1. Proceso general para producir resinas amínicas
La producción de aminoresinas es un proceso de dos pasos: hidroximetilación y condensación. La hidroximetilación es la adición de formaldehído a un compuesto amino, como la urea, para formar un derivado de hidroximetilo. La condensación es la reacción de dos derivados de hidroximetilo para formar una molécula más grande.
Tabla de contenido
La reacción de hidroximetilación normalmente se lleva a cabo en un medio ligeramente alcalino o ligeramente ácido, mientras que la reacción de condensación requiere una solución más ácida. Las excepciones son las resinas de melamina-formaldehído, que requieren un pH alcalino, y las resinas de melamina-urea-formaldehído, que se condensan en medios ligeramente alcalinos.
El proceso para la producción de resinas amínicas continúa hasta que el producto resultante es una mezcla oligomérica que todavía es soluble o fusible. Luego se protege contra una mayor condensación alcalinizando el medio. La condensación de la resina mediante catálisis ácida, es decir, reticulación para dar un producto sustancialmente infusible, no se lleva a cabo hasta que la resina se pone en uso. Este proceso se llama curado.
Incluso en estado curado, pueden estar presentes grupos hidroximetilo libres. Los compuestos monomoleculares e hidroximetílicos con bajos grados de polimerización y hasta seis unidades de urea-formaldehído son prácticamente todos conocidos y pueden prepararse en forma pura.
Sin embargo, las soluciones acuosas de los oligómeros con bajos grados de polimerización no tienen una vida útil suficientemente larga. Sólo cuando las concentraciones de grupos hidroximetilo y NH2 se reducen mediante condensación parcial o cuando los productos están presentes en forma sólida poseen una vida útil industrialmente útil, es decir, de varias semanas o más.
Las condensaciones realizadas en exceso de un alcohol, tal como metanol o butanol, con la adición de ácido y eliminación de agua según sea necesario, producen resinas amínicas eterificadas (es decir, alquiladas) curables. Son solubles en disolventes no acuosos y se pueden mezclar con resinas alquídicas, resinas epoxi, etc. Se utilizan como materiales de partida en la producción de revestimientos de superficies.
Las colas de resina a base de urea, melamina o ambas se han sometido a una eterificación parcial para estabilizarlas contra una mayor condensación. Históricamente, estas resinas se han utilizado para la fabricación de madera contrachapada, pero prácticamente ya no se utilizan.
Las dificultades básicas que se encuentran en la producción de resinas amínicas son evitar que las resinas se solidifiquen durante el proceso de producción y lograr selectivamente ciertas propiedades, como una larga vida útil, un bajo contenido de formaldehído, bajas emisiones de formaldehído de los productos finales, resistencia y resistencia al hinchamiento de tablero de partículas después del curado.
1.1. Hidroximetilación
La hidroximetilación es la adición de formaldehído a un compuesto amino, como la urea, para formar un derivado de hidroximetilo. La reacción puede catalizarse mediante condiciones alcalinas o ácidas, pero se prefieren las condiciones alcalinas ya que dan como resultado una velocidad de reacción más rápida.
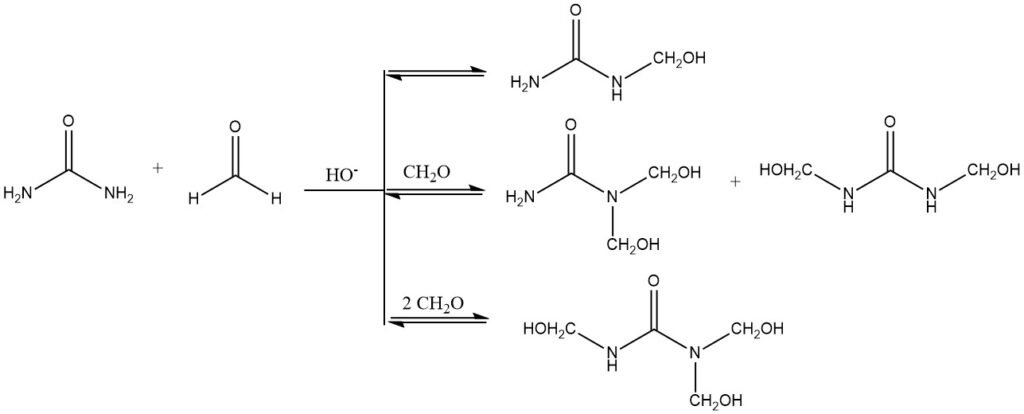
En medios alcalinos, la reacción de hidroximetilación se produce mediante la formación de un enlace semiminal. Este enlace es inestable y puede escindirse fácilmente, lo que significa que la reacción de hidroximetilación es reversible y se establece un equilibrio. Por este motivo es posible aislar mono, di y trihidroximetilurea, pero no tetrahidroximetilurea.
La hidroximetilación completa de todos los grupos amino para formar hexahidroximetilmelamina también es posible en condiciones alcalinas. La reacción es ligeramente exotérmica, lo que significa que se libera calor. La entalpía de hidroximetilación de la urea es de aproximadamente -23 kJ/mol.
La velocidad de reacción de la hidroximetilación se ve afectada por varios factores, incluida la concentración, la temperatura, el pH y la presencia de sustituyentes. En general, la velocidad de reacción aumenta con el aumento de la concentración, la temperatura y el pH. Los sustituyentes también pueden tener un efecto, ya que los grupos aceptores de electrones y los sustituyentes voluminosos disminuyen la velocidad de reacción.
Las velocidades de reacción de hidroximetilación se han medido con frecuencia, pero son sensibles a muchos parámetros. Esto dificulta definir una velocidad de reacción global para procesos industriales, que producen mezclas variables de oligómeros con unidades repetidas mixtas. Además, las importantes propiedades de la resina no se han correlacionado con las velocidades de reacción individuales.
A pesar de estos desafíos, la hidroximetilación es una reacción importante en la producción de resinas amínicas. Al comprender el mecanismo de reacción y los factores que afectan la velocidad de reacción, es posible optimizar el proceso y producir resinas de alta calidad con las propiedades deseadas.
1.2. Condensación
La condensación de derivados de hidroximetilo está catalizada por ácidos. También se pueden utilizar álcalis fuertes como catalizadores, pero las resinas amínicas resultantes no tienen importancia industrial. La condensación puede tener lugar a través de las siguientes vías:
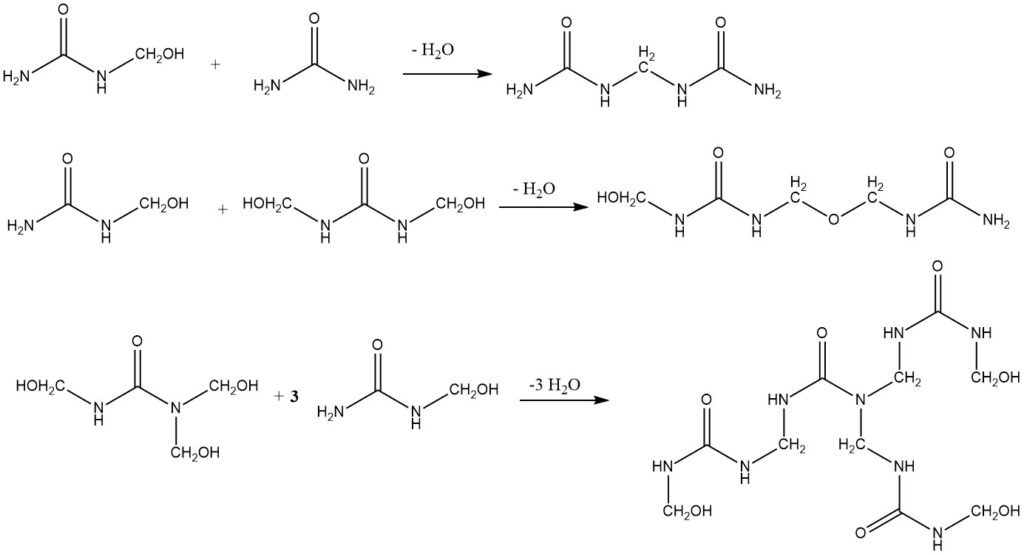
La presencia de compuestos de metileno en resinas amínicas se puede establecer mediante espectroscopia de RMN de 13C , pero los éteres de bis(ureametileno) sólo se pueden detectar indirectamente.
La espectroscopia de RMN 13C se puede utilizar para dilucidar muchas de las estructuras, pero no distingue entre los átomos de C que se muestran en (1) y (2), aunque sus terceros vecinos más cercanos son diferentes. Este problema se presenta también en el caso de las resinas de melamina.
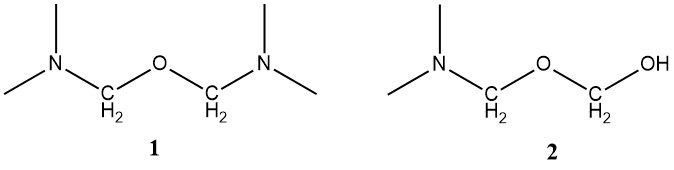
Los enlaces de metileno entre dos moléculas de urea son muy estables y sólo pueden hidrolizarse mediante ácidos fuertes a temperaturas elevadas. La reacción de condensación es ligeramente exotérmica, con una entalpía de -28 kJ/mol.
La estabilidad del enlace metileno-éter se encuentra entre la del enlace hidroximetilo y la del enlace metileno. Es imposible dar una velocidad de reacción única para el proceso de condensación porque hay muchos materiales de partida diferentes (compuestos de hidroximetilo) y muchos productos finales (compuestos de metileno).
El tipo de disolvente también influye en la velocidad de condensación. La dependencia de la reactividad de los compuestos hidroximetílicos de la composición química de los compuestos amino puede interpretarse basándose en varias reglas cualitativas.
1.3. Composición de una solución de aminoresina
La composición estructural de los oligómeros en soluciones de resinas amínicas se puede identificar mediante el uso de espectroscopía de RMN de 1H y 13C. Dentro del espectro, son detectables los hidratos de oligómeros de formaldehído, HO(CH2O)nH, con n aproximadamente igual a 5.
Se pueden distinguir varias estructuras de hidroximetilo, incluidos éteres como el hidroximetilmetiléter, observando los átomos de C correspondientes del alcohol original. Además se pueden detectar las estructuras (3) y (4) junto con compuestos anulares que contienen éteres cíclicos del tipo urona.
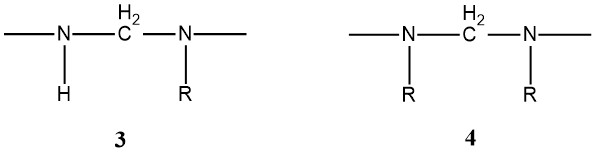
En un pegamento típico para tableros de partículas, el espectro de RMN de 13C podría mostrar, por ejemplo, las siguientes proporciones de átomos de carbono del formaldehído original (en fracciones molares):
- Formaldehído: 0,03
- Compuestos de hidroximetilo: 0,72
- Compuestos de metileno: 0,15
- Compuestos cíclicos: 0,10
También se pueden aplicar métodos analíticos alternativos para dilucidar mejor la estructura de la resina. Por ejemplo:
- Cromatografía líquida de alto rendimiento (HPLC), empleada principalmente para componentes de bajo peso molecular como urea, monometilolurea, N,N-dimetilolurea, N,N’-dimetilolurea, trimetilolurea y metilendiurea.
- Cromatografía de exclusión por tamaño, utilizada principalmente para especies de mayor masa molecular como dímeros y oligómeros.
2. Procesos de producción de resinas amino
Las resinas amino se producen normalmente en lotes de 5 a 100 metros cúbicos. Sin embargo, también se utilizan procesos continuos, especialmente para la producción de colas de resina. La literatura de patentes describe procesos en los que una etapa particular se opera de manera continua mientras que otras etapas se operan por lotes.
La velocidad de reacción y la composición del producto final están influenciadas por una gran cantidad de parámetros, por lo que la reacción debe controlarse cuidadosamente. Los parámetros de reacción importantes incluyen:
- Pureza o composición de los materiales de partida.
- Relación molar en cada una de las etapas de reacción.
- Tipo y cantidad de modificador
- Concentraciones de reactivo
- Valor de pH en cada etapa de la reacción.
- Temperatura en cada etapa de la reacción.
- Tipo y concentración de catalizador.
- Cantidad de sal tampón
- Tiempo de reacción en cada etapa.
2.1. Producción por lotes
El proceso por lotes es el método más común para producir resinas amínicas industrialmente. Tiene la desventaja de tener una capacidad de producción relativamente pequeña, pero permite una amplia variedad de productos y cambios frecuentes de producto.
Las reacciones se llevan a cabo en calderas agitadas en dos o más etapas a 70-100°C. En la primera etapa, que se lleva a cabo en una solución ligeramente ácida a alcalina, la reacción principal es la hidroximetilación.
En etapas posteriores se produce condensación, se elimina el agua y se forman productos de mayor peso molecular y viscosidad creciente. La duración de la condensación depende de las propiedades deseadas del producto.
En general, los productos se concentran hasta un 60-70% de soluciones acuosas mediante evaporación. Los materiales de partida, urea o melamina, se utilizan en forma de polvo. La urea también se puede utilizar en solución. El formaldehído se utiliza como una solución acuosa al 37-55%.
En algunos casos especiales, el formaldehído se utiliza en forma sólida, paraformaldehído. Finalmente, se pueden utilizar precondensados de urea-formaldehído en concentraciones no superiores al 80% en masa de los principios activos.
2.1.1. Soluciones acuosas
En la Figura 1 se ilustra un diagrama de planta para la producción por lotes de soluciones acuosas de resinas amino. El reactor consta de una caldera equipada con mecanismos de calentamiento y enfriamiento, un agitador, entradas para dispositivos de medición y adición de materia prima, una válvula inferior para descarga y una alcantarilla para su limpieza.
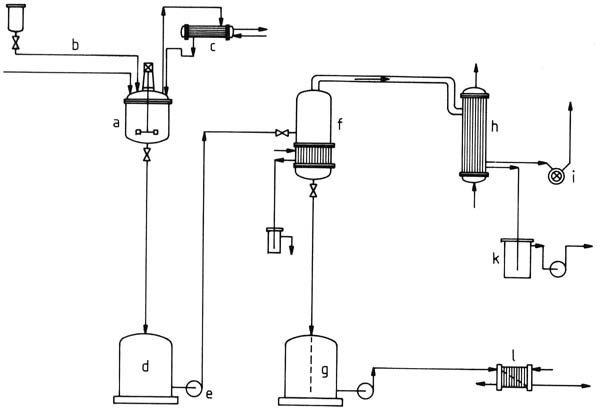
a) Caldera agitada; b) Alimentación de materias primas; c) Condensador de reflujo; d) Contenedor temporal; e) Bomba; f) Vaporizador; g) Contenedor para producto terminado; h) Condensador; i) Bomba de vacío; k) Recipiente para vapores condensados; l) Enfriador
Es habitual el uso de acero inoxidable, como materiales St. 1.4541 o St. 1.4571. Los serpentines internos o los tubos semicirculares fijados externamente facilitan el calentamiento y el enfriamiento. La agitación emplea agitadores de disco o de ancla robustos. Se incorporan boquillas para la adición controlada de materia prima, temperatura y medición de pH.
Una vez completada la condensación, puede tener lugar la evaporación del producto, ya sea en la caldera agitada o, más económicamente, en un vaporizador tubular de una o varias etapas. La evaporación se realiza a presión reducida para conservar la resina.
Luego se evalúa la calidad de la resina según las especificaciones y se transfiere a un contenedor de almacenamiento. Las tuberías pueden ser de aluminio o acero, ya que el medio es ligeramente alcalino, mientras que los tanques de producto pueden construirse de poliéster reforzado con fibra de vidrio o de hierro revestido.
Por ejemplo, un procedimiento típico para producir un pegamento para tableros de partículas implica introducir 85 partes (en masa) de urea sólida en 158 partes de una solución neutralizada de formaldehído al 50%. La mezcla se mantiene a 80°C durante 10 minutos para facilitar la hidroximetilación.
Luego se ajusta el pH a 4-5 usando una solución de ácido fórmico al 10%. Una mayor condensación eleva la temperatura a 90-100 °C en cuestión de minutos. Esta temperatura se mantiene hasta que se alcanza un punto final específico, determinado por la formación de un precipitado blanco o el logro de una viscosidad designada.
Luego se alcaliniza ligeramente la mezcla de reacción usando una solución de hidróxido de sodio al 25% para detener la condensación. Se añade urea adicional para lograr una relación molar de formaldehído a urea de 1,1.
La solución final contiene aproximadamente un 60% de sólidos, que se pueden evaporar a presión reducida para alcanzar una concentración comercial del 66%.
2.1.2. Polvos de resina amino
Para la producción de polvos de resina amino, inicialmente se produce una solución acuosa de resina y luego se somete a secado por aspersión (Figura 2).
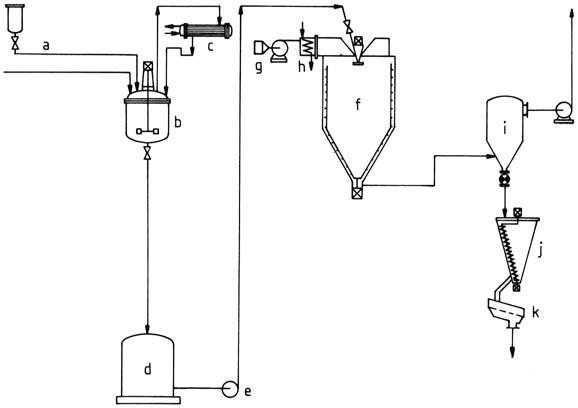
a) Alimentación de materia prima; b) Caldera agitada; c) Condensador de reflujo; d) Contenedor temporal; e) Bomba; f) Secador por aspersión; g) Soplador; h) Calentador de aire; i) Filtro; j) recipiente de mezcla; k) Tamiz vibratorio
La solución se atomiza usando un disco rociador o una boquilla en un secador por aspersión. Las gotas resultantes se secan en una corriente de gas caliente generada ya sea por calentamiento indirecto del aire o mezclando gas de escape caliente con aire. El polvo se recoge, se tamiza y luego se envasa.
2.1.3. Productos eterificados que contienen disolvente
Los productos que contienen disolventes, adecuados para fabricar revestimientos de superficies, se pueden producir en reactores similares a los utilizados para soluciones acuosas (Figura 3).
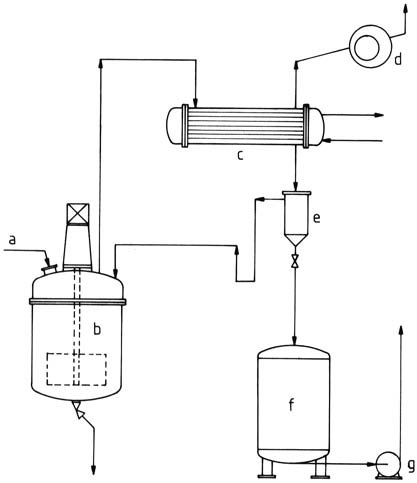
a) Alimentación de materia prima; b) Caldera agitada; c) Condensador; d) Bomba de vacío; e) Recipiente separador (separador de agua); f) Recipiente del producto; g) bomba
Para vaporizar la mezcla de agua y alcohol en exceso, a menudo butanol, se necesita un intercambiador de calor suficientemente grande.
Un separador de agua está colocado detrás del intercambiador de calor. La fase acuosa que se separa todavía contiene formaldehído y alcohol residuales y necesita procesamiento adicional. Con el contenido de alcohol adecuado, la fase disolvente se recicla al proceso de producción.
Para la producción de una resina de melamina-formaldehído butilada para revestimientos de superficies, se ponen a reflujo melamina y formaldehído en una solución acuosa al 40%, junto con butanol. Después de la destilación del agua, se enfría la mezcla, se determina el contenido de resina y se ajusta la concentración al 50% usando butanol.
2.2. Producción Continua
La producción industrial continua de resinas amínicas se introdujo para satisfacer la creciente demanda de estas resinas. Sin embargo, la producción continua tiene algunas desventajas.
La cantidad de resina producida por unidad de tiempo en una planta particular sólo puede variar dentro de límites relativamente estrechos. Esto se debe a que la residencia prolongada en condiciones constantes aumenta la proporción de moléculas con altos grados de condensación.
Además, no es fácil cambiar el producto que se produce en un proceso continuo. Si la planta no se limpia previamente, se producirá durante un tiempo un producto con una composición entre el producto antiguo y el nuevo.
Por este motivo, la producción continua se suele utilizar para una gama limitada de productos. Sin embargo, produce una calidad de producto muy uniforme.
La literatura de patentes describe una gran cantidad de procesos continuos para producir resinas amínicas. Estos procesos se diferencian únicamente en la tecnología del proceso para el flujo del producto.
Las diferencias normalmente implican variaciones en la temperatura, el pH, la concentración o los modificadores. Por lo demás, el proceso y el flujo del producto son los mismos.
En muchos casos, las publicaciones solo describen plantas a escala piloto o de laboratorio que no han sido ampliadas para uso industrial.
2.2.1. Soluciones acuosas de resinas amino
La producción continua de soluciones acuosas de aminorresinas implica diversos aparatos, tales como reactores tubulares, cascadas de calderas agitadas o combinaciones de ambos.
Los procesos continuos presentan un mayor riesgo de incrustaciones debido a productos insolubles altamente condensados en comparación con los procesos por lotes.
En los procesos por lotes, los residuos se disuelven en soluciones de resina frescas, un mecanismo que no se aplica con tanta eficacia en los procesos continuos debido a la limitada retromezcla.
En la literatura de patentes se han detallado varios procesos de producción continua:
1. Girdler Corp. (1943) describió un proceso de dos reactores en el que los reactivos se mezclaban en el primer reactor, se calentaban bajo presión y luego se trasladaban a una segunda etapa para su condensación.
2. Sherwood Paints (1949) empleó una columna empaquetada para la reacción, expulsando vapor de agua a través de una corriente de gas en contracorriente.
3. Allied Chemical Corp. (1951) utilizó un reactor de serpentín tubular, seguido de evaporación. Otro proceso de Allied Chemical Corp. (1952) utilizó vapor inyectado bajo presión.
4. Spumalit-Anstalt (Liechtenstein) utilizó un catalizador sólido (resina de policarbamida) bajo presión para formar la resina.
5. Rütgerswerke (Alemania, 1955) empleó un intercambiador de iones como catalizador de lecho fijo para resinas utilizadas en compuestos de moldeo.
6. Skanska Attifabriken AB (Suecia, 1955) utilizó un proceso de dos cámaras en el que los materiales de partida se condensaban parcialmente en la primera cámara antes de completar la reacción en la segunda cámara.
7. Du Pont (1956) describió un proceso en cascada que implicaba de dos a cuatro calderas agitadas para producir resinas eterificadas de formaldehído-urea.
8. El proceso de Meissner (1966) llevó a cabo la etapa de hidroximetilación de forma continua mientras que la etapa de condensación posterior funcionó por lotes.
9. BASF (1971) describió un proceso que utiliza una cascada de tres o más calderas agitadas para la hidroximetilación seguida de condensación (Figura 4).
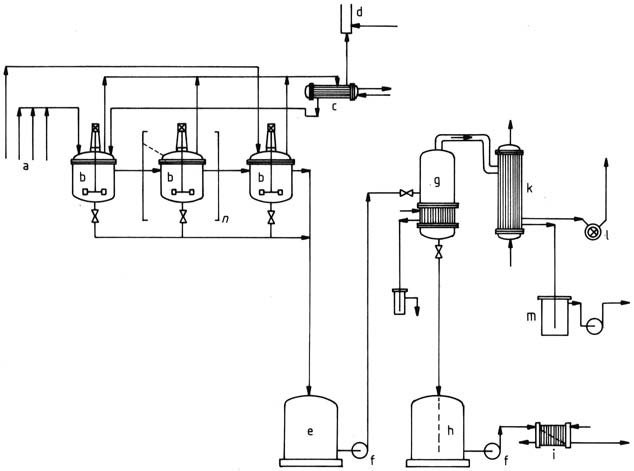
a) Alimentación de material de partida; b) Caldera agitada; c) Condensador de reflujo; d) llamarada; e) Contenedor temporal; f) Bomba; g) Vaporizador; h) Envase del producto; i) Enfriador; k) Condensador; l) Bomba de vacío; m) Contenedor para vapores condensados
10. Stamicarbon y American Cyanamid discutieron la producción continua de soluciones concentradas de melamina-formaldehído ricas en formaldehído para materiales de partida de aminoresinas.
11. DSM describió un proceso continuo en el que se prepara resina de condensación en un medio acuoso a temperaturas y presión elevadas, utilizando un reactor tubular con elementos mezcladores estáticos.
Cada uno de estos procesos demuestra los diversos enfoques adoptados para lograr una producción continua de aminoresinas y al mismo tiempo afrontar desafíos como la incrustación y la variedad de productos.
2.2.2. Resinas en polvo
Las resinas en polvo también se pueden producir continuamente alimentando las soluciones de pulverización, que normalmente se producen en lotes, de forma continua desde un contenedor temporal a una torre de pulverización.
La torre de aspersión es una cámara alta y estrecha donde las soluciones de aspersión se atomizan en finas gotas. Luego, las gotas se secan con aire caliente o gas. El polvo de resina seco se recoge en el fondo de la torre.
Este proceso es continuo porque las soluciones de pulverización se alimentan continuamente a la torre. Esto permite una calidad del producto más consistente que el proceso por lotes.
2.3. Producción de Productos Especiales y Espumas
Además de las resinas de impregnación, otros productos especiales incluyen resinas espumadas y resinas para auxiliares de papel, adhesivos para etiquetas, licuantes de hormigón, auxiliares para cuero, revestimientos para alfombras, microcápsulas, etc. Estas resinas normalmente se producen en lotes porque se producen en cantidades relativamente pequeñas y existe una amplia variedad de productos.
La producción de resinas espumadas es similar a la producción de colas de resina. El know-how patentado de estos productos se refiere a modificadores y variaciones pequeñas pero importantes en el proceso.
Las resinas espumantes son un tipo interesante de resina amino que se utiliza para producir espumas sólidas. Estas espumas tienen una amplia variedad de aplicaciones, incluido el aislamiento térmico, el aislamiento acústico, el acondicionamiento del suelo en la agricultura, el relleno de cavidades mineras, el material portador para líquidos de limpieza y el recubrimiento de vertederos.
Las primeras resinas espumadas se produjeron en los años 30. El proceso implica agregar un agente espumante y aire a una solución de pegamento. El agente espumante hace que la solución forme burbujas y el aire ayuda a expandirlas.
Luego, la resina se cura y forma una espuma sólida. Las resinas de urea formaldehído espumadas secas tenían densidades aparentes que oscilaban entre 5 y 70 kg/m3, adoptando más del 60% de la espuma la forma de células abiertas.
El desarrollo de aparatos portátiles para la producción in situ de resinas espumadas dio lugar a aplicaciones mucho más amplias para estos productos. Hoy en día, las resinas espumadas se utilizan en una variedad de industrias, incluidas la construcción, la automoción y el embalaje.
Referencias
- Amino Resins; Ullmann’s Encyclopedia of Industrial Chemistry. – https://onlinelibrary.wiley.com/doi/10.1002/14356007.a02_115.pub2
- Amino resin and a method for its production. – https://patents.google.com/patent/EP0277106B1/en
- Amino resins; Encyclopedia of Polymer Science and Technology. – https://onlinelibrary.wiley.com/doi/abs/10.1002/0471440264.pst017