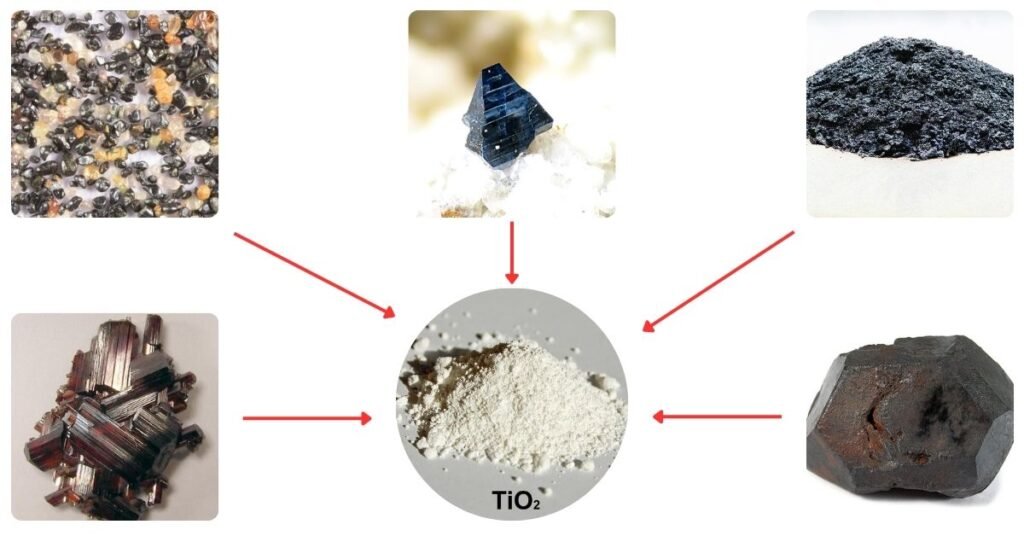
Les matières premières utilisées pour la production de dioxyde de titane comprennent des produits naturels tels que l’ilménite, le leucoxène et le rutile, ainsi que des matières synthétiques très importantes comme les scories de titane et le rutile synthétique.
En 2007, la production totale de matières premières titanoferreuses a dépassé les 6 millions de tonnes. L’Australie est le premier producteur, suivie de l’Afrique du Sud, du Canada et de la Chine.
Le tableau 1 présente les données de production des principales matières premières contenant du titane.
Matière première | Localisation | Production minière, 103 t/a |
---|---|---|
Ilménite | Australie | 1400 |
Canada | 816 | |
Ukraine | 290 | |
Inde | 378 | |
Norvège | 377 | |
Afrique du Sud | 1100 | |
États-Unis | 300 | |
Chine | 550 | |
Vietnam | 254 | |
Brésil | 127 | |
Autres | 129 | |
Total | 5720 | |
Rutile (naturel et synthétique) | Australie | 340 |
Ukraine | 70 | |
Afrique du Sud | 120 | |
Sierra Leone | 80 | |
Inde | 20 | |
Autres | 30 | |
Total | 660 | |
Laitier de titane | Canada | 920 |
Norvège | 160 | |
Afrique du Sud | 1300 | |
Total | ~2400 |
1. Matières premières naturelles
Le titane est le neuvième élément le plus abondant de la croûte terrestre. Il forme régulièrement des composés avec l’oxygène. Parmi les minéraux naturels de titane, seuls l’ilménite (dont le leucoxène) et le rutile présentent une importance économique. Le leucoxène est formé par l’altération et la décomposition naturelles de l’ilménite.
Plus de 90 % de la production mondiale d’ilménite et de rutile est destinée à la production de pigments. Le reste est utilisé dans la fabrication du titane métallique et pour les revêtements des baguettes de soudage.
Le tableau 2 répertorie les minéraux contenant du titane les plus importants.
Minéraux | Formule | Teneur en TiO2, % en poids |
---|---|---|
Rutile | TiO2 | 92–98 |
Anatase | TiO2 | 90–95 |
Brookite | TiO2 | 90–100 |
Ilménite | FeTiO3 | 35-60 |
Leucoxène | Fe2O3TiO2 | 60 à 90 |
Pérovskite | CaTiO3 | 40 à 60 |
Sphène (titanite) | CaTiSiO5 | 30 à 42 |
Titanomagnétite | Fe(Ti)Fe2O4 | 2–20 |
1.1. Ilménite et leucoxène
L’ilménite est présente partout dans le monde dans des gisements massifs primaires et des gisements alluviaux secondaires (sable) contenant des minéraux lourds. Les minerais massifs associent fréquemment l’ilménite à des intrusions intermédiaires, comme celles trouvées à Tellnes, en Norvège, et au lac Allard, au Canada.
Les concentrés dérivés de ces minerais massifs présentent souvent une teneur élevée en fer, présent sous forme d’hématite ou de magnétite ségréguée au sein de l’ilménite. Ces composés de fer diminuent la teneur en dioxyde de titane des concentrés. L’utilisation directe de ces ilménites riches en fer a diminué.
L’enrichissement en ilménite des sables de plage, tant sur les côtes actuelles que fossiles, est important pour la production de dioxyde de titane. L’action des vagues, des courants ou du vent concentre l’ilménite et d’autres minéraux lourds, notamment le rutile, le zircon, la monazite et d’autres silicates, dans les dunes ou sur les plages. Ce processus de concentration entraîne souvent une stratification minérale.
L’exposition à l’eau de mer et à l’atmosphère sur plusieurs échelles de temps géologiques induit la corrosion de l’ilménite. Le fer est extrait du réseau cristallin de l’ilménite, enrichissant le matériau restant en dioxyde de titane. Le réseau reste stable avec des teneurs en TiO2 allant jusqu’à environ 65 %. Une élimination supplémentaire du fer produit un mélange minéral submicroscopique, principalement composé d’anatase, de rutile et de phases amorphes.
Les mélanges dont la teneur en dioxyde de titane peut atteindre 90 % sont appelés leucoxènes. Le leucoxène est présent dans l’ilménite corrodée et dans certains gisements ; il est récupéré et traité séparément. Cependant, les volumes de production de leucoxène sont faibles par rapport à ceux de l’ilménite.
Les concentrés de sable d’ilménite, appauvris en fer, présentent généralement une teneur en dioxyde de titane plus élevée que ceux des gisements massifs. Ces concentrés contiennent également du magnésium, du manganèse et du vanadium (inhérents à l’ilménite), ainsi que de l’aluminium, du calcium, du chrome et du silicium (provenant d’intrusions minérales).
Les réserves d’ilménite économiquement viables s’élèvent à environ 680 millions de tonnes, dont 30 % en Chine, 20 % en Australie, 13 % en Inde et 9 % en Afrique du Sud. Compte tenu des capacités de production actuelles, la demande mondiale pourrait être satisfaite pendant plus d’un siècle.
Composant | Tellnes (Norvège) | Richard’s Bay (Afrique du Sud) | Capel (Australie-Occidentale) | Quilon (Inde) |
---|---|---|---|---|
TiO2 | 43,8 | 46,5 | 54,8 | 60,3 |
Fe2O3 | 14,0 | 11,4 | 16,0 | 24,8 |
FeO | 34,4 | 34,2 | 23,8 | 9,7 |
Al2O3 | 0,6 | 1,3 | 1,0 | 1,0 |
SiO2 | 2,2 | 1,6 | 0,8 | 1,4 |
MnO | 0,3 | - | 1,5 | 0,4 |
Cr2O3 | - | 0,1 | 0,1 | 0.1 |
V2O5 | 0,3 | 0,3 | 0,2 | 0,2 |
MgO | 3,7 | 0,9 | 0,15 | 0,9 |
1.2. Rutile
Le rutile se forme principalement par cristallisation de magma, notamment à partir de magmas riches en titane et pauvres en fer. Il provient de la métamorphose de sédiments titanifères ou de magmatites.
Les concentrations de rutile dans les roches primaires sont trop faibles pour permettre une exploitation commerciale. Par conséquent, seuls les sables contenant du rutile, du zircon, de l’ilménite et d’autres minéraux lourds, sont considérés comme des réserves viables. Les réserves mondiales de rutile sont estimées à 45 millions de tonnes.
Les principaux producteurs de rutile naturel sont l’Australie, l’Afrique du Sud et la Sierra Leone. En 2007, la production minière mondiale de rutile a atteint environ 564 000 tonnes. L’offre de rutile naturel étant insuffisante pour répondre à la demande, le rutile synthétique le remplace largement.
Le tableau 4 présente la composition de certains concentrés de rutile.
Composante du rutile | Australie orientale | Sierra Leone | Afrique du Sud |
---|---|---|---|
TiO2 | 96,00 | 95,70 | 95,40 |
Fe2O3 | 0,70 | 0,90 | 0,70 |
Cr2O3 | 0,27 | 0,23 | 0,10 |
MnO | 0,02 | - | - |
Nb2O5 | 0,45 | 0,21 | 0,32 |
V2O5 | 0,50 | 1,00 | 0,65 |
ZrO2 | 0,50 | 0,67 | 0,46 |
Al2O3 | 0,15 | 0,20 | 0,65 |
CaO | 0,02 | - | 0,05 |
P2O5 | 0,02 | 0,04 | 0,02 |
SiO2 | 1,00 | 0,70 | 1,75 |
1.3. Anatase
L’anatase, un polymorphe du dioxyde de titane, est principalement présent dans d’importantes réserves au sein des intrusions carbonifères brésiliennes. Les techniques de préparation du minerai permettent de produire des concentrés contenant 80 % de TiO2. Un traitement ultérieur à l’acide chlorhydrique peut enrichir ces concentrés jusqu’à 90 % de TiO2.
La teneur estimée en dioxyde de titane de ces gisements minéraux atteint 108 tonnes.
1.4. Préparation du minerai
La production mondiale de minerai de titane provient principalement des sables minéraux lourds. La figure 1 illustre le processus de production.
L’ilménite coexiste fréquemment avec le rutile et le zircon ; par conséquent, la récupération de l’ilménite est liée à ces minéraux. Lorsque les conditions géologiques et hydrologiques le permettent, le sable brut, contenant généralement 3 à 10 % de minéraux lourds, est obtenu par dragage humide (a).
Après un essai au tamis (b), le sable brut subit une concentration gravimétrique en plusieurs étapes à l’aide de cônes de Reichert (d) ou de spirales (e) pour obtenir un produit contenant 90 à 98 % de minéraux lourds. Cet équipement sépare les minéraux lourds (densités : 4,2 à 4,8 g/cm³) des minéraux légers (densités : <3 g/cm³).
Les minéraux magnétiques, notamment l’ilménite, sont ensuite séparés des composants non magnétiques (rutile, zircon, silicates) par séparation magnétique sèche ou humide (f). Le minerai provenant de gisements non altérés subit d’abord une première élimination de la magnétite.
Une étape de séparation électrostatique (h) facilite l’élimination des impuretés minérales non conductrices nocives, telles que le granite, les silicates et les phosphates, de l’ilménite.
La fraction non magnétique (leucoxène, rutile, zircon) subit ensuite un traitement hydromécanique supplémentaire (i), à l’aide de tables vibrantes ou de spirales, afin d’éliminer les minéraux résiduels de faible densité, principalement le quartz.
Les ilménites et leucoxènes altérés faiblement magnétiques sont récupérés par séparation magnétique à haute intensité (j) lors d’une dernière étape sèche. Le rutile conducteur est ensuite séparé électrostatiquement du zircon non conducteur en plusieurs étapes (l). Un jet d’air élimine le quartz résiduel.
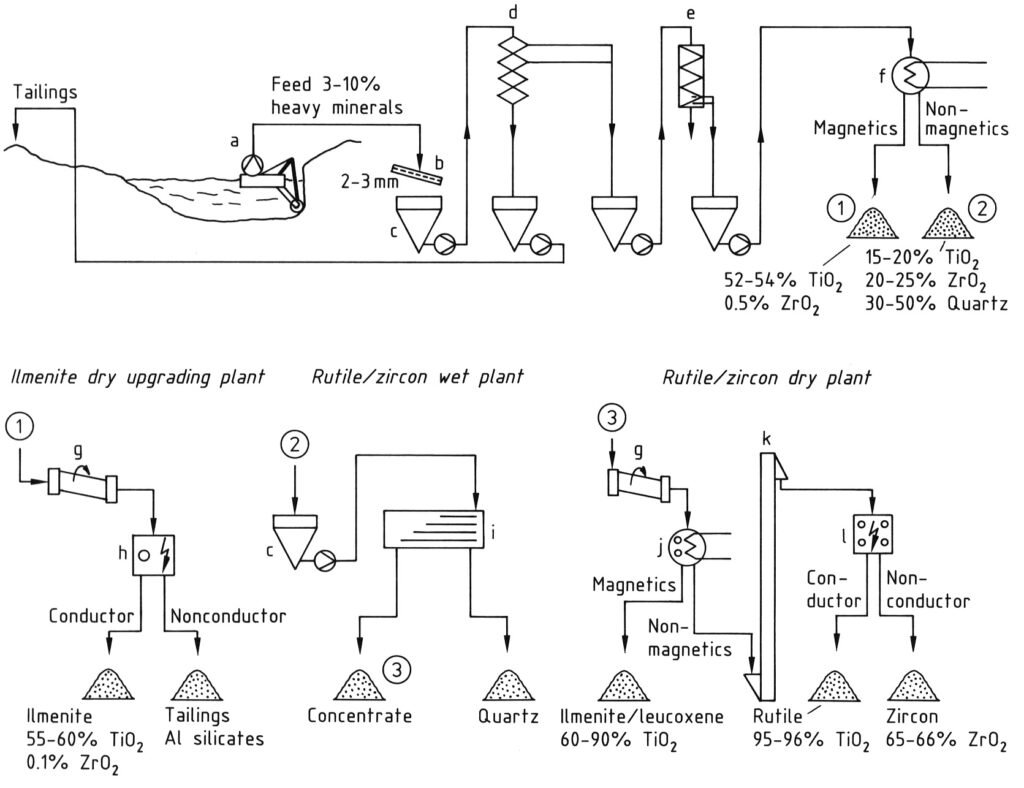
a) Drague ; b) Tamis ; c) Bunker ; d) Cônes de Reichert ; e) Spirales ; f) Séparateur magnétique ; g) Séchoir ; h) Séparateur électrostatique ; i) Table vibrante ; j) Séparateur magnétique sec ; k) Convoyeur à bande vertical ; l) Séparateur électrostatique
2. Matières premières synthétiques
La demande croissante de matières premières à forte teneur en dioxyde de titane a favorisé le développement de matières premières synthétiques. Dans toutes les méthodes de production, le fer est extrait des ilménites ou des titanomagnétites.
2.1. Laitier de titane
Le procédé métallurgique d’extraction du fer de l’ilménite repose sur la formation de laitier, au cours duquel le fer est réduit en métal à l’aide d’anthracite ou de coke à 1 200-1 600 °C dans un four à arc électrique. On obtient ainsi de la fonte brute sans titane et un laitier contenant 75 à 85 % de dioxyde de titane, selon le minerai utilisé.
Ce laitier est adapté à la chloration ou à la digestion à l’acide sulfurique en raison de sa teneur élevée en Ti3+ et de sa faible teneur en carbone. L’aptitude du laitier au procédé au chlorure ou au sulfate dépend de sa teneur en titane, de ses niveaux d’impuretés et de la granulométrie.
Le calcium et le magnésium exercent spécifiquement un effet néfaste sur le procédé au chlorure. Le laitier de titane est produit par QIT Fer et Titane Inc. au Canada, Richard’s Bay Minerals en Afrique du Sud et Tinfos AS à Tyssedal, en Norvège.
En 2007, la production totale de laitier a dépassé les 2 millions de tonnes, la majeure partie étant destinée au procédé au chlorure. Une partie de ce laitier subit un traitement supplémentaire pour produire un laitier valorisé, contenant plus de 95 % de TiO2, destiné au procédé au chlorure.
2.2. Rutile synthétique
Les gisements de rutile naturel sont rares et coûteux à exploiter. Par conséquent, divers procédés d’extraction du fer des concentrés d’ilménite ont été développés. Ces méthodes préservent la granulométrie du minéral, ce qui est optimal pour la chloration ultérieure en lit fluidisé.
Les procédés industriels impliquent la réduction du Fe3+ par le carbone ou l’hydrogène, parfois après une oxydation préliminaire de l’ilménite. La formation de Fe2+ dans un réseau d’ilménite activée ou de fer métallique dépend des conditions de réduction.
L’ilménite activée contenant du Fe2+ est traitée à l’acide chlorhydrique ou sulfurique dilué, idéalement sous pression. On obtient ainsi du rutile synthétique contenant 85 à 96 % de dioxyde de titane. Les solutions de sels de fer(II) obtenues sont concentrées puis décomposées thermiquement pour former de l’oxyde de fer et de l’acide chlorhydrique. L’acide chlorhydrique est recyclable pour la digestion.
Le fer métallique peut être éliminé par diverses méthodes. La littérature brevetable décrit les procédés suivants :
- Réduction de taille suivie d’une séparation physique (par exemple, séparation magnétique, flottation).
- Dissolution dans des solutions de chlorure de fer(III). Le sel de fer(II) obtenu subit une oxydation à l’air, produisant des oxydes-hydroxydes de fer et des sels de fer(III).
- Dissolution acide
- Oxydation à l’air en présence d’un électrolyte. Différentes phases d’oxyde de fer ou d’oxyde-hydroxyde de fer se forment selon l’électrolyte utilisé. Parmi les électrolytes utilisés, on peut citer les solutions de chlorure de fer(II), le chlorure d’ammonium ou le carbonate d’ammonium-acide carbonique.
- Oxydation par le sulfate de fer(III) issu de la digestion de l’ilménite, suivie de la cristallisation du sulfate de fer(II).
- Chloration pour produire du chlorure de fer(III).
- Réaction avec le monoxyde de carbone pour former des carbonyles de fer, qui se décomposent pour produire du fer de haute pureté.
La chloration partielle du fer dans le carbone est une autre méthode permettant d’augmenter la teneur en dioxyde de titane de l’ilménite. En 2008, 17 entreprises produisaient du rutile (naturel ou synthétique). Les principaux producteurs étaient Iluka (25 %), Richard’s Bay Minerals (RBM) (13 %), Sierra Leone Ltd. (12 %) et Consolidated Rutile Ltd. (CRL) (11 %).
Environ 60 % de la consommation mondiale de rutile est destinée à la production de pigments de dioxyde de titane. La production mondiale de rutile s’élevait à 663 000 tonnes en 2008.
Référence
Pigments, Inorganic, 2. White Pigments. – https://onlinelibrary.wiley.com/doi/10.1002/14356007.n20_n01.pub2