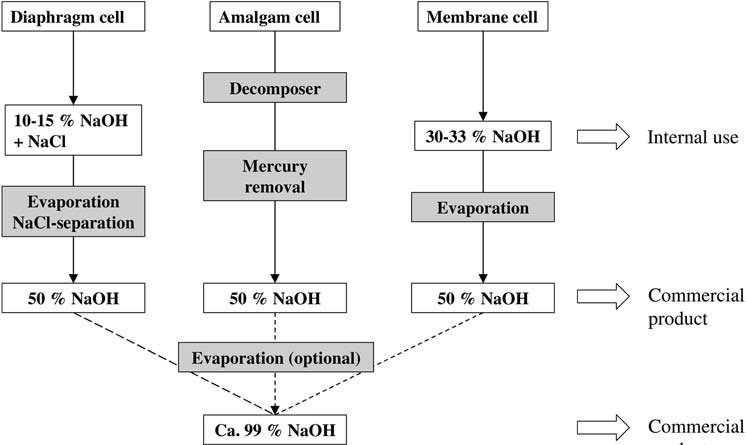
1. Electrolysis of Sodium Chloride
The industrial production of sodium hydroxide solution primarily involves the electrolysis of sodium chloride.
The reaction yields sodium hydroxide solution, chlorine gas, and hydrogen gas in the mass ratio of 1: 0.88: 0.025, as represented by the overall equation:
2 NaCl + 2 H2O → 2 NaOH + Cl2 + H2
The membrane process was introduced in the early 1980s as an alternative to the amalgam and diaphragm processes for chlor-alkali production.
In 2004, the membrane process accounted for more than 44% of the total installed chlor-alkali capacity. This process saves approximately 30% of electrical power and is considered the best available technique, leading to an increasing use of the technology in new units.
In Japan, the amalgam process was phased out, and some diaphragm plants were replaced by membrane plants due to cost and quality considerations by 1988.
In the amalgam process, sodium hydroxide solution is produced from sodium amalgam and water over a graphite catalyst at 80 – 120 °C, yielding a 50 wt% solution that is cooled, and then sold without further treatment after mercury is removed by centrifugation or filtration.
The diaphragm cell produces a solution containing approximately 18 wt% sodium chloride and 10-15 wt% sodium hydroxide.
During evaporation, impurities carried over with the depleted sodium chloride solution are removed to their limiting solubility by fractional crystallization, and the sodium chloride content can only be reduced to around 1 – 1.5 wt%.
The membrane process involves the use of a hydraulically impermeable membrane to prevent mixing of the electrolytes.
This process produces a high-purity, virtually chloride-free sodium hydroxide solution comparable to that of the amalgam process. However, the chloride content increases by a factor of approximately 10 if cell operation is interrupted due to diffusion of Cl‾ ions through the membrane.
The sulfate and chlorate present in the anolyte also affect the concentration of impurities in the caustic liquor from the membrane cell. This is because the cation-selective membrane has an appreciable residual permeability for anions. Most membrane cells give optimum economic performance at a NaOH concentration of 30 – 35 wt%.
An ion-exchange membrane has been developed that allows for the production of a 50 wt% sodium hydroxide solution in the cell, but at the expense of a considerable increase in voltage. Such membranes are only feasible if steam costs are high and electricity costs are low.
The 30 – 33 wt% sodium hydroxide solution is typically concentrated in a two- or three-stage falling-film evaporator, depending on steam costs and plant size, to give a commercial 50 wt% solution.
The steam consumption for a three-stage evaporator is 0.55 t per ton NaOH (100%), and for a two-stage evaporator, it is 0.71 t per ton NaOH (100%), with the sodium hydroxide solution and steam in counter current flow.
Unlike diaphragm cell liquor, the evaporation of membrane cell liquor does not produce any solid material that can foul the heat exchanger or erode the pipework.
The pickup of metals during evaporation is approximately 1 wt ppm if appropriate construction materials such as nickel and stainless steel are used.
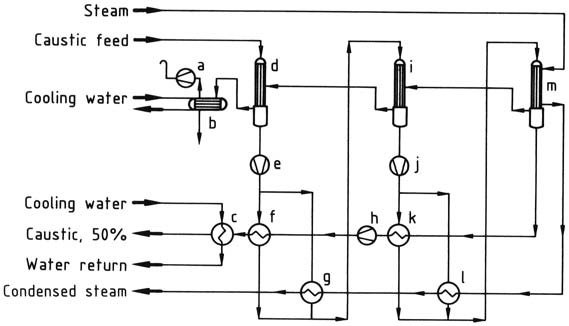
The three different electrolytic processes used to produce sodium hydroxide have varying energy requirements.
The membrane process demands the least amount of electrical energy, which ranges from 2200 to 2500 kWh per ton NaOH. However, to generate a 50 wt % solution, an extra 200-300 kWh per ton NaOH in the form of steam is necessary.
In contrast, the diaphragm process uses less electrical energy than the amalgam process, but it necessitates 700-900 kWh per ton NaOH for the evaporation stage. As a result, the diaphragm process has the highest total energy consumption.
Due to the high demand for electrical energy, researchers have focused on reducing the cell voltage. The membrane cell process can achieve a voltage reduction of approximately 1 V by using an oxygen diffusion cathode, similar to a fuel cell. Nonetheless, in this case, no hydrogen byproducts are generated.
This technology has piqued significant interest. The development of cell design, oxygen diffusion cathodes, and their integration into the cell design are primary areas of focus. Research efforts are also directed toward exploring operational parameters and cell peripherals.
The electrolysis of fused NaCl at 350°C with a β-Al2O3 diaphragm is a promising technique. Laboratory-scale cells have achieved a power consumption of 2350 kWh per ton NaOH. Nevertheless, this technique has yet to be used on a commercial scale.
2. Other Processes
- The production of sodium hydroxide using the causticization of sodium carbonate solution is the oldest known method. It was the sole available method until the advent of electrolysis. This method has regained interest amongst companies that have access to synthetic or natural sodium carbonate.
In this process, a hot solution of approximately 12% sodium carbonate is combined with quicklime. The precipitated calcium carbonate is eliminated, and the approximately 12% sodium hydroxide solution is evaporated in several stages.
Na2CO3 + CaO·H2O → 2 NaOH + CaCO3
Impurities that precipitate, including NaCl and Na2SO4, are filtered off.
- Combining electrolytic and dialysis cells is a way to split sodium salts into the corresponding acids and alkalis:
Na2SO4 + 2 H2O → 2 NaOH + H2SO4
In a two-chamber cell, a cation or anion exchange membrane can be used. In a three-chamber cell, a cation-exchange and an anion-exchange membrane can be employed. Alternatively, a multichamber cell can be used, which utilizes a combination of cation, anion, and bipolar membranes.
However, all industrially operated cells yield a diluted sodium hydroxide solution (15-30 wt %) containing some starting material salt.
Therefore, this type of process is most suited for treating sodium-salt containing wastewater from processes in which the obtained dilute sodium hydroxide solution can be recycled for neutralization purposes.
- The ferrite recovery process provides an alternative way of producing sodium hydroxide solution suitable for small paper pulp plants.
This process involves evaporating waste liquor containing sodium salts and organic substances. The resulting residue is mixed with Fe2O3 and calcined, forming sodium ferrite that, when decomposed by water, yields NaOH and Fe2O3.
References
- Sodium Hydroxide; Ullmann’s Encyclopedia of Industrial Chemistry. Weinheim: Wiley-VCH.- https://onlinelibrary.wiley.com/doi/10.1002/14356007.a24_345.pub2