El benceno se producía tradicionalmente a partir del carbón, pero el petróleo se convirtió en la fuente principal a mediados del siglo XX debido a nuevos procesos y al aumento de la demanda. El craqueo catalítico y el reformado de fracciones de petróleo producen benceno y otros aromáticos.
Tabla de contenido
1. Producción de benceno a partir del carbón
La carbonización del carbón produce aceites ligeros que contienen benceno, tolueno y xilenos (BTX). El rendimiento y composición de estos aceites dependen del tipo de carbón y de la temperatura de carbonización.
La coquización a baja temperatura produce un coque de combustión limpia con un menor contenido de benceno. La coquización a alta temperatura produce un coque duro para altos hornos y aceites ligeros con un mayor contenido de benceno.
Los aceites ligeros se separan de los alquitranes de hulla y la fracción BTX se extrae utilizando una fracción de petróleo de alto punto de ebullición. Luego se recupera la BTX del aceite absorbente y se purifica mediante destilación, tratamiento con ácido sulfúrico e hidrotratamiento. La extracción con disolventes y el fraccionamiento cercano se utilizan para aislar componentes aromáticos individuales.
Se han desarrollado varios procesos para refinar el corte de BTX en benceno de alta pureza o componentes de BTX de calidad superior. El proceso Houdry-Litol es un ejemplo de un proceso que utiliza una serie de reacciones y un reactor catalítico para refinar el corte de BTX. El proceso Litol modificado es particularmente adaptable para materiales aromáticos complejos de hornos de coque.
También se puede obtener una pequeña cantidad de benceno a partir de la destilación de alquitranes de coque, pero esta fuente no es de gran importancia en la producción de benceno. Los alquitranes de hulla son más importantes como fuente de brea, naftaleno, antraceno y otros materiales aromáticos condensados.
2. Producción de benceno a partir del petróleo
El craqueo catalítico y el reformado del petróleo, desarrollados a finales de los años 1930 y 1940, se convirtieron en una nueva fuente de benceno, tolueno, xilenos y aromáticos superiores. El petróleo reemplazó al carbón como fuente de materiales BTX, especialmente en Estados Unidos. La transición del carbón al petróleo se produjo en el Reino Unido y Europa alrededor de 1960.
El tolueno tuvo una gran demanda durante la Segunda Guerra Mundial para la producción de TNT. Sin embargo, era caro producir a partir de naftas vírgenes y, más tarde, a partir de naftas reformadas y craqueadas catalíticamente. Uno de los primeros procesos de craqueo catalítico fue desarrollado por Houdry Corp.
Este proceso utilizó un catalizador de sílice-alúmina depositado en varios lechos fijos y regenerado frecuentemente con aire para quemar el coque depositado. Otro proceso desarrollado por Mobil Oil utilizó un catalizador de sílice-alúmina de lecho móvil. El tercer tipo de proceso, desarrollado por Exxon y otros, se conoce como proceso de craqueo catalítico fluido (FCC) y ahora se utiliza exclusivamente.
Aunque los procesos de craqueo catalítico se desarrollaron principalmente para aumentar el rendimiento y el octanaje de los combustibles para motores, la gasolina producida tenía un alto contenido aromático, lo que proporcionaba una fuente de benceno petroquímico.
2.1. Benceno de Reformado
El reformado catalítico se convirtió en otra fuente de aromáticos BTX procedentes del petróleo. Se instaló en la década de 1940 y principios de la de 1950 para satisfacer la creciente demanda de benceno, que se utilizaba para fabricar resinas, detergentes, fibras sintéticas y otros productos químicos.
La reforma implica deshidrogenar naftenos a aromáticos o isomerizar alquilnaftenos seguido de deshidrogenación. Las parafinas también se pueden deshidrociclar a compuestos aromáticos. La reacción es lenta, por lo que se deben ajustar las condiciones del proceso para que sea económica. También puede producirse una pequeña cantidad de desalquilación de compuestos aromáticos alquilados.
Las primeras unidades de reformado catalítico utilizaban catalizadores de metales base, como molibdeno sobre alúmina activada. Estos procesos tenían una duración de ciclo corta y requerían una regeneración frecuente del catalizador.
El proceso de hidroformado operó a temperaturas y presiones elevadas con reciclaje de hidrógeno. Convirtió fracciones de nafta en gasolinas de alto octanaje. El catalizador requirió regeneración cada 8-16 horas.
Los procesos de reformado catalítico posteriores utilizaron lechos de catalizador móviles o lechos fluidizados con un catalizador finamente dividido. También se han desarrollado varios procesos catalíticos que utilizan platino sobre alúmina y platino con modificadores sobre alúmina.
Estos procesos pueden tener ciclos de hasta seis meses o mucho menos, dependiendo de la materia prima, las condiciones del proceso y la severidad de la operación. La materia prima de nafta debe tratarse previamente con hidrotratamiento catalítico para eliminar los compuestos de azufre.
Los procesos comerciales de reformado catalítico incluyen: reformado catalítico (Institut Français du Pétrole), magnaformación (Engelhard Industries), plataformas (UOP), formación de potencia (Exxon Research & Engineering), reniformación (Chevron Research Co.) y ultraformación (Standard Oil of Indiana). .
Las condiciones de funcionamiento varían ampliamente. Las temperaturas oscilan entre 425 y 525 °C y las presiones manométricas entre 0,7 y 3,5 MPa.
Las conversiones de nafteno se acercan al 100%. La ciclación de parafinas es mucho menor. Por ejemplo, para producir benceno a partir de C6 y reservas superiores, el metilciclopentano se isomeriza a ciclohexano y se deshidrogena a benceno. La conversión de n-hexano en benceno es limitada.
Las unidades de reformador catalítico pueden funcionar a presiones relativamente altas con una serie de reactores de lecho fijo. El catalizador se regenera a intervalos definidos. Las unidades diseñadas para una mayor conversión operan a menor presión con una regeneración del catalizador más frecuente. Se utilizan ciclos más cortos, reactores oscilantes o regeneración continua.
El proceso de formación de plataformas que se muestra en la Figura 1 emplea la regeneración continua del catalizador.
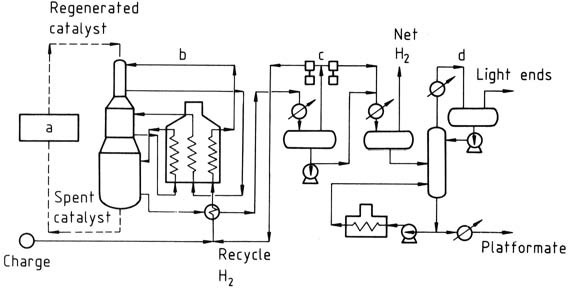
a) Regeneración del catalizador; b) reactores; c) Separación de productos; d) Estabilizador
Otro diseño desarrollado por Standard Oil de Indiana utiliza un reactor oscilante en el que el catalizador de lecho fijo de un reactor se regenera y se vuelve a poner en funcionamiento, mientras que los catalizadores de cada uno de los reactores restantes se regeneran en rotación. En los diferentes procesos se emplean presiones manométricas de 0,7 a 2,4 MPa.
Para la producción de gasolina se utilizan naftas con un intervalo de ebullición de entre 80 y 210 °C. Si el reformado se lleva a cabo para la producción de cargas aromáticas, la composición y el rango de ebullición de la nafta pueden verse alterados.
El reformado puede tener un octanaje claro RON de hasta 100 y puede contener hasta un 70% en volumen de aromáticos.
Con el paso de los años, el proceso se ha hecho más eficaz. Se han modificado los catalizadores de reformado. Se descubrió que pequeñas cantidades de agua mejoraban los rendimientos de benceno con ciertos catalizadores al producir BTX. Se han obtenido mayores rendimientos de xileno al operar a mayores velocidades espaciales.
2.2. Benceno de gasolina de pirólisis
La gasolina de pirólisis, un subproducto de la producción de etileno, es otra buena fuente de BTX. La cantidad de gasolina de pirólisis producida depende de la materia prima y de las condiciones de operación. Es mayor con materias primas más pesadas y puede llegar hasta el 20% para la nafta de rango medio.
La composición de la gasolina de pirólisis varía según el punto de ebullición de la alimentación, y las alimentaciones más pesadas producen más tolueno y xileno que benceno.
La gasolina de pirólisis contiene > 60 % de BTX, pero también contiene compuestos insaturados y diolefinas debido a la alta temperatura necesaria para la producción de etileno. El contenido de diolefina es típicamente del 3 al 5 %, y el contenido total de olefinas cíclicas y diolefinas cíclicas también es del 3 al 5 %.
La gasolina de pirólisis es inestable debido al material diolefínico. Las diolefinas de bajo punto de ebullición se pueden eliminar mediante destilación, pero esto puede resultar difícil debido a su tendencia a polimerizar y despolimerizar. Por lo tanto, generalmente se utiliza un proceso de hidrotratamiento de dos etapas.
La primera etapa convierte diolefinas en olefinas. Si la gasolina se va a utilizar como combustible, es posible que no sea necesario ningún tratamiento adicional. Sin embargo, si la gasolina es una fuente de aromáticos, se utiliza una segunda etapa para saturar las olefinas y eliminar el azufre residual.
3. Otros métodos de producción de benceno
Para satisfacer la demanda, se puede aumentar la producción de benceno a partir de otros compuestos aromáticos, como las fracciones de BTX obtenidas del reformado catalítico, la gasolina de pirólisis o los aceites ligeros de la carbonización del carbón. Esto se puede hacer mediante procesos de hidrodesalquilación, desproporción o combinación.
3.1. Producción de benceno por hidrodesalquilación
La hidrodesalquilación es un proceso de eliminación de grupos alquilo de compuestos aromáticos utilizando hidrógeno. Es una fuente de benceno y el tolueno es la carga habitual. También se pueden utilizar compuestos aromáticos alquilados superiores, pero la reacción transcurre por etapas. Otros alquilbencenos, como el etilbenceno y el propilbenceno, se desalquilan en un solo paso y forman los alcanos correspondientes.
Procesos catalíticos y térmicos
Para la hidrodesalquilación se utilizan procesos tanto catalíticos como térmicos. Los procesos catalíticos, como Detol y Hydeal, funcionan a 575-650 °C y 2,5-6 MPa. Los procesos térmicos, como HDA y THD, operan a temperaturas más altas que los procesos catalíticos, pero los rendimientos y los sistemas de reacción son similares en ambos tipos.
proceso de eliminación
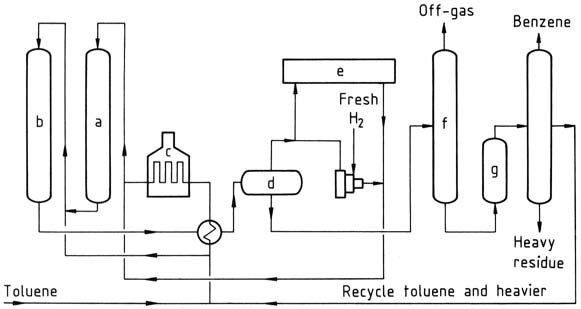
a) Reactor I; b) Reactor II; c) Horno; d) Separador; e) purificación de hidrógeno; f) Estabilizador; g) Tratador de arcilla
El proceso Detol es un proceso de desalquilación catalítica que utiliza un catalizador de desalquilación de lecho fijo. La alimentación se compone de tolueno o mezclas de tolueno y otros bencenos alquilados. Los compuestos aromáticos alquilados y el hidrógeno pasan a temperatura y presión elevadas sobre el catalizador en serie.
Los intercambiadores de calor enfrían los productos del reactor y condensan el benceno, el tolueno sin reaccionar y los bencenos alquilados sin reaccionar, más pesados. Un tambor flash de alta presión separa el hidrógeno reciclado y el gas producto. El gas producto se divide en corrientes para gas combustible, para purificación de hidrógeno si es necesario y para reciclaje de hidrógeno.
El líquido del tambor flash se bombea a un estabilizador, donde el gas restante y los hidrocarburos de bajo punto de ebullición se eliminan y se utilizan como gas combustible. Las colas del estabilizador se tratan con arcilla y se pasan a una columna donde se destila el benceno por cabeza.
El tolueno que no ha reaccionado y los aromáticos más pesados se reciclan. El benceno producido con rendimientos de alrededor del 99% en moles es muy puro, normalmente del 99,95%, con un punto de congelación de 5,45 °C.
proceso hydeal
El proceso Hydeal es otro proceso de desalquilación catalítica. Es similar al proceso Detol, pero en su lugar utiliza un catalizador de cromia-alúmina. El benceno apto para nitración se obtiene con rendimientos de aprox. 98% molar. El material de carga aromática que no ha reaccionado procedente de la operación de un solo paso se recicla para obtener una conversión prácticamente completa. El proceso también se utiliza para hidrodesalquilar alquilnaftalenos.
Procesos HDA y THD
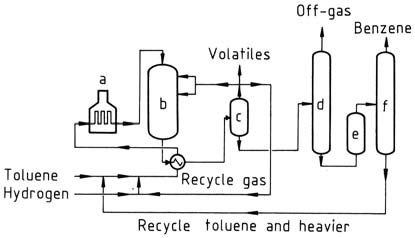
a) Calentador; b) reactor; c) Separador; d) Estabilizador; e) Tratador de arcillas; f) Destilación
Los procesos HDA y THD son procesos de desalquilación térmica. Operan a temperaturas y presiones más altas que los procesos catalíticos. Se alcanzan rendimientos de benceno del 99% en moles.
proceso MHC
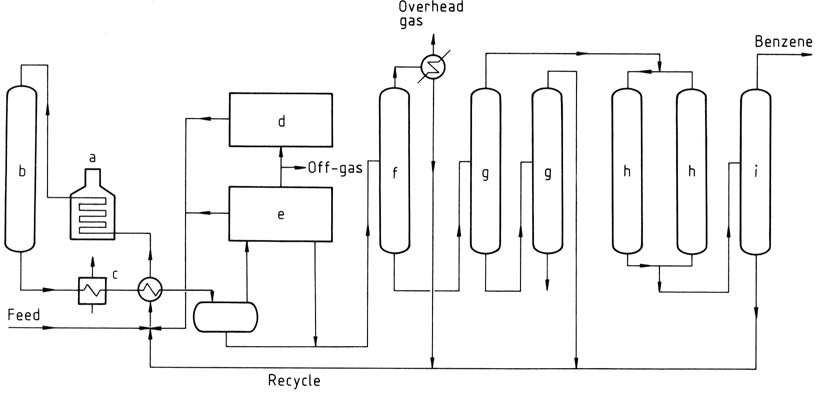
a) Calentador; b) reactor; c) Caldera de calor residual; d) regeneración de hidrógeno; e) Recuperación de aromáticos; f) Fraccionamiento; g) columnas de vacío; h) Tratadores de arcilla; i) columna de benceno
El proceso MHC es un proceso de desalquilación térmica desarrollado por Mitsubishi Petrochemical Co. Puede manejar materias primas que contienen hasta un 30% de compuestos no aromáticos sin recurrir a pasos de extracción aromática y destilación fraccionada. El proceso funcionará con hidrógeno de baja pureza, lo que reducirá la cantidad de hidrógeno de reposición necesaria. Se consigue fácilmente benceno con una pureza del 99,95%.
3.2. Producción de benceno por desproporción
El proceso Tatoray es una forma de producir benceno y xilenos a partir de tolueno y aromáticos C9. Utiliza un catalizador de metal noble o de tierras raras y recicla hidrógeno para que la reacción funcione. El proceso opera a 350-525 °C y 1-5 MPa.
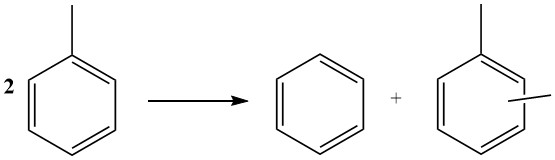
El benceno producido es muy puro y los xilenos contienen muy pocos hidrocarburos saturados. Cuando la materia prima se limita a aromáticos C9 y C10, el proceso produce una mezcla de benceno, tolueno y xilenos.
El proceso Tatoray se utiliza en varias plantas comerciales en todo el mundo. El rendimiento de benceno y xilenos es aproximadamente del 97% cuando se utiliza tolueno como materia prima.
3.3. Producción de benceno mediante procesos combinados de desalquilación
Se han desarrollado varios procesos para producir benceno a partir de materias primas impuras de BTX combinando hidrogenación y desalquilación.
Un ejemplo es el proceso Pyrotol, que implica fraccionar la alimentación para eliminar compuestos ligeros y pesados, vaporizar la fracción C6-C8 y pasarla a través de un reactor catalítico para hidrogenar selectivamente diolefinas, diolefinas cíclicas y estireno.
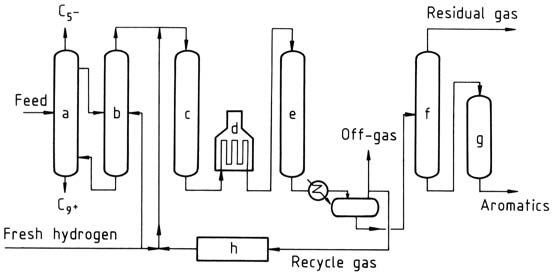
a) Destilación; b) Vaporizador; c) Prerreactor; d) Calentador; e) reactor de pirotol; f) Estabilizador; g) Tratador de arcilla; h) Purificación de hidrógeno
El efluente del reactor de pretratamiento luego se carga a los reactores de Pyrotol, donde los aromáticos se desalquilan a benceno. Otras reacciones incluyen la desulfuración y el hidrocraqueo de productos no aromáticos. El tolueno que no ha reaccionado y los aromáticos más pesados se reciclan. El producto benceno contiene menos de 0,5 ppm de tiofeno y tiene un punto de congelación de al menos 5,47 °C.
Otro ejemplo es el proceso Litol, desarrollado por la División Houdry de Air Products y por Bethlehem Steel. Este proceso produce benceno puro a partir de aceite ligero aromático obtenido de la carbonización del carbón. Utiliza dos etapas de reacción catalítica.
Después del prefraccionamiento del petróleo ligero crudo para eliminar el C5 y las fracciones más ligeras de la parte superior y el C9 y las más pesadas de la parte inferior, se vaporiza la fracción C6-C8. En la primera etapa se hidrogenan diolefinas y estireno.
Luego, el efluente entra en contacto con el catalizador de cromia-alúmina Litol a 500-600 °C, donde se producen la desulfuración, el hidrocraqueo y la desalquilación. Son típicas una pureza de benceno del 99,97% con un punto de congelación de 5,5 °C y un contenido de tiofeno inferior a 0,5 ppm.
Mitsubishi Petrochemical Co. desarrolló un proceso para producir benceno a partir de gasolina de pirólisis. Este proceso implica una hidrogenación en dos etapas seguida de una extracción con solvente para extraer los aromáticos o, alternativamente, una reacción del material hidrogenado en el proceso MHC de Mitsubishi.
Mobil Chemical Co. ha desarrollado un proceso de desproporción en fase líquida para convertir tolueno en benceno y xilenos. Este proceso de desproporción a baja temperatura (LTD) emplea un catalizador a base de zeolita altamente activo que permite que la reacción se desarrolle a temperaturas tan bajas como 260 °C. No se requiere reciclaje de hidrógeno en este proceso en fase líquida.
Referencia
- Benzene; Ullmann’s Encyclopedia of Industrial Chemistry. – https://onlinelibrary.wiley.com/doi/10.1002/14356007.a03_475