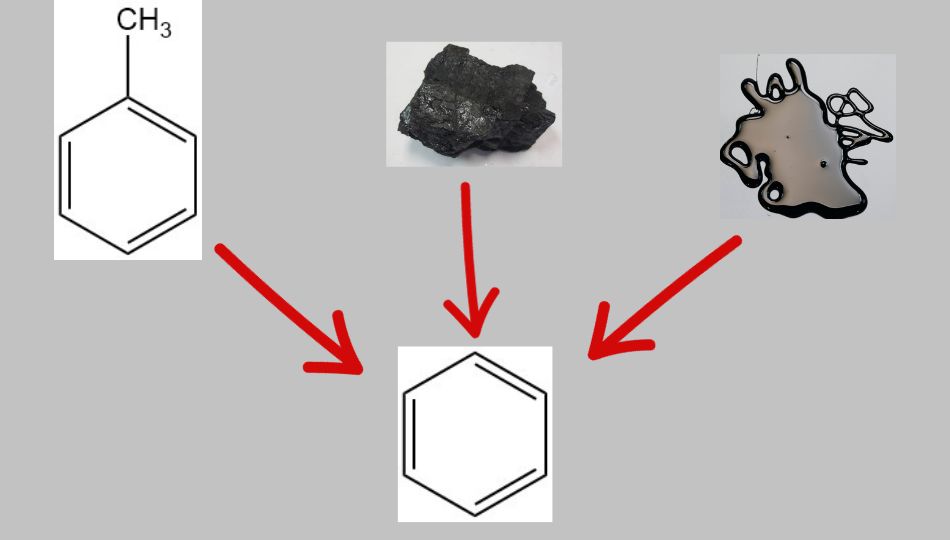
Benzeen werd traditioneel geproduceerd uit steenkool, maar petroleum werd halverwege de 20e eeuw de primaire bron vanwege nieuwe processen en toegenomen vraag. Katalytisch kraken en reformeren van petroleumfracties produceert benzeen en andere aromaten.
Inhoudsopgave
1. Productie van benzeen uit steenkool
Bij steenkoolcarbonisatie ontstaan lichte oliën die benzeen, tolueen en xylenen (BTX) bevatten. De opbrengst en samenstelling van deze oliën zijn afhankelijk van het type steenkool en de carbonisatietemperatuur. Cokesvorming bij lagere temperaturen produceert een schoon brandende cokes met een lager benzeengehalte. Cokesvorming bij hoge temperaturen produceert een harde cokes voor hoogovens en lichte oliën met een hoger benzeengehalte.
De lichte oliën worden gescheiden van de steenkoolteer en de BTX-fractie wordt geëxtraheerd met behulp van een hoogkokende petroleumfractie. De BTX wordt vervolgens gewonnen uit de absorberende olie en gezuiverd door destillatie, behandeling met zwavelzuur en hydrobehandeling. Oplosmiddelextractie en nauwe fractionering worden gebruikt om afzonderlijke aromatische componenten te isoleren.
Er zijn verschillende processen ontwikkeld om de BTX-snede te verfijnen tot benzeen met een hoge zuiverheid of BTX-componenten van superieure kwaliteit. Het Houdry-Litol-proces is een voorbeeld van een proces dat een reeks reacties en een katalytische reactor gebruikt om de BTX-snede te verfijnen. Het aangepaste Litol-proces is met name geschikt voor complexe cokesoven-aromatische materialen.
Een kleine hoeveelheid benzeen kan ook worden verkregen uit de destillatie van cokesoventeer, maar deze bron is niet van groot belang bij de productie van benzeen. Steenkoolteer is belangrijker als bron van pek, naftaleen, antraceen en andere gecondenseerde aromatische materialen.
2. Productie van benzeen uit aardolie
Katalytisch kraken en reformeren van aardolie, ontwikkeld in de late jaren 1930 en 1940, werd een nieuwe bron van benzeen, tolueen, xylenen en hogere aromaten. Aardolie verving steenkool als bron van BTX-materialen, vooral in de Verenigde Staten. De overgang van steenkool naar aardolie vond plaats in het Verenigd Koninkrijk en Europa rond 1960.
Tolueen was tijdens de Tweede Wereldoorlog erg gewild voor de productie van TNT. Het was echter duur om te produceren uit zuivere nafta’s en later uit katalytisch gekraakte en gereformeerde nafta’s. Een van de eerste katalytische kraakprocessen werd ontwikkeld door Houdry Corp.
Dit proces gebruikte een silica-alumina katalysator die in verschillende vaste bedden werd afgezet en regelmatig werd geregenereerd met lucht om afgezette cokes te verbranden. Een ander proces dat werd ontwikkeld door Mobil Oil gebruikte een bewegende bed silica-alumina katalysator. Het derde type proces, ontwikkeld door Exxon en anderen, staat bekend als het vloeistofkatalytische kraakproces (FCC) en wordt nu exclusief gebruikt.
Hoewel de katalytische kraakprocessen voornamelijk werden ontwikkeld om de opbrengst en het octaangetal van motorbrandstoffen te verhogen, had de geproduceerde benzine een hoog aromatengehalte, wat een bron van petrochemische benzeen opleverde.
2.1. Benzeen uit reformaat
Katalytische reforming werd een andere bron van BTX-aromaten uit aardolie. Het werd in de jaren 40 en begin jaren 50 geïnstalleerd om te voldoen aan de groeiende vraag naar benzeen, dat werd gebruikt om harsen, detergenten, synthetische vezels en andere chemicaliën te maken.
Reforming omvat het dehydrogeneren van naftenen tot aromaten, of het isomeriseren van alkylnaftenen gevolgd door dehydrogenering. Paraffines kunnen ook worden gedehydrocycliseerd tot aromaten. De reactie is traag, dus de procesomstandigheden moeten worden aangepast om het economisch te maken. Een kleine hoeveelheid dealkylering van gealkyleerde aromaten kan ook optreden.
Vroege katalytische reforming-eenheden gebruikten basismetaalkatalysatoren, zoals molybdeen op geactiveerde alumina. Deze processen hadden een korte cycluslengte en vereisten frequente katalysatorregeneratie. Het hydroformingproces werkte bij verhoogde temperaturen en druk met waterstofrecycling. Het zette naftafracties om in benzines met een hoog octaangehalte. De katalysator vereiste elke 8-16 uur regeneratie.
Latere katalytische reformingprocessen gebruikten bewegende katalysatorbedden of gefluïdiseerde bedden met een fijn verdeelde katalysator. Er zijn ook verschillende katalytische processen ontwikkeld met platina op aluminiumoxide en platina met modificatoren op aluminiumoxide.
Deze processen kunnen cycluslengtes hebben van zes maanden of veel korter, afhankelijk van de grondstof, procesomstandigheden en de ernst van de operatie. De nafta-grondstof moet worden voorbehandeld met katalytische hydrobehandeling om zwavelverbindingen te verwijderen.
Commerciële katalytische reformingprocessen omvatten: katalytische reforming (Institut Français du Pétrole), magnaforming (Engelhard Industries), platforming (UOP), powerforming (Exxon Research & Engineering), rheniforming (Chevron Research Co.) en ultraforming (Standard Oil of Indiana).
De bedrijfsomstandigheden variëren sterk. Temperaturen variëren van 425 tot 525 °C en manometerdrukken van 0,7 tot 3,5 MPa.
Nafteenconversies naderen 100%. Cyclisatie van paraffines is veel lager. Om bijvoorbeeld benzeen te produceren uit C6 en hogere voorraden, wordt methylcyclopentaan geïsomeriseerd tot cyclohexaan en gedehydrogeneerd tot benzeen. De omzetting van n-hexaan naar benzeen is beperkt.
Katalytische reformer-eenheden kunnen worden bediend bij relatief hoge druk met een reeks vastebedreactoren. De katalysator wordt geregenereerd met gedefinieerde intervallen. Eenheden die zijn ontworpen voor hogere conversie werken bij lagere druk met frequentere katalysatorregeneratie. Kortere cycli, swingreactoren of continue regeneratie worden gebruikt.
Het platformingproces dat wordt weergegeven in Figuur 1 maakt gebruik van continue katalysatorregeneratie.
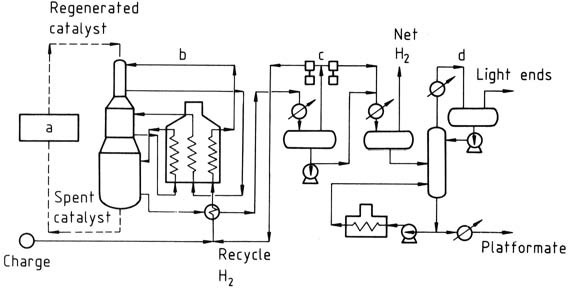
a) Katalysatorregeneratie; b) Reactoren; c) Productscheiding; d) Stabilisator
Een ander ontwerp dat is ontwikkeld door Standard Oil of Indiana maakt gebruik van een swingreactor waarin de vaste-bedkatalysator in één reactor wordt geregenereerd en weer in bedrijf wordt genomen, waarbij de katalysatoren in elk van de resterende reactoren in rotatie worden geregenereerd. Manometerdrukken van 0,7-2,4 MPa worden gebruikt in de verschillende processen.
Voor de productie van benzine worden nafta’s met kookbereiken van ongeveer 80-210 °C gebruikt. Als reforming wordt uitgevoerd voor de productie van aromatische ladingsvoorraden, kunnen de samenstelling en het kookbereik van de nafta worden gewijzigd.
Het reformaat kan een RON-helder octaangetal van wel 100 hebben en kan tot 70 vol% aromaten bevatten.
In de loop der jaren is het proces effectiever gemaakt. Reformingkatalysatoren zijn aangepast. Er werd vastgesteld dat kleine hoeveelheden water de benzeenopbrengsten met bepaalde katalysatoren bij de productie van BTX verbeterden. Hogere xyleenopbrengsten zijn het resultaat van werken bij hogere ruimtesnelheden.
2.2. Benzeen uit pyrolysebenzine
Pyrolysebenzine, een bijproduct van de productie van ethyleen, is een andere goede bron van BTX. De hoeveelheid geproduceerde pyrolysebenzine is afhankelijk van de grondstof en de bedrijfsomstandigheden. Het is hoger bij zwaardere grondstoffen en kan oplopen tot 20% voor nafta van gemiddelde sterkte.
De samenstelling van pyrolysebenzine varieert met het kookpunt van de grondstof, waarbij zwaardere grondstoffen meer tolueen en xyleen produceren dan benzeen.
Pyrolysebenzine bevat > 60% BTX, maar bevat ook onverzadigde vetzuren en diolefinen vanwege de hoge temperatuur die nodig is voor de productie van ethyleen. Het diolefinengehalte is doorgaans 3-5% en het totale gehalte aan cyclische olefinen en cyclische diolefinen is ook 3-5%.
Pyrolysebenzine is onstabiel vanwege het diolefinische materiaal. Diolefinen met een lager kookpunt kunnen worden verwijderd door destillatie, maar dit kan moeilijk zijn vanwege hun neiging tot polymeriseren en depolymeriseren. Daarom wordt over het algemeen een twee-fasen hydrobehandelingsproces gebruikt.
De eerste fase zet diolefinen om in olefinen. Als de benzine als brandstof wordt gebruikt, is verdere behandeling mogelijk niet nodig. Als de benzine echter een bron van aromaten is, wordt een tweede fase gebruikt om olefinen te verzadigen en resterende zwavel te verwijderen.
3. Andere productiemethoden van benzeen
Om aan de vraag te voldoen, kan de benzeenproductie worden verhoogd uit andere aromatische verbindingen, zoals de BTX-fracties verkregen uit katalytisch reformaat, pyrolysebenzine of lichte oliën uit koolcarbonisatie. Dit kan worden gedaan met behulp van hydrodealkylering, disproportionering of combinatieprocessen.
3.1. Productie van benzeen door hydrodealkylering
Hydrodealkylering is een proces waarbij alkylgroepen uit aromatische verbindingen worden verwijderd met behulp van waterstof. Het is een bron van benzeen en tolueen is de gebruikelijke lading. Hoger gealkyleerde aromaten kunnen ook worden gebruikt, maar de reactie verloopt stapsgewijs. Andere alkylbenzenen, zoals ethylbenzeen en propylbenzeen, dealkyleren in één stap en vormen de overeenkomstige alkanen.
Katalytische en thermische processen
Zowel katalytische als thermische processen worden gebruikt voor hydrodealkylering. Katalytische processen, zoals Detol en Hydeal, werken bij 575-650 °C en 2,5-6 MPa. Thermische processen, zoals HDA en THD, werken bij hogere temperaturen dan katalytische processen, maar opbrengsten en reactiesystemen zijn vergelijkbaar in beide typen.
Detolproces (Figuur 2)
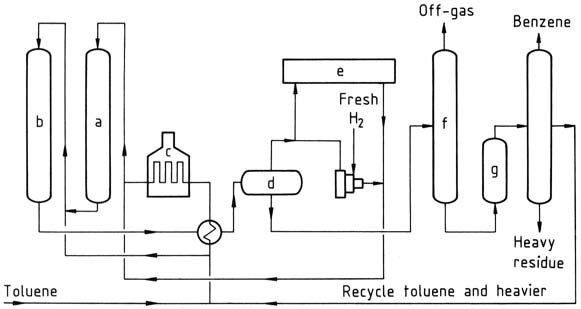
a) Reactor I; b) Reactor II; c) Oven; d) Separator; e) Waterstofzuivering; f) Stabilisator; g) Kleibehandelingsinstallatie
Het Detol-proces is een katalytisch dealkyleringsproces dat gebruikmaakt van een vaste-bed dealkyleringskatalysator. De voeding bestaat uit tolueen of mengsels van tolueen en andere gealkyleerde benzenen. De gealkyleerde aromaten en waterstof passeren bij verhoogde temperatuur en druk in serie over de katalysator.
Warmtewisselaars koelen de reactorproducten af en condenseren benzeen, niet-gereageerde tolueen en de zwaardere niet-gereageerde gealkyleerde benzenen. Een hogedruk-flashdrum scheidt gerecyclede waterstof en productgas. Het productgas wordt gesplitst in stromen voor brandstofgas, voor waterstofzuivering indien nodig en voor gerecyclede waterstof.
De vloeistof uit de flashdrum wordt naar een stabilisator gepompt, waar het resterende gas en laagkokende koolwaterstoffen worden afgevoerd en gebruikt als brandstofgas. De bodems van de stabilisator worden behandeld met klei en doorgegeven aan een kolom waar de benzeen overhead wordt gedestilleerd.
Niet-gereageerde tolueen en zwaardere aromaten worden gerecycled. De benzeen die wordt geproduceerd in opbrengsten van ongeveer 99 mol% is zeer zuiver, doorgaans 99,95%, met een vriespunt van 5,45 °C.
Hydeal-proces
Het Hydeal-proces is een ander katalytisch dealkyleringsproces. Het is vergelijkbaar met het Detol-proces, maar gebruikt in plaats daarvan een chroom-alumina-katalysator. Nitratie-kwaliteit benzeen wordt verkregen in opbrengsten van ca. 98 mol%. Niet-gereageerd aromatisch ladingsmateriaal van de once-through-bewerking wordt gerecycled om praktisch volledige omzetting te verkrijgen. Het proces wordt ook gebruikt om alkylnaftalenen te hydrodealkyleren.
HDA- en THD-processen (Figuur 3)
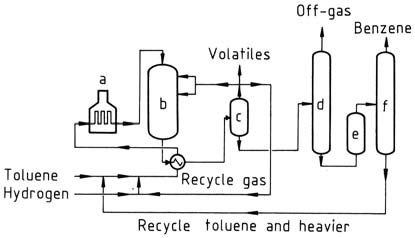
a) Verwarmer; b) Reactor; c) Separator; d) Stabilisator; e) Kleibehandelingsapparaat; f) Destillatie
De HDA- en THD-processen zijn thermische dealkyleringsprocessen. Ze werken bij hogere temperaturen en druk dan katalytische processen. Benzeenopbrengsten van 99 mol% worden bereikt.
MHC-proces (Figuur 4)
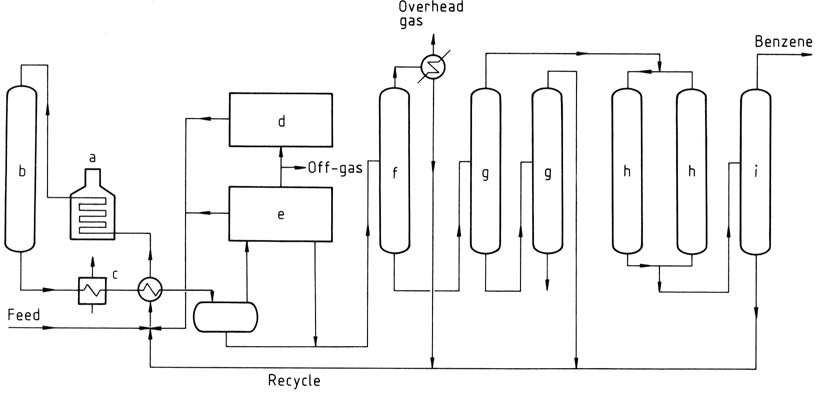
a) Verwarming; b) Reactor; c) Afvalwarmteketel; d) Waterstofregeneratie; e) Aromatische terugwinning; f) Fractionering; g) Vacuümkolommen; h) Kleibehandelingsinstallaties; i) Benzeenkolom
Het MHC-proces is een thermisch dealkyleringsproces dat is ontwikkeld door Mitsubishi Petrochemical Co. Het kan grondstoffen verwerken die tot 30% niet-aromaten bevatten zonder toevlucht te nemen tot aromatische extractie en fractionele destillatiestappen. Het proces werkt op waterstof met een lage zuiverheid, waardoor de hoeveelheid benodigde make-up waterstof wordt verminderd. Benzeen met een zuiverheid van 99,95% wordt gemakkelijk bereikt.
3.2. Productie van benzeen door disproportionering
Het Tatoray-proces is een manier om benzeen en xylenen te maken uit tolueen en C9-aromaten. Het gebruikt een edelmetaal- of zeldzame-aardekatalysator en recycleert waterstof om de reactie te laten werken. Het proces werkt bij 350-525 °C en 1-5 MPa.
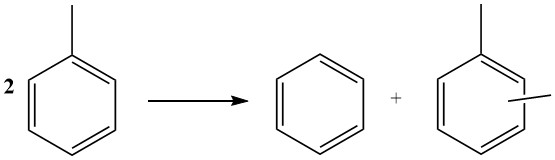
De geproduceerde benzeen is zeer zuiver en de xylenen bevatten zeer weinig verzadigde koolwaterstoffen. Wanneer de grondstof beperkt is tot C9- en C10-aromaten, produceert het proces een mengsel van benzeen, tolueen en xylenen.
Het Tatoray-proces wordt gebruikt in een aantal commerciële fabrieken over de hele wereld. De opbrengst van benzeen en xylenen is ongeveer 97% wanneer tolueen als grondstof wordt gebruikt.
3.3. Productie van benzeen door gecombineerde dealkyleringsprocessen
Er zijn verschillende processen ontwikkeld om benzeen te produceren uit onzuivere BTX-grondstoffen door hydrogenering en dealkylering te combineren.
Een voorbeeld is het Pyrotol-proces (Figuur 5), waarbij de grondstof wordt gefractioneerd om lichte en zware verbindingen te verwijderen, de C6-C8-fractie wordt verdampt en door een katalytische reactor wordt geleid om selectief diolefinen, cyclische diolefinen en styreen te hydrogeneren.
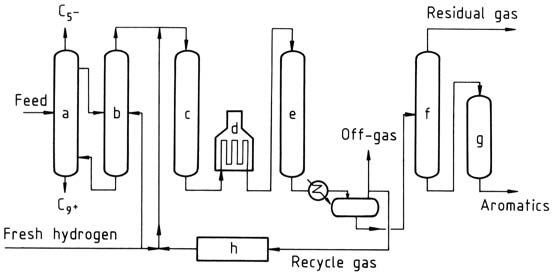
a) Destillatie; b) Verdamper; c) Voorreactor; d) Verwarmer; e) Pyrotolreactor; f) Stabilisator; g) Kleibehandelingsapparaat; h) Waterstofzuivering
Het effluent van de voorbehandelingsreactor wordt vervolgens geladen in de Pyrotol-reactoren, waar aromaten worden gedealkyleerd tot benzeen. Andere reacties omvatten ontzwaveling en hydrokraken van niet-aromaten. Niet-gereageerde tolueen en zwaardere aromaten worden gerecycled. Het benzeenproduct bevat minder dan 0,5 ppm thiofeen en heeft een vriespunt van ten minste 5,47 °C.
Een ander voorbeeld is het Litol-proces, ontwikkeld door de Houdry Division van Air Products en door Bethlehem Steel. Dit proces produceert zuivere benzeen uit aromatische lichte olie verkregen uit kolencarbonisatie. Het maakt gebruik van twee katalytische reactiestappen.
Na prefractionering van de ruwe lichte olie om C5 en lichtere fracties bovenin en C9 en zwaardere als bodem te verwijderen, wordt de C6-C8-fractie verdampt. In de eerste stap worden diolefinen en styreen gehydrogeneerd.
Het effluent komt vervolgens in contact met de Litol chroom-alumina katalysator bij 500-600 °C, waar ontzwaveling, hydrokraken en dealkylering plaatsvinden. Benzeenzuiverheid van 99,97% met vriespunt van 5,5 °C en een thiofeengehalte van minder dan 0,5 ppm zijn typisch.
Mitsubishi Petrochemical Co. heeft een proces ontwikkeld voor het produceren van benzeen uit pyrolysebenzine. Dit proces omvat twee-fase hydrogenering gevolgd door oplosmiddelextractie om de aromaten te extraheren, of alternatief, reactie van het gehydrogeneerde materiaal in Mitsubishi’s MHC-proces.
Mobil Chemical Co. heeft een vloeistoffase disproportioneringsproces ontwikkeld voor het omzetten van tolueen in benzeen en xylenen. Dit lage-temperatuur disproportioneringsproces (LTD) maakt gebruik van een zeer actieve op zeoliet gebaseerde katalysator die de reactie mogelijk maakt bij temperaturen zo laag als 260 °C. Waterstofrecycling is niet vereist in dit vloeistoffaseproces.
Referentie
- Benzene; Ullmann’s Encyclopedia of Industrial Chemistry. – https://onlinelibrary.wiley.com/doi/10.1002/14356007.a03_475