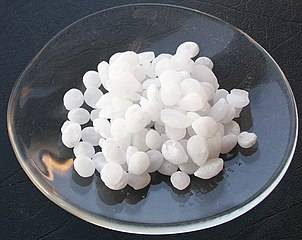
Solid sodium hydroxide, also known as caustic soda, is obtained by evaporating the sodium hydroxide solution until the water content falls below 0.5 – 1.5 wt %.
The most efficient utilization of energy is achieved with multistage equipment, as shown in the flow diagram of a plant constructed by Bertrams in Basel, Switzerland (Figure 1).
In the first stage, a 50 wt % solution is vacuum-evaporated in a pre-concentration unit, by using the heat of the vapor from the main concentrator, until the concentration reaches approximately 60 wt %.
In the second stage, a concentration of approximately 99 wt % is achieved by heating the solution with a molten salt heat-transfer medium (NaNO2 – NaNO3 – KNO3) at temperatures exceeding 400 °C in a falling-film evaporator.
The concentrated product is then fed to a flash evaporator that operates as a gas-lift pump, where molten NaOH is raised by vacuum into a heated riser pipe, causing the remaining water to evaporate. The steam bubbles lift the molten NaOH to the highest point of the system, where the steam is pumped off.
The almost anhydrous melt passes through a downcomer pipe into the holding vessel, from which it is pumped to the conditioning plant.
To prevent premature crystallization, the holding vessel, pumps, and pipes must be heated.
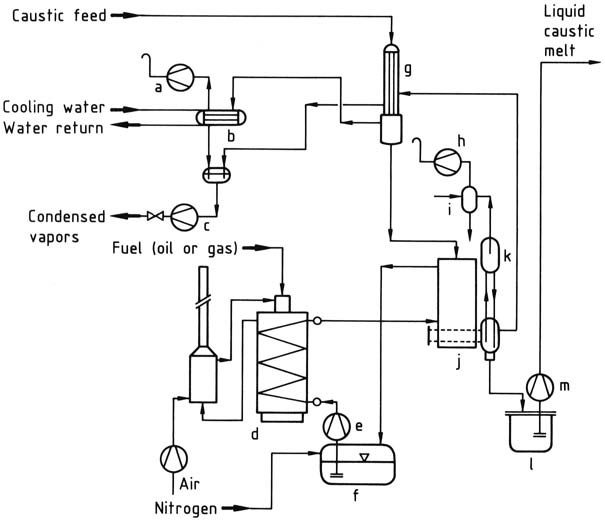
Forming
To prevent caking due to unsolidified monohydrate, the cooling and solidification of the NaOH melt must be carried out quickly, passing through both the solidification point of NaOH (322 °C) and that of the monohydrate, NaOH· H2O (62 °C).
Various forms of solid sodium hydroxide are available in the market such as flakes, prills, cast blocks, tablets, briquettes, and granules.
Flakes have a thickness of approximately 1.5 mm and a diameter of 5 – 20 mm, and their bulk density is approximately 0.9 kg/dm3. They tend to break easily, resulting in the formation of some dust during handling.
Prills bulk density is higher than 1 kg/dm3 and they take form of spheres with a diameter of 0.1 – 0.8 mm (microprills) or 0.5 –2.5 mm.
1. Flakes
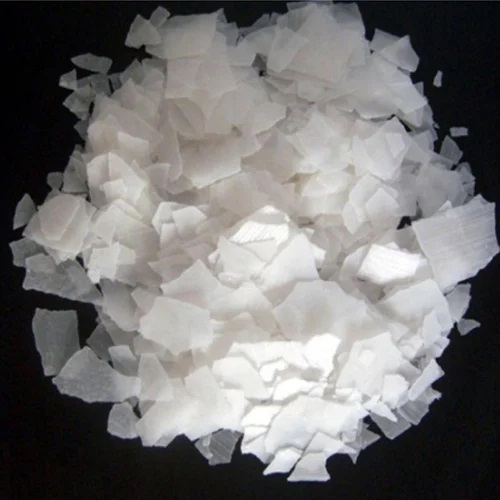
The production of flakes involves the delivery of molten NaOH into a trough that contains a partially submerged, internally cooled drum that rotates. The molten substance solidifies on the surface of the drum and is then scrapped off by a knife.
The resulting sheet of NaOH is broken into flakes, which are then transported to an intermediate storage silo. To prevent bridging, the material is stored in small silos and packed into sacks or steel drums as soon as possible.
2. Prills
Prills are produced by spraying molten NaOH at approximately 360 °C to create droplets. A spinning disk or basket is used to create these finely divided droplets that form uniform spheres due to surface tension.
As the prills fall down a shaft, air is blown upward to cool them to around 250 °C. The finished product is collected in a funnel and transferred to a cooling drum, where they are cooled to approximately 50 °C.
Prills are less likely to cake than flakes, are free-flowing, and almost dust-free, which makes them ideal for storage and transportation in silos or containers.
3. Cast Blocks
In the case of cast blocks, molten NaOH is directly poured into iron drums or similar containers. To prevent further contamination by iron, the drums are externally cooled with a spray of water that immediately forms a solid film of sodium hydroxide on the walls of the container.
4. Special Shapes
Tablets, pills, or pellets are produced using a droplet process, where molten NaOH is dripped from a special device made of silver onto a slowly rotating, cooled table or conveyor belt.
This process produces a product with a low content of metallic impurities, which makes it ideal for producing small quantities for analytical purposes.
Reference
- “Sodium Hydroxide”. Ullmann’s Encyclopedia of Industrial Chemistry. Weinheim: Wiley-VCH.- https://onlinelibrary.wiley.com/doi/10.1002/14356007.a24_345.pub2