
Kohlenstoffdisulfid (CS2) ist eine bedeutende chemische Verbindung, die in verschiedenen industriellen Anwendungen weit verbreitet ist. Seine Entdeckung kann Lampadius im Jahr 1796 zugeschrieben werden, der beim Erhitzen einer Kombination aus Eisenpyrit und Kohlenstoff darauf stieß.
Die Verbindung erregte bereits 1839 industrielles Interesse, als Schrötter sie erfolgreich aus Holzkohle und Schwefel in einer beheizten Retorte synthetisierte. Die bemerkenswerte Lösungsmittelfähigkeit von Schwefelkohlenstoff wurde schnell erkannt, was dazu führte, dass er über einen längeren Zeitraum weit verbreitet bei der Gewinnung von Fetten und Ölen eingesetzt wurde.
Seine wahre Bedeutung als großtechnische Industriechemikalie wurde jedoch erst mit der Einführung des Viskoseverfahrens zu Beginn des 20. Jahrhunderts deutlich. Dieses Verfahren verwendete Schwefelkohlenstoff zum Auflösen von Zellulose und etablierte damit seine zentrale Rolle in der Industrie.
Dennoch erlebte das schnelle Wachstum von Rayon in den späten 1960er Jahren aufgrund der Konkurrenz durch synthetische Fasern auf Erdölbasis Rückschläge, was in den 1970er Jahren zu einem Rückgang sowohl auf dem Rayon- als auch auf dem Schwefelkohlenstoffmarkt führte. Allerdings hat sich die Verwendung von Schwefelkohlenstoff in jüngster Zeit stabilisiert, und für die Zukunft wird ein geringes Marktwachstum prognostiziert.
Im Jahr 1984 wurden von der weltweiten Gesamtproduktion von 1,1 Millionen Tonnen Kohlenstoffdisulfid mehr als 75 % hauptsächlich von der Industrie für regenerierte Zellulose verbraucht. Der verbleibende Teil fand seine Verwendung bei der Herstellung von Tetrachlorkohlenstoff und verschiedenen Organoschwefelverbindungen, die in großem Umfang als Gummichemikalien, Flotationsmittel und Pestizide verwendet werden.
Inhaltsverzeichnis
1. Physikalische Eigenschaften von Kohlenstoffdisulfid
Schwefelkohlenstoff ist eine hochflüchtige Flüssigkeit mit erheblicher Dichte, die in Gegenwart von Luft einen breiten Entflammbarkeitsbereich aufweist, der von 1 bis 50 Volumenprozent reicht. Es verfügt insbesondere über eine außergewöhnlich niedrige Selbstentzündungstemperatur von 100 ° C und einen Flammpunkt von -30 ° C. Seine Verdunstungsgeschwindigkeit in die Atmosphäre übertrifft die von Diethylether um den Faktor 1,6.
Diese Verbindung dient als außergewöhnliches Lösungsmittel für zahlreiche organische Substanzen und löst leicht Schwefel, Phosphor, Jod, Wachse, Gummi und Harze. Die im Handel erhältliche Form verströmt ein stechendes Aroma, das für Verbindungen auf Schwefelbasis charakteristisch ist.
Einige der nützlichsten physikalischen Eigenschaften von Schwefelkohlenstoff sind wie folgt:
- Molmasse = 76,13 g/mol
- Schmelzpunkt = -111,6 ° C
- Siedepunkt = 46,23 ° C
- Dichte bei 25 ° C = 1,26 g/ml
- Kritische Temperatur = 273 ° C
- Kritischer Druck = 7600 kPa
- Oberflächenspannung bei 20 ° C = 32,3 mN/m
- Brechungsindex bei 20 ° C = 1,62546
- Viskosität bei 25 ° C = 0,36 mPa.s
2. Chemische Reaktionen von Kohlenstoffdisulfid
Kohlenstoffdisulfid weist eine Vielzahl chemischer Reaktionen auf, die ausführlich untersucht und dokumentiert wurden.
Wenn Kohlenstoffdisulfid mit Sulfiden, Alkoholen, Ammoniak, Aminen und Chlor reagiert, entstehen industriell bedeutsame Derivate und Zwischenprodukte. In Gegenwart wässriger Alkalien reagiert Schwefelkohlenstoff langsam unter Bildung von Trithiocarbonat- und Carbonatverbindungen, wie durch die Gleichung dargestellt:
3 CS2 + 6 NaOH → 2 Na2CS3 + Na2CO3 + 3 H2O
Metallsulfide bilden bei Reaktion mit Schwefelkohlenstoff Trithiocarbonate, wie in der Reaktion gezeigt:
K2S (wässrig) + CS2 → K2CS3
Darüber hinaus entstehen bei der Reaktion von Schwefelkohlenstoff mit alkoholischen Alkalien Xanthate, bei denen es sich um Salze von Dithiocarbonaten handelt, und zwar durch den folgenden Prozess:
ROH + NaOH → RONa + H2O
RONa + CS2 → ROCSSNa
Diese Reaktion dient als Grundlage für den Viskoseprozess, bei dem Cellulose in Xanthat umgewandelt und anschließend zu Fasern und Filmen regeneriert wird, wie in der Reaktion gezeigt:
(Zellulose) ONa + CS2 → (Zellulose) OCSSNa
2 (Cellulose) OCSSNa + H2SO4 → 2 (Cellulose) OH + 2 CS2 + Na2SO4
In Gegenwart von Ammoniak bildet Schwefelkohlenstoff je nach Ammoniakkonzentration und Temperatur Ammoniumdithiocarbamat (1), Ammoniumtrithiocarbonat (2) und Ammoniumthiocyanat (3):
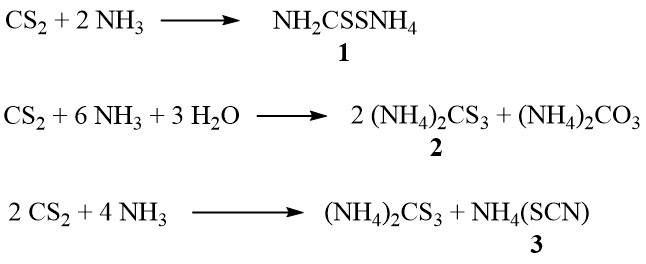
Darüber hinaus zersetzt sich das Thiocyanat bei höheren Temperaturen in der Dampfphase unter Bildung von Thioharnstoff:
NH4 (SCN) → SC (NH2) 2
Primäre und sekundäre Amine ergeben bei ihrer Reaktion mit Schwefelkohlenstoff überwiegend Dithiocarbamatsalze:
2 RNH2 + CS2 → RNHCSSNH3R
2 R2NH + CS2 → R2NCSSNH2R2
In Gegenwart von Alkalien können verschiedene kommerziell wichtige Salze der Dithiocarbaminsäure gewonnen werden:
R2NH + CS2 + NaOH → R2NCSSNa + H2O
Durch die Reaktion von Schwefelkohlenstoff mit Methylamin und Natronlauge in einer wässrigen Lösung entsteht Natriummethyldithiocarbamat (CH3NHCSSNa), ein essentielles Bodenbegasungsmittel. In ähnlicher Weise reagiert Schwefelkohlenstoff mit Ethylendiamin zum Fungizid Natriumethylen-bis (dithiocarbamat):

Anilin– und Schwefelkohlenstoffreaktionen führen zur Bildung zweier bedeutender Vulkanisationsbeschleuniger. In Abwesenheit von Schwefel entsteht Thiocarbanilid, während in Gegenwart von Schwefel 2-Mercaptobenzothiazol (MBT) erhalten wird:
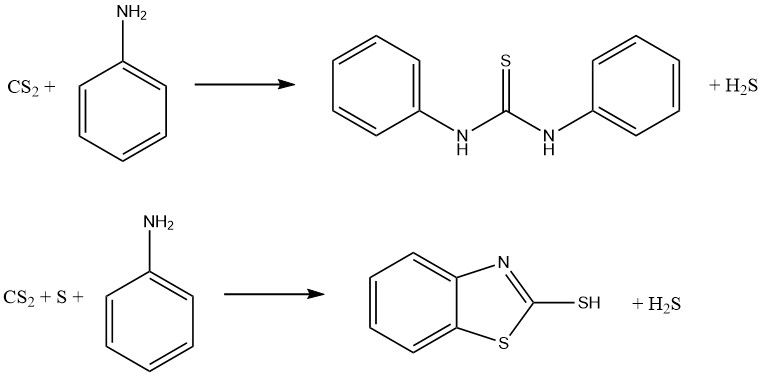
Dithiocarbamate können zu einer Familie von Verbindungen oxidiert werden, die als Thiuriumdisulfide bekannt sind und als Fungizide und Vulkanisationsbeschleuniger verwendet werden. Die Reaktion beinhaltet die folgende Gleichung:
2 R2NCSSNa + H2O2 + H2SO4 → (R2NCSS–) 2 + Na2SO4 + 2 H2O
Bei der Chlorierung von Schwefelkohlenstoff entstehen verschiedene chlorierte Produkte. Unter Jodkatalyse entsteht bei der Chlorierung bei Temperaturen zwischen 5 und 30 ° C Trichlormethansulfenylchlorid sowie je nach Chlorierungsgrad Tetrachlorkohlenstoff, Schwefeldichlorid und Thiophosgen.
In Gegenwart von Eisen und Metallchloriden entstehen bei höheren Temperaturen (70 – 100 ° C) ausschließlich Tetrachlorkohlenstoff und Schwefelchloride.
Schwefelkohlenstoff reagiert in Gegenwart von Aluminiumoxid- und Oxidkatalysatoren oberhalb von 150 ° C leicht mit Wasser und erzeugt dabei Kohlendioxid und Schwefelwasserstoff. Carbonylsulfid fungiert bei dieser Hydrolysereaktion als Zwischenprodukt. Bei Temperaturen zwischen 200 und 300 ° C erreicht die Umwandlung von Schwefelkohlenstoff in diese Produkte ein Gleichgewicht.
Bei hohen Temperaturen (über 150- 200 ° C) in Gegenwart von Metallsulfidkatalysatoren wie Molybdän- und Nickelsulfiden wird Schwefelkohlenstoff durch Wasserstoff reduziert, was zu unterschiedlichen Mengen an Methanthiol, Dimethylsulfid, Methan und Schwefelwasserstoff führt.
3. Herstellung von Kohlenstoffdisulfid
Der Schwefelkohlenstoff wird durch die Reaktion von Schwefel mit Holzkohle oder Methan gebildet. Obwohl Ethan, Propan und Propen in begrenztem Umfang verwendet wurden, hat das Methanverfahren seit seiner Einführung in den frühen 1950er Jahren erheblich an Bedeutung gewonnen.
Folglich ist das ältere Holzkohleverfahren bei der Herstellung von Schwefelkohlenstoff in den Vereinigten Staaten, Europa und Japan nicht mehr relevant. In Regionen, in denen Erdgas oder Methan nicht leicht zugänglich sind oder in denen die Anlagengröße relativ klein ist, wird jedoch immer noch das Holzkohleverfahren eingesetzt, um den lokalen Bedarf für die Viskoseproduktion zu decken.
3.1. Herstellung von Kohlenstoffdisulfid aus Kohle und Schwefel
Der grundlegende Prozess der Reaktion von Holzkohle mit Schwefel hat seit seiner Einführung Mitte der 1840er Jahre nur minimale Veränderungen erfahren. Nach wie vor werden extern beheizte Retorten verwendet, obwohl sich das Gerätedesign durch die Verfügbarkeit hochwertiger Baumaterialien deutlich verbessert hat.
In Retortenanlagen wird geschmolzener Schwefel entweder vor oder nach dem Einbringen in die Retorte verdampft und überhitzt. In der Retorte reagiert der überhitzte Schwefeldampf bei Temperaturen zwischen 850 und 900 ° C und leicht über dem Atmosphärendruck mit einem stationären Holzkohlebett.
Das resultierende Produktgas, das Schwefelkohlenstoff, Schwefel, Schwefelwasserstoff, Carbonylsulfid und Inertgase enthält, durchläuft eine Reihe von Kondensatoren, Wäschern und Ölabsorbern, um rohen Schwefelkohlenstoff zurückzugewinnen.
Die weitere Behandlung in Destillationskolonnen liefert das reine Produkt. Das Abgas, das hauptsächlich aus Schwefelwasserstoff, Carbonylsulfid und Inertgasen besteht, kann entweder verbrannt und mit einer Ätzlösung gewaschen oder einer Schwefelrückgewinnungsanlage zugeführt werden.
Normalerweise ist jede Retorte in der Lage, 1 bis 3 Tonnen Schwefelkohlenstoff pro Tag zu produzieren. Die Nutzungsdauer von Retorten aus Gusseisen ist aufgrund von Hochtemperaturkorrosion auf weniger als ein Jahr begrenzt.
Um den Bedarf an Reaktorreinigungen zu minimieren, sollten die in den Retorten verwendeten Rohstoffe einen geringen Asche- und Rückstandsgehalt aufweisen. Eine Verschmutzung der Retorten beeinträchtigt die Wärmeübertragung und verringert deren Lebensdauer.
Die Qualität der Holzkohle ist entscheidend, da weniger reaktive Materialien für einen zufriedenstellenden Betrieb höhere Temperaturen erfordern. Aus diesem Grund wird Holzkohle aus Hartholz bevorzugt.
Die Holzkohle wird typischerweise bei 500 ° C vorkalziniert, um flüchtige Substanzen zu entfernen, die zur Bildung unerwünschter Nebenprodukte führen könnten. Der thermische Wirkungsgrad von Retorten beträgt etwa 25 %, wobei die Kohlenstoff- und Schwefelausbeute im Allgemeinen unter 90 % liegt.
Eine alternative Wärmequelle für die Reaktion von Holzkohle mit Schwefel ist die elektrische Widerstandsheizung in gemauerten elektrothermischen Reaktoren. Wenn kostengünstiger Strom zur Verfügung steht, kann die elektrische Methode kostengünstiger sein.
Der Stromverbrauch pro produzierter Tonne Schwefelkohlenstoff beträgt rund 1200 kWh. Elektrothermische Reaktoren bieten mehrere Vorteile, darunter eine größere Kapazität pro Reaktor (bis zu 10 Tonnen pro Tag) und eine längere Reaktorlebensdauer. Darüber hinaus kann ein breiteres Spektrum an festem Kohlenstoff eingesetzt werden, da elektrothermische Reaktoren höhere Temperaturen erzeugen können.
3.2. Herstellung von Kohlenstoffdisulfid aus Methan und Schwefel
Aufgrund der wachsenden Nachfrage nach Schwefelkohlenstoff in den 1940er Jahren führten die Einschränkungen der Holzkohleprozesse zur Entwicklung einer effizienteren großtechnischen Herstellungsmethode.
Als erfolgreiche Alternative erwies sich die katalysierte Reaktion zwischen Methan und Schwefel unter Nutzung von leicht verfügbarem und kostengünstigem Erdgas. Zwischen 1943 und 1965 wurden zahlreiche Patente erteilt, die verschiedene Aspekte dieses Verfahrens abdeckten.
Das kommerzielle Methanverfahren, das hauptsächlich auf den von Pure Oil Co. erworbenen Patenten basierte, wurde später von Food Machinery Corp. (FMC) und Stauffer Chemical Co. übernommen.
1953 baute FMC die erste Methanverarbeitungsanlage in South Charleston, West Virginia, drei Jahre später folgte eine Stauffer-Anlage in LeMoyne, Alabama. Mitte der 1960er Jahre erfolgte die gesamte Schwefelkohlenstoffproduktion in den Vereinigten Staaten mit dieser Methode, und bald entstanden ähnliche Anlagen in Europa und anderen Regionen.
Derzeit basieren über 85 % der weltweiten Produktionskapazität für Schwefelkohlenstoff auf dem Methanprozess.
Ein typisches Flussdiagramm eines Methanprozesses ist in Abbildung 1 dargestellt. Gereinigtes Erdgas, das über 95 % Methan und geringe Konzentrationen an Propan und schwereren Kohlenwasserstoffen enthält, wird im Konvektionsbereich des Reaktionsofens auf etwa 250 ° C vorgewärmt.
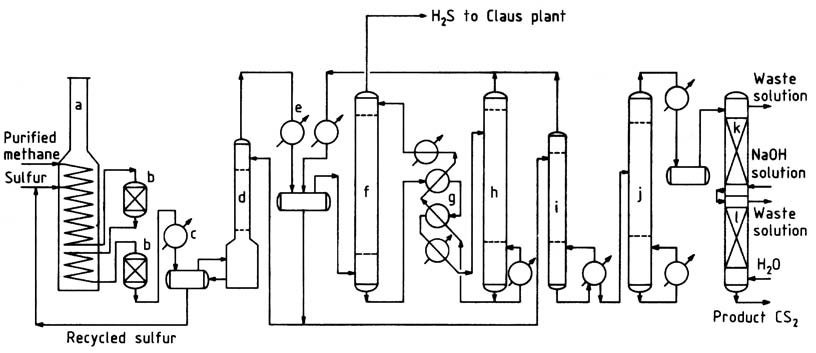
a) Reaktionsofen; B) Katalytische Reaktoren; C) Schwefelkondensator; D) CS2-Wäscher; E) CS2-Kondensator; F) CS2-Absorber; G) Ölaustauscher; H) CS2-Stripper; I) Stabilisatorsäule; J) Reinigungskolonne; K) Laugenwaschkolonne; L) Wasserwaschkolonne
Der Ofen, ein kastenförmiger Pyrolyseofen, der üblicherweise in der petrochemischen Industrie eingesetzt wird, besteht aus Strahlungs- und Konvektionsabschnitten. Das heiße Methangas wird mit flüssigem Schwefel vermischt und in die horizontale Heizschlange im Strahlungsabschnitt eingeleitet.
In diesem Abschnitt verdampft der flüssige Schwefel und die Temperatur der Mischung steigt auf 550–650 ° C. Der Betriebsdruck liegt typischerweise zwischen 400 und 700 kPa.
Alternativ können Methan und Schwefel separat und an verschiedenen Stellen innerhalb der Spule eingeführt werden. Um eine effiziente Methanumwandlung zu gewährleisten und die Kohlenstoff- und Teerbildung zu minimieren, wird ein leichter Überschuss an Schwefel (ca. 5 %) eingesetzt.
Um der korrosiven Hochtemperaturumgebung standzuhalten, wird als Rohrmaterial hochlegierter Edelstahlguss verwendet, der eine Rohrlebensdauer von ca. 2-3 Jahren gewährleistet. Gepackte, mit Ziegeln ausgekleidete Reaktoren sind mit der Heizschlange verbunden, um zusätzliche Verweilzeit und Unterbringung für Katalysatorbetten zu bieten.
Die Reaktion findet sowohl in den Rohren als auch in den Reaktoren statt und gewährleistet eine nahezu vollständige Umwandlung der Kohlenwasserstoffe, bevor das Gas den letzten Reaktor verlässt. Das das Reaktionsofensystem verlassende Gas durchläuft einen Schwefelkondensator, in dem der größte Teil des überschüssigen Schwefels abgetrennt wird.
Anschließend gelangt das abgekühlte Gas zu einem Schwefelwäscher und dann zum CS2-Wäscher, wo der restliche Schwefel entfernt wird. Das relativ schwefelfreie Gas gelangt in wassergekühlte Kondensatoren zur Massenabtrennung von Schwefelkohlenstoff.
Der verbleibende Schwefelkohlenstoff wird im Ölabsorber aus dem Schwefelwasserstoffgas extrahiert. Das den Ölabsorber verlassende Schwefelwasserstoffgas enthält etwa 1–2 % Methan und weniger als 1000 ppm Schwefelkohlenstoff.
Dieses Gas wird zu einer Claus-Schwefelrückgewinnungsanlage geleitet, wo es wieder in Schwefel umgewandelt wird.
Roher Schwefelkohlenstoff, einschließlich des im Stripper gewonnenen, wird zur Stabilisatorkolonne geleitet, um niedrigsiedende Verunreinigungen zu entfernen.
Das Sumpfprodukt der Stabilisatorkolonne wird dann in der Reinigungskolonne verarbeitet, um hochsiedende Verunreinigungen aus dem Produkt abzutrennen. Die Produktreinigung wird durch Laugen- und Wasserwäschen abgeschlossen. Anschließend wird das fertige Produkt in Kontrolltanks und Lager gepumpt.
4. Verwendung von Kohlenstoffdisulfid
Der Hauptverbraucher von Schwefelkohlenstoff ist die Industrie für regenerierte Zellulose, auf die über 65 % der Weltproduktion entfallen. Insbesondere wird bei der Herstellung von Viskose ein erheblicher Teil Schwefelkohlenstoff verbraucht, wobei für jedes produzierte Kilogramm Viskose etwa 0,32 kg Schwefelkohlenstoff verbraucht werden.
Etwa 10 % des Schwefelkohlenstoffs werden bei der Zellophanherstellung verwendet, weitere 10 % werden zur Herstellung von Tetrachlorkohlenstoff chloriert. Auf diese Methode entfallen etwa 25 % der weltweiten Tetrachlorkohlenstoffproduktion.
Die restlichen 15 % des Schwefelkohlenstoffs verteilen sich auf verschiedene Anwendungen, darunter Gummichemikalien, Flotationsmittel, Pestizide, verschiedene chemische Reagenzien, Extraktionslösungsmittel, Katalysator-Vorsulfidierungsmittel und Ölquellenlösungsmittel.
Allerdings steht die Industrie für regenerierte Zellulose aufgrund der Konkurrenz durch synthetische Fasern und Folien vor Herausforderungen, was ihr Marktwachstum einschränkt. Um den Fortschritt voranzutreiben, ist eine schrittweise Verbesserung des Schwefelkohlenstoffverbrauchs erforderlich, insbesondere durch eine verstärkte Nutzung bei der Herstellung von Agrar- und Spezialchemikalien.
Referenz
- Carbon Disulfide; Ullmann’s Encyclopedia of Industrial Chemistry. – https://onlinelibrary.wiley.com/doi/10.1002/14356007.a05_185