1. Processo generale per la produzione di resine amminiche
La produzione di resine amminiche è un processo in due fasi: idrossimetilazione e condensazione. L’idrossimetilazione è l’aggiunta di formaldeide a un composto amminico, come l’urea, per formare un derivato idrossimetilico. La condensazione è la reazione di due derivati idrossimetilici per formare una molecola più grande.
Sommario
La reazione di idrossimetilazione viene in genere eseguita in un mezzo leggermente alcalino o leggermente acido, mentre la reazione di condensazione richiede una soluzione più fortemente acida. Le eccezioni sono le resine melammina-formaldeide, che richiedono un pH alcalino, e le resine melammina-urea-formaldeide, che vengono condensate in mezzi leggermente alcalini.
Il processo per la produzione di resine amminiche viene continuato fino a quando il prodotto risultante è una miscela oligomerica che è ancora solubile o fusibile. Viene quindi protetto da ulteriore condensazione rendendo il mezzo alcalino.
La condensazione della resina mediante catalisi acida, ovvero reticolazione per dare un prodotto sostanzialmente infusibile, non viene eseguita fino a quando la resina non viene messa in uso. Questo processo è chiamato polimerizzazione.
Anche nello stato polimerizzato, possono essere presenti gruppi idrossimetilici liberi. Composti monomolecolari e idrossimetilici con bassi gradi di polimerizzazione e fino a sei unità urea-formaldeide sono praticamente tutti noti e possono essere preparati in forma pura.
Tuttavia, le soluzioni acquose degli oligomeri con bassi gradi di polimerizzazione non hanno una durata di conservazione sufficientemente lunga. Solo quando le concentrazioni di gruppi idrossimetilici e NH2 vengono ridotte mediante condensazione parziale o quando i prodotti sono presenti in forma solida possiedono una durata di conservazione utile a livello industriale, ovvero di diverse settimane o più.
Le condensazioni effettuate in un eccesso di un alcol, come metanolo o butanolo, con l’aggiunta di acido e la rimozione di acqua se necessario, producono resine amminiche eterificate (ovvero alchilate) induribili. Queste sono solubili in solventi non acquosi e possono essere miscelate con resine alchidiche, resine epossidiche, ecc. Sono utilizzate come materiali di partenza nella produzione di rivestimenti superficiali.
Le colle di resina a base di urea, melamina o entrambe sono state sottoposte a eterificazione parziale per stabilizzarle contro ulteriore condensazione. Storicamente, queste resine sono state utilizzate per la fabbricazione di compensato, ma non sono praticamente più utilizzate.
Le difficoltà di base incontrate nella produzione di resine amminiche sono impedire alle resine di solidificarsi durante il processo di produzione e ottenere selettivamente determinate proprietà, come lunga durata di conservazione, basso contenuto di formaldeide, basse emissioni di formaldeide dai prodotti finali, resistenza e resistenza al rigonfiamento del pannello truciolare dopo la polimerizzazione.
1.1. Idrossimetilazione
L’idrossimetilazione è l’aggiunta di formaldeide a un composto amminico, come l’urea, per formare un derivato idrossimetilico. La reazione può essere catalizzata da condizioni alcaline o acide, ma le condizioni alcaline sono preferite in quanto determinano una velocità di reazione più rapida.
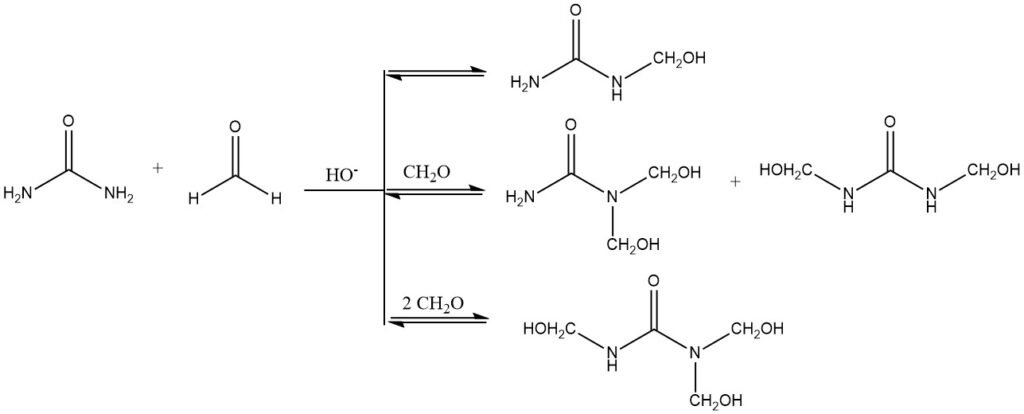
In mezzi alcalini, la reazione di idrossimetilazione procede attraverso la formazione di un legame semiamminale. Questo legame è instabile e può essere facilmente scisso, il che significa che la reazione di idrossimetilazione è reversibile e si stabilisce un equilibrio. Ecco perché è possibile isolare mono-, di- e tri-idrossimetilurea, ma non tetraidrossimetilurea.
La completa idrossimetilazione di tutti i gruppi amminici per formare esaidrossimetilmelammina è possibile anche in condizioni alcaline. La reazione è leggermente esotermica, il che significa che viene rilasciato calore. L’entalpia di idrossimetilazione dell’urea è di circa -23 kJ/mol.
La velocità di reazione dell’idrossimetilazione è influenzata da una serie di fattori, tra cui concentrazione, temperatura, pH e presenza di sostituenti. In generale, la velocità di reazione aumenta con l’aumento di concentrazione, temperatura e pH. Anche i sostituenti possono avere un effetto, con gruppi elettron-attrattori e sostituenti ingombranti che riducono la velocità di reazione.
Le velocità di reazione dell’idrossimetilazione sono state misurate frequentemente, ma sono sensibili a molti parametri. Ciò rende difficile definire una velocità di reazione complessiva per i processi industriali, che producono miscele variabili di oligomeri con unità ripetute miste. Inoltre, le importanti proprietà della resina non sono state correlate alle singole velocità di reazione.
Nonostante queste sfide, l’idrossimetilazione è una reazione importante nella produzione di resine amminiche. Comprendendo il meccanismo di reazione e i fattori che influenzano la velocità di reazione, è possibile ottimizzare il processo e produrre resine di alta qualità con le proprietà desiderate.
1.2. Condensazione
La condensazione dei derivati idrossimetilici è catalizzata da acidi. Anche gli alcali forti possono essere utilizzati come catalizzatori, ma le resine amminiche risultanti non sono importanti a livello industriale. La condensazione può avvenire attraverso i seguenti percorsi:
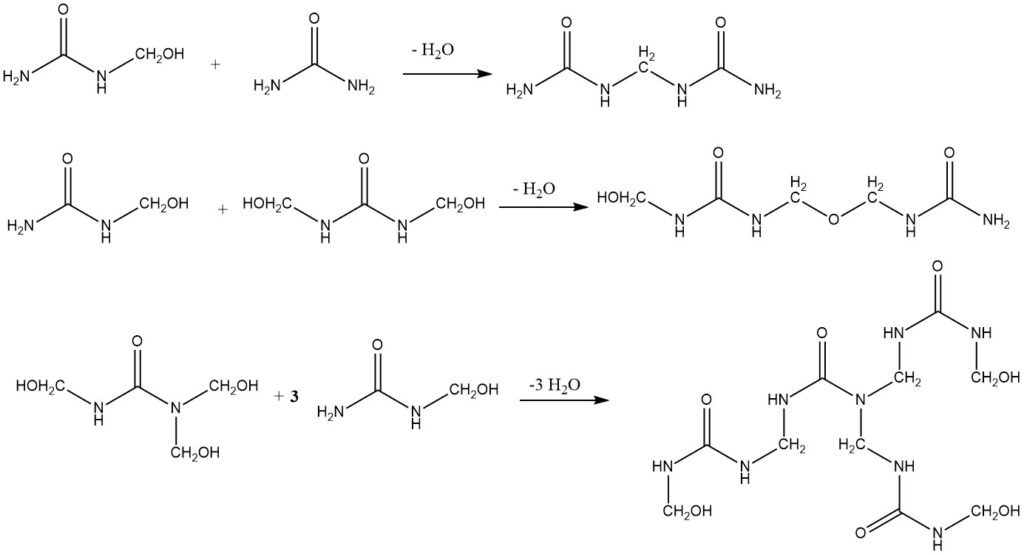
La presenza di composti metilenici nelle resine amminiche può essere stabilita tramite spettroscopia NMR 13C, ma gli eteri bis(ureametilene) possono essere rilevati solo indirettamente.
La spettroscopia NMR 13C può essere utilizzata per chiarire molte delle strutture, ma non distingue tra gli atomi di C mostrati in (1) e (2), anche se i loro terzi vicini più prossimi sono diversi. Questo problema si verifica anche nel caso delle resine melamminiche.
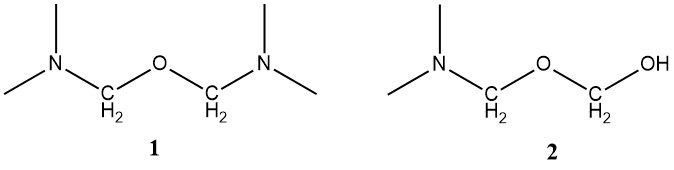
I legami metilenici tra due molecole di urea sono molto stabili e possono essere idrolizzati solo da acidi forti a temperature elevate. La reazione di condensazione è leggermente esotermica, con un’entalpia di -28 kJ/mol.
La stabilità del legame metilene-etere è compresa tra quella del legame idrossimetilico e quella del legame metilene. È impossibile fornire una singola velocità di reazione per il processo di condensazione perché ci sono molti materiali di partenza diversi (composti idrossimetilici) e molti prodotti finali (composti metilenici).
Anche il tipo di solvente ha un effetto sulla velocità di condensazione. La dipendenza della reattività dei composti idrossimetilici dalla composizione chimica dei composti amminici può essere interpretata sulla base di diverse regole qualitative.
1.3. Composizione di una soluzione di resina amminica
La composizione strutturale degli oligomeri nelle soluzioni di resina amminica può essere identificata mediante l’uso della spettroscopia NMR 1H e 13C. All’interno dello spettro, sono rilevabili gli idrati degli oligomeri di formaldeide, HO(CH2O)nH, con n approssimativamente uguale a 5.
Varie strutture idrossimetiliche, inclusi eteri come l’idrossimetil metil etere, possono essere distinte osservando gli atomi di C corrispondenti dell’alcol genitore. Inoltre, possono essere rilevate le strutture (3) e (4) insieme ai composti ad anello, contenenti eteri ciclici del tipo urone.
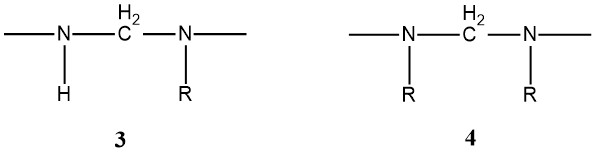
In una tipica colla per pannelli truciolari, lo spettro NMR 13C potrebbe mostrare, ad esempio, le seguenti proporzioni di atomi di carbonio dalla formaldeide originale (in frazioni molari):
- Formaldeide: 0,03
- Composti idrossimetilici: 0,72
- Composti metilenici: 0,15
- Composti ciclici: 0,10
Si possono applicare anche metodi analitici alternativi per chiarire ulteriormente la struttura della resina. Ad esempio:
- Cromatografia liquida ad alte prestazioni (HPLC), utilizzata principalmente per costituenti a bassa massa molecolare come urea, monometilolurea, N,N-dimetilolurea, N,N’-dimetilolurea, trimetilolurea e metilendiurea.
- Cromatografia ad esclusione dimensionale, utilizzata principalmente per specie a massa molecolare più elevata come dimeri e oligomeri.
2. Processi di produzione di resine amminiche
Le resine amminiche vengono solitamente prodotte in lotti da 5-100 metri cubi. Tuttavia, vengono utilizzati anche processi continui, in particolare per la produzione di colle di resina. La letteratura brevettuale descrive processi in cui una fase particolare viene eseguita in continuo mentre altre fasi vengono eseguite in lotti.
La velocità di reazione e la composizione del prodotto finale sono influenzate da un gran numero di parametri, quindi la reazione deve essere attentamente controllata. I parametri di reazione importanti includono:
- Purezza o composizione dei materiali di partenza
- Rapporto molare in ciascuna delle fasi di reazione
- Tipo e quantità di modificatore
- Concentrazioni dei reagenti
- Valore pH in ciascuna fase della reazione
- Temperatura in ciascuna fase della reazione
- Tipo e concentrazione del catalizzatore
- Quantità di sale tampone
- Tempo di reazione in ciascuna fase
2.1. Produzione in lotti
Il processo in lotti è il metodo più comune per la produzione industriale di resine amminiche. Ha lo svantaggio di avere una capacità di produzione relativamente piccola, ma consente un’ampia varietà di prodotti e frequenti cambi di prodotto.
Le reazioni vengono eseguite in bollitori agitati in due o più fasi a 70-100 °C. Nella prima fase, che viene eseguita in una soluzione leggermente acida o alcalina, la reazione principale è l’idrossimetilazione.
Nelle fasi successive, si verifica la condensazione, l’acqua viene eliminata e si formano prodotti con peso molecolare più elevato e viscosità crescente. La durata della condensazione dipende dalle proprietà desiderate del prodotto.
In generale, i prodotti vengono concentrati al 60-70% di soluzioni acquose tramite evaporazione. I materiali di partenza, urea o melamina, vengono utilizzati in polvere. L’urea può essere utilizzata anche in soluzione. La formaldeide viene utilizzata come soluzione acquosa al 37-55%.
In alcuni casi speciali, la formaldeide viene utilizzata in forma solida, paraformaldeide. Infine, è possibile utilizzare precondensati urea-formaldeide in concentrazioni non superiori all’80% in massa dei principi attivi.
2.1.1. Soluzioni acquose
Nella Figura 1 è illustrato uno schema di impianto per la produzione in lotti di soluzioni acquose di resine amminiche. Il reattore è costituito da un bollitore dotato di meccanismi di riscaldamento e raffreddamento, un agitatore, ingressi per l’aggiunta di materie prime e dispositivi di misurazione, una valvola di fondo per lo scarico e un tombino per la pulizia.
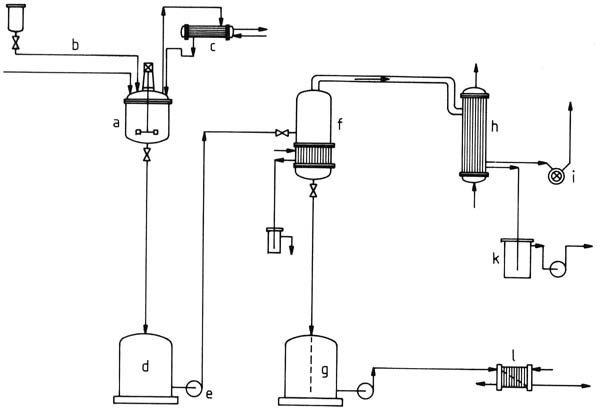
a) Bollitore agitato; b) Alimentazione materie prime; c) Condensatore a riflusso; d) Contenitore temporaneo; e) Pompa; f) Vaporizzatore; g) Contenitore per prodotto finito; h) Condensatore; i) Pompa per vuoto; k) Recipiente per vapori condensati; l) Refrigeratore
L’uso di acciaio inossidabile, come i materiali St. 1.4541 o St. 1.4571, è comune. Le serpentine interne o i tubi semicircolari fissati esternamente facilitano il riscaldamento e il raffreddamento. L’agitazione impiega robusti agitatori a disco o ad ancora. Sono incorporati ugelli per l’aggiunta controllata di materie prime, temperatura e misurazione del pH.
Al termine della condensazione, può avvenire l’evaporazione del prodotto, sia nel bollitore agitato o più economicamente in un vaporizzatore tubolare monostadio o multistadio. L’evaporazione viene eseguita a pressione ridotta per preservare la resina.
La qualità della resina viene quindi valutata in base alle specifiche e trasferita in un contenitore di stoccaggio. Le tubazioni possono essere realizzate in alluminio o acciaio, poiché il mezzo è leggermente alcalino, mentre i serbatoi del prodotto possono essere costruiti in poliestere rinforzato con fibra di vetro o ferro rivestito.
Ad esempio, una tipica procedura per produrre una colla per pannelli truciolari prevede l’introduzione di 85 parti (in massa) di urea solida in 158 parti di una soluzione di formaldeide neutralizzata al 50%. La miscela viene mantenuta a 80 °C per 10 minuti per facilitare l’idrossimetilazione.
Il pH viene quindi regolato a 4–5 utilizzando una soluzione di acido formico al 10%. Un’ulteriore condensazione aumenta la temperatura a 90–100 °C in pochi minuti. Questa temperatura viene mantenuta fino al raggiungimento di un endpoint specifico, determinato dalla formazione di un precipitato bianco o dal raggiungimento di una viscosità designata.
La miscela di reazione viene quindi leggermente alcalinizzata utilizzando una soluzione di idrossido di sodio al 25% per interrompere la condensazione. Viene aggiunta ulteriore urea per ottenere un rapporto molare formaldeide-urea di 1,1.
La soluzione finale contiene circa il 60% di solidi, che possono essere evaporati a pressione ridotta per ottenere una concentrazione commerciale del 66%.
2.1.2. Polveri di resina amminica
Per la produzione di polveri di resina amminica, viene inizialmente prodotta una soluzione di resina acquosa e quindi sottoposta a essiccazione a spruzzo (Figura 2).
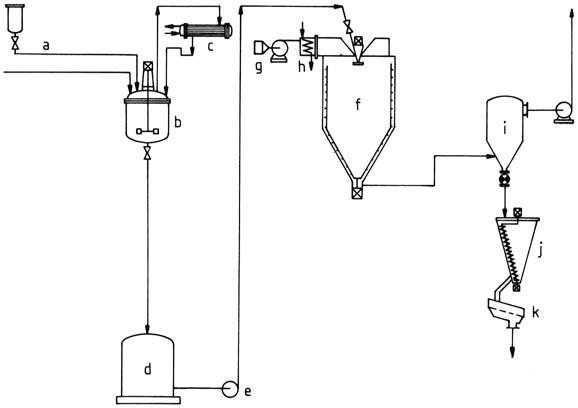
a) Alimentazione del materiale di partenza; b) Bollitore agitato; c) Condensatore a riflusso; d) Contenitore temporaneo; e) Pompa; f) Essiccatore a spruzzo; g) Soffiante; h) Riscaldatore d'aria; i) Filtro; j) Contenitore di miscelazione; k) Setaccio vibrante
La soluzione viene atomizzata utilizzando un disco o un ugello di spruzzatura in un essiccatore a spruzzo. Le goccioline risultanti vengono essiccate in un flusso di gas caldo generato tramite riscaldamento indiretto dell’aria o miscelando gas di scarico caldo con aria. La polvere viene raccolta, setacciata e quindi confezionata.
2.1.3. Prodotti eterificati contenenti solvente
I prodotti contenenti solventi, adatti per realizzare rivestimenti superficiali, possono essere prodotti in reattori simili a quelli utilizzati per le soluzioni acquose (Figura 3).
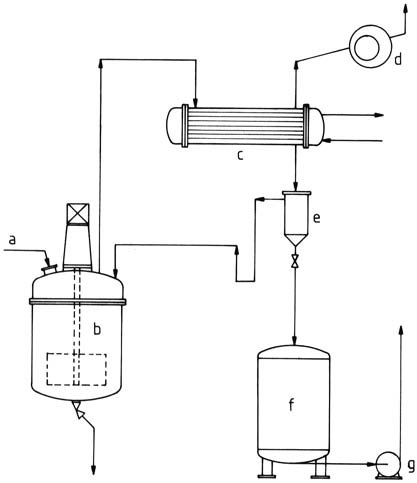
a) Alimentazione delle materie prime; b) Bollitore agitato; c) Condensatore; d) Pompa per vuoto; e) Recipiente di separazione (separatore d'acqua); f) Recipiente del prodotto; g) Pompa
È necessario uno scambiatore di calore sufficientemente grande per vaporizzare la miscela di acqua e alcol in eccesso, spesso butanolo.
Un separatore d’acqua è posizionato a valle dello scambiatore di calore. La fase acquosa che si separa contiene ancora formaldeide residua e alcol e necessita di ulteriore lavorazione. Al contenuto di alcol appropriato, la fase solvente viene riciclata nel processo di produzione.
Per la produzione di una resina melammina-formaldeide butilata per rivestimenti superficiali, melammina e formaldeide in una soluzione acquosa al 40%, insieme al butanolo, vengono sottoposte a riflusso. Dopo la distillazione dell’acqua, la miscela viene raffreddata, il contenuto di resina determinato e la concentrazione viene regolata al 50% utilizzando butanolo.
2.2. Produzione continua
La produzione industriale continua di resine amminiche è stata introdotta per soddisfare la crescente domanda di queste resine. Tuttavia, la produzione continua presenta alcuni svantaggi.
La quantità di resina prodotta per unità di tempo in un particolare impianto può variare solo entro limiti relativamente ristretti. Ciò avviene perché la residenza prolungata in condizioni costanti aumenta la proporzione di molecole con alti gradi di condensazione.
Inoltre, non è facile cambiare il prodotto prodotto in un processo continuo. Se l’impianto non viene pulito in anticipo, per un certo periodo verrà prodotto un prodotto con una composizione tra il vecchio e il nuovo prodotto.
Per questo motivo, la produzione continua è in genere utilizzata per una gamma limitata di prodotti. Tuttavia, produce una qualità del prodotto molto uniforme.
La letteratura brevettuale descrive un gran numero di processi continui per la produzione di resine amminiche. Questi processi differiscono solo nella tecnologia di processo per il flusso del prodotto.
Le differenze in genere comportano variazioni nella temperatura, nel pH, nella concentrazione o nei modificatori. Il processo e il flusso del prodotto sono altrimenti gli stessi.
In molti casi, le pubblicazioni descrivono solo impianti su scala di laboratorio o pilota che non sono stati ampliati per uso industriale.
2.2.1. Soluzioni acquose di resine amminiche
La produzione continua di soluzioni acquose di resine amminiche coinvolge vari apparati, come reattori tubolari, cascate di bollitori agitati o combinazioni di entrambi.
I processi continui presentano un rischio maggiore di incrostazioni a causa di prodotti altamente condensati e insolubili rispetto ai processi in batch.
Nei processi in batch, i residui vengono disciolti da soluzioni di resina fresca, un meccanismo che non si applica in modo efficace nei processi continui a causa della limitata miscelazione posteriore.
Diversi processi di produzione continua sono stati descritti in dettaglio nella letteratura brevettuale:
1. Girdler Corp.. (1943) ha descritto un processo a due reattori in cui i reagenti venivano miscelati nel primo reattore, riscaldati sotto pressione e quindi spostati in una seconda fase per la condensazione.
2. Sherwood Paints (1949) ha utilizzato una colonna riempita per la reazione, espellendo il vapore acqueo attraverso un flusso di gas controcorrente.
3. Allied Chemical Corp. (1951) ha utilizzato un reattore a serpentina tubolare, seguito da evaporazione. Un altro processo di Allied Chemical Corp. (1952) ha utilizzato vapore iniettato sotto pressione.
4. Spumalit-Anstalt (Liechtenstein) ha utilizzato un catalizzatore solido (resina policarbammidica) sotto pressione per formare la resina.
5. Rütgerswerke (Germania, 1955) ha utilizzato uno scambiatore di ioni come catalizzatore a letto fisso per resine utilizzate nei composti di stampaggio.
6. Skanska Attifabriken AB (Svezia, 1955) ha utilizzato un processo a due camere in cui i materiali di partenza subivano una condensazione parziale nella prima camera prima di completare la reazione nella seconda camera.
7. Du Pont (1956) ha descritto un processo a cascata che coinvolge da due a quattro bollitori agitati per produrre resine formaldeide-urea eterificate.
8. Il processo Meissner (1966) ha condotto la fase di idrossimetilazione in modo continuo mentre la successiva fase di condensazione funzionava in batch.
9. BASF (1971) ha descritto un processo che utilizza una cascata di tre o più bollitori agitati per l’idrossimetilazione seguita da condensazione (Figura 4).
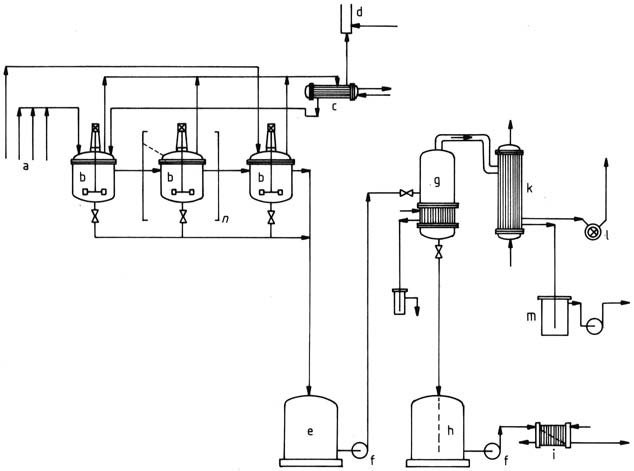
a) Alimentazione del materiale di partenza; b) Bollitore agitato; c) Condensatore a riflusso; d) Fiaccola; e) Contenitore temporaneo; f) Pompa; g) Vaporizzatore; h) Contenitore del prodotto; i) Refrigeratore; k) Condensatore; l) Pompa per vuoto; m) Contenitore per vapori condensati
10. Stamicarbon e American Cyanamid hanno discusso la produzione continua di soluzioni concentrate di melammina-formaldeide ricche di formaldeide per materiali di partenza in resina amminica.
11. DSM ha delineato un processo continuo in cui la resina di condensazione viene preparata in un mezzo acquoso a temperature e pressioni elevate, utilizzando un reattore tubolare con elementi miscelatori statici.
Ognuno di questi processi dimostra i diversi approcci adottati per ottenere una produzione continua di resina amminica gestendo al contempo sfide come incrostazioni e varietà di prodotti.
2.2.2. Resine in polvere
Le resine in polvere possono anche essere prodotte in modo continuo alimentando le soluzioni spray, che sono in genere prodotte in lotti, in modo continuo da un contenitore temporaneo in una torre di spruzzatura.
La torre di spruzzatura è una camera alta e stretta in cui le soluzioni spray vengono atomizzate in goccioline fini. Le goccioline vengono quindi essiccate tramite aria calda o gas. La polvere di resina secca viene raccolta sul fondo della torre.
Questo processo è continuo perché le soluzioni spray vengono alimentate nella torre in modo continuo. Ciò consente una qualità del prodotto più costante rispetto al processo in lotti.
2.3. Produzione di prodotti e schiume speciali
Oltre alle resine impregnanti, altri prodotti speciali includono resine espanse e resine per ausiliari di carta, adesivi per etichette, fluidificanti per calcestruzzo, ausiliari per pelle, rivestimenti per tappeti, microcapsule e così via. Queste resine sono in genere prodotte in lotti perché sono prodotte in quantità relativamente piccole e c’è un’ampia varietà di prodotti.
La produzione di resine espanse è simile alla produzione di colle di resina. Il know-how proprietario per questi prodotti riguarda modificatori e piccole ma importanti variazioni nel processo.
Le resine schiumogene sono un interessante tipo di resina amminica che viene utilizzata per produrre schiume solide. Queste schiume hanno un’ampia varietà di applicazioni, tra cui isolamento termico, isolamento acustico, condizionamento del terreno in agricoltura, riempimento di cavità minerarie, materiale di supporto per fluidi di pulizia e copertura per discariche.
Le prime resine espanse furono prodotte negli anni ’30. Il processo prevede l’aggiunta di un agente schiumogeno e aria a una soluzione di colla. L’agente schiumogeno fa sì che la soluzione formi bolle e l’aria aiuta a espandere le bolle.
La resina quindi si indurisce, formando una schiuma solida. Le resine di urea formaldeide espanse essiccate avevano densità apparenti che andavano da 5 a 70 kg/m³, con oltre il 60% della schiuma che adottava la forma di celle aperte.
Lo sviluppo di apparecchiature portatili per la produzione in loco di resine espanse ha portato ad applicazioni molto più ampie per questi prodotti. Oggi, le resine espanse sono utilizzate in una varietà di settori, tra cui edilizia, automotive e imballaggio.
Riferimenti
- Amino Resins; Ullmann’s Encyclopedia of Industrial Chemistry. – https://onlinelibrary.wiley.com/doi/10.1002/14356007.a02_115.pub2
- Amino resin and a method for its production. – https://patents.google.com/patent/EP0277106B1/en
- Amino resins; Encyclopedia of Polymer Science and Technology. – https://onlinelibrary.wiley.com/doi/abs/10.1002/0471440264.pst017