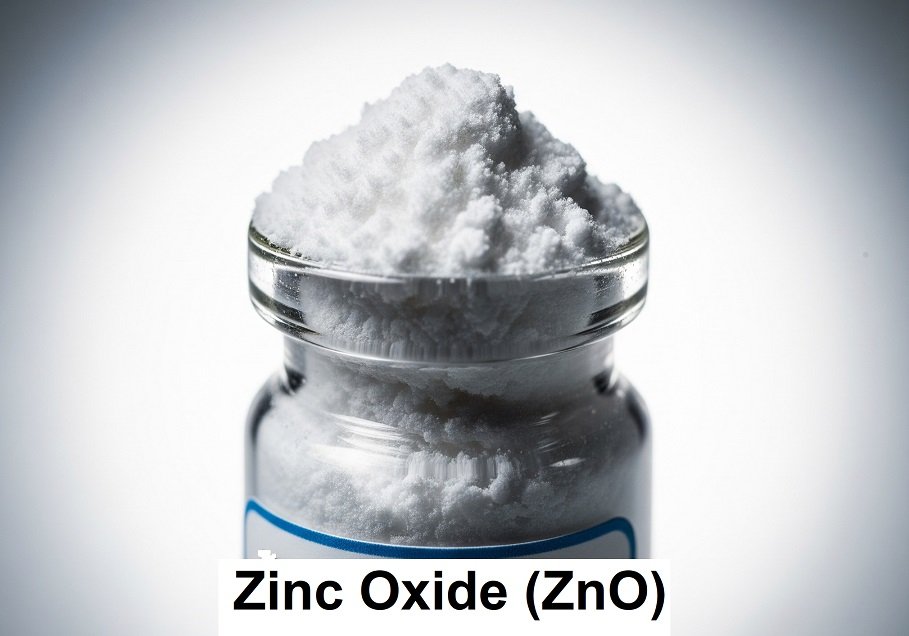
Qu’est-ce que l’oxyde de zinc ?
L’oxyde de zinc est un composé inorganique de formule chimique ZnO. C’est une poudre blanche insoluble dans l’eau. Bien qu’il puisse être présent naturellement sous forme de zincite, la plupart des oxydes de zinc utilisés commercialement sont produits synthétiquement.
Autrefois, l’oxyde de zinc était uniquement utilisé comme pigment blanc, connu sous différents noms, notamment blanc de zinc (C.I. Pigment White 4), blanc de Chine et fleurs de zinc.
L’oxyde de zinc est apparu comme un sous-produit de la fusion du cuivre. Les Romains l’appelaient « cadmia » et l’utilisaient pour la production de laiton. Ils le raffinaient également par une séquence de réduction-oxydation pour la fabrication d’onguents médicinaux. Les alchimistes médiévaux pensaient que le cadmia pouvait être converti en or.
Au milieu du XVIIIe siècle, le chimiste allemand Cramer produisit de l’oxyde de zinc par combustion de zinc métallique. Courtois commença la production de blanc de zinc en France en 1781 ; Cependant, la fabrication à l’échelle industrielle ne débuta qu’en 1840 par Leclaire, utilisant le procédé indirect, ou procédé français.
L’oxyde de zinc remplaça rapidement le céruse grâce à ses propriétés supérieures, telles que sa non-toxicité, sa résistance à la décoloration due aux gaz sulfureux et sa bonne opacité.
Vers 1850, S. Wetherill, de la New Jersey Zinc Company, développa un four de grillage dans lequel une grille chargée de charbon était chargée de charbon, puis recouverte d’un mélange de minerai de zinc et de charbon. Le zinc subissait une réduction par combustion partielle du charbon, puis se réoxydait à la sortie du four.
Cette méthode devint connue sous le nom de procédé direct, ou procédé américain. Bien que ces fours aient connu des améliorations ultérieures, ils ne sont plus utilisés.
Dans la seconde moitié du XIXe siècle, l’oxyde de zinc fut incorporé aux formulations de caoutchouc afin de réduire le temps de vulcanisation. La découverte des accélérateurs organiques en 1906 améliora considérablement le processus de vulcanisation, augmentant ainsi l’importance de l’oxyde de zinc, utilisé comme activateur dans l’industrie du caoutchouc.
Table des matières
1. Propriétés physiques de l’oxyde de zinc
L’oxyde de zinc est une fine poudre blanche qui vire au jaune lorsqu’elle est chauffée à plus de 300 °C. Il absorbe les ultraviolets (UV) à des longueurs d’onde inférieures à 366 nm.
L’introduction d’éléments traces monovalents ou trivalents dans son réseau cristallin lui confère des propriétés semi-conductrices. Les particules élémentaires de ZnO produites par des procédés thermiques peuvent être granulaires ou nodulaires (0,1 à 5 µm) ou aciculaires (en forme d’aiguille).
Le ZnO est insoluble dans l’eau, avec une solubilité d’environ 0,16 mg/100 mL à 30 °C ; cependant, il se dissout dans les acides dilués et les bases fortes en raison de sa nature amphotère.
Les principales propriétés physiques de l’oxyde de zinc sont résumées dans le tableau ci-dessous :
Propriété | Valeur |
---|---|
Numéro CAS | [1314-13-2] |
Formule chimique | ZnO |
Poids moléculaire | 81,38 g/mol |
Point de fusion | 1975 °C |
Point d'ébullition | environ 2360 °C |
Densité | 5,65–5,68 g/cm3 |
Indice de réfraction | 1,95–2,1 |
Capacité thermique à 25 °C | 40,26 J mol-1 K-1 |
Capacité thermique à 100 °C | 44,37 J mol-1 K-1 |
Capacité thermique à 1000 °C | 54,95 J mol-1 K-1 |
Conductivité thermique | 25,2 W m-1 K-1 |
Structure cristalline | hexagonale, wurtzite |
Dureté Mohs | 4–4,5 |
Absorption d'huile | 20–24 g/100 g |
Densité apparente | 100 cm3/100 g |
Taille moyenne des particules | 0,11–0,22 mm |
Surface BET | 3–10 m2/g |
2. Propriétés chimiques de l’oxyde de zinc
L’oxyde de zinc est amphotère. Il réagit avec les acides organiques et inorganiques. Il se dissout également dans les solutions alcalines et l’ammoniac pour former des zincates. Le ZnO réagit facilement avec les gaz acides, tels que le dioxyde de carbone, le dioxyde de soufre et le sulfure d’hydrogène. Les réactions à haute température avec d’autres oxydes produisent des composés comme les ferrites de zinc.
Il réagit avec les acides pour produire des sels de zinc et de l’eau. Il s’agit d’une réaction de neutralisation où le ZnO agit comme base.
ZnO + 2 HCl → ZnCl2 + H2O
ZnO + H2SO4 → ZnSO4 + H2O
ZnO + 2 HNO3 → Zn(NO3)2 + H2O
L’oxyde de zinc réagit avec les bases fortes pour former des zincates solubles. Le ZnO agit comme un acide dans ces réactions.
ZnO + 2 NaOH → Na2ZnO2 + H2O (zincate de sodium)
L’oxyde de zinc peut être réduit en zinc métallique à haute température et à l’aide d’un agent réducteur. Il s’agit d’une étape standard de l’extraction du minerai de zinc.
Le carbone (coke) réduit l’oxyde de zinc en zinc métallique, et le carbone est oxydé en monoxyde de carbone. Cette réaction revêt une importance historique et industrielle.
L’hydrogène ou les métaux réactifs comme le magnésium peuvent également réduire l’oxyde de zinc.
L’oxyde de zinc réagit avec de nombreux composés organiques, notamment les acides carboxyliques et les acides gras (par exemple, l’acide stéarique, présent dans les huiles et les formulations de caoutchouc), pour former des carboxylates de zinc (savons de zinc).
Le stéarate de zinc (1), formé par la réaction de l’acide stéarique avec l’oxyde de zinc, est utilisé comme activateur d’accélérateur et peut également contribuer à la dégradation des peintures à l’huile contenant du pigment ZnO.
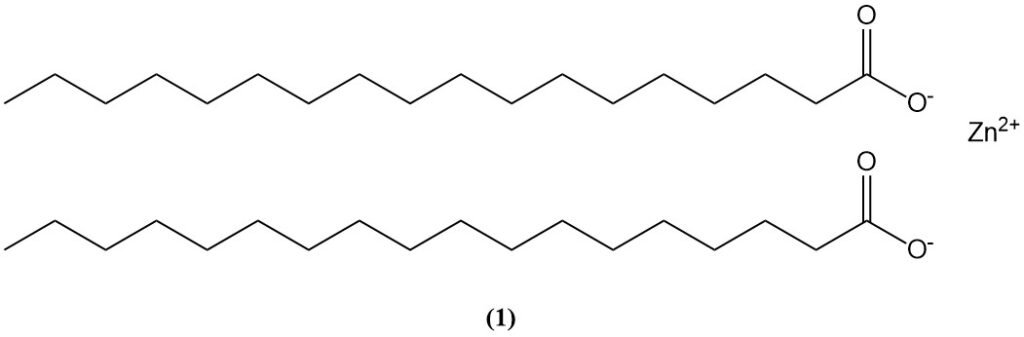
L’oxyde de zinc est thermiquement stable, mais il peut se dissocier à des températures extrêmement élevées. Cette décomposition thermique est une étape clé de certains cycles thermochimiques pour la production d’hydrogène.
3. Production industrielle d’oxyde de zinc
Industriellement, l’oxyde de zinc est principalement produit par deux procédés principaux : le procédé indirect (procédé français) et le procédé direct (procédé américain). Une plus petite quantité est également produite par voie chimique humide.
Le procédé humide représente environ 1 à 2 % de la production d’oxyde de zinc. Le procédé direct contribue pour 10 à 20 %, et le procédé indirect fournit la majorité restante.
Historiquement, les matières premières du procédé direct étaient principalement constituées de minerais ou de concentrés de zinc. Le procédé indirect utilisait du zinc métallique vierge provenant des producteurs. La fabrication actuelle d’oxyde de zinc utilise principalement des résidus et du zinc secondaire.
Ce fait, associé aux exigences des utilisateurs en matière de pureté chimique élevée, a conduit à des modifications des procédés et au recours à diverses techniques de purification.
3.1. Production d’oxyde de zinc par procédé direct ou américain
Le procédé direct, ou américain, de production d’oxyde de zinc se caractérise par sa simplicité, sa rentabilité et son rendement thermique élevé. Il implique une réduction initiale à haute température (1 000 à 1 200 °C) des matériaux contenant du zinc. Le charbon est utilisé comme agent réducteur. La réduction s’effectue selon les réactions de Boudouard :
ZnO + C ⇌ Zn + CO
ZnO + CO ⇌ Zn + CO
2 C + O2 ⇌ CO
2 CO2 + C ⇌ 2 CO
La vapeur de zinc et le monoxyde de carbone gazeux subissent ensuite une oxydation pour former de l’oxyde de zinc et du dioxyde de carbone au-dessus du lit réactionnel ou à la sortie du four.
Diverses matières premières contenant du zinc sont utilisées. Il s’agit notamment des concentrés de zinc, des résidus de métallisation, de l’hydroxyde de zinc (sous-produit) et, principalement, des scories de zinc provenant des fours de coulée ou des opérations de galvanisation. Les scories doivent être prétraitées par chauffage à environ 1 000 °C dans des fours rotatifs afin d’éliminer les impuretés de chlorure et de plomb.
Actuellement, seuls les fours rotatifs sont utilisés pour le procédé direct. Les fours statiques ne sont plus utilisés. Les matières premières contiennent généralement entre 60 % et 75 % de zinc. Il existe deux principaux types de fours rotatifs : les fours longs et étroits et les fours plus courts et plus larges.
1. Fours longs et étroits : Ces fours mesurent environ 30 m de long et 2,5 m de diamètre et sont chauffés au gaz ou au fioul. La matière première, un mélange de substance contenant du zinc et de charbon, est alimentée en continu à contre-courant ou à co-courant des gaz de combustion.
Les résidus, contenant du zinc résiduel et du charbon imbrûlé, sortent en continu du four à l’extrémité opposée au point d’alimentation. L’excédent de charbon est tamisé et recyclé. Les gaz de combustion, composés de vapeur de zinc, de ZnO et de CO, pénètrent dans une chambre où l’oxydation s’achève et où les grosses particules d’impuretés se déposent.
Les gaz sont ensuite refroidis par un échangeur de chaleur ou par dilution à l’air. L’oxyde de zinc est ensuite collecté dans des filtres à manches.
2. Fours plus courts et plus larges : Ce type de four rotatif mesure environ 5 m de long et 3 m de diamètre. Le chargement des matières premières est continu ; cependant, les résidus dézincifiés sont éliminés par lots.
Les conditions de fonctionnement des deux types de fours sont contrôlées avec précision afin de garantir un rendement élevé et l’obtention de la forme et de la taille de particules souhaitées. La pureté chimique, en l’absence de contamination externe, est uniquement déterminée par la composition des matières premières initiales.
3.2. Production d’oxyde de zinc par procédé indirect ou French
Dans le procédé indirect, ou French, le zinc est porté à ébullition et la vapeur de zinc formée subit une oxydation par combustion à l’air selon des paramètres contrôlés. Les propriétés cristallographiques et physiques de l’oxyde de zinc généré peuvent être ajustées en modifiant les conditions de combustion, telles que la turbulence de la flamme et l’excès d’air.
La composition chimique du ZnO produit dépend exclusivement de la composition de la vapeur de zinc.
Différents types de fours permettent de produire de la vapeur de zinc avec la pureté requise à partir de diverses matières premières, garantissant ainsi un rendement élevé en zinc.
Les matières premières utilisées dans ce procédé comprennent le zinc pur (super haute qualité, SHG ; haute qualité, HG) et, de plus en plus, des résidus métalliques (par exemple, ferrailles de zinc, scories de moulage sous pression, scories de galvanisation). Avant l’oxydation, des techniques de séparation en phase liquide ou vapeur éliminent les impuretés telles que le cadmium, le plomb, le fer et l’aluminium du zinc métallique.
Les méthodes spécifiques de vaporisation et de purification du zinc comprennent :
1. Fours à moufle ou cornues (graphite/carbure de silicium) : la charge métallique est introduite dans le four sous forme de lots solides ou de flux liquides continus. La chaleur de vaporisation est fournie par le chauffage externe de la cornue à l’aide d’un brûleur.
Des résidus non volatils, tels que le fer et le plomb provenant des scories de fusion, s’accumulent dans la cornue. Il est nécessaire d’éliminer périodiquement ces résidus, souvent en inclinant la cornue.
2. Distillation fractionnée : La vapeur de zinc, contenant des impuretés telles que le cadmium, le plomb, le fer, l’aluminium et le cuivre, peut être purifiée par distillation fractionnée. Ce procédé se déroule dans des colonnes, souvent équipées de plaques de carbure de silicium (par exemple, celles de la New Jersey Zinc Co.). L’oxydation de la vapeur de zinc purifiée a lieu à la sortie de la colonne.
3. Fours à deux chambres : La matière première métallique, principalement en gros morceaux, pénètre dans une chambre de fusion primaire, reliée à une chambre secondaire chauffée électriquement. La distillation a lieu dans la seconde chambre, à l’abri de l’air.
Les résidus non métalliques sont extraits de la surface de la chambre de fusion. Les impuretés, notamment le fer, l’aluminium et une partie du plomb, s’accumulent dans la chambre de distillation et sont périodiquement éliminées sous forme liquide. Les traces de plomb résiduelles sont ensuite éliminées par distillation fractionnée. Lundevall a développé la première version de ce type de four.
4. Procédé de fusion en four rotatif : L’oxyde de zinc indirect peut également être produit par fusion dans un four rotatif, à partir des mêmes matières premières. La fusion, la distillation et une partie de l’oxydation se déroulent dans une seule zone de réaction, ce qui permet d’exploiter une grande partie de la chaleur de combustion du zinc.
Le contrôle de la température et des pressions partielles de dioxyde de carbone et d’oxygène permet de limiter la teneur en impuretés de plomb et d’ajuster la forme et la taille des particules de ZnO, bien qu’avec moins de précision que d’autres méthodes.
3.3. Production d’oxyde de zinc par voie humide
L’oxyde de zinc est produit par voie humide, qui précipite le carbonate de zinc basique à partir de solutions purifiées de sulfate ou de chlorure de zinc. Le précipité est lavé et filtré, puis calciné pour former de l’oxyde de zinc. Cette méthode produit du ZnO à surface spécifique élevée.
Des produits similaires sont obtenus à partir d’hydroxydes résiduaires, qui sont purifiés chimiquement puis calcinés.
3.4. Post-traitement
Le post-traitement thermique, à des températures allant jusqu’à 1 000 °C, améliore les propriétés pigmentaires du ZnO et s’applique principalement aux oxydes produits par voie directe. La calcination atmosphérique contrôlée améliore encore les propriétés photoconductrices de l’oxyde de haute pureté, utilisé en photocopie.
La surface de l’oxyde de zinc peut être rendue plus organophile en l’enduisant d’huile et d’acide propionique. L’oxyde de zinc subit souvent une désaération. Il est parfois granulé ou granulé pour améliorer ses propriétés de manipulation.
A | B | C | D | |
---|---|---|---|---|
Paramètre | Procédé indirect | Procédé indirect | Procédé direct | Procédé humide |
ZnO (min.), % en poids | 99,5 | 99 | 98,5 | 93 |
Pb (max.), % en poids | 0,004 | 0,25 | 0,25 | 0,001 |
Cd (max.), % en poids | 0,001 | 0,05 | 0,03 | 0,001 |
Cu (max.), % en poids | 0,0005 | 0,003 | 0,005 | 0,001 |
Mn (max.), % en poids | 0,0005 | 0,001 | 0,005 | 0,001 |
Sels hydrosolubles (max.), % en poids | 0,02 | 0,1 | 0,65 | 1 |
Perte au feu (max.), % en poids | 0,3 | 0,3 | 0,3 | 4 |
Acidité, g H2SO4/100 g | 0,01 | 0,1 | 0,3 | 0,2 |
Surface spécifique, m2/g | 3–8 | 3–10 | 1–5 | 25 (min.) |
4. Utilisations de l’oxyde de zinc
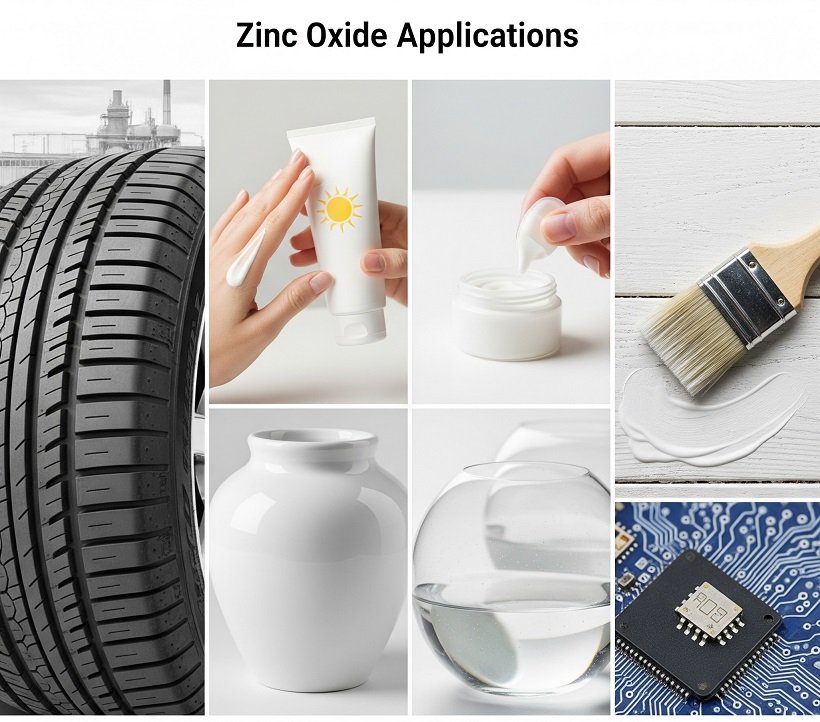
L’oxyde de zinc a de nombreuses utilisations, de loin la plus importante dans l’industrie du caoutchouc. Près de la moitié du ZnO mondial est utilisé comme activateur pour les accélérateurs de vulcanisation du caoutchouc naturel et synthétique.
4.1. Utilisation de l’oxyde de zinc dans la production de caoutchouc naturel et synthétique
L’ajout d’oxyde de zinc aux composés de caoutchouc contenant du soufre et des accélérateurs augmente la densité de réticulation. Pour les caoutchoucs à usage général, notamment le caoutchouc naturel et le caoutchouc styrène-butadiène, des dosages de ZnO allant jusqu’à environ 5 phr (parties pour cent de caoutchouc) permettent d’obtenir des valeurs de résistance à la traction et de contrainte élevées. Des dosages plus élevés n’améliorent pas ces propriétés.
Les acides gras activent le système caoutchouc-soufre-accélérateur-oxyde de zinc. L’acide stéarique ou le stéarate de zinc sont couramment utilisés. L’ajout de sels de zinc spécifiques, en plus du ZnO, peut augmenter la densité de réticulation et améliorer le comportement de réversion.
La réactivité de l’oxyde de zinc dépend de sa surface spécifique, mais la présence d’impuretés, telles que le plomb et les sulfates, l’influence également. L’oxyde de zinc assure une bonne durabilité du caoutchouc vulcanisé et augmente sa conductivité thermique. La teneur en ZnO varie généralement de 2 % à 5 %.
4.2. Utilisation de l’oxyde de zinc dans les peintures et revêtements
L’oxyde de zinc n’est plus le principal pigment blanc des peintures et revêtements. Cependant, il est toujours utilisé par les artistes pour son excellente couleur blanche. Il est utilisé comme additif dans les peintures de préservation du bois extérieur, ainsi que dans les peintures antisalissures et anticorrosion.
L’oxyde de zinc est généralement associé à d’autres pigments anticorrosion actifs. Son pouvoir inhibiteur repose sur sa capacité à réagir avec les substances corrosives et à maintenir un pH alcalin dans le revêtement. Il réagit également avec les liants acides pour former des savons et absorber les rayons ultraviolets (UV).
La teneur en plomb de l’oxyde de zinc commercial varie selon le fabricant, entre 0,002 % et 1,5 %. Un revêtement d’oxyde de zinc sans plomb nécessite une teneur en plomb inférieure à 1,5 %.
L’oxyde de zinc améliore la formation du film, la durabilité et la résistance à la moisissure. Il présente un effet synergique avec d’autres fongicides, car il peut réagir avec les produits acides de l’oxydation et absorber les rayons UV.
4.3. Utilisation de l’oxyde de zinc dans les industries pharmaceutique et cosmétique
Les industries pharmaceutique et cosmétique utilisent l’oxyde de zinc dans les poudres et les onguents en raison de ses propriétés bactéricides. Il était également utilisé pour former des ciments dentaires par réaction avec l’eugénol, mais son utilisation est aujourd’hui rare.
Les composants réactifs, ZnO et eugénol (80 à 96 % en poids), sont fournis sous forme de deux pâtes. Des huiles (par exemple, huile d’olive, huile minérale) et des charges (par exemple, talc, kaolin, colophane, vaseline) permettent d’ajuster la consistance. L’acétate de zinc et le chlorure de magnésium sont utilisés comme accélérateurs de formation d’eugénolate de zinc.
L’oxyde de zinc est également utilisé comme additif de protection UV dans les cosmétiques. Il est utilisé comme écran solaire sur et dans la couche cornée. Il agit comme un filtre lumineux « physique », principalement en réfléchissant et en diffusant les rayons UVA et UVB, offrant une protection à large spectre. Le ZnO micronisé et nanométrique est souvent utilisé pour réduire les résidus blancs visibles.
Il est utilisé comme pigment blanc pour la production de poudres colorées et de pigments nacrés, comme les fards à paupières en poudre.
L’oxyde de zinc est utilisé dans divers produits pour la peau en raison de ses propriétés apaisantes, astringentes et antiseptiques. On peut citer comme exemples les crèmes contre l’érythème fessier, les lotions à la calamine, les onguents antiseptiques et les traitements contre l’acné.
4.4. Utilisation de l’oxyde de zinc dans l’industrie de la céramique et du verre
L’oxyde de zinc est utilisé dans l’industrie du verre, de la céramique et des émaux pour abaisser les points de fusion et améliorer la brillance, l’éclat et la résistance aux fissures (prévention des craquelures et des frisures). Il peut également être utilisé pour modifier la brillance ou améliorer l’opacité.
Des concentrations plus élevées de ZnO permettent d’obtenir des surfaces mates et cristallines. Sa capacité thermique et sa conductivité thermique élevées sont avantageuses pour la production de céramique.
4.5. Utilisation de l’oxyde de zinc comme matière première
L’oxyde de zinc est utilisé comme matière première pour différents produits, notamment les stéarates, les phosphates, les chromates, les bromates, les dithiophosphates organiques et les ferrites (ZnO, MnO, Fe2O3). Il est également utilisé en électrozingage (notamment dans les formulations de bains de cyanure).
L’oxyde de zinc est utilisé comme source de zinc dans l’alimentation animale et pour la désulfuration des gaz.
L’oxyde de zinc est utilisé comme catalyseur dans les synthèses organiques, telles que la production de méthanol, souvent en association avec d’autres oxydes. Il entre également dans la composition de certains adhésifs.
4.6. Utilisation de l’oxyde de zinc en électronique
Le ZnO de la plus haute pureté, calciné avec des additifs comme l’oxyde de bismuth (Bi2O3), est utilisé dans la production de varistances, caractérisées par une résistance dépendante de la tension, c’est-à-dire un comportement non ohmique.
Une composition typique comprend 96,5 % en masse de ZnO, 0,5 % de Bi2O3, 1 % de CoO, 0,5 % de MnO, 1 % de Sb2O3 et 0,5 % de Cr2O3. Le comportement non ohmique résulte de la présence de grains de ZnO semi-conducteurs et d’une fine phase isolante au joint de grains.
Une varistance à oxyde métallique à base de ZnO dopé au bismuth est supérieure aux varistances classiques en carbure de silicium (SiC) car ses caractéristiques tension-courant présentent une pente beaucoup plus faible, ce qui se traduit par une augmentation de tension par unité de courant bien plus faible.
Les propriétés photoconductrices du ZnO sont exploitées dans les procédés de photoreproduction. Le dopage à l’alumine réduit sa résistance électrique, ce qui permet son utilisation dans les revêtements des papiers maîtres pour la reproduction offset.
L’oxyde de zinc est un semi-conducteur à large bande interdite (3,3 eV). Cette propriété le rend idéal pour :
- les lasers UV et les LED, notamment pour les applications optoélectroniques à courte longueur d’onde ;
- les capteurs de gaz, en raison de sa sensibilité à divers gaz ;
- les électrodes conductrices transparentes dans des dispositifs tels que les cellules solaires (par exemple, comme couche tampon dans les cellules solaires CIGS) ;
- les transistors et les diodes ;
- les dispositifs piézoélectriques, étudiés pour les capteurs et la récupération d’énergie.
5. Toxicologie de l’oxyde de zinc
Contrairement à d’autres métaux lourds, le zinc n’est pas classé comme intrinsèquement toxique ou dangereux. C’est un élément essentiel à la physiologie humaine, animale et végétale. Le corps humain contient environ 2 g de zinc. Un apport quotidien de 10 à 20 mg est recommandé.
La DL50 orale chez le rat est de 630 mg/kg. Les concentrations de poussière d’oxyde de zinc dans l’air ambiant sont autorisées à 5 mg/m³ (MAK) et 10 mg/m³ (TLV-TWA). Pour les fumées d’oxyde de zinc, les valeurs sont de 5 mg/m³ (TLV-TWA) et 10 mg/m³ (TLV-STEL).
Les valeurs limites d’exposition professionnelle (LEP) pour l’oxyde de zinc sont détaillées dans le Tableau 3.
Pays | VME sur 8 h, mg/m3 | VLE sur 15 min, mg/m3 | Références |
---|---|---|---|
États-Unis | 5 (fumées), 10 (poussières) | 10 (fumées) (plafond) | ACGIH (1991, valeurs indicatives) |
États-Unis | 5 (fumées), 15 (poussières ; totales), 5 (poussières ; respirables) | OSHA (1989, valeurs limites légales) | |
Pays-Bas | 5 (fumées) | SZW (1997) | |
Allemagne | 5 (fumées), 6 (poussières) | DFG (1997) | |
Royaume-Uni | 5 (fumées), 10 (poussières) | HSE (1998) | |
Suède | 5 (fumées) | Conseil national de la sécurité et de la santé au travail, Suède (1993) | |
Danemark | 4 (fumées), 10 (poussières) | Arbejdstilsynet (1992) |
L’ingestion ou l’inhalation accidentelle de grandes quantités de ZnO peut provoquer de la fièvre, des nausées et une irritation des voies respiratoires après plusieurs heures. Ces symptômes sont transitoires et disparaissent rapidement sans conséquences à long terme.
Références
- Pigments, Inorganic, 2. White Pigments. – https://onlinelibrary.wiley.com/doi/10.1002/14356007.n20_n01.pub2
- Rubber, 9. Chemicals and Additives. – https://onlinelibrary.wiley.com/doi/10.1002/14356007.a23_365.pub3
- Pigments, Inorganic, 5. Anticorrosive Pigments. – https://onlinelibrary.wiley.com/doi/10.1002/14356007.n20_n04
- Pigments, Inorganic, 7. Transparent Pigments. – https://onlinelibrary.wiley.com/doi/10.1002/14356007.n20_n06
- Dental Materials. – https://onlinelibrary.wiley.com/doi/10.1002/14356007.a08_251.pub2
- Skin Cosmetics. – https://onlinelibrary.wiley.com/doi/10.1002/14356007.a24_219
- Ceramics, Electronic. – https://onlinelibrary.wiley.com/doi/10.1002/14356007.a06_079.pub2
- The effect of formulation on the penetration of coated and uncoated zinc oxide nanoparticles into the viable epidermis of human skin in vivo
- Zinc Compounds. – https://onlinelibrary.wiley.com/doi/10.1002/14356007.a28_537.pub2