Il benzene veniva tradizionalmente prodotto dal carbone, ma il petrolio è diventato la fonte primaria a metà del XX secolo a causa di nuovi processi e di una domanda crescente. Il cracking catalitico e il reforming delle frazioni di petrolio producono benzene e altri aromatici.
Sommario
1. Produzione di benzene dal carbone
La carbonizzazione del carbone produce oli leggeri che contengono benzene, toluene e xileni (BTX). La resa e la composizione di questi oli dipendono dal tipo di carbone e dalla temperatura di carbonizzazione. La coking a bassa temperatura produce un coke a combustione pulita con un contenuto di benzene inferiore. La coking ad alta temperatura produce un coke duro per altiforni e oli leggeri con un contenuto di benzene superiore.
Gli oli leggeri vengono separati dai catrami di carbone e la frazione BTX viene estratta utilizzando una frazione di petrolio ad alto punto di ebollizione. Il BTX viene quindi recuperato dall’olio assorbente e purificato mediante distillazione, trattamento con acido solforico e idrotrattamento. L’estrazione con solvente e il frazionamento ravvicinato vengono utilizzati per isolare i singoli componenti aromatici.
Sono stati sviluppati vari processi per raffinare il BTX tagliato in benzene ad alta purezza o componenti BTX di qualità superiore. Il processo Houdry-Litol è un esempio di processo che utilizza una serie di reazioni e un reattore catalitico per raffinare il taglio BTX. Il processo Litol modificato è particolarmente adattabile per materiali aromatici complessi da forno a coke.
Una piccola quantità di benzene può anche essere ottenuta dalla distillazione di catrami da forno a coke, ma questa fonte non è di grande importanza nella produzione di benzene. I catrami di carbone sono più importanti come fonti di pece, naftalene, antracene e altri materiali aromatici condensati.
2. Produzione di benzene dal petrolio
Il cracking catalitico e il reforming del petrolio, sviluppati alla fine degli anni ’30 e ’40, divennero una nuova fonte di benzene, toluene, xileni e aromatici superiori. Il petrolio sostituì il carbone come fonte di materiali BTX, soprattutto negli Stati Uniti. La transizione dal carbone al petrolio avvenne nel Regno Unito e in Europa intorno al 1960.
Il toluene era molto richiesto durante la seconda guerra mondiale per la produzione di TNT. Tuttavia, era costoso produrlo da nafte vergini e in seguito da nafte crackizzate e riformate cataliticamente. Uno dei primi processi di cracking catalitico fu sviluppato da Houdry Corp.
Questo processo utilizzava un catalizzatore silice-allumina depositato in diversi letti fissi e rigenerato frequentemente con aria per bruciare il coke depositato. Un altro processo sviluppato da Mobil Oil utilizzava un catalizzatore silice-allumina a letto mobile. Il terzo tipo di processo, sviluppato da Exxon e altri, è noto come processo di cracking catalitico fluido (FCC) ed è ora utilizzato esclusivamente.
Sebbene i processi di cracking catalitico siano stati sviluppati principalmente per aumentare la resa e il numero di ottano dei carburanti per motori, la benzina prodotta aveva un alto contenuto aromatico, fornendo una fonte di benzene petrolchimico.
2.1. Benzene da Reformate
Il reforming catalitico è diventato un’altra fonte di aromatici BTX dal petrolio. È stato installato negli anni ’40 e all’inizio degli anni ’50 per soddisfare la crescente domanda di benzene, che veniva utilizzato per produrre resine, detergenti, fibre sintetiche e altri prodotti chimici.
Il reforming comporta la deidrogenazione dei nafteni in aromatici o l’isomerizzazione degli alchilnafteni seguita dalla deidrogenazione. Anche le paraffine possono essere deidrociclizzate in aromatici. La reazione è lenta, quindi le condizioni di processo devono essere regolate per renderla economica. Può verificarsi anche una piccola quantità di dealchilazione degli aromatici alchilati.
Le prime unità di reforming catalitico utilizzavano catalizzatori di metalli di base, come la molibdena su allumina attivata. Questi processi avevano una breve durata del ciclo e richiedevano una frequente rigenerazione del catalizzatore. Il processo di idroformatura funzionava a temperature e pressioni elevate con riciclo dell’idrogeno. Converte le frazioni di nafta in benzine ad alto numero di ottano. Il catalizzatore richiedeva la rigenerazione ogni 8-16 ore.
I successivi processi di reforming catalitico utilizzavano letti catalitici mobili o letti fluidizzati con un catalizzatore finemente suddiviso. Sono stati sviluppati anche vari processi catalitici che utilizzano platino su allumina e platino con modificatori su allumina.
Questi processi possono avere durate di ciclo fino a sei mesi o molto più brevi, a seconda della materia prima, delle condizioni di processo e della gravità dell’operazione. La materia prima di nafta deve essere pretrattata con idrotrattamento catalitico per rimuovere i composti di zolfo.
I processi di reforming catalitico commerciali includono: reforming catalitico (Institut Français du Pétrole), magnaforming (Engelhard Industries), platforming (UOP), powerforming (Exxon Research & Engineering), rheniforming (Chevron Research Co.) e ultraforming (Standard Oil of Indiana).
Le condizioni operative variano ampiamente. Le temperature variano da 425 a 525 °C e le pressioni manometriche da 0,7 a 3,5 MPa.
Le conversioni del naftene si avvicinano al 100%. La ciclizzazione delle paraffine è molto più bassa. Ad esempio, per produrre benzene da stock C6 e superiori, il metilciclopentano viene isomerizzato a cicloesano e deidrogenato a benzene. La conversione di n-esano in benzene è limitata.
Le unità di reforming catalitico possono essere azionate a pressioni relativamente elevate con una serie di reattori a letto fisso. Il catalizzatore viene rigenerato a intervalli definiti. Le unità progettate per una conversione più elevata funzionano a pressioni inferiori con una rigenerazione del catalizzatore più frequente. Vengono utilizzati cicli più brevi, reattori oscillanti o rigenerazione continua.
Il processo di platforming mostrato nella Figura 1 impiega la rigenerazione continua del catalizzatore.
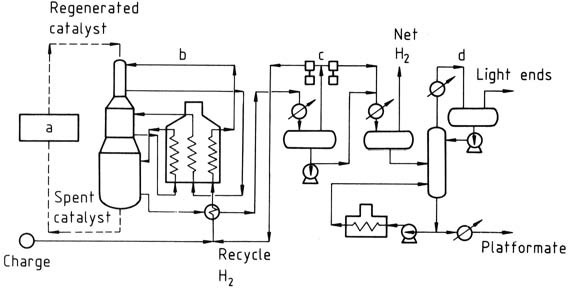
a) Rigenerazione del catalizzatore; b) Reattori; c) Separazione del prodotto; d) Stabilizzatore
Un altro progetto sviluppato da Standard Oil of Indiana utilizza un reattore oscillante in cui il catalizzatore a letto fisso in un reattore viene rigenerato e riportato in funzione, mentre i catalizzatori in ciascuno dei reattori rimanenti vengono rigenerati a rotazione. Nei diversi processi vengono utilizzate pressioni manometriche di 0,7-2,4 MPa.
Per la produzione di benzina, vengono utilizzate nafte con intervalli di ebollizione di circa 80-210 °C. Se si esegue il reforming per la produzione di stock di carica aromatica, la composizione e l’intervallo di ebollizione della nafta possono essere alterati.
Il reformato può avere un numero di ottano RON pari a 100 e può contenere fino al 70% in volume di aromatici.
Nel corso degli anni, il processo è stato reso più efficace. I catalizzatori di reforming sono stati modificati. Si è scoperto che piccole quantità di acqua migliorano le rese di benzene con determinati catalizzatori durante la produzione di BTX. Rese di xilene più elevate sono risultate dal funzionamento a velocità spaziali maggiori.
2.2. Benzene da benzina di pirolisi
La benzina di pirolisi, un sottoprodotto della produzione di etilene, è un’altra buona fonte di BTX. La quantità di benzina di pirolisi prodotta dipende dalla materia prima e dalle condizioni operative. È più alta con materie prime più pesanti e può arrivare fino al 20% per la nafta a medio raggio.
La composizione della benzina di pirolisi varia a seconda del punto di ebollizione dell’alimentazione, con alimentazioni più pesanti che producono più toluene e xilene rispetto al benzene.
La benzina di pirolisi contiene > 60% di BTX, ma contiene anche insaturi e diolefine a causa dell’alta temperatura necessaria per la produzione di etilene. Il contenuto di diolefine è in genere del 3-5% e il contenuto totale di olefine cicliche e diolefine cicliche è anch’esso del 3-5%.
La benzina di pirolisi è instabile a causa del materiale diolefinico. Le diolefine a basso punto di ebollizione possono essere rimosse tramite distillazione, ma ciò può essere difficile a causa della loro tendenza a polimerizzare e depolimerizzare. Pertanto, viene generalmente utilizzato un processo di idrotrattamento in due fasi.
La prima fase converte le diolefine in olefine. Se la benzina deve essere utilizzata come carburante, potrebbe non essere necessario un ulteriore trattamento. Tuttavia, se la benzina è una fonte di aromatici, viene utilizzata una seconda fase per saturare le olefine e rimuovere lo zolfo residuo.
3. Altri metodi di produzione del benzene
Per soddisfare la domanda, la produzione di benzene può essere aumentata da altri composti aromatici, come le frazioni BTX ottenute da reforming catalitico, benzina da pirolisi o oli leggeri dalla carbonizzazione del carbone. Ciò può essere fatto utilizzando processi di idrodealchilazione, disproporzione o combinazione.
3.1. Produzione di benzene mediante idrodealchilazione
L’idrodealchilazione è un processo di rimozione dei gruppi alchilici dai composti aromatici utilizzando idrogeno. È una fonte di benzene e il toluene è la carica di carica usuale. Possono essere utilizzati anche aromatici più alchilati, ma la reazione procede per gradi. Altri alchilbenzeni, come l’etilbenzene e il propilbenzene, dealchilano in un unico passaggio e formano gli alcani corrispondenti.
Processi catalitici e termici
Per l’idrodealchilazione vengono utilizzati sia processi catalitici che termici. I processi catalitici, come Detol e Hydeal, operano a 575-650 °C e 2,5-6 MPa. I processi termici, come HDA e THD, operano a temperature più elevate rispetto ai processi catalitici, ma le rese e i sistemi di reazione sono simili in entrambi i tipi.
Processo Detol (Figura 2)
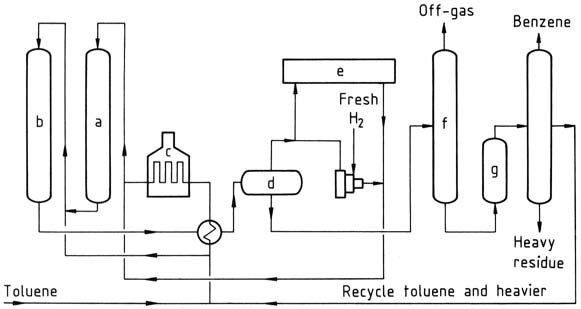
a) Reattore I; b) Reattore II; c) Fornace; d) Separatore; e) Purificazione dell'idrogeno; f) Stabilizzatore; g) Trattamento dell'argilla
Il processo Detol è un processo di dealchilazione catalitica che utilizza un catalizzatore di dealchilazione a letto fisso. L’alimentazione è costituita da toluene o miscele di toluene e altri benzeni alchilati. Gli aromatici alchilati e l’idrogeno passano a temperatura e pressione elevate sul catalizzatore in serie.
Gli scambiatori di calore raffreddano i prodotti del reattore e condensano benzene, toluene non reagito e benzeni alchilati non reagiti più pesanti. Un tamburo flash ad alta pressione separa l’idrogeno di riciclo e il gas prodotto. Il gas prodotto viene suddiviso in flussi per gas combustibile, per la purificazione dell’idrogeno se necessario e per l’idrogeno di riciclo.
Il liquido dal tamburo flash viene pompato in uno stabilizzatore, dove il gas rimanente e gli idrocarburi bassobollenti vengono allontanati e utilizzati come gas combustibile. I fondi dello stabilizzatore vengono trattati con argilla e passati in una colonna dove il benzene viene distillato in alto.
Il toluene non reagito e gli aromatici più pesanti vengono riciclati. Il benzene prodotto in rese di circa il 99% molare è altamente puro, in genere 99,95%, con un punto di congelamento di 5,45 °C.
Processo Hydeal
Il processo Hydeal è un altro processo di dealchilazione catalitica. È simile al processo Detol, ma utilizza invece un catalizzatore di cromo-allumina. Il benzene di grado di nitrazione si ottiene in rese di circa il 98% molare. Il materiale di carica aromatica non reagito dall’operazione once-through viene riciclato per ottenere una conversione praticamente completa. Il processo viene utilizzato anche per idrodealchilare gli alchilnaftaleni.
Processi HDA e THD (Figura 3)
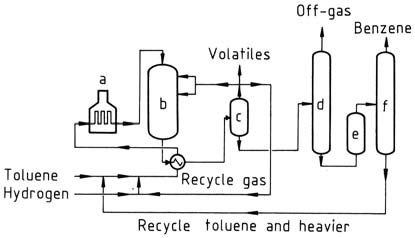
a) Riscaldatore; b) Reattore; c) Separatore; d) Stabilizzatore; e) Trattamento argilla; f) Distillazione
I processi HDA e THD sono processi di dealchilazione termica. Operano a temperature e pressioni più elevate rispetto ai processi catalitici. Si ottengono rese di benzene del 99% in moli.
Processo MHC (Figura 4)
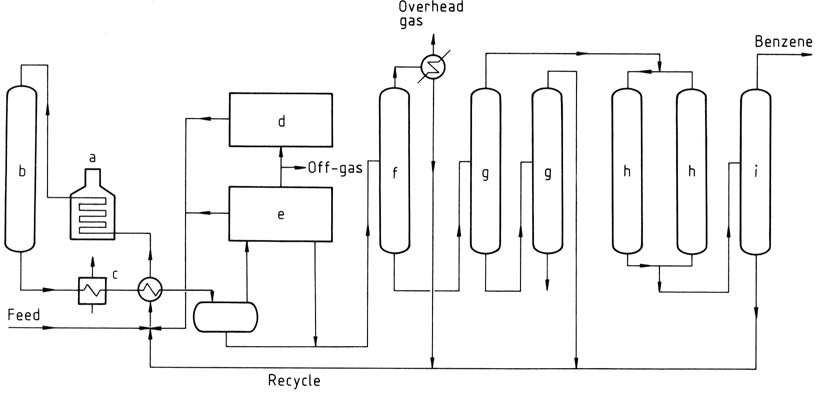
a) Riscaldatore; b) Reattore; c) Caldaia a recupero di calore; d) Rigenerazione dell'idrogeno; e) Recupero aromatico; f) Frazionamento; g) Colonne a vuoto; h) Trattatori di argilla; i) Colonna benzene
Il processo MHC è un processo di dealchilazione termica sviluppato da Mitsubishi Petrochemical Co. Può gestire materie prime contenenti fino al 30% di non aromatici senza ricorrere a fasi di estrazione aromatica e distillazione frazionata. Il processo opererà su idrogeno a bassa purezza, riducendo così la quantità di idrogeno di reintegro richiesta. Si ottiene facilmente benzene con una purezza del 99,95%.
3.2. Produzione di benzene per disproporzione
Il processo Tatoray è un modo per produrre benzene e xileni da toluene e aromatici C9. Utilizza un catalizzatore di metalli nobili o terre rare e ricicla l’idrogeno per far funzionare la reazione. Il processo opera a 350-525 °C e 1-5 MPa.
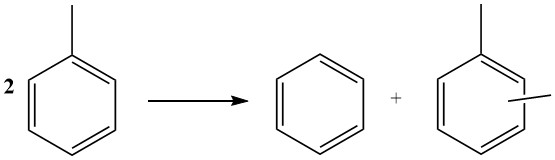
Il benzene prodotto è molto puro e gli xileni contengono pochissimi idrocarburi saturi. Quando la materia prima è limitata ad aromatici C9 e C10, il processo produce una miscela di benzene, toluene e xileni.
Il processo Tatoray è utilizzato in numerosi impianti commerciali in tutto il mondo. La resa di benzene e xileni è di circa il 97% quando il toluene viene utilizzato come materia prima.
3.3. Produzione di benzene mediante processi di dealchilazione combinata
Sono stati sviluppati diversi processi per produrre benzene da materie prime BTX impure combinando idrogenazione e dealchilazione.
Un esempio è il processo Pyrotol (Figura 5), che prevede il frazionamento della materia prima per rimuovere composti leggeri e pesanti, la vaporizzazione della frazione C6-C8 e il suo passaggio attraverso un reattore catalitico per idrogenare selettivamente diolefine, diolefine cicliche e stirene.
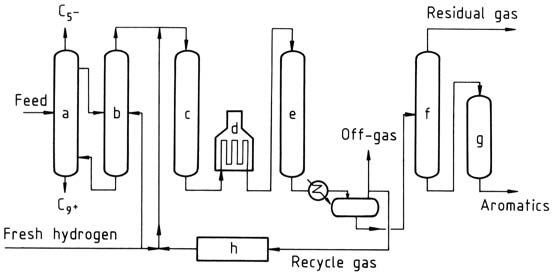
a) Distillazione; b) Vaporizzatore; c) Prereattore; d) Riscaldatore; e) Reattore Pyrotol; f) Stabilizzatore; g) Trattamento argilla; h) Purificazione idrogeno
L’effluente dal reattore di pretrattamento viene quindi caricato nei reattori Pyrotol, dove gli aromatici vengono dealchilati a benzene. Altre reazioni includono la desolforazione e l’idrocracking dei non aromatici. Il toluene non reagito e gli aromatici più pesanti vengono riciclati. Il prodotto benzenico contiene meno di 0,5 ppm di tiofene e ha un punto di congelamento di almeno 5,47 °C.
Un altro esempio è il processo Litol, sviluppato dalla divisione Houdry di Air Products e dalla Bethlehem Steel. Questo processo produce benzene puro da olio leggero aromatico ottenuto dalla carbonizzazione del carbone. Utilizza due stadi di reazione catalitica.
Dopo il prefrazionamento dell’olio leggero grezzo per rimuovere le frazioni C5 e più leggere in testa e C9 e più pesanti come fondo, la frazione C6-C8 viene vaporizzata. Nella prima fase, diolefine e stirene vengono idrogenati.
L’effluente entra quindi in contatto con il catalizzatore Litol cromo-allumina a 500-600 °C, dove si verificano desolforazione, idrocracking e dealchilazione. La purezza del benzene del 99,97% con punto di congelamento di 5,5 °C e un contenuto di tiofene inferiore a 0,5 ppm sono tipici.
Un processo è stato sviluppato da Mitsubishi Petrochemical Co. per produrre benzene dalla benzina di pirolisi. Questo processo prevede un’idrogenazione in due fasi seguita da estrazione con solvente per estrarre gli aromatici o, in alternativa, una reazione del materiale idrogenato nel processo MHC di Mitsubishi.
Mobil Chemical Co. ha sviluppato un processo di disproporzionamento in fase liquida per convertire il toluene in benzene e xileni. Questo processo di disproporzione a bassa temperatura (LTD) impiega un catalizzatore altamente attivo a base di zeolite che consente alla reazione di procedere a temperature basse fino a 260 °C. Il riciclo dell’idrogeno non è richiesto in questo processo in fase liquida.
Riferimento
- Benzene; Ullmann’s Encyclopedia of Industrial Chemistry. – https://onlinelibrary.wiley.com/doi/10.1002/14356007.a03_475