Acetyleen wordt geproduceerd door verschillende methoden: calciumcarbide-reactie, gedeeltelijke verbranding van koolwaterstoffen, elektrische boogprocessen, thermisch kraken met warmtedragers en als bijproduct van stoomkraken.
1. Reactie op calciumcarbide:
- Deze traditionele methode omvat het laten reageren van calciumcarbide met water, waarbij zowel acetyleen als calciumhydroxide ontstaat.
- Het is een eenvoudig en goed ingeburgerd proces, maar de productie van calciumcarbide vereist veel energie en brengt milieuproblemen met zich mee.
2. Gedeeltelijke verbranding van koolwaterstoffen:
- Deze methode maakt gebruik van de gedeeltelijke oxidatie van aardgas, methaan of zwaardere koolwaterstoffen zoals nafta en vacuümgasolie in een brander om ter plaatse acetyleen te genereren.
- Het biedt flexibiliteit in de keuze van de grondstof en mogelijk een hogere efficiëntie vergeleken met calciumcarbide, maar nauwkeurige controle van de reactieomstandigheden is cruciaal.
3. Elektrische boogprocessen:
- Deze processen kraken koolwaterstoffen met behulp van elektrische bogen met hoge temperatuur, waardoor de endotherme acetyleensynthesereactie direct wordt aangestuurd.
- Ze bieden onafhankelijkheid van het type koolwaterstofgrondstof en potentieel verminderd koolwaterstofverbruik vergeleken met gedeeltelijke verbranding, maar vereisen hoogwaardige elektriciteit en een complex boogreactorontwerp.
4. Thermisch kraken met warmtedragers:
- Deze methode maakt gebruik van indirecte warmteoverdracht via verschillende warmtedragers zoals vuurvaste materialen of hete verbrandingsgassen om grondstoffen te kraken.
- Hoewel oudere processen zoals Wulff en Hoechst HTP beperkingen ondervonden, zijn nieuwere ontwikkelingen zoals de ACR en Dow PCC-processen veelbelovend voor het verwerken van zwaardere grondstoffen en het bereiken van efficiënt kraken voor acetyleenproductie.
5. Bijproduct van stoomkraken:
- Stoomkraken voor olefinproductie zoals ethyleen creëert op natuurlijke wijze acetyleen als bijproduct.
- Deze bron kan worden aangeboord door acetyleenverwijderingstechnieken te implementeren zoals katalytische hydrogenering of oplosmiddelextractie voor acetyleenwinning met een hoge zuiverheid.
1. Thermodynamische en kinetische aspecten
Hoge temperaturen en snelle reactietijden zijn essentieel voor acetyleenproductie uit koolwaterstoffen. Dit komt door de volgende aspecten:
- Thermodynamische beperkingen: Bij standaardtemperaturen is acetyleen instabiel vergeleken met andere koolwaterstoffen (hoge ΔHf en ΔGf). Boven ~1230 °C wordt acetyleen echter thermodynamisch bevoordeeld, waarbij het snijpunt in ΔGf-diagrammen naar links verschuift met afnemende koolwaterstofketenlengte (methaan vereist de hoogste temperatuur).
- Kinetische overwegingen: Zelfs bij deze hoge temperaturen blijft acetyleen minder stabiel dan zijn elementaire bestanddelen (C en H). Deze thermodynamische voorkeur voor ontleding vereist snelle blussing van nieuw gevormd acetyleen (verblijftijden ~0,1-10 ms) om afbraak te voorkomen.
- Concurrerende reacties: Kraken en recombinatie van grondstofkoolwaterstoffen, samen met verdere acetyleenconversie naar bijproducten, vinden plaats naast acetyleenvorming. Korte verblijftijden zijn cruciaal om deze concurrerende reacties te minimaliseren en de acetyleenopbrengst te maximaliseren.
Gedeeltelijke oxidatie biedt een alternatieve route, waarbij verbranding van een deel van de koolwaterstof de warmte genereert die nodig is voor acetyleenproductie uit het resterende deel. Precieze controle van de methaan:zuurstofverhouding is belangrijk om de gewenste reactietemperatuur te bereiken en de acetyleenopbrengst te optimaliseren.
Samenvattend vereist succesvolle acetyleenproductie uit koolwaterstoffen het overwinnen van thermodynamische beperkingen door hoge temperaturen, gecombineerd met snelle blussing en nauwkeurige reactiecontrole om concurrerende en ongewenste reacties te minimaliseren.
2. Productie van acetyleen door gedeeltelijke verbrandingsprocessen
Gedeeltelijke verbrandingsprocessen maken gebruik van in situ warmtegeneratie door gedeeltelijke oxidatie van een deel van de grondstof om acetyleensynthese uit het resterende deel aan te drijven. Deze methode maakt het gebruik van diverse grondstoffen mogelijk, van methaan en ethaan tot zwaardere fracties zoals nafta en vacuümgasolie. Aardgas is vanwege de brede beschikbaarheid een bijzonder geschikte grondstof.
Procesbeschrijving
In dit proces ondergaan zowel de grondstof als de zuurstof een aparte voorverwarming voor optimale prestaties. De voorverwarmde stromen komen in een brander, waar ze mengen en ontbranden in een reactiezone. Het productmengsel verlaat de reactiezone en wordt snel gekoeld, meestal met water of olie, om ongewenste ontleding te voorkomen.
Efficiënte acetyleenvorming vereist een korte en uniforme verblijftijd voor het gas in de reactiezone, meestal een paar milliseconden. Nauwkeurige controle van de stroomsnelheid balanceert een hoge opbrengst met het vermijden van voorontsteking, vlaminstabiliteit en cokesafzetting.
Voorbeelden van industriële installaties zijn:
- BASF-proces is het meest gebruikte gedeeltelijke verbrandingsproces voor aardgas, met ondergedompelde branders en efficiënte warmteterugwinning.
- Submerged Flame Process (SFP) is een proces dat is ontworpen voor zware oliefracties, met eenvoudig kraken, gelijktijdige acetyleen-ethyleenproductie en een hoge thermische efficiëntie.
- Partial Combustion Carbide Process is een proces op pilot-plant-schaal met cokes, zuurstof en kalk, dat potentiële toekomstige voordelen biedt zoals een hoge koolstofconversie en thermische efficiëntie voor op steenkool gebaseerde acetyleenproductie.
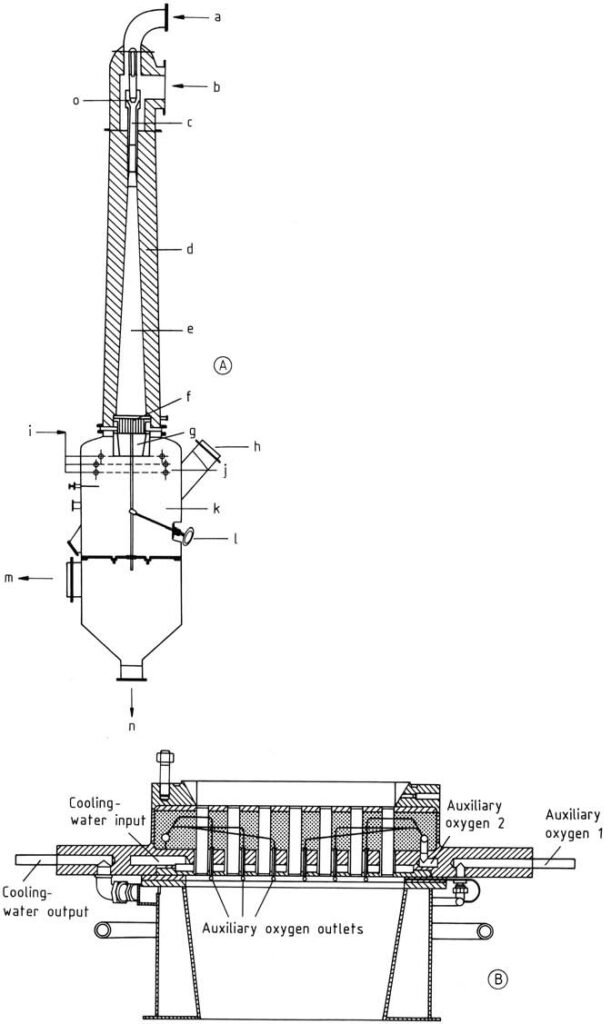
A) De brander: a) Zuurstof: b) Koolwaterstof; c) Menger; d) Betonvoering; e) Diffusor; f) Branderblok; g) Reactiekamer; h) Breekplaat; i) Inlaat blusmedium; j) Blusringen; k) Bluskamer; l) Handmatige schraper; m) Uitlaat gebarsten gas; n) Uitlaat blusmedium. B) Het branderblok
Hoewel gedeeltelijke verbrandingsprocessen primair gericht zijn op acetyleen, genereren ze ook bijproducten zoals waterstof en koolmonoxide. Binnen een complexe chemische fabriek kunnen deze bijproducten worden omgezet in waardevolle producten zoals synthesegas, zuivere waterstof en koolmonoxide, wat uiteindelijk de algehele economische levensvatbaarheid van het proces verbetert.
- Voor een meer gedetailleerde beschrijving van deze industriële processen kunt u de referentie aan het einde van dit artikel raadplegen.
3. Acetyleenproductie door elektrothermische processen
Elektrothermische processen, die verschillen van gedeeltelijke oxidatie, gebruiken elektrische boogtechnologie om acetyleensynthese te bereiken. Deze methode biedt verschillende voordelen:
- Grondstofonafhankelijkheid: De energie die nodig is voor de vorming van acetyleen is losgekoppeld van de specifieke koolwaterstofgrondstof.
- Verminderd koolwaterstofverbruik: Vergeleken met gedeeltelijke oxidatie kunnen elektrothermische processen het koolwaterstofverbruik met wel 50% verminderen.
- Gunstige economie: Onder gunstige omstandigheden zoals toegang tot goedkope elektriciteit (kernenergie, waterkracht, steenkool) of beperkte beschikbaarheid van koolwaterstoffen, kunnen elektrothermische processen zuiniger zijn.
Onder de elektrothermische opties zijn de elektrische boogproces onderscheidt zich door zijn geschiktheid voor het aandrijven van de zeer endotherme hogetemperatuuracetyleensynthesereactie. Het werd in 1925 in Duitsland gepionierd voor de productie van butadieen, het elektrische boogproces voor acetyleensynthese werd voor het eerst gecommercialiseerd in 1940 bij Chemische Werke Hüls.
Zowel gasvormige als vloeibare koolwaterstoffen, evenals vaste stoffen zoals steenkool, kunnen dienen als grondstof voor elektrische boogprocessen. Het ontwerp van de boogoven en de stappen voor productzuivering zijn afgestemd op de specifieke grondstof.
Gasvormige/vergaste feeds gebruiken doorgaans een eenstapsproces waarbij de boog het kraakgas rechtstreeks verwarmt. Vloeibare en vaste feeds kunnen een tweestapsproces gebruiken waarbij waterstof, voorverwarmd in de boogoven, fungeert als een plasmamedium voor grondstofinjectie.
Waterstof gevormd tijdens het kraken creëert een waterstofatmosfeer voor de boog in beide procestypen. Vanwege de hoge geleidbaarheid van waterstof en de ion-elektron recombinatiesnelheid, vereisen booglengtes die een bepaalde drempel overschrijden gelijkstroom (DC) bij standaardfrequenties en hoge spanningen. Bijgevolg zijn alle commerciële elektrische boogacetyleeninstallaties afhankelijk van DC-stroom.
Voorbeelden van industriële elektrothermische processen zijn:
- Productie uit gasvormige en/of vergaste koolwaterstoffen (Hüls Arc Process)
- Productie uit vloeibare koolwaterstoffen (Plasma Arc Process)
- Productie uit steenkool (Arc Coal Process)
- Productie uit calciumcarbide
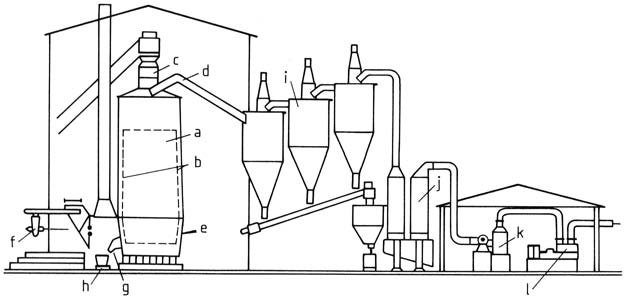
a) Carbidoven; b) Vuurvaste bakstenen bekleding; c) Vultrechter; d) Gasuitlaat; e) Zuurstofstraal; f) Aftapbrander; g) Aftapgoot; h) Bogey; i) Cycloon; j) Waskolom; k) Desintegrator; l) Compressor
- Voor een meer gedetailleerde beschrijving van deze industriële processen kunt u de referentie aan het einde van dit artikel raadplegen.
4. Productie van acetyleen door andere kraakprocessen
4.1. Thermisch kraken door warmtedragers
Thermisch kraken met warmtedragers biedt een alternatieve route voor de productie van acetyleen, die verschilt van gedeeltelijke oxidatie en elektrische boogmethoden. Oudere processen zoals de Wulff en Hoechst HTP werden echter gehinderd door beperkingen zoals grondstofbeperkingen (geraffineerde nafta en LPG) en roetvorming, wat uiteindelijk leidde tot hun stopzetting.
Voorbeelden van opkomende technologieën die het oude Wulff en Hoechst HTP-proces vervangen zijn:
- Kureha, Chiyoda, Union Carbide ACR-proces: Dit proces op pilotschaal maakt gebruik van oververhitte stoom als warmtedrager bij 2000 °C, gegenereerd via verbranding van H2-CH4-mengsels met zuurstof. Ruwe olie grondstof ondergaat snelle kraak in een multi-poort reactor, wat hoge waterstof, olefinen en acetyleen opbrengsten oplevert (4,2 wt%, aanzienlijk hoger dan traditionele olefin processen).
- Dow Partial Combustion Cracking (PCC) Process: Dit proces pakt coking en roetproblemen aan door gedeeltelijke oxidatie van gerecyclede blusolie (van het kraken) in de brander om synthesegas te genereren en een hoge waterstofpartiële druk in de reactiezone te handhaven. Hoewel zwaardere feeds zoals ruwe olie en residuen worden geaccepteerd, is de acetyleen opbrengst (2,5 wt%) lager dan het ACR proces vanwege langere verblijftijden (3-10x langer).
De volgende tabel geeft een vergelijking van de kenmerken van deze processen:
Kenmerk | Wulff & Hoechst HTP | ACR | Dow PCC |
---|---|---|---|
Grondstof | Geraffineerde nafta, LPG | Ruwe olie | Ruwe olie, zware residuen |
Warmtedrager | Vuurvast materiaal, hete verbrandingsgassen | Oververhitte stoom (2000°C) | Synthesegas van gedeeltelijke oxidatie van blusolie |
Acetyleenopbrengst | Beperkt | Hoog (4,2 gew.%) | Matig (2,5 gew.%) |
Voordelen | Indirecte warmteoverdracht, hoge thermische efficiëntie | Compatibiliteit met ruwe olie, hoge olefineopbrengst | Zware toevoercapaciteit, hoge waterstofwinning |
Nadelen | Roetvorming, nafta/LPG-beperking | Pilotschaalfase, complexe brander | Lagere acetyleenopbrengst, langere verblijftijd |
4.2. Acetyleen als bijproduct van stoomkraken
Stoomkraken produceert gewenste olefinen zoals ethyleen en propeen, maar genereert ook verschillende bijproducten, waaronder acetyleen. De concentratie is afhankelijk van:
- Grondstof: Verschillende koolwaterstoffen leveren verschillende acetyleengehaltes op.
- Residentietijd: Langere kraakduur verhoogt de vorming van acetyleen.
- Kraakernst: Hogere scheurernst (conversie of P/E-verhouding) leidt tot meer acetyleen.
Typische acetyleenconcentraties in het afgas variëren van 0,25 tot 1,35 gew.%, met specifieke gevallen tot 2,1 gew.%. De C2-fractie bevat doorgaans 0,4-2,5 gew.% acetyleen. Een 400.000 t/a ethyleenfabriek genereert 4.500-11.000 t/a acetyleen.
Om acetyleen te verwijderen, gebruiken de meeste ethyleenfabrieken: katalytische selectieve hydrogenering, de dominante methode voor het omzetten van acetyleen in ethyleen op Pd-gedoteerde katalysatoren, of oplosmiddelextractie die DMF gebruikt voor het terugwinnen van acetyleen met een hoge zuiverheid.
Wereldwijd werd in 2006 meer dan 112.000 t/a petrochemisch acetyleen teruggewonnen als bijproduct. De totale acetyleenmarkt daalde echter als gevolg van verschillende factoren, wat leidde tot beperkte nieuwe installaties voor het terugwinnen van acetyleen in de afgelopen jaren.
Petrochemisch acetyleen blijft economisch aantrekkelijk, zelfs met verdubbelde ethyleenprijzen. Het ombouwen van bestaande olefininstallaties met acetyleenabsorptie en -extractie uit onvermijdelijk bijproduct acetyleen blijft de meest haalbare route om aan de vraag naar acetyleen te voldoen.
Referentie
- Acetylene; Ullmann’s Encyclopedia of Industrial Chemistry. – https://onlinelibrary.wiley.com/doi/10.1002/14356007.a01_097.pub4