes hornos eléctricos modernos, capaces de manejar hasta 60 MW, emplean electrodos Soderberg y están completamente cerrados, lo que permite la recuperación de subproductos de monóxido de carbono. Los avances recientes se han centrado en el desarrollo de hornos cerrados fiables y de tamaño mediano que se adaptan mejor a las demandas del mercado y a las materias primas disponibles.
El proceso carbotérmico, empleado por BASF en Alemania entre 1940 y 1960, proporcionó una ruta alternativa para la producción de carburo de calcio, pero desde entonces ha sido abandonado.
1. Propiedades físicas del carburo de calcio
El carburo de calcio, CaC2, es un compuesto iónico binario con una masa molar de 64,10 g/mol. En su forma pura es incoloro e inodoro. Sin embargo, el material de calidad técnica a menudo presenta varios tonos de gris a negro parduzco, ocasionalmente con tonos violetas o marrón rojizo, debido a las impurezas.
El olor característico a fosfina del carburo de calcio de grado técnico proviene de trazas de fosfuro de calcio que reaccionan con la humedad.
El carburo de calcio puro posee un alto punto de fusión de 2160°C y se descompone completamente por encima de 2500°C. Existen cuatro modificaciones cristalográficas distintas:
- Fase I: tetragonal, estable entre 25 y 440 °C (dominante en carburo comercial)
- Fases II y III: simetría más baja, estable por debajo de 440°C
- Fase IV: cúbica centrada en las caras, estable por encima de 440 °C
El calor de transformación a 440°C es 8,68 J/g. Cabe destacar que el diagrama de fases CaC2-CaO muestra un comportamiento eutéctico simple, sin formación de compuestos ni soluciones sólidas en estado sólido. Los componentes se vuelven totalmente miscibles sólo por encima de la línea de liquidus. Las impurezas del carburo de grado técnico reducen su temperatura líquida.
El carburo de calcio tiene una capacidad calorífica específica promedio de 1047 J kg⁻¹ K⁻¹ entre 20 y 440°C y un calor de fusión de 1470 J/g para materia pura. Su entalpía estándar de formación a partir de elementos a 298 K es -59,4 kJ/mol y su entropía estándar es 70,3 J mol⁻¹ K⁻¹.
La conductividad eléctrica del carburo de calcio oscila entre 100 y 1000 S m⁻¹ y depende en gran medida de la pureza y la temperatura.
2. Propiedades químicas del carburo de calcio
El carburo de calcio, CaC2, sufre una serie de reacciones químicas importantes:
Síntesis de cianamida cálcica: Esta reacción exotérmica (ΔH₂₉₈ = -289 kJ/mol) convierte el carburo de calcio y el gas nitrógeno en cianamida cálcica y carbono: CaC₂ + N₂ → CaCN₂ + C.
Hidrólisis a acetileno: La reacción con agua produce fácilmente acetileno, hidróxido de calcio y calor (ΔH₂₉₈ = -128,4 kJ/mol): CaC₂ + 2 H₂O → C₂H₂ + Ca(OH)₂.
La producción eficiente de acetileno ocurre por debajo de 300°C, con carburo de calcio puro produciendo 346,89 L/kg (seco) a 0°C y 101,3 kPa (ligeramente más alto a 15°C). C con vapor de agua presente). En su lugar, las altas temperaturas producen óxido de calcio, hidrógeno y dióxido de carbono.
Reacción con azufre: El carburo de calcio reacciona con el azufre en el hierro fundido para formar sulfuro de calcio y liberar carbono: CaC2 + [S]Fe → CaS + 2 [C]Fe.
Hidrogenación: bajo presión, la hidrogenación del carburo de calcio produce no solo hidruro de calcio y metano, sino también otros hidrocarburos.
El carburo de calcio se disuelve en varias sales fundidas, lo que permite diversas reacciones de reducción.
Electrólisis: La electrólisis del carburo de calcio disuelto en sales fundidas produce calcio en el cátodo y carbono en el ánodo.
3. Producción de carburo de calcio
Si bien la preparación de carburo de calcio puro tiene interés académico, su producción industrial prioriza el material de grado técnico para aplicaciones prácticas. Esto depende en gran medida de la reacción a alta temperatura de la cal viva (CaO) con fuentes carbonosas como el coque y la antracita:
CaO + 3 C → CaC2 + CO (ΔH₂₉₈ = +465 kJ/mol)
La velocidad de reacción sólo se vuelve significativa por encima de 1600°C. Sin embargo, superar los 2000°C introduce reacciones secundarias indeseables, en particular:
CaC2 → Ca + 2 C
CaC2 + 2 CaO → 3 Ca + 2 CO
Por lo tanto, los procesos industriales operan dentro del rango de 1800-2100 °C, lo que produce carburo de calcio de grado técnico con aproximadamente un 80 % de contenido de CaC2 . El resto se compone principalmente de CaO, con impurezas adicionales como SiO₂ y Al₂O₃ de las materias primas.
Las altas temperaturas son cruciales para la producción de carburo de calcio y requieren dos posibles enfoques:
- Horno de cuba electrotérmico: Funde el material carbonoso con CaO en un horno corto, introduciendo directamente energía eléctrica.
- Horno de eje de combustión de oxígeno: quema material carbonoso con oxígeno puro o enriquecido en presencia de CaO.
Si bien este último método ofrecía gas de síntesis como subproducto, finalmente fue abandonado después de 50 años debido a la producción más barata del mismo gas a partir del petróleo. Hoy en día, toda la producción comercial de carburo de calcio utiliza el primer enfoque electrotérmico.
3.1. Materias primas
Las materias primas para la producción de carburo de calcio, conocidas como «carga» en el horno electrotérmico, desempeñan un papel crucial en la eficiencia y la calidad del producto. Estos materiales constan de dos componentes principales: una fuente carbonosa y un componente calcáreo.
El tamaño, la resistencia y la conductividad de las partículas afectan significativamente el rendimiento y la estabilidad operativa del horno. Los hornos abiertos más pequeños ofrecen flexibilidad para ajustar estas propiedades de forma manual o mecánica, mientras que los hornos cerrados de alta capacidad requieren especificaciones más estrictas para su funcionamiento sin supervisión.
Los volátiles y el contenido de cenizas influyen en la eficiencia de la reacción y la generación de residuos. Los hornos cerrados modernos permiten la inyección de materiales de grano fino directamente a través de electrodos huecos. Las impurezas como los óxidos metálicos pueden provocar reacciones secundarias indeseables y requieren un manejo cuidadoso.
Fuente de carbono
- Coque: Derivado del carbón bituminoso o lignito, el coque es el principal material carbonoso utilizado a nivel mundial debido a su disponibilidad y propiedades adecuadas. El tamaño de grano suele oscilar entre 3 y 25 mm, y las fracciones más finas se inyectan a través de electrodos. El contenido de humedad debe estar por debajo del 2 % y el contenido de cenizas por debajo del 15 % para una producción óptima.
- Otras opciones: La antracita sin calcinar y el coque de petróleo se pueden usar parcialmente en hornos cerrados, pero requieren calcinación para reducir los volátiles por debajo del 2 % para el lenguado. usar. El carbón vegetal sólo encuentra aplicación en pequeños hornos abiertos.
Componente que contiene cal
- Cal viva: la opción predominante, con grandes hornos cerrados que requieren un tamaño de grano de 6 a 50 mm e inyección de fracciones más finas. El contenido de magnesio debe ser inferior al 2% para un funcionamiento eficiente. La cal debe ser blanda pero duradera, lo que se puede lograr mediante hornos modernos y tener un contenido de CO2 inferior al 2 %.
- Hidróxido de calcio reciclado: este subproducto de la generación de acetileno se puede utilizar como materia prima barata después de la granulación o briquetas, pero se acumulan impurezas. limita su potencial de reciclaje.
Los plásticos de desecho se exploran cada vez más como fuente secundaria de carbono, con especificaciones estrictas sobre el contenido de cloro (máx. 12%) debido a su indeseable vaporización y reacción con el calcio.
Las tablas 1 y 2 proporcionan ejemplos de composiciones típicas de materias primas para la producción de carburo de calcio.
Material | Carbón Fijo | Carbón volátil | Humedad | Azufre | Ceniza |
---|---|---|---|---|---|
Coque metalúrgico | 89,0 | 0,8 | 0,8 | 0,8 | 9.4 |
Antracita | 80.0 | 6.0 | 8.0 | 0,8 | 6.0 |
Coque de petróleo | 81,6 | 9.0 | 8.0 | 1.9 | 0,3 |
Componente | Nueva Lima | Cal reciclada |
---|---|---|
CaO total | 93,8 | 89,0 |
CaO libre | 93,6 | - |
CaSO4 | 0,4 | - |
SiO2 | 1.3 | 2.9 |
Fe2O3 | 0,4 | 0,4 |
Al2O3 | 0,5 | 2.4 |
MgO | 0,8 | 0,8 |
CO2 | 2.7 | 3.0 |
P2O5 | 0,015 | 0,01 |
Pérdida por ignición (CO2) | 0,5 | 0,5 |
3.2. Reducción electrotérmica
La mezcla de materias primas para la producción de carburo de calcio se procesa a alta temperatura en un horno eléctrico de eje corto. Las investigaciones sugieren un mecanismo de reacción de dos pasos:
- Calcinación: CaO + C → Ca + CO
- Formación de carburo: Ca + 2 C → CaC2
La zona de reacción primaria dentro del horno se encuentra en una fase fundida de CaC2 -CaO. Sin embargo, la compleja interacción entre la corriente eléctrica, el suministro de calor, la temperatura y las reacciones químicas aún no se comprende bien.
El paso limitante de la velocidad probablemente implica transportar CaO disuelto en la masa fundida hasta la superficie del grano de coque, donde se produce la formación de CaC2. Este CaC2 recién formado se disuelve fácilmente en la masa fundida.
Finalmente, el carburo de calcio fundido se extrae del fondo del horno.
3.3. Hornos
Los hornos de carburo de calcio se pueden clasificar según tres aspectos clave:
- Suministro eléctrico: Monofásico o trifásico.
- Disposición de los electrodos: Configuraciones en serie, simétricas u otras.
- Exclusión de aire: abierto, semicubierto o cerrado.
1. Hornos Monofásicos
Desarrollados en 1928, estos hornos funcionan con alta corriente y bajo voltaje, logrando factores de potencia de hasta 0,95. Sin embargo, son menos eficientes y han caído en desgracia en comparación con los diseños trifásicos.
2. Hornos Trifásicos
El tipo dominante hoy en día, categorizado por disposición de los electrodos:
- Serie: ofrece ventajas en alimentación y distribución pero limitaciones en recuperación de gas y consumo de energía.
- Simétrico: diseño de alto rendimiento con factores de potencia equilibrados y zonas fundidas superpuestas a mayor potencia.
3. Hornos Semicubiertos
Los primeros hornos expulsaban CO directamente, lo que provocaba contaminación. Los diseños modernos emplean campanas recolectoras de gas, aunque las calderas cerradas ofrecen el mejor control ambiental.
4. Hornos Cerrados
Estos modernos hornos proporcionan una recuperación del 100% del gas y un impacto ambiental mínimo. Los componentes clave incluyen:
- Hogar: Construido con acero y materiales refractarios para soportar altas temperaturas.
- Electrodos: los electrodos Soderberg se prefieren por su rentabilidad y funcionamiento continuo. Los electrodos huecos permiten la inyección directa de materias primas.
- Fuente de alimentación: Transformadores con refrigeración por aceite y salida controlable para gestionar las fluctuaciones.
- Diagrama de potencia: representa la compleja interacción de resistencias y reactancias dentro del horno.
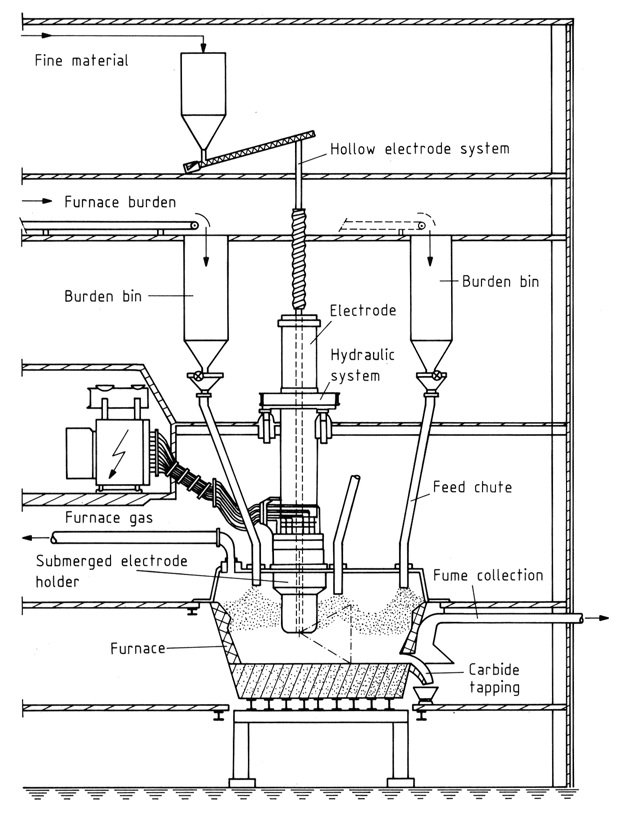
Control y Operación
Los hornos trifásicos requieren control de impedancia ajustando la profundidad de inmersión del electrodo para gestionar la potencia y la resistencia del horno. Las campanas cerradas pueden permitir la manipulación de los conductos de alimentación para regular aún más la resistencia.
3.4. Proceso Industrial
La producción de carburo de calcio comienza con una base de coque grueso en capas dentro del horno. Los electrodos se bajan meticulosamente hacia el coque hasta que los arcos eléctricos señalan el contacto. A medida que el coque alcanza el color rojo, el fondo del horno se alimenta gradualmente con carga y la potencia se eleva gradualmente para igualar el aumento de temperatura.
La alimentación de carga constante es esencial para el funcionamiento óptimo del horno. Las variaciones menores de composición se pueden mitigar mediante la adición de cal, lo que requiere una inmersión más profunda del electrodo debido a la menor conductividad de la cal.
Una altura excesiva del electrodo corre el riesgo de que se forme carburo en las capas de carga superiores, lo que podría provocar peligrosos «chorros» de fusión. Mantener la permeabilidad al gas dentro del material sólido es esencial para una producción constante.
La presión de la campana del horno debe equilibrarse meticulosamente con la presión atmosférica para evitar la intrusión de oxígeno o la fuga de monóxido de carbono. Las configuraciones de hornos a gran escala suelen emplear salas de control centralizadas para un funcionamiento eficiente y un seguimiento exhaustivo de los parámetros ambientales.
El roscado implica abrir mecánicamente el horno o utilizar un arco eléctrico para crear un orificio de roscado. Un electrodo horneado exclusivo facilita la fusión del carburo, que fluye a temperaturas que oscilan entre 1700 y 2100 °C, según la pureza, en cucharas de hierro fundido enfriadas específicamente diseñadas.
Debido a su alto punto de fusión y rápida pérdida de calor, el carburo de grado técnico (80% CaC2) se solidifica rápidamente, lo que requiere un mantenimiento continuo del orificio de roscado con varillas de acero.
Las cortinas de cadena, las redes de alambre y los escudos de acero protegen a los operadores de gases calientes, polvo y chorros de carburo potencialmente peligrosos durante el proceso de roscado. Es obligatorio que todo el personal involucrado en las operaciones de extracción tenga equipo de protección especializado, que incluye abrigos ignífugos cubiertos de aluminio, gafas oscuras y visores protectores.
Los sistemas de extracción de humos eliminan eficazmente las partículas de aerosol nocivas, reduciendo el impacto ambiental.
Los manipuladores hidráulicos modernos equipados con herramientas intercambiables han revolucionado los procedimientos de roscado, minimizando la necesidad de participación humana directa y mejorando la seguridad.
La reducción de impurezas como Fe2O3 y SiO2 por el carbono produce ferrosilicio que, debido a su mayor densidad, se deposita debajo de la masa fundida de carburo y normalmente fluye durante la extracción. Sin embargo, su punto de fusión más bajo en relación con el carburo requiere una vigilancia constante y medidas preventivas para evitar fugas a través de grietas en el revestimiento del horno.
4. Usos del carburo de calcio
El carburo de calcio se utiliza en la producción de acetileno, la reacción con nitrógeno para formar cianamida cálcica y la desulfuración de metales calientes.
Si bien su uso como precursor de productos químicos pesados ha disminuido debido al predominio de los petroquímicos desde la década de 1960, el acetileno derivado del carburo de calcio sigue siendo importante en la soldadura con gas. Su adaptabilidad y portabilidad lo hacen indispensable para tareas como la construcción de tuberías, incluso en medio de avances en las técnicas de unión de materiales.
El acetileno continúa encontrando aplicaciones específicas en la síntesis de sustancias químicas específicas, como butinodiol para plásticos y fibras, y negro de acetileno para baterías secas.
La reactividad del carburo de calcio con el azufre lo convierte en una herramienta valiosa en metalurgia. Los estrictos estándares de calidad del acero exigen un contenido mínimo de azufre, y la desulfuración con carburo de calcio antes del convertidor de producción de acero resulta ser el método más económico.
La inyección de carburo de calcio finamente molido (< 100 mm) en el metal fundido reduce eficazmente el contenido de azufre, normalmente desde un 0,2 % hasta un mínimo de 0,001 %. Se exploran cada vez más combinaciones de carburo de calcio con magnesio para mejorar la reactividad dentro del metal caliente.
En las prácticas de fundición, el carburo de calcio de grano grueso, a menudo combinado con aditivos como el espato flúor, encuentra uso en la desulfuración. La mezcla se agita en el cazo después del roscado y antes de la fundición, lo que contribuye a mejorar la calidad del metal.
5. Toxicología del carburo de calcio
El carburo de calcio está clasificado como irritante grave para los ojos y la piel, con bajo potencial de sensibilización.
El carburo de calcio de calidad comercial puede provocar daños agudos por inhalación debido a sus propiedades corrosivas/irritantes.
Se dispone de datos limitados sobre el carburo de calcio en sí, pero ciertos componentes traza generan preocupación:
- Fosfina: existe evidencia genotóxica, pero su baja concentración en carburo de calcio (< 0,1%) minimiza el riesgo.
- Arsénico: aunque está presente en < 0,1%, este carcinógeno potencial puede generar arsina al entrar en contacto con el agua. Sin embargo, los criterios CLP actuales no requieren la clasificación como carcinógeno.
Debido a los bajos niveles de arsénico y su limitada conversión en arsina, no se justifica la clasificación como carcinógeno.
Debido a su rápida descomposición en agua, la ecotoxicidad del compuesto puro es insignificante.
Los estudios sobre peces, dafnias y algas proporcionan información sobre la toxicidad de los productos de descomposición y los componentes menores.
La CL50 alta para peces (>50 mg/L) y la CE50 para Daphnia (4,42 mg/L) probablemente reflejan la toxicidad del sulfuro de hidrógeno, producido a partir de la impureza sulfuro de calcio.
En general, los estudios de biodegradación sugieren propiedades fácilmente biodegradables del carburo de calcio y sus productos de degradación.
Referencia
- Calcium Carbide; Ullmann’s Encyclopedia of Industrial Chemistry. – https://onlinelibrary.wiley.com/doi/10.1002/14356007.a04_533.pub2