
Wat is koolstofdisulfide?
Koolstofdisulfide is een kleurloze vloeistof met de formule CS2. Het is een belangrijke chemische verbinding die veel wordt gebruikt in verschillende industriële toepassingen.
De ontdekking van koolstofdisulfide kan worden toegeschreven aan Lampadius in 1796, die het ontdekte toen hij een combinatie van ijzerpyriet en koolstof verhitte.
De verbinding wekte al in 1839 industriële interesse, toen Schrötter het met succes synthetiseerde met behulp van houtskool en zwavel in een verhitte retort. De opmerkelijke oplossende capaciteiten van koolstofdisulfide werden snel herkend, wat leidde tot wijdverbreid gebruik bij de extractie van vetten en oliën gedurende een aanzienlijke periode.
De ware betekenis ervan als grootschalige industriële chemische stof kwam echter aan het licht met de komst van het viscose-rayonproces in het begin van de jaren 1900. Dit proces vertrouwde op koolstofdisulfide om cellulose op te lossen, waardoor het een cruciale rol in de industrie kreeg.
Niettemin kreeg de snelle groei van rayon eind jaren zestig te maken met tegenslagen door concurrentie van op aardolie gebaseerde synthetische vezels, wat resulteerde in een daaropvolgende daling van zowel de rayon- als de koolstofdisulfidemarkt in de jaren zeventig. De laatste tijd is het gebruik van koolstofdisulfide echter gestabiliseerd en wordt er een kleine marktgroei voor de toekomst voorspeld.
In 1984 werd van de totale wereldwijde productie van 1,1 miljoen ton koolstofdisulfide meer dan 75% voornamelijk verbruikt door de industrie voor geregenereerde cellulose. Het resterende deel vond zijn toepassing in de productie van koolstoftetrachloride en diverse organozwavelverbindingen, die op grote schaal worden gebruikt als rubberchemicaliën, flotatiemiddelen en pesticiden.
Inhoudsopgave
1. Fysische eigenschappen van koolstofdisulfide
Koolstofdisulfide is een zeer vluchtige vloeistof met een aanzienlijke dichtheid, die een breed ontvlambaarheidsbereik vertoont in aanwezigheid van lucht, variërend van 1 tot 50 volumeprocent. Het bezit een uitzonderlijk lage zelfontbrandingstemperatuur van 100 °C en een vlampunt van -30 °C. De verdampingssnelheid in de atmosfeer overtreft die van di-ethylether met een factor 1,6.
Deze verbinding dient als een uitzonderlijk oplosmiddel voor talrijke organische stoffen, en lost zwavel, fosfor, jodium, wassen, rubber en harsen gemakkelijk op. De commercieel verkrijgbare vorm verspreidt een scherpe geur, kenmerkend voor op zwavel gebaseerde verbindingen.
Enkele van de meest bruikbare fysische eigenschappen van koolstofdisulfide zijn als volgt:
- Molaire massa = 76,13 g/mol
- Smeltpunt = -111,6 °C
- Kookpunt = 46,23 °C
- Dichtheid bij 25 °C = 1,26 g/ml
- Kritische temperatuur = 273 °C
- Kritische druk = 7600 kPa
- Oppervlaktespanning bij 20 °C = 32,3 mN/m
- Breukindex bij 20 °C = 1,62546
- Viscositeit bij 25 °C = 0,36 mPa.s
2. Chemische reacties van koolstofdisulfide
Koolstofdisulfide vertoont een breed scala aan chemische reacties die uitgebreid zijn bestudeerd en gedocumenteerd.
Wanneer koolstofdisulfide reageert met sulfiden, alcoholen, ammoniak, aminen en chloor, genereert het industrieel belangrijke derivaten en tussenproducten. In de aanwezigheid van waterige alkaliën reageert koolstofdisulfide langzaam om trithiocarbonaat- en carbonaatverbindingen te vormen, zoals weergegeven door de vergelijking:
3 CS2 + 6 NaOH → 2 Na2CS3 + Na2CO3 + 3 H2O
Metaalsulfiden vormen trithiocarbonaten wanneer ze reageren met koolstofdisulfide, zoals blijkt uit de reactie:
K2S (waterig) + CS2 → K2CS3
Bovendien ontstaan er bij de reactie van koolstofdisulfide met alcoholische alkaliën xanthaten, zouten van dithiocarbonaten, via het volgende proces:
ROH + NaOH → RONa + H2O
RONa + CS2 → ROCSSNa
Deze reactie vormt de basis voor het viscoseproces, waarbij cellulose wordt omgezet in xanthaat en vervolgens wordt geregenereerd tot vezels en films, zoals blijkt uit de volgende reactie:
(cellulose)ONa + CS2 → (cellulose)OCSSNa
2 (cellulose)OCSSNa + H2SO4 → 2 (cellulose)OH + 2 CS2 + Na2SO4
In aanwezigheid van ammoniak vormt koolstofdisulfide ammoniumdithiocarbamaat (1), ammoniumtrithiocarbonaat (2) en ammoniumthiocyanaat (3), afhankelijk van de concentratie ammoniak en de temperatuur:
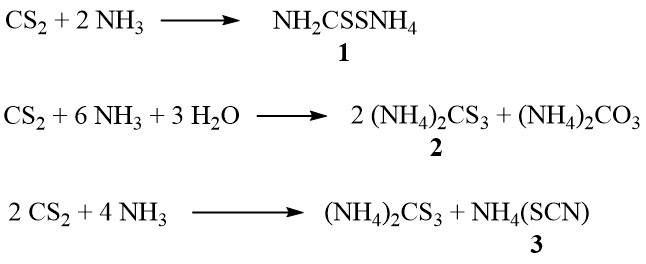
Bovendien ontleedt het thiocyanaat bij hogere temperaturen in de dampfase tot thioureum:
NH4(SCN) → SC(NH2)2
Primaire en secundaire aminen leveren bij hun reactie met koolstofdisulfide voornamelijk dithiocarbamaatzouten op:
2 RNH2 + CS2 → RNHCSSNH3R
2 R2NH + CS2 → R2NCSSNH2R2
In aanwezigheid van alkaliën kunnen verschillende commercieel belangrijke zouten van dithiocarbaminezuur worden verkregen:
R2NH+ CS2 + NaOH → R2NCSSNa + H2O
De reactie van koolstofdisulfide met methylamine en natronloog in een waterige oplossing produceert natriummethyldithiocarbamaat (CH3NHCSSNa), een essentieel bodemontsmettingsmiddel. Op soortgelijke wijze reageert koolstofdisulfide met ethyleendiamine om het fungicide natriumethyleenbis(dithiocarbamaat) te verkrijgen:

Aniline– en koolstofdisulfidereacties resulteren in de vorming van twee belangrijke vulkanisatieversnellers. Bij afwezigheid van zwavel wordt thiocarbanilide geproduceerd, terwijl bij aanwezigheid van zwavel 2-mercaptobenzothiazol wordt verkregen:
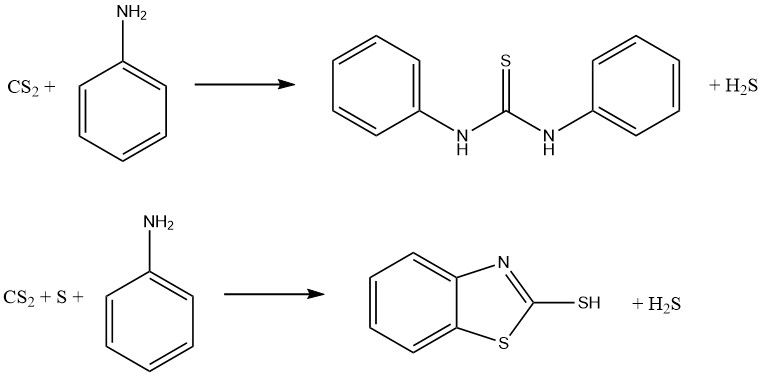
Dithiocarbamaten kunnen worden geoxideerd om een familie van verbindingen te vormen die bekend staan als thiuriumdisulfiden, die worden gebruikt als fungiciden en vulkanisatieversnellers. De reactie omvat de volgende vergelijking:
2 R2NCSSNa + H2O2 + H2SO4 → (R2NCSS–)2 + Na2SO4 + 2 H2O
Chlorering van koolstofdisulfide leidt tot de vorming van verschillende gechloreerde producten. Onder jodiumkatalyse produceert chlorering bij temperaturen tussen 5 en 30 °C trichloormethaansulfenylchloride, samen met koolstoftetrachloride, zwaveldichloride en thiofosgeen, afhankelijk van de mate van chlorering.
In aanwezigheid van ijzer- en metaalchloriden bij hogere temperaturen (70 – 100 °C) worden uitsluitend koolstoftetrachloride en zwavelchloriden verkregen.
Koolstofdisulfide reageert gemakkelijk met water in aanwezigheid van alumina en oxidekatalysatoren boven 150 °C, waarbij koolstofdioxide en waterstofsulfide worden geproduceerd. Carbonylsulfide fungeert als een intermediair in deze hydrolysereactie. Bij temperaturen variërend van 200 tot 300 °C bereikt de omzetting van koolstofdisulfide in deze producten een evenwicht.
Wanneer koolstofdisulfide wordt blootgesteld aan hoge temperaturen (boven 150 – 200 °C) in aanwezigheid van metaalsulfidekatalysatoren zoals molybdeen- en nikkelsulfiden, ondergaat het koolstofdisulfide reductie door waterstof, wat resulteert in wisselende hoeveelheden methaanthiol, dimethylsulfide, methaan en waterstofsulfide.
3. Productie van koolstofdisulfide
Koolstofdisulfide wordt geproduceerd door de reactie van zwavel met houtskool of methaan. Hoewel ethaan, propaan en propeen in beperkte mate zijn gebruikt, heeft het methaanproces sinds de introductie ervan in het begin van de jaren 50 aanzienlijk aan populariteit gewonnen.
Bijgevolg is het oudere houtskoolproces niet langer relevant voor de productie van koolstofdisulfide in de Verenigde Staten, Europa en Japan. In regio’s waar aardgas of methaan niet gemakkelijk toegankelijk is of wanneer de fabrieksgrootte relatief klein is, wordt het houtskoolproces echter nog steeds gebruikt om te voldoen aan de lokale vraag naar de productie van viscose rayon.
3.1. Productie van koolstofdisulfide uit houtskool en zwavel
Het fundamentele proces voor de reactie van houtskool met zwavel heeft minimale veranderingen ondergaan sinds de introductie halverwege de jaren 1840. Extern verwarmde retorten worden nog steeds gebruikt, hoewel het ontwerp van de apparatuur aanzienlijk is verbeterd met de beschikbaarheid van superieure bouwmaterialen.
In retortinstallaties wordt gesmolten zwavel verdampt en oververhit, hetzij vóór of nadat het in de retort is gebracht. In de retort, bij temperaturen variërend van 850 tot 900 °C en iets boven de atmosferische druk, reageert de oververhitte zwaveldamp met een stationair bed van houtskool.
Het resulterende productgas, dat koolstofdisulfide, zwavel, waterstofsulfide, carbonylsulfide en inerte gassen omvat, gaat door een reeks condensors, scrubbers en olie-absorbers om ruwe koolstofdisulfide terug te winnen.
Verdere behandeling in destillatiekolommen levert het zuivere product op. Het staartgas, dat voornamelijk bestaat uit waterstofsulfide, carbonylsulfide en inerte gassen, kan worden verbrand en gewassen met een bijtende oplossing of naar een zwavelwinningsinstallatie worden geleid.
Normaal gesproken kan elke retort 1 tot 3 metrische ton koolstofdisulfide per dag produceren. De bruikbare levensduur van gietijzeren retorten is beperkt tot minder dan een jaar vanwege corrosie bij hoge temperaturen. Om de noodzaak van reactorreiniging te minimaliseren, moeten de grondstoffen die in de retorten worden gebruikt een laag as- en residugehalte hebben. Vervuiling van de retorten belemmert de warmteoverdracht en verkort hun levensduur.
De kwaliteit van houtskool is cruciaal, omdat minder reactieve materialen hogere temperaturen vereisen voor een bevredigende werking. Om deze reden heeft houtskool afkomstig van hardhout de voorkeur.
De houtskool wordt doorgaans voorgecalcineerd bij 500 °C om vluchtige stoffen te verwijderen die kunnen leiden tot de vorming van ongewenste bijproducten. De thermische efficiëntie van retorten is ongeveer 25%, met koolstof- en zwavelopbrengsten over het algemeen onder de 90%.
Een alternatieve warmtebron voor de reactie van houtskool met zwavel wordt geleverd door elektrische weerstandsverwarming in met bakstenen beklede elektrothermische reactoren. Wanneer goedkope energie beschikbaar is, kan de elektrische methode kosteneffectiever zijn.
Het stroomverbruik per geproduceerde ton koolstofdisulfide is ongeveer 1200 kWh. Elektrothermische reactoren bieden verschillende voordelen, waaronder een grotere capaciteit per reactor (tot 10 ton per dag) en een langere levensduur van de reactor. Bovendien kan een breder scala aan vaste koolstoftoevoer worden gebruikt, aangezien elektrothermische reactoren hogere temperaturen kunnen genereren.
3.2. Productie van koolstofdisulfide uit methaan en zwavel
Vanwege de groeiende vraag naar koolstofdisulfide in de jaren 40, hebben de beperkingen van houtskoolprocessen geleid tot de ontwikkeling van een efficiëntere grootschalige productiemethode.
De gekatalyseerde reactie tussen methaan en zwavel, waarbij gebruik werd gemaakt van gemakkelijk verkrijgbaar en kosteneffectief aardgas, kwam naar voren als een succesvol alternatief. Tussen 1943 en 1965 werden er talloze patenten uitgegeven, die verschillende aspecten van dit proces bestreken.
Het commerciële methaanproces, voornamelijk gebaseerd op de patenten die werden verkregen door Pure Oil Co., werd later overgenomen door Food Machinery Corp. (FMC) en Stauffer Chemical Co.
In 1953 bouwde FMC de eerste methaanverwerkingsfabriek in South Charleston, West Virginia, gevolgd door een Stauffer-fabriek in LeMoyne, Alabama, drie jaar later. Halverwege de jaren 60 werd alle koolstofdisulfideproductie in de Verenigde Staten via deze methode uitgevoerd en al snel ontstonden er soortgelijke fabrieken in Europa en andere regio’s.
Momenteel is meer dan 85% van de wereldwijde productiecapaciteit voor koolstofdisulfide gebaseerd op het methaanproces.
Een typisch methaanprocesstroomschema is weergegeven in Figuur 1. Gezuiverd aardgas, dat meer dan 95% methaan en lage concentraties propaan en zwaardere koolwaterstoffen bevat, wordt voorverwarmd tot ongeveer 250 °C in het convectiegedeelte van de reactiekachel.
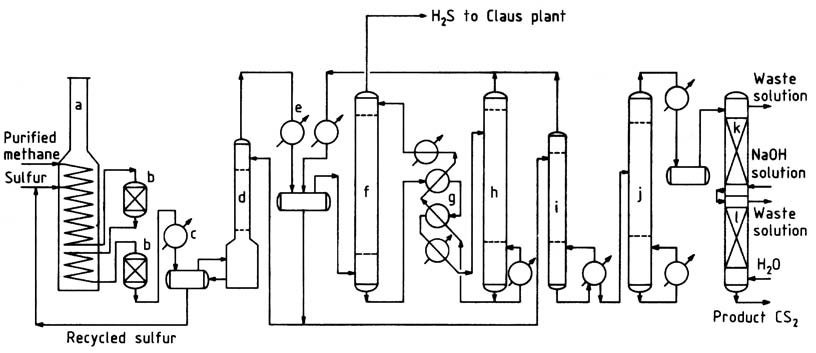
a) Reactieoven; b) Katalytische reactoren; c) Zwavelcondensor; d) CS2-wasser; e) CS2-condensor; f) CS2-absorber; g) Oliewisselaars; h) CS2-stripper; i) Stabilisatorkolom; j) Zuiveringskolom; k) Bijtende waskolom; l) Waterwaskolom
De oven, een pyrolyse-oven van het doostype die gewoonlijk wordt gebruikt in de petrochemische industrie, bestaat uit stralings- en convectiegedeelten. Het hete methaangas wordt gemengd met vloeibare zwavel en in de horizontale verwarmingsspiraal in het stralingsgedeelte gebracht.
In dit gedeelte verdampt de vloeibare zwavel en stijgt de temperatuur van het mengsel tot 550–650 °C. De werkdruk varieert doorgaans van 400 tot 700 kPa.
Als alternatief kunnen methaan en zwavel afzonderlijk en op verschillende locaties in de spiraal worden geïntroduceerd. Een kleine overmaat zwavel (ongeveer 5%) wordt gebruikt om een efficiënte methaanconversie te garanderen en de vorming van koolstof en teer te minimaliseren.
Om de corrosieve omgeving met hoge temperaturen te weerstaan, wordt gegoten roestvrij staal van hoge legering gebruikt als buismateriaal, wat een levensduur van de buis van ongeveer 2–3 jaar oplevert. Gevulde, met bakstenen beklede reactoren worden aangesloten op de verwarmingsspiraal om extra verblijftijd en behuizing voor katalysatorbedden te bieden.
De reactie vindt plaats in zowel de buizen als de reactoren, waardoor een bijna volledige omzetting van koolwaterstoffen wordt gegarandeerd voordat het gas de laatste reactor verlaat. Het gas dat het reactie-ovensysteem verlaat, passeert een zwavelcondensor, waar het grootste deel van de overtollige zwavel wordt afgescheiden.
Vervolgens gaat het gekoelde gas naar een zwavelwasser en vervolgens naar de CS2-wasser, waar de resterende zwavel wordt verwijderd. Het relatief zwavelvrije gas komt in watergekoelde condensors voor bulkafscheiding van koolstofdisulfide.
Het resterende koolstofdisulfide wordt uit het waterstofsulfidegas in de olie-absorber gehaald. Het waterstofsulfidegas dat de olie-absorber verlaat, bevat ongeveer 1-2% methaan en minder dan 1000 ppm koolstofdisulfide.
Dit gas wordt naar een Claus-zwavelwinningsinstallatie geleid, waar het weer wordt omgezet in zwavel.
Ruwe koolstofdisulfide, inclusief die welke in de stripper wordt gewonnen, wordt naar de stabilisatorkolom gestuurd om laagkokende onzuiverheden te verwijderen.
De bodems van de stabilisatorkolom worden vervolgens verwerkt in de zuiveringskolom om hoogkokende verontreinigingen van het product te scheiden. De productzuivering wordt voltooid door middel van loog- en waterwassingen, waarna het eindproduct wordt gepompt naar controletanks en opslag.
4. Toepassingen van koolstofdisulfide
De primaire consument van koolstofdisulfide is de geregenereerde cellulose-industrie, die goed is voor meer dan 65% van de wereldproductie. Specifiek gebruikt de productie van rayon een aanzienlijk deel koolstofdisulfide, met ongeveer 0,32 kg koolstofdisulfide verbruikt voor elke kilogram geproduceerd rayon.
Ongeveer 10% koolstofdisulfide wordt gebruikt bij de productie van cellofaan, terwijl nog eens 10% wordt gechloreerd om koolstoftetrachloride te produceren. Deze methode is goed voor ongeveer 25% van de wereldwijde productie van koolstoftetrachloride.
De resterende 15% koolstofdisulfide wordt verdeeld over verschillende toepassingen, waaronder rubberchemicaliën, flotatiemiddelen, pesticiden, diverse chemische reagentia, extractieoplosmiddelen, katalysatorpresulfidatiemiddelen en oliebronoplosmiddelen.
De geregenereerde cellulose-industrie kampt echter met uitdagingen vanwege de concurrentie van synthetische vezels en films, wat de marktgroei beperkt. Om vooruitgang te bevorderen, is er behoefte aan geleidelijke verbetering van het gebruik van koolstofdisulfide, met name door een verhoogd gebruik in de productie van landbouw- en specialiteitschemicaliën.
Referentie
- Carbon Disulfide; Ullmann’s Encyclopedia of Industrial Chemistry. – https://onlinelibrary.wiley.com/doi/10.1002/14356007.a05_185