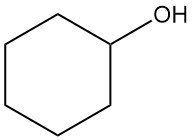
What is cyclohexanol?
Cyclohexanol is an organic compound with the chemical formula C6H12O. It is a colorless, viscous liquid or cristalline solid with a camphor-like odor that is very soluble in most organic solvents.
Cyclohexanol is an important chemical product that is produced on a large commercial scale.
Table of Contents
1. Physical Properties of Cyclohexanol
Cyclohexanol is a colorless substance that forms hygroscopic crystalline needles with a camphor-like odor. In its pure state, it melts near room temperature at 25.15 °C.
Cyclohexanol is very soluble in most organic solvents, such as alcohols, ketones, ethers, and alicyclic and aromatic hydrocarbons. It dissolves many oils, waxes, gums, and resins and forms azeotrope with water and phenol.
The most important physical properties of cyclohexanol are shown in Table 1.
Property | Value |
---|---|
CAS number | [108-93-0] |
Chemical formula | C6H11OH |
Molecular mass | 100.16 g/mol |
Melting point | 25.15 °C |
Boiling point | 161.1 °C |
Vapor pressure | 0.15 kPa at 20 °C 0.48 kPa at 35 °C |
Density | 0.9493 g/cm3 |
Refractive index | 1.4656 |
Expansion coefficient | 8.25 × 10-4 |
Dynamic viscosity | 41.07 mPa · s at 30 °C 17.20 mPa · s at 45 °C |
Specific heat | 1.747 J/g |
Surface tension at 30 °C | 33.47 mN/m |
Heat of fusion | 1.791 kJ/mol |
Heat of combustion | -3.722 MJ/mol |
Heat of vaporization | 45.51 kJ/mol |
Heat of formation | -352 kJ/mol |
Flash point | 68 °C |
Autoignition temperature | 300 °C |
Solubility in water at 20 °C | 3.6 g/100 g of water |
2. Chemical Reactions of Cyclohexanol
Cyclohexanol undergoes most of the typical reactions of secondary alcohols. It forms esters with organic acids and cyclohexyl halides with halogen acids. The most important commercial esters of cyclohexanol are dicyclohexyl phthalate, dicyclohexyl adipate, and cyclohexyl acrylate.
The reaction of cyclohexanol with phthalic acid produces cyclohexyl and dicyclohexyl phthalates, which are used as plasticizers.
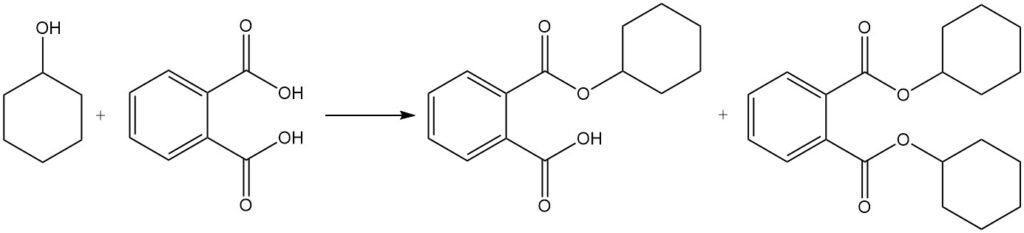
The dehydration of cyclohexanol with sulfuric acid or vapor-phase treatment with alumina at 300–400 °C produces cyclohexene.
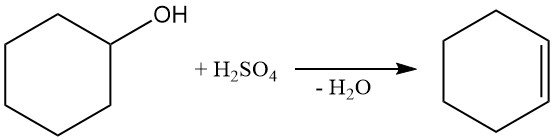
Cyclohexanol reacts with sodium bromide and sulphuric acid to produce bromocyclohexane with a yield of > 50%.
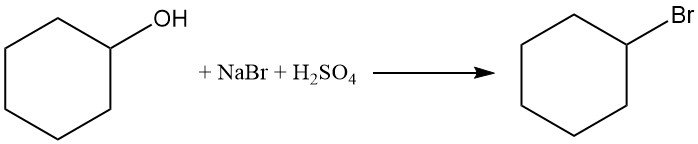
Mild oxidation or catalytic dehydrogenation gives cyclohexanone, which can be further oxidized to adipic acid using nitric acid at 75–80 °C and 1–4 bar. This reaction is industrially important.
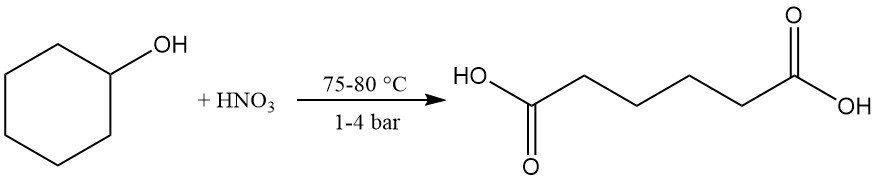
The reaction of cyclohexanol with ammonia yields cyclohexylamine.
3. Industrial Production of Cyclohexanol
Cyclohexanol was produced industrially by hydrogenation of phenol, which also forms cyclohexanone. In the 1940s, liquid-phase air oxidation of cyclohexane catalyzed by transition metals was developed to synthesize a cyclohexanol-cyclohexanone mixture. Catalyst selection influenced the product ratio.
In the 1950s, Scientific Design produced cyclohexanol selectively by boric acid modified liquid-phase air oxidation of cyclohexane, passing by an intermediate cyclohexyl hydroperoxide. around 1990, Asahi produced cyclohexanol from cyclohexene, which is obtained from benzene partial hydrogenation.
3.1. Production of Cyclohexanol by Hydrogenation of Phenol
The choice of metal catalysts in phenol hydrogenation determines the product distribution, either cyclohexanol, cyclohexanone, or their mixture.
Cyclohexanol can be produced in high yields by both vapor- and liquid-phase hydrogenation of phenol.
Cyclohexanol is produced with a 98% yield by vapor-phase hydrogenation of phenol using nickel-based catalysts, often supported on alumina or silica.
A flow diagram of the vapor-phase hydrogenation of phenol is shown in Figure 1.
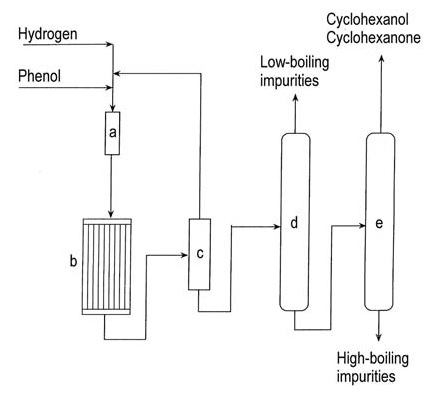
a) Phenol evaporator; b) Hydrogenation reactor; c) Condenser; d) Low-boiler removal column; e) Cyclohexanol/cyclohexanone recovery column
Commercial liquid-phase hydrogenation of phenol under mild conditions with a Raney nickel catalyst achieves 99.9 % selectivity for cyclohexanol.
3.2. Production of Cyclohexanol by Liquid-Phase Oxidation of Cyclohexane
Cyclohexane liquid-phase air oxidation to cyclohexanol and cyclohexanone emerged in the 1940s. This process is conducted in agitated reactors at 140–180 °C and 0.8–2 MPa and uses either cobalt catalysis or uncatalyzed conditions.
Cyclohexyl hydroperoxide is an intermediate that forms during the reaction and is subsequently converted to cyclohexanol and cyclohexanone.
Catalyst choice influences the cyclohexanol-to-cyclohexanone ratio, with cobalt catalysts yielding a 3.5 ratio of cyclohexanol to cyclohexanone. Various oxygenated compounds are produced as by-products.
Cyclohexanol yield can be improved by maintaining high hydroperoxide levels in the oxidizer effluent.
Methods and conditions used to decompose hydroperoxide intermediates influence the cyclohexanol-to-cyclohexanone ratio obtained. (see Table 2)
Solution/Modification | Catalyst | Temperature (°C) | Ratio (Cyclohexanol : Cyclohexanone) |
---|---|---|---|
A | none | 155 | 0.8 |
A | Cr | 155 | 0.4 |
A | Ni | 155 | 1.4 |
A | V | 155 | 1.4 |
A | Co | 155 | 3.0 |
A | Mn | 155 | 3.3 |
B | Co | 160 | 2.5 |
A - hydrogenation of cyclohexyl hydroperoxide | Pd | 150 | 5 - 10 |
A - separate caustic aqueous phase | Co | 120 | 0.2 |
* A = cyclohexyl hydroperoxide in cyclohexane; B = cyclohexyl hydroperoxide in air oxidizer tails.
3.3. Production of Cyclohexanol by Boric Acid-Modified Oxidation of Cyclohexane
In the 1950s, Scientific Design modified the process of cyclohexane air oxidation by adding anhydrous metaboric acid to the first oxidation reactor (Figure 2). Cyclohexyl hydroperoxide is trapped as a cyclohexyl perborate ester and then reacts with cyclohexane to form borate ester and cyclohexanol.
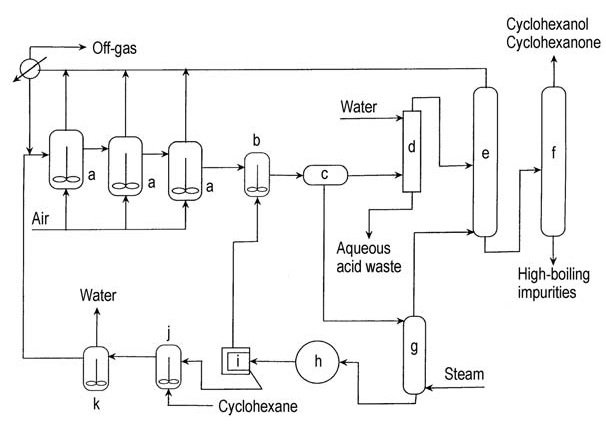
a) Air oxidizers; b) Ester hydrolysis vessel; c) Decanter; d) Extraction column; e) Cyclohexane recovery column; f) Refining column; g) Stripping column; h) Vaccuum crystallizer; i) Boric acid centrifuge; j) Boric acid slurry tank; k) Dehydrator
This stable ester resists over-oxidation and is subsequently hydrolyzed to cyclohexanol and boric acid. Boric acid is dehydrated to metaboric acid, which is recycled to the air oxidizer.
The process chemistry is similar to the metal-catalyzed oxidation of cyclohexane, but the cyclohexyl ring is protected from oxidation.
Despite higher investment and operating costs compared to other methods, the boric acid process gives higher cyclohexanol and cyclohexanone yields up to 88%, with a high cyclohexanol selectivity of 91%. The Institut Francais du Petrole has further developed this technology.
The major current manufacturers using this process are Solutia, DuPont (UK), Bayer, and Mitsubishi. Rhône-Poulenc’s original plant based on this technology is now closed.
3.4. Production of Cyclohexanol by Hydration of Cyclohexene
In 1972, selective benzene hydrogenation to cyclohexene was first patented. Subsequently, patents for cyclohexene hydration to cyclohexanol using various catalysts followed.
Asahi commercialized this process in 1990 with a 100 t/a plant. The process comprises three stages: benzene selective hydrogenation, cyclohexene separation from unconverted benzene and cyclohexane, and cyclohexene hydration (Figure 3).
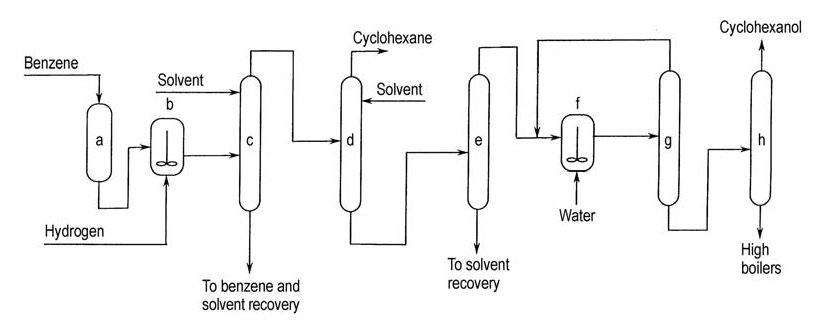
a) Benzene purification; b) Partial hydrogenation; c) Separation of unconverted benzene from cyclohexene and cyclohexane; d) Separation of cyclohexene from cyclohexane; e) Separation of cyclohexene from extractive solvent; f) Hydration of cyclohexene; g) Recycle of unconverted cyclohexene; h) Purification of cyclohexanol
Hydrogenation of benzene uses a specialized heterogeneous nickel catalyst and operates at approximately 50% conversion to yield a mixture of about 35 % cyclohexene, 15 % cyclohexane, and 50 % unconverted benzene.
Impurities like sulfur and iron significantly impact selectivity, which is why it is necessary to use purified benzene and line the hydrogenation vessel with an inert material.
The cyclohexane-cyclohexene-benzene mixture undergoes two successive extractive distillations. Recovered cyclohexane can be converted back to benzene or sold to other caprolactam and adipic acid producers.
Hydration of cyclohexene to cyclohexanol also employs a heterogeneous catalyst in a slurry reactor. Equilibrium limits conversion to approximately 14%.
The benzene-to-cyclohexanol yield is exceptionally high, likely exceeding 95%. While byproducts are minimal, investment surpasses conventional cyclohexane oxidation plants.
4. Uses of Cyclohexanol
Cyclohexanol is used industrially in the production of primarily adipic acid, which is used in the manufacture of nylon-6,6 and cyclohexanone, which is a caprolactam precursor.
In 1992, the U.S. cyclohexanol market (excluding nylon intermediates) reached 10,000 tons.
Major applications of cyclohexanol are:
- As a solvent for lacquers, varnishes, oils, alkyd resins, gums, shellacs, ethyl cellulose, acid dyes, and natural resins.
- In the preparation of esters for plasticizers, e.g., dicyclohexyl phthalate.
- In the laundry industry and in soaps and synthetic detergents, as a homogenizer and stabilizer.
- In paint and varnish removers.
- In the production of cyclohexylamine, which is a corrosion inhibitor.
- In the insecticide, fragrance, polish, and rubber cement industries.
- In the textile industry as a dye solvent and kier-boiling assistant.
5. Toxicology of Cyclohexanol
Cyclohexanol exhibits low oral toxicity and mild skin irritation. Ocular exposure induces severe irritation and transient corneal damage. Inhalation of high vapor concentrations (approximately 1000 ppm) in rabbits leads to conjunctival and respiratory irritation, lethargy, incoordination, narcosis, and mild convulsions.
Reproductive toxicity studies in mice indicate increased offspring mortality following maternal cyclohexanol consumption during gestation. Testicular atrophy with loss of spermatogenic cells has been reported in rats and gerbils after repeated subcutaneous administration.
Similar effects occurred in rabbits following oral exposure. However, one study failed to demonstrate testicular atrophy in rats despite high-dose oral administration.
The ACGIH has established a TLV-TWA of 50 ppm (approximately 200 mg/m³) with a skin notation.
Proper handling of cyclohexanol necessitates adequate ventilation, avoidance of prolonged exposure, ingestion prevention, and ocular protection.
References
- Cyclohexanol and Cyclohexanone; Ullmann’s Encyclopedia of Industrial Chemistry. – https://onlinelibrary.wiley.com/doi/10.1002/14356007.a08_217.pub2
- Cyclohexanol and Cyclohexanone. – https://onlinelibrary.wiley.com/doi/full/10.1002/0471238961.0325031206091908.a01
- https://onlinelibrary.wiley.com/doi/10.1002/0471743984.vse2329.pub2
- https://www.sciencedirect.com/science/article/abs/pii/B9780323851596501093
- https://onlinelibrary.wiley.com/doi/abs/10.1002/recl.19630820107
- https://onlinelibrary.wiley.com/doi/10.1002/0471740039.vec0746
- https://www.sciencedirect.com/science/article/abs/pii/S1460156705800200
- https://pubchem.ncbi.nlm.nih.gov/compound/Cyclohexanol