Ziegler Processes refer to a group of chemical reactions or processes developed by Karl Ziegler, a German chemist. These processes are primarily used in the production of polymers and organic compounds.
Table of Contents
1. Ziegler Direct Process
The synthesis of aluminum trialkyls AlR3 and dialkylaluminum hydrides R2AlH is a significant process accomplished through the Ziegler direct method. This loop process involves two simultaneous reactions called hydrogenation and hydroalumination.
During the hydrogenation step, aluminum reacts with hydrogen in the presence of AlR3, resulting in the formation of dialkylaluminum hydrides. The hydroalumination step involves the addition of an olefin to the aluminum hydride.
In the case of triethylaluminum, the reactions take place as follows:
Hydrogenation:

Hydroalumination:

Overall reaction:
Al + 1.5 H2 + 3 CH2=CH2 → AlEt3
The overall reaction results in the formation of aluminum trialkyls from activated aluminum powder, hydrogen, and α-olefins. The reaction can be directed towards the formation of trialkyls or dialkyl hydrides by varying the aluminum/olefin ratio.
The alkyl group can be altered, with n-butyl and isobutyl compounds, along with ethyl compounds, being manufactured on an industrial scale.
The Ziegler direct synthesis is a continuous process and can be carried out in one or two stages. The availability of triethylaluminum, which is easily obtained through this process, played a crucial role in the development of stoichiometric and catalytic reactions of AlEt3, which are described in subsequent sections.
2. Ziegler Olefin Synthesis
During the early 1950s, Ziegler made a significant finding known as the “growth reaction.” This reaction involves the repeated insertion of ethylene into aluminum-ethyl bonds, resulting in the formation of long-chain aluminum trialkyls. These trialkyls can then be used in a subsequent displacement reaction to produce long-chain alpha-olefins.
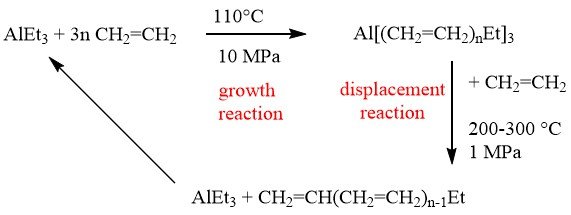
The Ziegler growth reaction involves the repeated insertion of ethylene into aluminum-ethyl bonds leading to the formation of long-chain aluminum trialkyls, which are subsequently displaced to produce long-chain alpha-olefins.
Gulf Oil and Ethyl Corporation have successfully scaled up this process for industrial applications.
In the Gulf Oil Process, catalytic quantities of triethylaluminum are used, and both the growth and displacement reactions occur in a single reactor. The resulting product, called “Gulftenes,” has a broad molecular mass distribution of linear C4-C30 olefins.
The Ethyl process, on the other hand, involves two successive steps, with the first step also using catalytic amounts of triethylaluminum to produce a broad distribution of olefins. The short-chain olefins are then fractionally distilled and reacted with stoichiometric amounts of aluminum trialkyls in the second step.
Ethyl Corporation has successfully implemented this process at its plant in Pasadena, Texas.
3. Ziegler Alcohol Synthesis
The Ziegler method can also be used for the production of alcohols. In this process, the aluminum trialkyls formed are oxidized by atmospheric oxygen to form aluminum trialkoxides. These trialkoxides are then hydrolyzed to yield the long-chain alcohols:
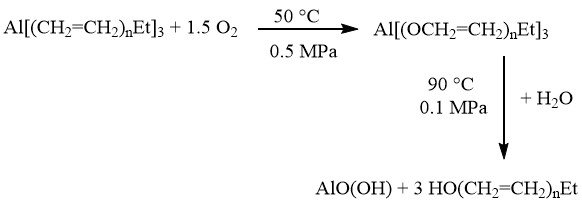
3.1. The Alfol Process
The Ziegler alcohol synthesis was first realized on an industrial scale by Conoco, who built an Alfol plant in Lake Charles, United States in 1962. This plant is currently operated by Vista Chemical. In 1964, a similar plant was constructed by Condea-Chemie in Brunsbüttel, Germany.
The alcohols produced in this process with chain lengths of C12, C14, and C16 are of particular interest, as they can be sulfated to form fatty alcohol sulfates with excellent biodegradability.
However, the Alfol Process, like the Gulf Oil Process for Ziegler olefins, produces a mixture of products with a broad Poisson distribution.
Aluminum oxides are coproduced and have significant industrial applications as starting materials for catalysts and ceramics.
3.2. The Epal Process
The Epal process, which is based on the principle of the Ethyl olefin process, is a development of the Ethyl Corporation. Fractional distillation is employed to obtain an alcohol mixture with a considerably narrower distribution of homologues, such as in the desired C12-C16 range, after growth reactions.
The hydrolysis that follows the oxidation step is performed with sulfuric acid, resulting in high-purity aluminum sulfate as a byproduct. The Ethyl Corporation plant in Pasadena, Texas, can produce both alcohols and olefins, but the flexibility requires a complex plant, leading to high capital and operating costs.
4. Ziegler Catalysts
4.1. Catalyst Systems
The terms Ziegler catalysts and Ziegler-Natta catalysts refer to a general range of catalyst systems formed by mixing the following building blocks in an inert solvent:
1) An organometallic compound of a metal from groups 1, 2, or 13 (such as aluminum trialkyl).
2) A compound of a transition metal from groups 4-8 (such as titanium tetrachloride).
Polynuclear complexes are formed from these two components. The structure and function of various Ziegler catalysts continue to be the subject of debate in the literature.
A fundamental experiment with bis(cyclopentadienyl)titanium dichloride and diethylaluminum chloride isolated a binuclear complex with a vacant coordination site on the titanium:
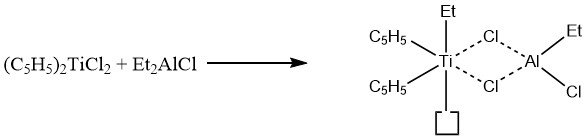
It is assumed that coordination of unsaturated molecules, such as ethylene, occurs at a specific site on titanium before the molecule is inserted into a titanium-ethyl bond, resulting in the creation of a new vacant coordination site.
The process can be repeated indefinitely, leading to the formation of long-chain polymers, while a breakdown of the chain mechanism results in the formation of oligomers.
4.2. Oligomerization with Ziegler Catalysts
In 1952, Holzkamp discovered the first oligomerization using a Ziegler catalyst system at the Max Planck Institut für Kohlenforschung, which involved a growth reaction with aluminum alkyls and ethylene with the addition of nickel salts.
The Ni-Al catalyst system exclusively produced ethylene dimers, or butenes, instead of a broad distribution of α-olefins, which marked the birth of Ziegler catalysts.
Ziegler catalysts based on various compounds, including titanium, zirconium, chromium, tungsten, cobalt, and palladium, can be used for the oligomerization of ethylene, with butenes being the main product in most cases.
Ziegler catalysts can also be used for the oligomerization of propene, butene, and 1,3-dienes, such as butadiene, to produce higher olefins such as vinylcyclohexene and 1,5-cyclododecatriene.
Ligands can be added to control the course of the reaction.
4.3. Polymerizations with Ziegler Catalysts
The most important application of Ziegler catalysts is in the synthesis of polyolefins. The first catalysts for the polymerization of ethylene were based on β-titanium trichloride, which was produced in situ from TiCl4 and aluminum ethyl chlorides.
Since 1969, MgCl2-supported Ziegler catalysts have been used, which possess considerably greater activity.
Natta first used the Ziegler catalyst TiCl4/AlEt3 with propene in 1954, which was found to be stereoselective, producing crystalline isotactic polypropylene.
Metallocenes activated by methylaluminoxane are a further important development in Ziegler catalysts, discovered in the 1970s by Kaminsky and Sinn at the University of Hamburg.
The hypothesis that the catalytically active species is an ion pair consisting of a metallocene cation and a stabilized methylaluminoxane anion is currently under discussion.
These catalyst systems have led to a new breakthrough in the synthesis of polypropylene, with the use of bridged bis(indenyl)zirconocenes enabling isotactic polypropylene to be produced with extremely high catalyst activities and stereoselectivities.
Reference
- Ziegler Processes; Ullmann’s Encyclopedia of Industrial Chemistry. – https://onlinelibrary.wiley.com/doi/10.1002/14356007.a28_505