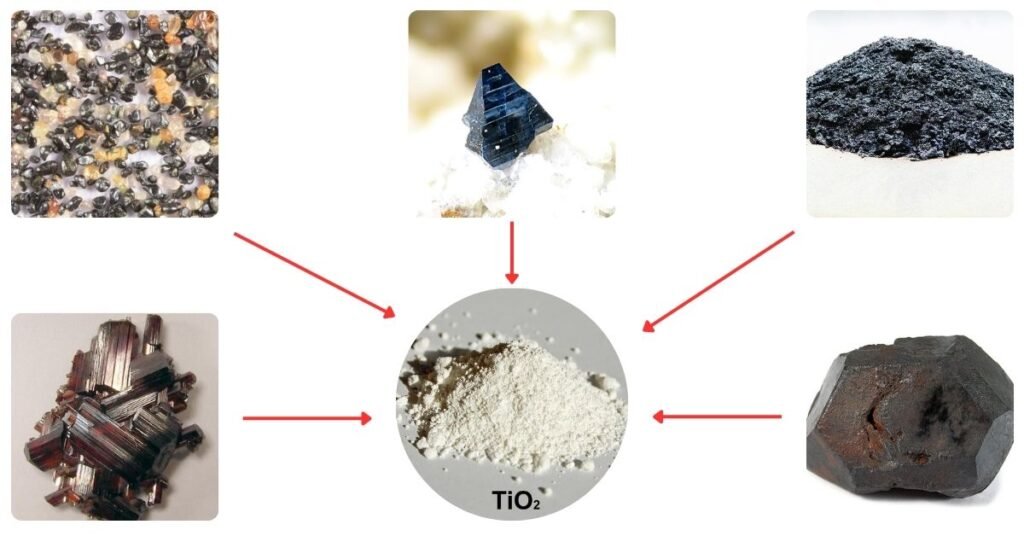
Zu den Rohstoffen für die Titandioxidproduktion gehören Naturstoffe wie Ilmenit, Leukoxen und Rutil sowie einige sehr wichtige synthetische Materialien wie Titanschlacke und synthetischer Rutil.
Im Jahr 2007 überstieg die Gesamtproduktion titanoferroischer Rohstoffe 6 Millionen Tonnen. Australien ist der größte Produzent, gefolgt von Südafrika, Kanada und China.
Tabelle 1 zeigt Produktionsdaten wichtiger titanhaltiger Rohstoffe.
Rohstoff | Standort | Minenproduktion, 103 t/a |
---|---|---|
Ilmenit | Australien | 1400 |
Kanada | 816 | |
Ukraine | 290 | |
Indien | 378 | |
Norwegen | 377 | |
Südafrika | 1100 | |
USA | 300 | |
China | 550 | |
Vietnam | 254 | |
Brasilien | 127 | |
Andere | 129 | |
Gesamt | 5720 | |
Rutil (natürlich und synthetisch) | Australien | 340 |
Ukraine | 70 | |
Südafrika | 120 | |
Sierra Leone | 80 | |
Indien | 20 | |
Sonstige | 30 | |
Gesamt | 660 | |
Titanschlacke | Kanada | 920 |
Norwegen | 160 | |
Südafrika | 1300 | |
Gesamt | ~2400 |
1. Natürliche Rohstoffe
Titan ist das neunthäufigste Element in der Erdkruste. Es bildet regelmäßig Verbindungen mit Sauerstoff. Unter den natürlichen Titanmineralien sind nur Ilmenit (einschließlich Leukoxen) und Rutil wirtschaftlich bedeutsam. Leukoxen entsteht durch natürliche Verwitterung und Zersetzung von Ilmenit.
Über 90 % der weltweiten Ilmenit- und Rutilproduktion werden für die Pigmentproduktion verwendet. Der verbleibende Anteil wird in der Titanmetallherstellung und für Schweißdrahtbeschichtungen verwendet.
Tabelle 2 listet die wichtigsten titanhaltigen Minerale auf.
Mineral | Formel | TiO2-Gehalt, Gew.-% |
---|---|---|
Rutil | TiO2 | 92–98 |
Anatas | TiO2 | 90–95 |
Brookit | TiO2 | 90–100 |
Ilmenit | FeTiO3 | 35–60 |
Leukoxen | Fe2O3TiO2 | 60–90 |
Perowskit | CaTiO3 | 40–60 |
Sphen (Titanit) | CaTiSiO5 | 30–42 |
Titanomagnetit | Fe(Ti)Fe2O4 | 2–20 |
1.1. Ilmenit und Leukoxen
Ilmenit kommt weltweit in primären Massiv- und sekundären alluvialen (Sand-)Lagerstätten mit Schwermineralien vor. Massiv-Erze gehen häufig mit intermediären Intrusionen einher, wie sie beispielsweise in Tellnes (Norwegen) und Lake Allard (Kanada) vorkommen.
Konzentrate aus diesen Massiv-Erzen weisen häufig einen erhöhten Eisengehalt auf, der als segregierter Hämatit oder Magnetit im Ilmenit vorliegt. Diese Eisenverbindungen verringern den Titandioxidgehalt der Konzentrate. Die direkte Nutzung dieser eisenreichen Ilmenite ist zurückgegangen.
Die Anreicherung von Ilmenit in Strandsanden, sowohl an aktuellen als auch an fossilen Küsten, ist wichtig für die Titandioxidproduktion. Wellenbewegungen, Strömungen oder Wind konzentrieren Ilmenit und andere Schwermineralien, darunter Rutil, Zirkon, Monazit und andere Silikate, in Dünen oder Stränden. Dieser Konzentrationsprozess führt häufig zur Mineralschichtung.
Meerwasser und atmosphärische Einflüsse über geologische Zeiträume führen zur Korrosion von Ilmenit. Eisen wird aus dem Ilmenitkristallgitter entfernt, wodurch das verbleibende Material mit Titandioxid angereichert wird. Das Gitter bleibt bei TiO2-Gehalten von bis zu ca. 65 % stabil. Weitere Eisenentfernung führt zu einem submikroskopischen Mineralgemisch, das hauptsächlich aus Anatas, Rutil und amorphen Phasen besteht.
Gemische mit Titandioxidgehalten von bis zu 90 % werden als Leukoxen bezeichnet. Leukoxen kommt in korrodiertem Ilmenit und einigen Lagerstätten vor; es wird separat gewonnen und verarbeitet. Die Leukoxenproduktionsmengen sind jedoch im Vergleich zu Ilmenit gering.
Ilmenitsandkonzentrate sind eisenarm und weisen im Allgemeinen einen höheren Titandioxidgehalt auf als solche aus massiven Lagerstätten. Weitere in diesen Konzentraten enthaltene Elemente sind Magnesium, Mangan und Vanadium (inhärent in Ilmenit) sowie Aluminium, Calcium, Chrom und Silizium (aus Mineralintrusionen).
Die wirtschaftlich nutzbaren Ilmenitreserven betragen rund 680 Millionen Tonnen, davon 30 % in China, 20 % in Australien, 13 % in Indien und 9 % in Südafrika. Basierend auf den aktuellen Produktionskapazitäten kann der weltweite Bedarf über ein Jahrhundert lang gedeckt werden.
Komponente | Tellnes (Norwegen) | Richard’s Bay (Südafrika) | Capel (Westaustralien) | Quilon (Indien) |
---|---|---|---|---|
TiO2 | 43.8 | 46.5 | 54.8 | 60.3 |
Fe2O3 | 14.0 | 11.4 | 16.0 | 24.8 |
FeO | 34.4 | 34.2 | 23.8 | 9.7 |
Al2O3 | 0.6 | 1.3 | 1.0 | 1.0 |
SiO2 | 2.2 | 1.6 | 0.8 | 1.4 |
MnO | 0.3 | - | 1.5 | 0.4 |
Cr2O3 | - | 0.1 | 0.1 | 0.1 |
V2O5 | 0.3 | 0.3 | 0.2 | 0.2 |
MgO | 3.7 | 0.9 | 0.15 | 0.9 |
1.2. Rutil
Rutil entsteht hauptsächlich durch Magmakristallisation, insbesondere aus titanreichen und eisenarmen Schmelzen. Er entsteht durch die Metamorphose titanhaltiger Sedimente oder Magmatite.
Die Rutilkonzentrationen in Primärgesteinen sind für eine kommerzielle Nutzung zu gering. Daher gelten nur Sande, die neben Zirkon, Ilmenit und anderen Schwermineralien auch Rutil enthalten, als gewinnbringende Reserven. Die weltweiten Rutilreserven werden auf 45 Millionen Tonnen geschätzt.
Zu den wichtigsten Produzenten von natürlichem Rutil zählen Australien, Südafrika und Sierra Leone. Im Jahr 2007 erreichte die weltweite Rutilminenproduktion rund 564.000 Tonnen. Das Angebot an natürlichem Rutil reicht nicht aus, um die Nachfrage zu decken; daher wird es weitgehend durch synthetischen Rutil ersetzt.
Tabelle 4 zeigt die Zusammensetzung ausgewählter Rutilkonzentrate.
Rutilkomponente | Ostaustralien | Sierra Leone | Südafrika |
---|---|---|---|
TiO2 | 96.00 | 95.70 | 95.40 |
Fe2O3 | 0.70 | 0.90 | 0.70 |
Cr2O3 | 0.27 | 0.23 | 0.10 |
MnO | 0.02 | - | - |
Nb2O5 | 0.45 | 0.21 | 0.32 |
V2O5 | 0.50 | 1.00 | 0.65 |
ZrO2 | 0.50 | 0.67 | 0.46 |
Al2O3 | 0.15 | 0.20 | 0.65 |
CaO | 0.02 | - | 0.05 |
P2O5 | 0.02 | 0.04 | 0.02 |
SiO2 | 1.00 | 0.70 | 1.75 |
1.3. Anatas
Anatas, ein Titandioxid-Polymorph, kommt hauptsächlich in bedeutenden Reserven in brasilianischen Karbonintrusionen vor. Erzaufbereitungsverfahren ermöglichen die Herstellung von Konzentraten mit 80 % TiO2. Durch anschließende Salzsäurebehandlung können diese Konzentrate weiter auf 90 % TiO2 angereichert werden.
Der geschätzte Titandioxidgehalt in diesen Mineralvorkommen erreicht 108 Tonnen.
1.4. Erzaufbereitung
Die weltweite Titanerzproduktion beginnt hauptsächlich mit Schwermineralsanden. Abbildung 1 veranschaulicht den Produktionsprozess.
Ilmenit kommt häufig zusammen mit Rutil und Zirkon vor; daher ist die Ilmenitgewinnung an diese Minerale gebunden. Sofern die geologischen und hydrologischen Bedingungen es zulassen, wird Rohsand, der typischerweise 3–10 % Schwermineralien enthält, durch Nassbaggerung gewonnen (a).
Nach einer Siebprobe (b) wird der Rohsand einer mehrstufigen Schwerkraftkonzentration mittels Reichert-Kegeln (d) oder -Spiralen (e) unterzogen, um ein Produkt mit 90–98 % Schwermineralien zu erhalten. Diese Anlage trennt Schwermineralien (Dichte: 4,2–4,8 g/cm³) von Leichtmineralien (Dichte: <3 g/cm³).
Magnetische Minerale, insbesondere Ilmenit, werden anschließend durch Trocken- oder Nassmagnetscheidung von nichtmagnetischen Bestandteilen (Rutil, Zirkon, Silikate) getrennt (f). Erze aus unverwitterten Lagerstätten werden zunächst einer Magnetitentfernung unterzogen.
Eine elektrostatische Trennstufe (h) erleichtert die Entfernung schädlicher nichtleitender Mineralverunreinigungen wie Granit, Silikate und Phosphate aus Ilmenit.
Die nichtmagnetische Fraktion (Leukoxen, Rutil, Zirkon) wird anschließend einer weiteren hydromechanischen Aufbereitung (i) mittels Schütteltischen oder Spiralen unterzogen, um verbleibende Minerale mit geringer Dichte, hauptsächlich Quarz, zu entfernen.
Schwach magnetische, verwitterte Ilmenite und Leukoxene werden in einer abschließenden Trockenstufe durch eine hochintensive Magnettrennung (j) gewonnen. Leitfähiger Rutil wird anschließend in mehreren Stufen elektrostatisch von nichtleitendem Zirkon getrennt (l). Ein Luftstoß entfernt Quarzreste.
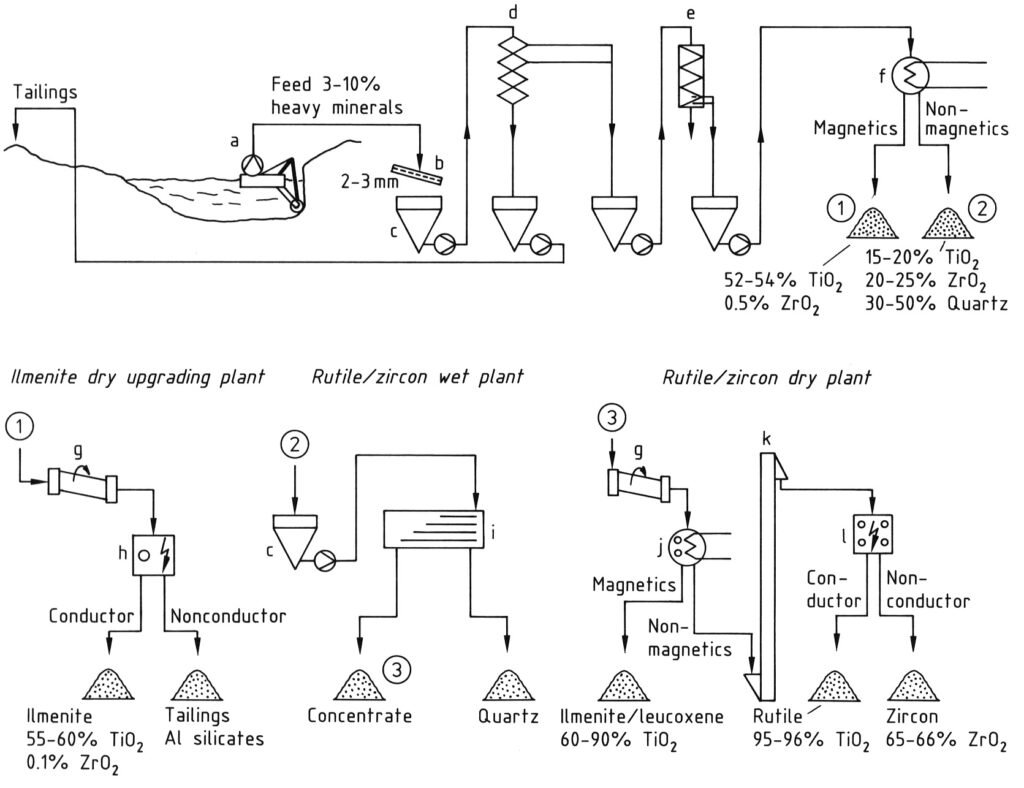
a) Bagger; b) Sieb; c) Bunker; d) Reichert-Kegel; e) Spiralen; f) Magnetabscheider; g) Trockner; h) Elektrostatischer Abscheider; i) Schütteltisch; j) Trockenmagnetabscheider; k) Vertikales Förderband; l) Elektrostatischer Abscheider
2. Synthetische Rohstoffe
Die steigende Nachfrage nach Rohstoffen mit hohem Titandioxidgehalt hat die Entwicklung synthetischer Ausgangsstoffe vorangetrieben. Bei allen Produktionsverfahren wird Eisen aus Ilmeniten oder Titanomagnetiten entfernt.
2.1. Titanschlacke
Das metallurgische Verfahren zur Eisenentfernung aus Ilmenit basiert auf der Schlackenbildung, bei der Eisen mit Anthrazit oder Koks bei 1200–1600 °C in einem Lichtbogenofen zu Metall reduziert wird. Dadurch entsteht titanfreies Roheisen und eine Schlacke mit 75–85 % Titandioxid, je nach verwendetem Erz.
Diese Schlacke eignet sich aufgrund ihres hohen Ti3+-Gehalts und niedrigen Kohlenstoffgehalts für die Chlorierung oder den Schwefelsäureaufschluss. Die Eignung der Schlacke für das Chlorid- oder Sulfatverfahren hängt vom Titangehalt, den Verunreinigungsgraden und der Partikelgröße ab.
Insbesondere Calcium und Magnesium wirken sich nachteilig auf den Chloridprozess aus. Titanschlacke wird von QIT Fer et Titane Inc. in Kanada, Richard’s Bay Minerals in Südafrika und Tinfos AS in Tyssedal, Norwegen, produziert.
Die Gesamtschlackenproduktion im Jahr 2007 überstieg 2 Millionen Tonnen, wobei der Großteil für den Chloridprozess bestimmt war. Ein Teil dieser Schlacke wird weiterverarbeitet, um veredelte Schlacke mit über 95 % TiO2 für den Chloridprozess zu erzeugen.
2.2. Synthetisches Rutil
Natürliche Rutilvorkommen sind selten und der Abbau kostspielig. Daher wurden verschiedene Verfahren zur Eisenentfernung aus Ilmenitkonzentraten entwickelt. Diese Methoden erhalten die Korngröße des Minerals, die für die anschließende Wirbelschichtchlorierung optimal ist.
Industrielle Prozesse beinhalten die Fe3+-Reduktion mit Kohlenstoff oder Wasserstoff, manchmal nach einer vorläufigen Ilmenitoxidation. Die Bildung von Fe2+ in einem aktivierten Ilmenitgitter oder von metallischem Eisen hängt von den Reduktionsbedingungen ab.
Aktivierter Ilmenit mit Fe2+ wird mit Salzsäure oder verdünnter Schwefelsäure behandelt, idealerweise unter Druck. Dadurch entsteht synthetischer Rutil mit einem Titandioxidgehalt von 85–96 %. Die entstehenden Eisen(II)-Salzlösungen werden konzentriert und anschließend thermisch zu Eisenoxid und Salzsäure zersetzt. Die Salzsäure kann für den Aufschluss recycelt werden.
Metallisches Eisen kann durch verschiedene Methoden abgetrennt werden. In der Patentliteratur werden folgende Verfahren beschrieben:
- Zerkleinerung mit anschließender physikalischer Trennung (z. B. Magnetscheidung, Flotation).
- Auflösung in Eisen(III)-chloridlösungen. Das entstehende Eisen(II)-Salz wird an der Luft oxidiert, wobei Eisenoxidhydroxide und Eisen(III)-Salze entstehen.
- Säureauflösung.
- Luftoxidation in Gegenwart eines Elektrolyten. Je nach verwendetem Elektrolyt bilden sich verschiedene Eisenoxid- oder Eisenoxidhydroxidphasen. Beispiele für Elektrolyte sind Eisen(II)-chloridlösungen, Ammoniumchlorid oder Ammoniumcarbonat-Kohlensäure.
- Oxidation mit Eisen(III)-sulfat aus dem Ilmenitaufschluss, gefolgt von der Eisen(II)-sulfatkristallisation.
- Chlorierung zur Herstellung von Eisen(III)-chlorid.
- Reaktion mit Kohlenmonoxid zu Eisencarbonylen, die sich zersetzen und hochreines Eisen ergeben.
Die partielle Chlorierung von Eisen in Kohlenstoff ist eine weitere Methode zur Erhöhung des Titandioxidgehalts in Ilmenit. Im Jahr 2008 produzierten 17 Unternehmen Rutil (natürlich oder synthetisch). Zu den führenden Produzenten zählten Iluka (25 %), Richard’s Bay Minerals (RBM) (13 %), Sierra Leone Ltd. (12 %) und Consolidated Rutile Ltd. (CRL) (11 %).
Etwa 60 % des weltweiten Rutilverbrauchs werden für die Herstellung von Titandioxidpigmenten verwendet. Die weltweite Rutilproduktion betrug 2008 663.000 Tonnen.
Referenz
Pigments, Inorganic, 2. White Pigments. – https://onlinelibrary.wiley.com/doi/10.1002/14356007.n20_n01.pub2