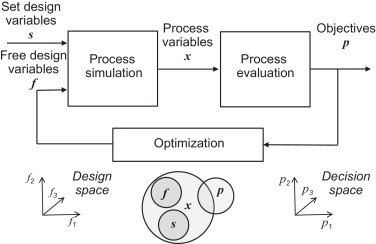
Chemical process optimization is the process of improving the efficiency and effectiveness of chemical processes in the industry. It is an essential aspect of modern manufacturing, and it plays a crucial role in maintaining the profitability of chemical plants.
Table of Contents
1. Importance of Chemical Process Optimization in Industry
Chemical process optimization is critical in the chemical industry for several reasons. First, it helps to increase productivity by reducing the amount of time and resources required to complete a chemical process.
This results in cost savings, which can be passed on to customers or reinvested into the company. Second, optimization improves product quality by reducing defects and variability in the manufacturing process.
In turn, It leads to increased customer satisfaction and loyalty. Third, process optimization can help companies meet regulatory requirements by ensuring that chemical processes comply with environmental, health, and safety regulations.
2. Strategies for Chemical Process Optimization
There are several strategies used to optimize chemical processes in industry. Some of the most common strategies are discussed below.
2.1. Process Monitoring and Control
Process monitoring and control involve the use of sensors, data acquisition systems, and control algorithms to monitor and control the various parameters of a chemical process. By continuously monitoring process variables, such as temperature, pressure, and flow rate, and adjusting the process accordingly, manufacturers can optimize the process and reduce variability.
2.2. Statistical Process Control
Statistical process control (SPC) is a statistical technique used to monitor and control a process. It involves collecting data on the process and using statistical methods to analyze the data and identify trends and patterns. SPC can help manufacturers identify when a process is deviating from its expected performance and take corrective action before defects occur.
2.3. Lean Manufacturing
Lean manufacturing is a manufacturing philosophy that focuses on reducing waste and maximizing efficiency. By eliminating non-value-added activities and optimizing the use of resources, lean manufacturing can help manufacturers improve productivity, reduce costs, and improve product quality.
2.4. Six Sigma
Six Sigma is a quality management methodology that seeks to eliminate defects and reduce variability in a process. By using statistical methods to analyze data and identify the root causes of defects, manufacturers can implement process improvements that reduce variability and improve product quality.
2.5. Simulation and Modeling
Simulation and modeling involve using computer software to simulate and optimize a chemical process. By creating a virtual model of the process and experimenting with different process parameters, manufacturers can identify the optimal process conditions that result in maximum efficiency and quality.
2.6. Process Integration
Process integration involves the integration of different chemical processes to create a more efficient and effective manufacturing process. By integrating processes, manufacturers can reduce waste, improve efficiency, and increase productivity.
3. Benefits of Chemical Process Optimization
Chemical process optimization offers several benefits to manufacturers. First, it improves productivity by reducing the amount of time and resources required to complete a process. This results in cost savings, which can be passed on to customers or reinvested into the company.
Process optimization improves product quality by reducing defects and variability in the manufacturing process. This, in turn, leads to increased customer satisfaction and loyalty.
Optimization can help companies meet regulatory requirements by ensuring that chemical processes comply with environmental, health, and safety regulations.
4. Conclusion
Chemical process optimization is critical in the chemical industry for several reasons. It helps to increase productivity, improve product quality, and meet regulatory requirements.
By using strategies such as process monitoring and control, statistical process control, lean manufacturing, Six Sigma, simulation and modeling, and process integration, manufacturers can optimize their processes and achieve these benefits.
In an increasingly competitive marketplace, chemical process optimization is essential for maintaining profitability and staying ahead of the competition.
References
- Machine Learning in Chemical Engineering: Strengths, Weaknesses, Opportunities, and Threats,Engineering. – https://www.sciencedirect.com/science/article/pii/S2095809921002010
- Statistical Process Control A Guide for Implementation (2020). – https://doi.org/10.1201/9781003065661
- Lean manufacturing: a review of research and practice (2016) – https://www.emerald.com/insight/content/doi/10.1108/IJOPM-01-2016-0043/full/html
- Quality improvement in the chemical process industry using Six Sigma technique (2003). – https://www.sciencedirect.com/science/article/abs/pii/S1570794603805515
- Process modeling and simulation for chemical engineers: theory and practice (2017) – https://www.wiley.com/en-gb/Process+Modeling+and+Simulation+for+Chemical+Engineers%3A+Theory+and+Practice-p-9781118914663
- Current status and future trends of computer-aided process design, applied to purification of liquid biofuels, using process intensification: A short review (2022). – https://doi.org/10.1016/j.cep.2022.108804