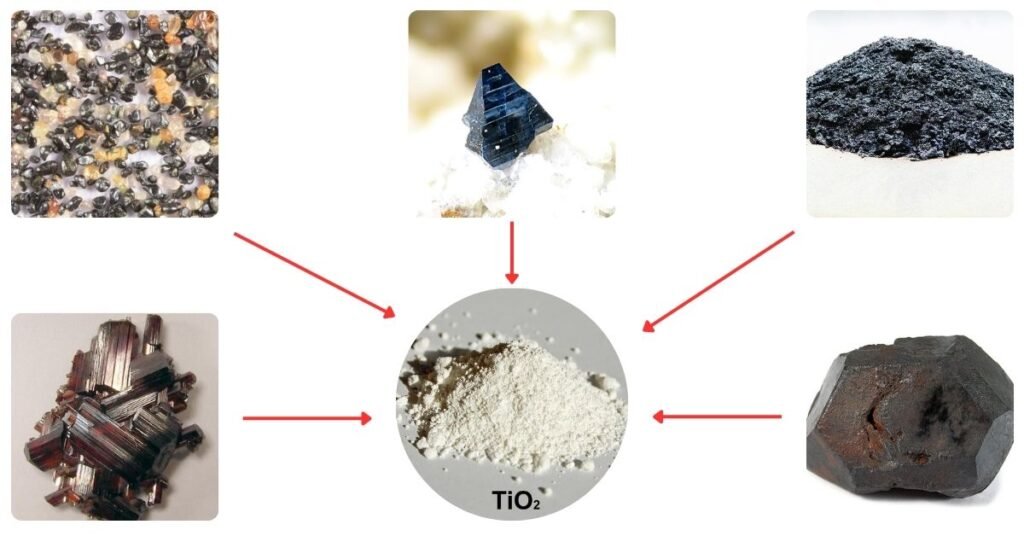
The raw materials for titanium dioxide production include natural products such as ilmenite, leucoxene, and rutile, and some very important synthetic materials such as titanium slag and synthetic rutile.
In 2007, total titanoferrous raw material production exceeded 6 million metric tons. Australia is the largest producer, followed by South Africa, Canada, and China.
Table 1 presents production data for important titanium-containing raw materials.
Raw Material | Location | Mine Production, 103 t/a |
---|---|---|
Ilmenite | Australia | 1400 |
Canada | 816 | |
Ukraine | 290 | |
India | 378 | |
Norway | 377 | |
South Africa | 1100 | |
United States | 300 | |
China | 550 | |
Vietnam | 254 | |
Brasil | 127 | |
Others | 129 | |
Total | 5720 | |
Rutile (natural and synthetic) | Australia | 340 |
Ukraine | 70 | |
South Africa | 120 | |
Sierra Leone | 80 | |
India | 20 | |
Others | 30 | |
Total | 660 | |
Titanium slag | Canada | 920 |
Norway | 160 | |
South Africa | 1300 | |
Total | ~2400 |
1. Natural raw materials
Titanium is the ninth most abundant element within the Earth’s crust. It consistently forms compounds with oxygen. Among natural titanium minerals, only ilmenite (including leucoxene) and rutile possess economic significance. Leucoxene is formed by the natural weathering and decomposition of ilmenite.
Over 90% of global ilmenite and rutile output is dedicated to pigment production. The remaining portion is utilized in titanium metal manufacturing and for welding-rod coatings.
Table 2 lists the most significant titanium-containing minerals.
Mineral | Formula | TiO2 content, wt% |
---|---|---|
Rutile | TiO2 | 92–98 |
Anatase | TiO2 | 90–95 |
Brookite | TiO2 | 90–100 |
Ilmenite | FeTiO3 | 35–60 |
Leucoxene | Fe2O3TiO2 | 60–90 |
Perovskite | CaTiO3 | 40–60 |
Sphene (titanite) | CaTiSiO5 | 30–42 |
Titanomagnetite | Fe(Ti)Fe2O4 | 2–20 |
1.1. Ilmenite and Leucoxene
Ilmenite occurs globally in primary massive ore deposits and secondary alluvial (sand) deposits containing heavy minerals. Massive ores frequently associate ilmenite with intermediary intrusions, such as those found in Tellnes, Norway, and Lake Allard, Canada.
Concentrates derived from these massive ores often have elevated iron content, present as segregated hematite or magnetite within the ilmenite. These iron compounds decrease the titanium dioxide content of the concentrates. Direct use of these high-iron ilmenites has declined.
The enrichment of ilmenite in beach sands, both current and fossil coastlines, is important for titanium dioxide production. Wave action, currents, or wind concentrate ilmenite and other heavy minerals, including rutile, zircon, monazite, and other silicates, within dunes or beaches. This concentration process often results in mineral layering.
Seawater and atmospheric exposure over geological timescales induce ilmenite corrosion. Iron is removed from the ilmenite crystal lattice, enriching the remaining material with titanium dioxide. The lattice remains stable with TiO2 contents up to approximately 65%. Further iron removal leads to a submicroscopic mineral mixture, mainly comprising anatase, rutile, and amorphous phases.
Mixtures with titanium dioxide contents as high as 90% are termed leucoxene. Leucoxene is present in corroded ilmenite and some deposits; it is recovered and processed separately. However, leucoxene production volumes are minor compared to ilmenite.
Ilmenite sand concentrates, being iron-depleted, generally possess higher titanium dioxide content than those from massive deposits. Other elements present in these concentrates include magnesium, manganese, and vanadium (inherent to ilmenite) and aluminum, calcium, chromium, and silicon (originating from mineral intrusions).
Economically viable ilmenite reserves are approximately 680 million metric tons, with 30% in China, 20% in Australia, 13% in India, and 9% in South Africa. Based on current production capacities, global demand can be met for over a century.
Component | Tellnes (Norway) | Richard’s Bay (South Africa) | Capel (Western Australia) | Quilon (India) |
---|---|---|---|---|
TiO2 | 43.8 | 46.5 | 54.8 | 60.3 |
Fe2O3 | 14.0 | 11.4 | 16.0 | 24.8 |
FeO | 34.4 | 34.2 | 23.8 | 9.7 |
Al2O3 | 0.6 | 1.3 | 1.0 | 1.0 |
SiO2 | 2.2 | 1.6 | 0.8 | 1.4 |
MnO | 0.3 | - | 1.5 | 0.4 |
Cr2O3 | - | 0.1 | 0.1 | 0.1 |
V2O5 | 0.3 | 0.3 | 0.2 | 0.2 |
MgO | 3.7 | 0.9 | 0.15 | 0.9 |
1.2. Rutile
Rutile is primarily formed by magma crystallization, specifically from melts rich in titanium and low in iron. It originates from the metamorphosis of titanium-bearing sediments or magmatites.
Rutile concentrations in primary rocks are too low for commercial exploitation. Consequently, only sands containing rutile alongside zircon, ilmenite, and other heavy minerals are considered viable reserves. Global rutile reserves are estimated at 45 million metric tons.
Major producers of natural rutile include Australia, South Africa, and Sierra Leone. In 2007, global rutile mine production reached approximately 564,000 metric tons. Natural rutile supply is insufficient to meet demand; therefore, synthetic rutile largely substitutes it.
Table 4 presents the compositions of selected rutile concentrates.
Rutile Component | Eastern Australia | Sierra Leone | South Africa |
---|---|---|---|
TiO2 | 96.00 | 95.70 | 95.40 |
Fe2O3 | 0.70 | 0.90 | 0.70 |
Cr2O3 | 0.27 | 0.23 | 0.10 |
MnO | 0.02 | - | - |
Nb2O5 | 0.45 | 0.21 | 0.32 |
V2O5 | 0.50 | 1.00 | 0.65 |
ZrO2 | 0.50 | 0.67 | 0.46 |
Al2O3 | 0.15 | 0.20 | 0.65 |
CaO | 0.02 | - | 0.05 |
P2O5 | 0.02 | 0.04 | 0.02 |
SiO2 | 1.00 | 0.70 | 1.75 |
1.3. Anatase
Anatase, a titanium dioxide polymorph, primarily occurs in significant reserves within Brazilian carboniferous intrusions. Ore preparation techniques enable the production of concentrates containing 80% TiO2. Subsequent hydrochloric acid treatment can further enrich these concentrates to 90% TiO2.
The estimated titanium dioxide content in these mineral deposits reaches 108 metric tons.
1.4. Ore Preparation
Global titanium ore production primarily starts from heavy mineral sands. Figure 1 illustrates the production process.
Ilmenite frequently co-occurs with rutile and zircon; consequently, ilmenite recovery is linked to these minerals. Where geological and hydrological conditions permit, raw sand, typically containing 3–10% heavy minerals, is obtained via wet dredging (a).
Following a sieve test (b), the raw sand undergoes multi-stage gravity concentration using Reichert cones (d) or spirals (e) to yield a product containing 90–98% heavy minerals. This equipment separates heavy minerals (densities: 4.2–4.8 g/cm³) from light minerals (densities: <3 g/cm³).
Magnetic minerals, specifically ilmenite, are then separated from nonmagnetic components (rutile, zircon, silicates) through dry or wet magnetic separation (f). Ore from unweathered deposits undergoes an initial magnetite removal first.
An electrostatic separation stage (h) facilitates the removal of detrimental nonconducting mineral impurities, such as granite, silicates, and phosphates, from ilmenite.
The nonmagnetic fraction (leucoxene, rutile, zircon) subsequently undergoes further hydromechanical processing (i), using shaking tables or spirals, to eliminate residual low-density minerals, mainly quartz.
Weakly magnetic weathered ilmenites and leucoxenes are recovered via high-intensity magnetic separation (j) in a final dry stage. Conducting rutile is then electrostatically separated from nonconducting zircon in multiple stages (l). An air blast removes residual quartz.
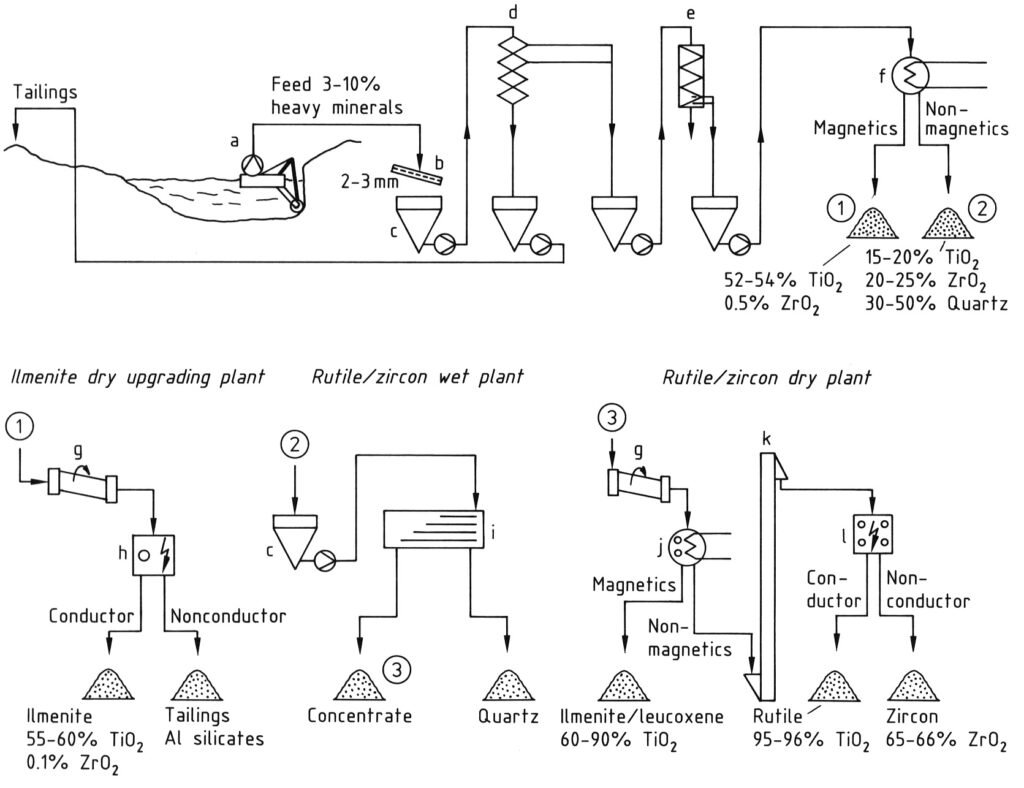
a) Dredger; b) Sieve; c) Bunker; d) Reichert cones; e) Spirals; f) Magnetic separator; g) Dryer; h) Electrostatic separator; i) Shaking table; j) Dry magnetic separator; k) Vertical belt conveyer; l) Electrostatic separator
2. Synthetic raw materials
Increased demand for raw materials with high titanium dioxide contents has driven the development of synthetic feedstocks. In all production methods, iron is removed from ilmenites or titanomagnetites.
2.1. Titanium slag
The metallurgical process for iron removal from ilmenite relies on slag formation in which iron is reduced to metal using anthracite or coke at 1200−1600 °C within an electric arc furnace. This yields titanium-free pig iron and a slag containing 75–85% titanium dioxide, depending on the ore used.
This slag is suitable for chlorination or sulfuric acid digestion due to its high Ti3+ content and low carbon levels. The suitability of slag for either the chloride or sulfate process is dependent upon titanium content, impurity levels, and particle size.
Calcium and magnesium specifically exert a detrimental effect in the chloride process. Titanium slag is produced by QIT Fer et Titane Inc. in Canada, Richard’s Bay Minerals in South Africa, and Tinfos AS in Tyssedal, Norway.
Total slag production in 2007 exceeded 2 million metric tons, with the majority designated for the chloride process. A portion of this slag undergoes further treatment to produce upgraded slag, containing over 95% TiO2, for the chloride process.
2.2. Synthetic rutile
Natural rutile deposits are scarce and costly to mine. Consequently, various processes for iron removal from ilmenite concentrates have been developed. These methods preserve the mineral’s grain size, which is optimal for subsequent fluidized-bed chlorination.
Industrial processes involve Fe3+ reduction using carbon or hydrogen, sometimes following a preliminary ilmenite oxidation. The formation of either Fe2+ within an activated ilmenite lattice or metallic iron depends on the reduction conditions.
Activated ilmenite containing Fe2+ undergoes treatment with hydrochloric or dilute sulfuric acid, ideally under pressure. This yields synthetic rutile with an 85–96% titanium dioxide content. The resulting iron(II) salt solutions are concentrated and then thermally decomposed to form iron oxide and hydrochloric acid. The hydrochloric acid is recyclable for digestion.
Metallic iron can be removed by diverse methods. Patent literature describes the following processes:
- Size reduction followed by physical separation (e.g., magnetic separation, flotation).
- Dissolution in iron(III) chloride solutions. The resulting iron(II) salt undergoes air oxidation, yielding iron oxide hydroxides and iron(III) salts.
- Acid dissolution.
- Air oxidation in the presence of an electrolyte. Various iron oxide or iron oxide hydroxide phases are formed depending on the electrolyte used. Examples of electrolytes include iron(II) chloride solutions, ammonium chloride, or ammonium carbonate–carbonic acid.
- Oxidation with iron(III) sulfate from ilmenite digestion followed by iron(II) sulfate crystallization.
- Chlorination to produce iron(III) chloride.
- Reaction with carbon monoxide to form iron carbonyls, which decompose to yield high-purity iron.
Partial iron chlorination in carbon is another method to increase titanium dioxide content in ilmenite. In 2008, 17 companies produced rutile (natural or synthetic). Leading producers included Iluka (25%), Richard’s Bay Minerals (RBM) (13%), Sierra Leone Ltd. (12%), and Consolidated Rutile Ltd. (CRL) (11%).
Approximately 60% of global rutile consumption is used for the production of titanium dioxide pigment. Global rutile production was 663,000 metric tons in 2008.
Reference
Pigments, Inorganic, 2. White Pigments. – https://onlinelibrary.wiley.com/doi/10.1002/14356007.n20_n01.pub2