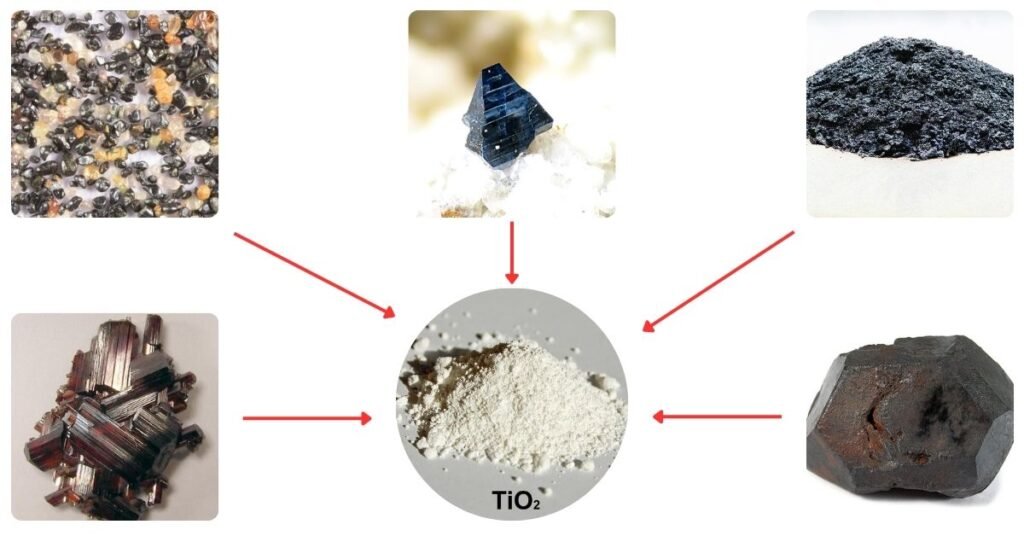
Las materias primas para la producción de dióxido de titanio incluyen productos naturales como la ilmenita, el leucoxeno y el rutilo, así como algunos materiales sintéticos muy importantes como la escoria de titanio y el rutilo sintético.
En 2007, la producción total de materia prima titanoferrosa superó los 6 millones de toneladas métricas. Australia es el mayor productor, seguida de Sudáfrica, Canadá y China.
La Tabla 1 presenta los datos de producción de importantes materias primas que contienen titanio.
Materia prima | Ubicación | Producción minera, 103 t/a |
---|---|---|
Ilmenita | Australia | 1400 |
Canadá | 816 | |
Ucrania | 290 | |
India | 378 | |
Noruega | 377 | |
Sudáfrica | 1100 | |
Estados Unidos | 300 | |
China | 550 | |
Vietnam | 254 | |
Brasil | 127 | |
Otros | 129 | |
Total | 5720 | |
Rutilo (natural y sintético) | Australia | 340 |
Ucrania | 70 | |
Sudáfrica | 120 | |
Sierra Leona | 80 | |
India | 20 | |
Otros | 30 | |
Total | 660 | |
Escoria de titanio | Canadá | 920 |
Noruega | 160 | |
Sudáfrica | 1300 | |
Total | ~2400 |
1. Materias primas naturales
El titanio es el noveno elemento más abundante en la corteza terrestre. Forma compuestos de forma constante con el oxígeno. Entre los minerales naturales de titanio, solo la ilmenita (incluido el leucoxeno) y el rutilo poseen importancia económica. El leucoxeno se forma mediante la meteorización y descomposición natural de la ilmenita.
Más del 90 % de la producción mundial de ilmenita y rutilo se destina a la producción de pigmentos. El resto se utiliza en la fabricación de titanio metálico y en el recubrimiento de varillas de soldadura.
La Tabla 2 enumera los minerales que contienen titanio más importantes.
Mineral | Fórmula | Contenido de TiO2, % en peso |
---|---|---|
Rutilo | TiO2 | 92–98 |
Anatasa | TiO2 | 90–95 |
Brookita | TiO2 | 90–100 |
Ilmenita | FeTiO3 | 35–60 |
Leucoxeno | Fe2O3TiO2 | 60–90 |
Perovskita | CaTiO3 | 40–60 |
Esfena (titanita) | CaTiSiO5 | 30–42 |
Titanomagnetita | Fe(Ti)Fe2O4 | 2–20 |
1.1. Ilmenita y leucoxeno
La ilmenita se encuentra globalmente en depósitos minerales masivos primarios y depósitos aluviales (de arena) secundarios que contienen minerales pesados. Los minerales masivos frecuentemente asocian la ilmenita con intrusiones intermedias, como las encontradas en Tellnes (Noruega) y el lago Allard (Canadá).
Los concentrados derivados de estos minerales masivos suelen presentar un alto contenido de hierro, presente en forma de hematita o magnetita segregada dentro de la ilmenita. Estos compuestos de hierro reducen el contenido de dióxido de titanio de los concentrados. El uso directo de estas ilmenitas con alto contenido de hierro ha disminuido.
El enriquecimiento de ilmenita en arenas de playa, tanto en costas actuales como fósiles, es importante para la producción de dióxido de titanio. La acción del oleaje, las corrientes o el viento concentran la ilmenita y otros minerales pesados, como el rutilo, el circón, la monacita y otros silicatos, en dunas o playas. Este proceso de concentración a menudo resulta en la estratificación mineral.
La exposición al agua de mar y a la atmósfera a lo largo de escalas de tiempo geológicas induce la corrosión de la ilmenita. El hierro se elimina de la red cristalina de la ilmenita, enriqueciendo el material restante con dióxido de titanio. La red permanece estable con contenidos de TiO2 de hasta aproximadamente el 65 %. Una mayor eliminación de hierro da lugar a una mezcla mineral submicroscópica, compuesta principalmente por fases de anatasa, rutilo y amorfa.
Las mezclas con contenidos de dióxido de titanio de hasta el 90 % se denominan leucoxeno. El leucoxeno está presente en la ilmenita corroída y en algunos depósitos; se recupera y procesa por separado. Sin embargo, los volúmenes de producción de leucoxeno son menores en comparación con los de ilmenita.
Los concentrados de arena de ilmenita, al estar empobrecidos en hierro, generalmente poseen un mayor contenido de dióxido de titanio que los de depósitos masivos. Otros elementos presentes en estos concentrados incluyen magnesio, manganeso y vanadio (inherentes a la ilmenita), así como aluminio, calcio, cromo y silicio (procedentes de intrusiones minerales).
Las reservas de ilmenita económicamente viables ascienden a aproximadamente 680 millones de toneladas métricas, de las cuales el 30 % se encuentra en China, el 20 % en Australia, el 13 % en India y el 9 % en Sudáfrica. Con la capacidad de producción actual, la demanda mundial podría satisfacerse durante más de un siglo.
Componente | Tellnes (Noruega) | Richard’s Bay (Sudáfrica) | Capel (Australia Occidental) | Quilon (India) |
---|---|---|---|---|
TiO2 | 43.8 | 46.5 | 54.8 | 60.3 |
Fe2O3 | 14.0 | 11.4 | 16.0 | 24.8 |
FeO | 34.4 | 34.2 | 23.8 | 9.7 |
Al2O3 | 0.6 | 1.3 | 1.0 | 1.0 |
SiO2 | 2.2 | 1.6 | 0.8 | 1.4 |
MnO | 0.3 | - | 1.5 | 0.4 |
Cr2O3 | - | 0.1 | 0.1 | 0.1 |
V2O5 | 0.3 | 0.3 | 0.2 | 0.2 |
MgO | 3.7 | 0.9 | 0.15 | 0.9 |
1.2. Rutilo
El rutilo se forma principalmente por cristalización de magma, específicamente a partir de fundidos ricos en titanio y bajos en hierro. Se origina de la metamorfosis de sedimentos o magmatitas que contienen titanio.
Las concentraciones de rutilo en rocas primarias son demasiado bajas para su explotación comercial. Por consiguiente, solo las arenas que contienen rutilo junto con circón, ilmenita y otros minerales pesados se consideran reservas viables. Las reservas mundiales de rutilo se estiman en 45 millones de toneladas métricas.
Los principales productores de rutilo natural son Australia, Sudáfrica y Sierra Leona. En 2007, la producción mundial de minas de rutilo alcanzó aproximadamente 564.000 toneladas métricas. La oferta de rutilo natural es insuficiente para satisfacer la demanda; por lo tanto, el rutilo sintético lo sustituye en gran medida.
La Tabla 4 presenta la composición de concentrados de rutilo seleccionados.
Componente de rutilo | Australia Oriental | Sierra Leona | Sudáfrica |
---|---|---|---|
TiO2 | 96.00 | 95.70 | 95.40 |
Fe2O3 | 0.70 | 0.90 | 0.70 |
Cr2O3 | 0.27 | 0.23 | 0.10 |
MnO | 0.02 | - | - |
Nb2O5 | 0.45 | 0.21 | 0.32 |
V2O5 | 0.50 | 1.00 | 0.65 |
ZrO2 | 0.50 | 0.67 | 0.46 |
Al2O3 | 0.15 | 0.20 | 0.65 |
CaO | 0.02 | - | 0.05 |
P2O5 | 0.02 | 0.04 | 0.02 |
SiO2 | 1.00 | 0.70 | 1.75 |
1.3. Anatasa
La anatasa, un polimorfo de dióxido de titanio, se encuentra principalmente en importantes reservas de las intrusiones carboníferas brasileñas. Las técnicas de preparación de minerales permiten la producción de concentrados con un 80 % de TiO2. El tratamiento posterior con ácido clorhídrico puede enriquecer aún más estos concentrados hasta alcanzar el 90 % de TiO2.
El contenido estimado de dióxido de titanio en estos depósitos minerales alcanza las 108 toneladas métricas.
1.4. Preparación de Minerales
La producción mundial de mineral de titanio se origina principalmente en arenas minerales pesadas. La Figura 1 ilustra el proceso de producción.
La ilmenita coexiste frecuentemente con el rutilo y el circón; por lo tanto, la recuperación de ilmenita está vinculada a estos minerales. Cuando las condiciones geológicas e hidrológicas lo permiten, se obtiene arena bruta, que suele contener entre un 3 % y un 10 % de minerales pesados, mediante dragado húmedo (a).
Tras una prueba de tamizado (b), la arena bruta se somete a una concentración gravitacional multietapa utilizando conos de Reichert (d) o espirales (e) para obtener un producto con entre un 90 % y un 98 % de minerales pesados. Este equipo separa los minerales pesados (densidades: 4,2-4,8 g/cm³) de los minerales ligeros (densidades: <3 g/cm³).
Los minerales magnéticos, en concreto la ilmenita, se separan posteriormente de los componentes no magnéticos (rutilo, circón, silicatos) mediante separación magnética seca o húmeda (f). El mineral de depósitos no meteorizados se somete primero a una extracción de magnetita.
Una etapa de separación electrostática (h) facilita la eliminación de impurezas minerales no conductoras perjudiciales, como granito, silicatos y fosfatos, de la ilmenita.
La fracción no magnética (leucoxeno, rutilo, circón) se somete posteriormente a un procesamiento hidromecánico adicional (i), mediante mesas vibratorias o espirales, para eliminar los minerales residuales de baja densidad, principalmente cuarzo.
Las ilmenitas y leucoxenos meteorizados, débilmente magnéticos, se recuperan mediante separación magnética de alta intensidad (j) en una etapa final en seco. A continuación, el rutilo conductor se separa electrostáticamente del circón no conductor en múltiples etapas (l). Un chorro de aire elimina el cuarzo residual.
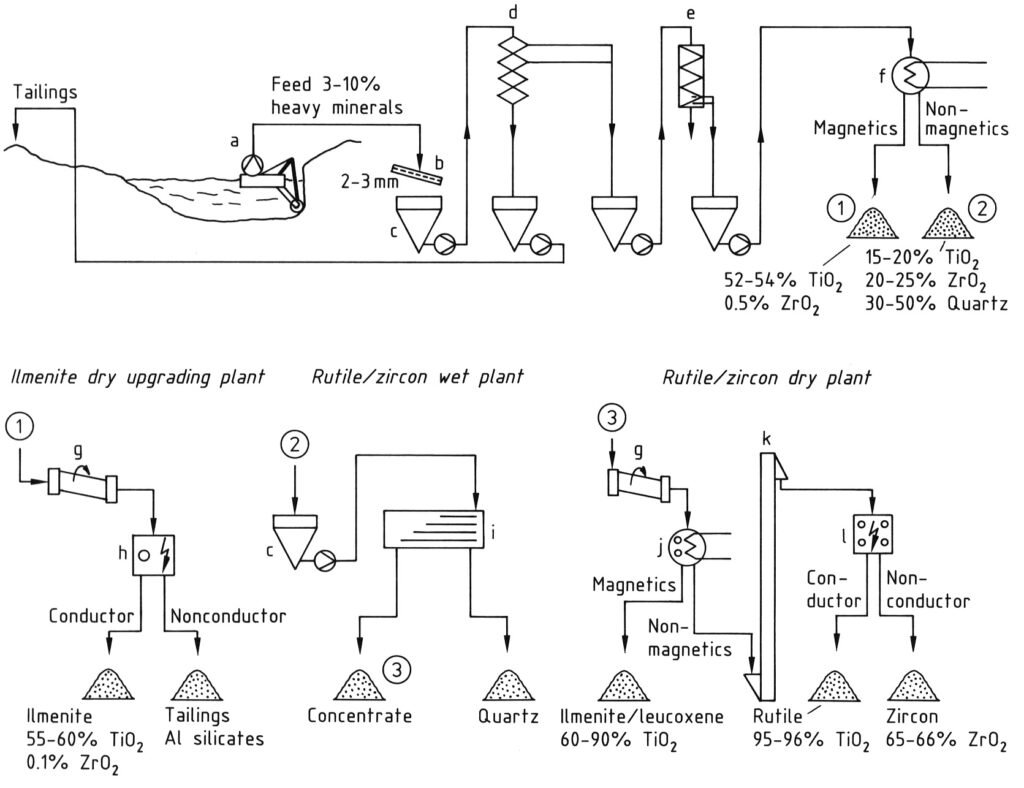
a) Draga; b) Tamiz; c) Búnker; d) Conos de Reichert; e) Espirales; f) Separador magnético; g) Secador; h) Separador electrostático; i) Mesa vibratoria; j) Separador magnético seco; k) Transportador de banda vertical; l) Separador electrostático
2. Materias primas sintéticas
La creciente demanda de materias primas con alto contenido de dióxido de titanio ha impulsado el desarrollo de materias primas sintéticas. En todos los métodos de producción, el hierro se elimina de las ilmenitas o titanomagnetitas.
2.1. Escoria de titanio
El proceso metalúrgico para la eliminación del hierro de la ilmenita se basa en la formación de escoria, en la que el hierro se reduce a metal utilizando antracita o coque a 1200-1600 °C en un horno de arco eléctrico. Esto produce arrabio sin titanio y una escoria con un contenido de dióxido de titanio del 75-85 %, dependiendo del mineral utilizado.
Esta escoria es apta para la cloración o la digestión con ácido sulfúrico debido a su alto contenido de Ti3+ y bajos niveles de carbono. La idoneidad de la escoria para el proceso de cloruro o sulfato depende del contenido de titanio, los niveles de impurezas y el tamaño de partícula.
El calcio y el magnesio ejercen un efecto perjudicial específico en el proceso de cloruro. La escoria de titanio es producida por QIT Fer et Titane Inc. en Canadá, Richard’s Bay Minerals en Sudáfrica y Tinfos AS en Tyssedal, Noruega.
La producción total de escoria en 2007 superó los 2 millones de toneladas métricas, la mayoría de las cuales se destinaron al proceso de cloruro. Una parte de esta escoria se somete a un tratamiento adicional para producir escoria mejorada, con más del 95 % de TiO2, para el proceso de cloruro.
2.2. Rutilo sintético
Los depósitos naturales de rutilo son escasos y costosos de extraer. Por consiguiente, se han desarrollado diversos procesos para la eliminación de hierro de los concentrados de ilmenita. Estos métodos preservan el tamaño de grano del mineral, lo cual es óptimo para la posterior cloración en lecho fluidizado.
Los procesos industriales implican la reducción de Fe3+ con carbono o hidrógeno, a veces tras una oxidación preliminar de la ilmenita. La formación de Fe2+ dentro de una red de ilmenita activada o de hierro metálico depende de las condiciones de reducción.
La ilmenita activada que contiene Fe2+ se somete a un tratamiento con ácido clorhídrico o sulfúrico diluido, idealmente a presión. Esto produce rutilo sintético con un contenido de dióxido de titanio del 85 al 96 %. Las soluciones de sales de hierro(II) resultantes se concentran y luego se descomponen térmicamente para formar óxido de hierro y ácido clorhídrico. El ácido clorhídrico es reciclable para la digestión.
El hierro metálico puede eliminarse mediante diversos métodos. La literatura de patentes describe los siguientes procesos:
- Reducción de tamaño seguida de separación física (p. ej., separación magnética, flotación).
- Disolución en soluciones de cloruro de hierro(III). La sal de hierro(II) resultante se oxida con el aire, produciendo hidróxidos de óxido de hierro y sales de hierro(III).
- Disolución ácida.
- Oxidación con el aire en presencia de un electrolito. Se forman diversas fases de óxido de hierro o hidróxido de óxido de hierro según el electrolito utilizado. Ejemplos de electrolitos incluyen soluciones de cloruro de hierro(II), cloruro de amonio o carbonato de amonio-ácido carbónico.
- Oxidación con sulfato de hierro(III) a partir de la digestión de ilmenita, seguida de su cristalización.
- Cloración para producir cloruro de hierro(III).
- Reacción con monóxido de carbono para formar carbonilos de hierro, que se descomponen para producir hierro de alta pureza.
La cloración parcial de hierro en carbono es otro método para aumentar el contenido de dióxido de titanio en la ilmenita. En 2008, 17 empresas produjeron rutilo (natural o sintético). Entre los principales productores se encontraban Iluka (25%), Richard’s Bay Minerals (RBM) (13%), Sierra Leone Ltd. (12%) y Consolidated Rutile Ltd. (CRL) (11%).
Aproximadamente el 60 % del consumo mundial de rutilo se destina a la producción de pigmento de dióxido de titanio. La producción mundial de rutilo fue de 663 000 toneladas métricas en 2008.
Referencia
Pigments, Inorganic, 2. White Pigments. – https://onlinelibrary.wiley.com/doi/10.1002/14356007.n20_n01.pub2